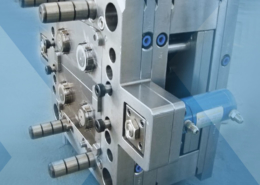
Plastic Injection Molding | Precision Molded Plastics Inc - high precision plast
Author:gly Date: 2024-10-15
Screw speed High screw speed, line speed is 1m / s; however, it is best to set the screw speed to a lower point, as long as the plasticizing process can be completed before the end of the cooling time; the required screw torque is low
Barrel temperature Zone 1 260 ~ 290 ° C (suggest 280 ° C)Zone 2 260 ~ 290 ° C (suggest 280 ° C)Zone 3 80 ~ 290 ° C (suggest 290 ° C)Zone 4 280 ~ 290 ° C (suggest 290 ° C)Zone 5 280 ~ 290 ° C (suggest 290 ° C)
Barrel equipment Standard screw, special geometry has strong plasticizing ability; anti-reverse ring, straight-through nozzle; for the addition of glass fiber reinforcement, it needs high wear-resistant bimetallic barrel
Compared to other plastic manufacturing processes, plastic injection molding offers a number of clear advantages, especially when working with a knowledgeable and skilled injection molding partner. These benefits encompass the following:
Feeding zone 60~90°C (suggest 80°C) Nozzle 280 ~ 290 ° C (suggest 290 ° C) the stroke utilization is 35% and 65%, and the ratio of module flow length to wall thickness is 50:1 to 100:1. The temperature in the feed zone and zone 1 directly affects the feed efficiency. Increasing these temperatures can make the feed more even.
Reduce the pressure of the pressure to reduce the stress inside the productBack pressure2 ~ 8MPa (20 ~ 80bar), need to be accurately adjusted, because the back pressure is too high, it will cause the plasticization uneven injection speed is recommended to use a relatively fast injection speed; the mold has good ventilation or the product is prone to coking
At The Sterling Healthcare Manufacturing, we understand the importance of quality in component manufacturing. By leveraging our extensive knowledge of the medical and pharmaceutical industries, we provide full-service, turnkey plastic injection molding solutions that fully comply with industry specifications and standards. For additional information about our plastic injection molding capabilities and how we serve the medical and pharmaceutical industries, contact us today.
Melt temperature 270 ~ 290 ° CBarrel constant temperature 240 ° CMold temperature 60~100°CInjection pressure 100 ~ 160MPa (1000 ~ 1600bar), if it is processing thin section long channel products (such as wire tie), you need to reach 180MPa (1800bar)Holding pressure 50% of the injection pressure; due to the relatively fast condensing of the material, a short holding time is sufficient.
Plastic injection molding is an efficient and cost-effective method of producing medical and pharmaceutical parts to high levels of precision, accuracy, and quality. It is used to create components from medical devices and equipment to laboratory tools and testing instruments. The following page provides an overview of the plastic injection molding process and its essential role in the medical and pharmaceutical industries.
As indicated above, injection molding is one of the most efficient and cost-effective ways of manufacturing parts that meet the strict specifications and standards of the medical and pharmaceutical industries. For example, the process is often used to manufacture the small, high-precision components found in diagnostic testing kits, such as the lateral flow in-vitro diagnostic test cartridge produced in large quantities by our team.
The injection molding process accommodates a wide range of plastic materials, making it well-suited to produce medical and pharmaceutical parts from whatever medical-grade plastic is required for the project. There are numerous plastics suitable for medical injection molding operations, each of which offers unique properties and performance characteristics. Common plastic material options for medical injection molding include:
Given the broad selection of suitable material options available, the first step in choosing a material for a project is narrowing down the list to the material family that fulfills the most part requirements (e.g., tensile strength, temperature load rate, etc.). From there, it is much easier to select the grade that best suits the project. Online databases—such as UL Prospector, MAT Web, and The British Plastics Federation—can provide information about materials that can further facilitate the selection process.
As mentioned above, there are many types of plastics available for medical injection molding operations. Each plastic possesses distinct qualities that influence how it performs in specific applications. Some of the key factors to consider when choosing between the material options include:
At Sterling Healthcare Manufacturing, we specialize in full-service, turnkey plastic component injection molding solutions. Our comprehensive part manufacturing capabilities allow customers to maintain oversight over the production of their parts, resulting in greater transparency and accountability. Additionally, we maintain ISO 9001:2015, our new ISO 13485 cleanroom certification and employ the use of FDA/medical-grade materials to ensure our injection molded components fully meet the strict specifications and standards of the medical and pharmaceutical industries.
0.7% to 2.0%, or 30% glass fiber, 0.4% to 0.7%; if the temperature is more than 60 °C, the product should be gradually cooled; gradually cooling can reduce the shrinkage after molding, that is, the product performs better. Dimensional stability and small internal stress; steam method is recommended; nylon products can be inspected by melt flux
Medical and pharmaceutical products play a vital role in the health and safety of patients. As such, ensuring the quality of each product and its individual components throughout the manufacturing process—from design to final inspection—is essential. For this reason, it is vital to partner with an experienced medical/pharmaceutical component manufacturer that emphasizes quality and offers complete part traceability from start to finish.
Advancements in material manufacturing techniques and technologies have led to the widespread use of plastics in modern manufacturing operations. In the medical and pharmaceutical industries, plastics are often used alongside the injection molding process to produce prototypes and full-production units of medical device and equipment components. As newer plastic materials and component designs are developed, injection molded plastics have increasingly contributed to lower infectious disease rates, better pain management, and lower medical costs.
To see an example of our work in the medical industry, check out this case study documenting how we optimized the mold design for a polystyrene diagnostic kit. You’ll also learn about how our custom capabilities — such as machine vision inspection — guarantee quality, cost efficiency, and 100% reliability for every order we complete.
Gate system point type, latent type, chip type and sprue can be used; blind hole and gate socket are recommended to break the cooling head; hot runner can be used; hot runner should be provided due to the narrow processing temperature range of the melt Closed loop temperature controlMachine downtimeNo need to clean with other materials; the melt remains in the barrel for up to 20 minutes, after which thermal degradation is easy to occur
Residual material amount 2~6mm depends on metering stroke and screw diameterPre-baking Drying at 80 ° C for 4 h, except directly feeding from the charging container; nylon is absorbent, should be stored in the moisture-proof container and closed hopper; water content of more than 0.25% will cause molding changes
GETTING A QUOTE WITH LK-MOULD IS FREE AND SIMPLE.
FIND MORE OF OUR SERVICES:
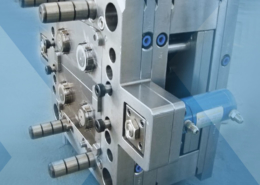
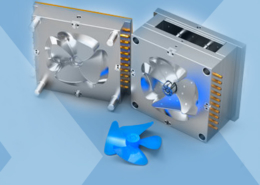
Plastic Molding

Rapid Prototyping
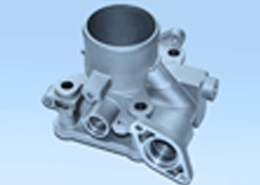
Pressure Die Casting
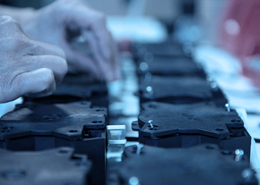
Parts Assembly
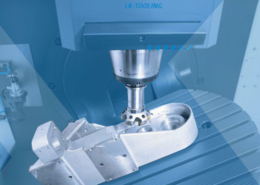