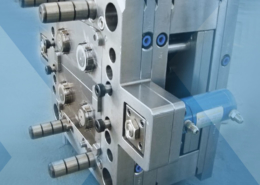
Plastic injection molding Precise and fast to small series - aluminum mold for p
Author:gly Date: 2024-10-15
Low volume injection molding is a versatile manufacturing process that finds applications across various industries. Here are some of the typical applications of this process:
Find out how Qenos Injection moulding resins have been used in a variety of in challenging real life customer applications
Choosing the suitable material is crucial to achieving the desired outcome in low volume injection molding. Factors to consider the material’s properties include strength, flexibility, durability, and compatibility with the injection molding process. Material selection can affect the final cost and quality of the parts produced.
Low volume injection molding offers flexibility in design, allowing for quick iterations and product changes without incurring significant costs.
Low volume injection molding is a cost-effective way of producing small quantities of plastic parts with consistent quality. This process offers many advantages over other manufacturing methods, including fast turnaround time, flexibility in design, and consistent quality. By considering factors such as material selection, design optimization, tooling costs, and production volume, businesses can decide whether low volume injection molding is the right choice for their manufacturing needs. With the right approach, low volume injection molding can effectively bring new products to market quickly and cost-effectively.
The custom tooling used in low volume injection molding produces consistent quality parts, ensuring that each piece is identical to the previous one.
For more about understanding low volume injection molding for small batch plastic parts production,you can pay a visit to Djmolding at https://www.djmolding.com/low-volume-injection-molding/ for more info.
Reduced tooling costs Short lead time Quick iterations Low risk for product design changes Flexible production capabilities Lower cost for prototyping Reduced waste material
Qenos is the leading supplier of polyethylene injection moulding resins to the Australian market. Our world class injection moulding resins are used in a variety of application including caps, pails, crates, sealant cartridges, mobile garbage bins and produce bins. A full range of HDPE, LDPE and LLDPE grades are available across the Melt Index and density spectrum. In addition, Qenos also distributes a number of speciality polymers suitable for injection moulding. Injection Moulding Grades Qenos manufactures a range of HDPE, LDPE, LLDPE grades for injection moulding. Find data sheets, SDS and application information. Info Injection Moulding Video Qenos produces a wide range of injection moulding grades for lids and caps, sealant cartridges, crates, produce bins, mobile garbage bins and more Info Injection Moulding Troubleshooting Guide A comprehensive polyethylene injection moulding troubleshooting guide to help optimise your operations. Find solutions to your technical challenges. Info Injection Moulding Technical Guide A comprehensive guide to injection moulding polyethylene including processing variables, mechanical properties and mould design Info Injection Moulding Case Studies Find out how Qenos Injection moulding resins have been used in a variety of in challenging real life customer applications Info
In the medical industry, manufacturers require the quick and consistent production of small batches of custom parts. Low volume injection molding is a cost-effective way of making medical devices such as surgical instruments, implants, and drug delivery devices.
Low volume injection molding is a cost-effective way to produce small quantities of plastic parts. The tooling costs are significantly lower than other manufacturing methods, and the production process is efficient.
Manufacturers require the quick and cost-effective production of small quantities of custom parts in the electronics industry. Low volume injection molding can produce parts such as electronic device housings, connectors, and switches. This process offers high precision and repeatability, essential in the electronics industry, where parts must fit perfectly.
Designers create custom tooling to produce a mold capable of producing consistent quality small quantities of plastic parts. Typically, manufacturers make the tooling from steel or aluminum, designing it to withstand the high pressures and temperatures of the injection molding process. The design of the mold is crucial for ensuring the quality of the final product, and it must consider factors such as geometry, material flow, and cooling time.
Article Original From: https://www.djmolding.com/understanding-low-volume-injection-molding-for-small-batch-plastic-parts-production/
The plastic material is melted and injected into the mold under high pressure. The mold is then cooled to allow the plastic to solidify and take the shape of the mold. Once the plastic hardens, someone opens the mold and removes the part.
