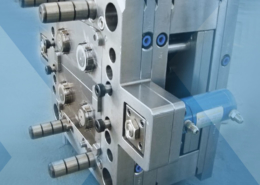
Plastic Injection Molding | Precision Molded Plastics Inc - precision plastic in
Author:gly Date: 2024-10-15
Plasticut’s product range includes intricate medical device components, high-precision aerospace parts, and durable industrial machine components. Utilizing advanced CNC machining technology, Plasticut ensures exceptional accuracy and quality in their products.
Amec Plastics is known for its ability to produce high-precision industrial components, durable automotive parts, and robust construction materials. By utilizing advanced mold injection techniques and state-of-the-art extrusion technologies, they ensure exceptional accuracy and quality in their products.
Visit the factories, if possible, to understand their processes and meet with representatives to discuss project details and cooperation terms.
Forme Technologies excels in creating intricate medical device components, precise automotive parts, and durable consumer goods. Utilizing advanced mold injection techniques and precision engineering, they ensure superior quality and consistency.
There are many variables that must be considered when choosing the right injection molding supplier for your business. Here are five key steps you can take to ensure the best decision for your company:
After transmitting an injection signal injection start or screw position to the gas-assisted control unit, the injection molding machine starts a gas injection process, waits for the next injection process to deliver another injection signal, starts another cycle, and so on.
In gas-assisted injection molding, less material is used due to not cramming a mold. This reduced material usage excludes the need to pack the material, resulting in a hollow core in thicker components and saving up to 40% on the material utilized.
The company’s ability to deliver customized solutions tailored to specific industry needs highlights their innovative approach and commitment to quality.
Gas-assisted injection molding is a plastic molding process that combines standard injection molding principles with the use of pressurized inert gas. It employs mold cavities in the shape of the product. 70%-80% of the mold is filled with molten plastic raw material. Filling the remaining volume with Nitrogen gas packs the plastic substance against the mold’s walls.
Romar Engineering’s products include intricate medical device parts, critical aerospace components, and robust industrial machinery parts. Utilizing cutting-edge technologies like 3D printing and advanced mold injection techniques, they deliver innovative and high-quality products. Their expertise in mold design, commitment to continuous improvement, and rigorous quality control distinguish them in the industry.
Melro is a specialized Australian company renowned for its production of rotationally molded plastic products. Their core business focuses on the design, manufacture, and supply of high-strength, durable plastic solutions for various industrial applications.
The company is known for its innovative solutions, stringent quality control, and ability to deliver customized products tailored to specific client needs. Their expertise in mold injection and commitment to excellence make Rapid Plastics Australia a leader in the plastic manufacturing industry, setting benchmarks for quality and reliability.
ADDE is a premier Australian firm renowned for its excellence in plastic injection molding, especially in Australian mold injection.
Known for handling complex molding projects, A Plus Plastics delivers high-quality, tailored solutions to meet various industry requirements. Their commitment to sustainability, innovation, and superior customer service ensures that each product not only meets but exceeds client expectations.
Main Services: Specializes in the design, manufacturing, and delivery of rotomoulded plastic products, including water tanks and custom mouldings.
Forme Technologies specializes in high-precision mold injection and plastic component manufacturing. Their core business provides comprehensive solutions from concept design to full-scale production for medical, automotive, and consumer product industries.
The gas used in gas-assisted injection molding must be inert (often nitrogen) with a maximum pressure of 35MPa, a maximum pressure of up to 70MPa, and a nitrogen purity of 98%.
Main Services: Specializes in CNC machining, plastic fabrication, and injection moulding services for various applications.
A Plus Plastics manufactures a diverse range of products, including automotive parts, consumer goods packaging, industrial containers, and building materials. The company leverages advanced automation and robotics in its production processes, significantly enhancing efficiency and precision.
Tight geometric tolerances are achieved due to the consistent packing of the resin substance. The mold shapes the exterior surface, while the homogeneous pressure distribution of the gas shapes the inner surface.
In this article, we highlight ten leading plastic injection moulding companies in Australia known for their innovation, quality, and exceptional customer service.
The company’s ability to handle complex projects and provide customized solutions underscores their innovative approach and stringent quality control. By focusing on mold injection, Plasticut consistently sets industry standards, showcasing their superior craftsmanship and specialized capabilities. This commitment to excellence makes Plasticut a leader in the plastic fabrication and mold injection industry.
There are two types of gas-assisted injection molding processes: exterior and internal. It also adheres to a specific process consisting of three parts. In the following sections, we distinguish between the two categories and walk you through the process.
Evaluate the shortlisted companies based on experience, certifications, technology, production capacity, quality, service, and delivery timelines.
Gas-assisted injection molding is an efficient, beneficial, and reliable production process for plastic products. However, before you rely on this method, it’s important to consider the limitations, process, and advantages this process offers to understand better if it is an ideal manufacturing approach for your product’s manufacturing demands.
