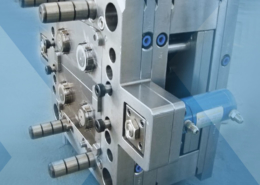
Plastic Injection Molding Manufacturing Company - custom plastic injection mould
Author:gly Date: 2024-10-15
When designing plastic products and components, one of the most challenging decisions is determining the right method of manufacturing them. Your goal is to have a durable, high-quality finished product while minimizing costs and speeding up efficiency and the right manufacturing method is key to meeting these goals. There are six main types of plastic manufacturing, and our thermoforming company in North Carolina is looking at each type and the associated benefits they offer.
Compression molding is most often used with thermoset plastics whose chemical structure changes when melted and cooled to create a hard, rigid final product. Plastic resin is heated to a soft, almost "putty" state where it's not quite liquid, then it's placed into a heated mold. The putty is then pressed into shape by the mold and allowed to cool.
At Advanced Plastiform, Inc., we specialize in heavy-gauge thermoforming and injection molding. Our experienced team includes engineers and designers as well as manufacturers, all of whom are dedicated to helping you meet your goals. Our company works with industries across the Mid-Atlantic and Southeast, including North Carolina, South Carolina, Pennsylvania, Maryland, Tennessee, Georgia, and Virginia. To learn more, call us at 919-404-2080 or fill out the contact form to get started.
Injection molding is a plastic manufacturing method in which a thermoplastic is melted to a liquid, then injected into a double-sided mold using a highly pressurized injector. The plastic coats and fills the mold to create the needed shape, and is then cooled and ejected for finishing.
Rotational molding, or "roto-molding," involves pouring melted plastic into a mold, which is then rotated at a high speed. This coats the plastic evenly along the walls of the heated metal mold, leaving the interior hollow. This method is primarily used for large, hollow-walled containers, storage bins, and even kayaks.
Extrusion molding is primarily used to manufacture long, straight pieces, such as tubing, hoses, or pipes. This method involves forcing liquid plastic into a die to form a shape. While round pieces are common, t-shapes, l-shapes, and squares are also achieved, depending on the shape of the die. Many thermoplastics can be used during extrusion molding.
Thermoforming involves heating a large sheet of plastic until it is soft and flexible, then stretching it over a single-sided, custom mold. Vacuum pressure or compressed air presses the thermoplastic tightly against the mold, creating the desired shape.
When you contact us our experienced team will process your LDPE injection molds order quickly and economically without sacrificing quality.
CTG is a one stop injection molding shop for manufacturing, sourcing, packaging and shipping parts on time, every time, even in an emergency.
We service the Houston, Texas, Arkansas, Oklahoma, Louisiana, Gulf Coast regions, and all of North America including Canada and Mexico.
Since 1988, Advanced Plastiform, Inc., has been providing superior custom plastic molding and fabrication services to companies in North Carolina, South Carolina, Maryland, Georgia and Pennsylvania. Contact us to make an appointment Mon-Fri 8-5.
In addition to LDPE injection molds and reverse engineering we also provide emergency manufacturing and delivery, engineering, PTFE processing, Plastics Injection Molding, PEEK Processing, Rubber Molding and value-added manufacturing solutions.
In addition to LDPE injection molds we specialize in Oil & Gas Seals, Viton Seals, Kalrez Seals, Custom Seals, High Temperature Seals, Viton Molding, FFKM Molding, PEEK Molding, PTFE Molding, 3D-Printing and many other high-performance products and services detailed on our website.
For your custom LDPE injection molds design, or reverse engineering, our exemplary service and efficient production ensures prompt deliveries coupled with outstanding service.
Blow molding is similar to injection molding as the plastic is heated to a liquid state and injected into a mold. However, once the plastic is placed in the mold, air is injected into the plastic, inflating it so that it presses against the walls of the mold and achieves the desired shape.
Injection molding provides a low cost at moderate to large quantities. Almost any 2D or 3D shape can be achieved for making extremely versatile plastic parts with an excellent finish. Commonly used materials include PEEK, Nylon, Acetal, Polycarbonate, Polystyrene, Acrylic, PTFE, ABS, PVC.
Our LDPE injection molds emergency manufacturing and delivery is here to help when your equipment breaks down, power goes out, or you are running over capacity.
When designing custom LDPE injection molds, the staff at CTG, Inc. helps customers through the complete life cycle of customer input and design, prototyping (optional), tooling/mold production, and production. We may also make suggestions on seal modifications to design for assembly which will aid in installation, cleaning, and repairs.
With over 100 years of engineering expertise we are dedicated to offering the highest quality LDPE injection molds and other products.
From communication to delivery, our team works efficiently to provide the services you need through interaction and input from our clients. Every product we create is always made from top-quality materials on which you can depend.
In an economy that requires the balance of inventory and production, it's difficult to stay prepared when unforeseen issues result in equipment breaking down, power going out, or running over capacity. CTG, Inc. helps you avoid loss of production. We work around the clock to get your LDPE injection molds completed promptly while maintaining our high standards in quality and precision.
No sample seal? No Problem! Our team can reverse engineer even the largest of OEM seals and provide you with a proper replacement design.
Our products and services have been a top choice for chemical processing, oil and gas, semiconductor, pulp and paper, medical, industrial, research & development, OEM, and other industries.
GETTING A QUOTE WITH LK-MOULD IS FREE AND SIMPLE.
FIND MORE OF OUR SERVICES:
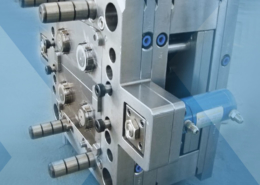
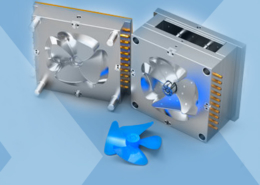
Plastic Molding

Rapid Prototyping
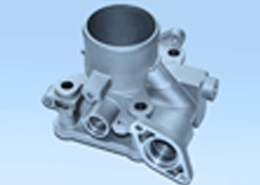
Pressure Die Casting
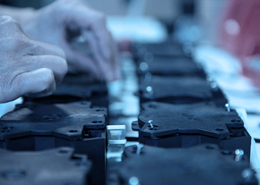
Parts Assembly
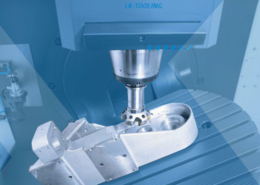