Low volume injection molding is a manufacturing process that allows for producing small quantities of plastic parts with consistent quality. The process involves the creation of custom tooling, injection molding of plastic material into the mold, and quality control measures. Let’s explore each step in detail:
Quality control measures are implemented throughout manufacturing to ensure the parts meet the required specifications. Inspectors examine the tooling to ensure it is in good condition and capable of producing high-quality parts. Operators monitor the quality of the materials used in the injection molding process to ensure consistency. Inspectors examine finished pieces to ensure they meet the required dimensional and visual specifications.
Design optimization is vital to achieving the best possible low-volume injection molding results. Designing efficient and cost-effective parts that meet functional requirements is the goal. Design optimization can minimize tooling costs and reduce production time.
A comprehensive guide to injection moulding polyethylene including processing variables, mechanical properties and mould design
Low volume injection molding is ideal for producing small batches of parts quickly and cost-effectively. However, it is vital to consider the production volume when choosing this manufacturing method. As the production volume increases, other manufacturing methods, such as high volume injection molding or other processes, may become more cost-effective.
Low volume injection molding is a manufacturing method that has become increasingly popular recently, and this process is ideal for producing consistent quality small quantities of plastic parts. This blog post will explore the basics of low volume injection molding, including its benefits, how it works, its advantages, applications, and factors to consider when choosing this manufacturing method.
Low volume injection molding offers many advantages, but there are also important factors to consider when choosing this manufacturing method. Here are some of the critical factors to keep in mind:
Low volume injection molding requires businesses to invest in custom tooling, which can result in a significant upfront cost. However, the cost per part decreases as the production volume increases.
Low volume injection molding produces small batches of custom plastic parts for consumer goods such as toys, sporting equipment, and household appliances. This method offers a cost-effective way of creating pieces with complex shapes and designs and with consistent quality. It also allows for producing unique or custom features unavailable in the mass market.
A comprehensive polyethylene injection moulding troubleshooting guide to help optimise your operations. Find solutions to your technical challenges.
Qenos manufactures a range of HDPE, LDPE, LLDPE grades for injection moulding. Find data sheets, SDS and application information.
Qenos produces a wide range of injection moulding grades for lids and caps, sealant cartridges, crates, produce bins, mobile garbage bins and more
The lead time for low volume injection molding is much shorter than other manufacturing methods. Manufacturers create the tooling quickly and execute the production process efficiently, resulting in faster turnaround times.
Low volume injection molding is a manufacturing process that involves the creation of custom tooling to produce small quantities of plastic parts with consistent quality. It is a cost-effective way to make small batches of parts for different industries.
In the aerospace industry, manufacturers require the production of custom parts in small quantities. Low volume injection molding can produce parts such as brackets, knobs, and handles for aircraft interiors. The process offers a high design flexibility, essential in the aerospace industry, where functions must meet specific weight, strength, and durability requirements.
GETTING A QUOTE WITH LK-MOULD IS FREE AND SIMPLE.
FIND MORE OF OUR SERVICES:
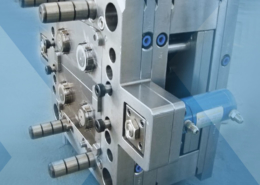
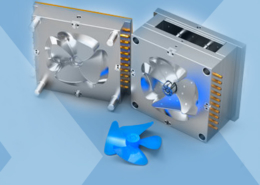
Plastic Molding

Rapid Prototyping
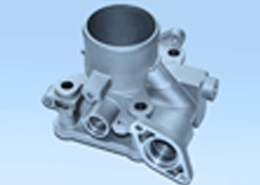
Pressure Die Casting
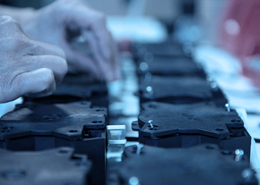
Parts Assembly
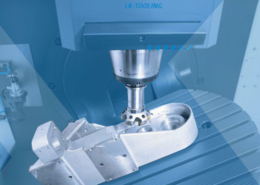