ACIS®, Autodesk Inventor®, CATIA® V5,Creo™ Parametric, IGES, Parasolid®, Pro/ENGINEER®,Siemens PLM Software’s NX™, SolidEdge®, SolidWorks®, STEP
The gas-assist injection molding procedure is divided into three steps (refer to the diagram below). Each stage is a key phase in the process and demands the manufacturing team’s design sensibility and practical skills.
In today’s fast-paced world, the manufacturing industry is one of the most innovative, always setting new norms. In this growing and evolving industry, gas-assisted injection molding is an innovative plastic manufacturing technology that produces high-quality products.
Romar Engineering specializes in advanced manufacturing solutions with a focus on mold injection. Their core business encompasses the design, development, and production of high-precision molds and plastic components for medical, aerospace, and industrial sectors.
Compare quotes considering price, service, quality, and delivery time. Select the best-fit supplier and sign a detailed contract.
This method is well-known for producing a high-quality surface finish. Because the gas pressure acts uniformly on the non-aesthetic side, the opposite end packs snugly into the mold extremities, acquiring its exact shape. The resulting surface is so exact, including the mold’s subtle textures and patterns. As a result, if the part contains surface patterns and imprints, external gas-aided molding is desirable.
Exterior gas-assisted injection molding is fundamentally different from internal injection molding. The gas does not enter the material, resulting in hollow regions. Rather, it enters the mold through microchannels on only one side. It applies pressure from the backside/non-aesthetic side of the part to pack the molten resin against the mold’s walls.
The pressurized gas’s homogeneity ensures steady pressure at all spots inside the mold. This contributes to an extremely smooth surface.
Utilizing advanced precision injection molding technology, the company ensures consistency and high accuracy in every product. Additionally, B&C Plastics excels in rapid prototyping, swiftly turning concepts into physical models, thereby reducing product development cycles.
Reach out to the shortlisted companies with your design drawings and request quotes. Inquire about additional services like design support and quality control.
External heating and friction cause the resin to melt, while the screw’s constantly decreasing pitch compresses it to pressurize it. Because of the hollow parts, the pressure required for gas-assist molding is lower than for conventional injection molding. Furthermore, because the pressure is generated by gas rather than a thick, viscous liquid, there are fewer viscosity-based frictional losses inside the pressurized media.
Because of the numerous gas channels, gas-assisted injection molding has a distinct advantage in this area. These pathways allow the gas to readily and swiftly infiltrate all mold sections, which a viscous liquid cannot do. As a result, the final item has a consistent pressure distribution and lower internal tensions.
Plastics are lightweight materials in general. They also only partially fill the mold cavity. Each of these variables indicates that the last section is light.
Flow markings, sink marks, internal tensions caused by non-uniform pressures, and shrinkage after cooling are frequent issues in injection molding. The finished product, however, is free of sink marks since the subsequent gas penetration phase compensates for shrinkage.
A Plus Plastics is a premier Australian company specializing in the design and production of high-performance plastic components. Their core business includes offering comprehensive injection molding solutions that span from initial concept design to full-scale production.
Plastral is a leading company specializing in the distribution and fabrication of high-quality plastic materials, with a strong focus on mold injection. Their core business involves supplying plastic sheets, rods, and tubes, along with offering custom plastic fabrication services for a wide range of applications.
Amec Plastics is a leading company specializing in mold injection and plastic extrusion. Their core business involves the design, engineering, and production of custom plastic components and extruded profiles for a wide range of industries, including automotive, industrial, and construction.
Parts with wide surfaces and curved profiles are also handled effectively. The gas channels parallel the entire surface, allowing the gas to exert pressure across a large region. As a result, producing huge surfaces is not a significant challenge.
Amec Plastics stands out for their innovative approach and stringent quality control, providing customized solutions that meet specific client needs. Their expertise in mold injection and commitment to continuous improvement and customer satisfaction position Amec Plastics as a leader in the plastic manufacturing industry.
This procedure uses gas-assisted equipment named a gas-assisted control unit and a nitrogen generator, which are part of the gas-assisted injection molding process gas-assisted equipment. It is a separate system not connected to the injection molding machine, and its sole interaction is the injection signal connecting line.
Today, we will dive further into the manufacturing process by discussing what it is and its various types, applications, benefits, and more.
Maintain regular communication with the supplier, conduct quality inspections, and provide feedback upon project completion to ensure quality and establish future cooperation.
Utilizing advanced CAD/CAM technologies, ADDE ensures optimal performance and durability in their molds. Known for managing large-scale production and complex mold designs, ADDE offers bespoke solutions tailored to client needs.
Main Services: Plastic Injection Moulding, 2 shot moulding (Over Moulding), Rapid Prototyping, CNC Machining, 3D Printing
To realize the injection, pressure holding, and cooling processes, pump high-pressure inert gas (nitrogen) into the molten plastic to generate a vacuum suction and push the molten material forward.
Main Services: Specializes in silicone injection moulding, precision engineering, and advanced 3D printing for medical and industrial sectors.
Specializing in the design, engineering, and production of precision molds and plastic components, ADDE serves diverse industries with expertise. Their products include intricate electronic device housings, sophisticated medical equipment parts, and high-quality consumer components.
Gas-assisted injection molding also benefits manufacturers as an innovative and unique manufacturing process. These benefits include:
B&C Plastics is a leading Australian plastic injection molding company specializing in the design, manufacture, and supply of custom plastic products. Their core business spans the entire process from concept design to final production, providing comprehensive end-to-end services to clients.
B&C Plastics produces a wide range of products, including industrial components, consumer goods housings, medical device parts, and complex-shaped injection molded parts.
Main Services: Specializes in plastic injection moulding, tooling, and engineering services, providing high-quality and innovative solutions for a wide range of industries.
Plasticut specializes in plastic fabrication and injection molding, with a strong emphasis on precision and quality in mold injection. Their core business involves the design, production, and supply of precision CNC machined plastic parts for industries such as medical, aerospace, and industrial machinery.
Australia’s manufacturing industry is robust and dynamic, with plastic injection moulding playing a crucial role. This advanced process is essential for producing a wide variety of plastic products, from everyday items to specialized industrial components.
It is a popular method for producing huge, hollow, molded plastic pieces. It has various advantages, including exceptional surface polish and geometric correctness.
Because the gas has high-efficiency pressure transfer, it can maintain consistent pressure in all sections of the air channel, eliminating internal stress, preventing product deformation, and considerably reducing pressure in the cavity, eliminating the need for high pressure during the molding process. Clamping force can also reduce product weight and remove sink marks.
Main Services: Provides plastic injection moulding, product design and development, and precision toolmaking services for medical, automotive, and consumer products.
The process of main gas penetration occurs once the requisite amount of resin is introduced into the mold. A pressurized gas source injects nitrogen into the spruce network, causing a bubble within the resin substance.
These companies exemplify the best of Australian manufacturing capabilities, driving the industry forward and ensuring Australia’s position as a key player in the global manufacturing arena.
Main Services: Provides high-quality plastic injection moulding services, product design and development, and precision toolmaking.
Rapid Plastics Australia specializes in the design, production, and supply of high-quality rotationally molded plastic products, with a strong emphasis on mold injection techniques.
Melro specializes in durable rotational molding, and ADDE uses advanced CAD/CAM technologies. Plasticut leads in CNC machining, and Plastral provides extensive material distribution and custom fabrication.
Main Services: Offers plastic fabrication, injection moulding, and material supply services for industrial and commercial applications.
With a strong focus on innovative design and stringent quality control, B&C Plastics guarantees that each product meets the highest standards, fulfilling client needs and expectations.
Initially, the mold clamps are closed, and raw resin is supplied into the injection molding equipment’s hopper. The machine melts and pressurizes the resin in its screw-feed part, just like in a typical injection molding operation.
This molten resin is then injected into the mold cavity. Nevertheless, the resin injection mechanism does not entirely fill the mold because the product comprises hollow areas. The amount of resin material injected is proportional to the volume of the part. It is often determined by geometrical elements such as wall thickness, ribbed features, holes, etc. Typically, 70%-80% of the mold is filled with plastic material.
The cycle time in this manufacturing during the manufacturing of thick-walled products is reduced by 50% or more when compared to traditional injection molding. This reduced cycle time is acquired because there is no molten core to solidify, and the material in the mold chamber hardens faster, allowing the component to be ejected sooner.
Their commitment to innovation and quality assurance underscores their leadership in mold manufacturing, exemplifying superior craftsmanship and specialized capabilities.
As a result, there is a secondary gas penetration phase during which extra gas flows into the mold to fill the holes. This ensures a smooth fill and maintains uniform pressure.
By integrating advanced mold injection processes, Romar Engineering consistently meets exacting client standards, showcasing superior craftsmanship and specialized capabilities. This dedication to excellence and innovation positions them as a leader in mold injection and advanced manufacturing.
Because internal gas-aided molding is more extensively used than external gas-assisted molding, we will cover it first. Molten plastic resin first enters the mold through spruce passages. The gas then enters the molten resin through a nozzle, producing a bubble. The pressure of the expanding gas bubble pushes the resin against the mold walls, giving the pieces their shape.
The sector has experienced significant growth, with companies investing in state-of-the-art machinery and sustainable practices. Key applications include automotive, medical, food packaging, and consumer goods, offering efficiency, precision, flexibility, and sustainability.
Plastral’s product offerings include industrial components, signage materials, and construction plastics. Utilizing advanced fabrication techniques and technologies, Plastral ensures precision and consistency in every product.
The gas-assisted control unit is a device that regulates the time and pressure of gas injection. It has a multi-group gas circuit architecture allows it to control the gas-assisted production of numerous injection molding machines at once. Furthermore, the gas-assisted control unit incorporates a gas recovery function to limit gas consumption as much as possible.
Known for innovation and rigorous quality control, Forme Technologies delivers customized solutions tailored to client needs, positioning them as a leader in the plastic manufacturing industry.
Internal gas-assisted molding also has much shorter cycle times. Because the geometries have hollow areas and narrow cross-sections, they cool down faster than solid parts.
This approach not only provides superior surface quality it provides but also allows for thicker sections due to improved packing and shrinkage resistance. For ribbed/boss features, the rib/wall ratio can be as high as 1, which is far superior to conventional methods. This gives the molded part strength and stability.
The resin begins to cool and contract at the end of the primary gas penetration phase. The gas pressure lowers significantly due to the gap generated by thermal contraction. This can result in part deformations and geometric inaccuracies, neither of which is acceptable.
Melro’s product range includes large water storage tanks, chemical storage containers, and agricultural equipment. Utilizing advanced rotational molding technology, Melro ensures that each product is robust, reliable, and meets exacting standards.
Australia’s injection molding industry features ten exemplary companies, each offering unique strengths. B&C Plastics excels in precision and rapid prototyping, while A Plus Plastics focuses on sustainable, automated solutions.
Romar Engineering and Forme Technologies excel in high-precision mold injection for medical and aerospace sectors. Amec Plastics combines mold injection with extrusion for industrial solutions, and Rapid Plastics Australia specializes in rotational molding for durable storage.
Their core business serves agricultural, industrial, and commercial sectors, producing durable water storage tanks, chemical storage containers, and custom-molded products. Utilizing advanced mold injection and rotational molding technologies, Rapid Plastics Australia ensures superior strength, consistency, and precision in their products.
Main Services: Specializes in the design and manufacturing of rotomoulded plastic products, including water tanks and custom mouldings, as well as injection moulding services.
Conduct industry research to find Australian plastic injection molding companies. Read reviews and case studies, then create a shortlist of potential suppliers.
By integrating mold injection into their services, Plastral sets the benchmark for excellence in plastic fabrication, emphasizing their superior craftsmanship and specialized capabilities. This dedication to quality and innovation positions Plastral as a leader in the plastic fabrication and mold injection industry.
The molten resin is pushed to the mold’s borders by the pressure and expanding volume of the gas bubble. The gas pressure remains constant throughout this procedure, ensuring the resin reaches all corners of the mold and completely fills it.
Clearly outline your product specifications, materials, quantity, budget, deadline, and quality requirements before searching for suppliers.
Nave ISK-8, Parque Industrial y Logístico Sky Plus, Avenida Mineral de Cinco Señores No.100, del Parque Industrial Santa Fe, Silao de la Victoria, Guanajuato, México
This method is ideal for producing hollow, lightweight shapes. Also, the gas exerts steady pressure on the resin, which aids in the reduction of shrinkage and distortion/warpage. These variables are typically the primary cause of diminishing dimensional accuracy in thin walls. Thin-walled pieces are hence another unique application of this technology.
The company’s ability to customize products to specific client requirements showcases their expertise in mold manufacturing. With a professional design and engineering team, Melro delivers innovative and high-quality products, making them a trusted name in the industry.
Main Services: Specializes in the design, tooling, and manufacturing of high-quality plastic injection-molded products, offering services such as custom molding, prototyping, and sub-assembly for various industries.
GETTING A QUOTE WITH LK-MOULD IS FREE AND SIMPLE.
FIND MORE OF OUR SERVICES:
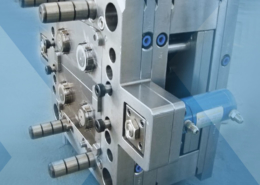
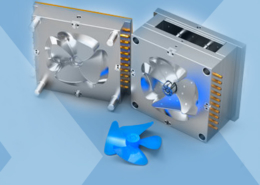
Plastic Molding

Rapid Prototyping
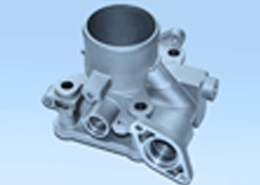
Pressure Die Casting
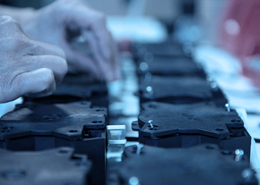
Parts Assembly
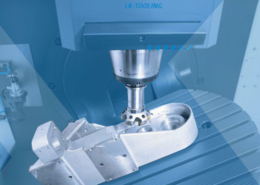