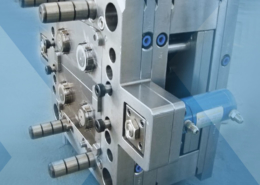
Plastic Injection Molding Manufacturing Company - best injection molding compani
Author:gly Date: 2024-10-15
Plastic is a common material in automotive manufacturing. It is known to make car units lighter. Car parts like fenders, hoods, grills, paneling, and door covers are made from this process. These parts are made more efficient to meet the specific preferences of reputable car brands worldwide.
By using exact mold designs and accurate material injection, rapid injection molding minimizes defects, ensuring that each piece meets the required specifications.
Large-part injection molding is a prominent technique for making high-quality large-sized items. It is a reliable method in plastic manufacturing, meeting the many unique demands of various industries. With many advantages tied up to its name, it is one of the groundbreaking processes in the industry.
In today’s fast-paced manufacturing world, efficiency and precision are paramount. One technology that has revolutionized production is rapid injection molding.
This innovative method blends the speed of prototyping with the scalability of mass production, offering manufacturers a competitive edge.
Depending on the complexity of the part and the process used, molds can be designed and produced in as little as a few days.
Before adopting rapid injection molding, manufacturers should consider several factors that can impact the success of the process.
Precision is a hallmark of rapid injection molding. With advanced technologies like high-speed machining and 3D printing, manufacturers can achieve tight tolerances and complex geometries that would be difficult or time-consuming with other methods.
Careful consideration is important to create the ideal plastic item, whether it is used for automotive or consumer goods industries, understanding various methods to make large plastic parts is important.
At Richfields Corporation, you can experience exceptional services for any large plastic components. Our large-part injection molding in China is one of the best in the industry. With over two decades in the field, we take pride in our accumulated knowledge and experience in plastic manufacturing.
Discover the advantages of large-part injection molding with Richfields Corporation in China. Our state-of-the-art facilities and experienced team ensure the highest quality and precision for your large-scale projects. Contact us today to learn more about our services and how we can meet your specific molding needs. Let's bring your vision to life with expert craftsmanship and reliable solutions!
Rapid injection molding is not the only manufacturing method available, and it is essential to understand how it compares with other popular techniques, such as CNC machining and traditional injection molding.
This speed advantage is especially beneficial for industries that demand fast turnaround times, such as consumer goods and electronics, where product lifecycles are shorter, and time-to-market is crucial.
China sits at the center of the global plastic manufacturing industry. It is only expected that their companies have the best tools. When you work with them, your product is made with advanced technology. These pieces of equipment are developed specifically to make processes more efficient without sacrificing quality. With their high technology, you can easily meet stringent standards.
Speed is one of the key differentiators of rapid injection molding, and it directly impacts production cycles. Compared to traditional injection molding, which can take weeks or even months to create a mold, rapid injection molding significantly reduces lead time.
Despite its many advantages, rapid injection molding comes with its own set of challenges. Being aware of these issues can help manufacturers avoid pitfalls and streamline the process.
Large-part injection molding in China offers flexibility and precision. It offers high-quality plastic parts for every purpose across many industries in global markets.
Additionally, high-speed CNC machining plays a pivotal role in creating mold inserts with precise tolerances, ensuring that every part meets strict quality standards.
This precision also leads to better product performance, especially in applications where detailed features or intricate designs are essential.
Large-part injection molding in China is a cost-effective method. It is designed to meet every need of the product. That is why it is often done with vigorously developed machinery. With its equipment, it can take care of most of the steps required for a high-stand plastic component. It is a great investment and reduces long-term labor costs.
Optimization is key to ensuring both efficiency and quality in the rapid injection molding process. By fine-tuning various aspects of the procedure, manufacturers can maximize their return on investment while producing high-quality parts.
The gas-assisted technique is a low-pressure process. It combines conventional injection molding and the application of pressurized inert gas. The molten material does not completely fill up the size of the mold. The empty space is used to allow the gas to manipulate the material from the inside. Through strategically placed gas channels, the molten plastic is shaped by the gas to reach the mold’s walls.
Plastic is a durable material since it withstands elements from corrosion to impact. It is the perfect material to make appliances including washing machine bodies, fridge interior and outer shells, air conditioning casings, and more. With large-part injection molding in China, your lifestyle is further enhanced with convenience.
Several advanced technologies support the rapid nature of this injection molding process, enabling manufacturers to create highly accurate parts in a fraction of the time required by traditional methods.
The decision to choose rapid injection molding over other manufacturing methods depends largely on the specific needs of the project.
ACIS®, Autodesk Inventor®, CATIA® V5,Creo™ Parametric, IGES, Parasolid®, Pro/ENGINEER®,Siemens PLM Software’s NX™, SolidEdge®, SolidWorks®, STEP
Large-part injection molding in China is a specialized field in plastic manufacturing. It offers numerous advantages in producing large-scale plastic components. It is an innovative solution for any plastic item, from plastic pallets to car bumpers. As a sought-after service for making sizeable products, it is an ideal choice for businesses across various industries looking for reliable production capabilities.
In a recent exploration by 3ERP, the numerous advantages of rapid injection molding are meticulously examined, highlighting its transformative impact on manufacturing processes.
Crafting a sizeable plastic part requires more than one strategy. There are other ways to mold molten plastic into the ideal component. While molds and their designs are pivotal, how it is processed is also necessary. It is the same with large-part injection molding.
The rapid injection molding process follows a structured series of steps, ensuring speed and accuracy from design to production.
This method stands out as a pivotal solution for industries aiming to optimize their production cycles and respond swiftly to market demands.
Rapid injection molding offers a range of advantages that make it an attractive option for both prototyping and short-run production.
As advancements continue to push the boundaries of this technology, manufacturers can expect even greater efficiencies, better materials, and more sustainable processes in the future.
Rapid injection molding is an accelerated version of traditional injection molding, designed for quick production of plastic parts using pre-engineered molds.
Design is a critical aspect of the rapid injection molding process, as optimizing the design can improve efficiency and product quality.
Unlike conventional methods, this process focuses on reducing tooling time while maintaining the precision of the final product.
This innovative approach not only accelerates production timelines but also significantly reduces costs, offering a competitive edge in today’s fast-paced market.
Various pieces of sports equipment are manufactured from large-part injection molding in China. It can mostly be seen in gears needed for water sports, such as kayaks, canoes, surfboards, and rowing shells. A combination of polyethylene, high-impact ABS, and acrylic are typically involved in making these sports materials.
Choosing the right material is essential for achieving the best results in rapid injection molding. Different materials offer unique properties, making them more suitable for specific applications.
As technology continues to evolve, rapid injection molding is expected to become even more efficient and versatile. Several advancements in materials, processes, and machinery are on the horizon, promising to further revolutionize the industry.
The electronic industry uses this type of injection molding for the mass production of large-part electronic components. These could be battery encasings, generator shells, computer monitor bezels, and more. Plastic is the ideal material since it seals water off and resists UV rays. These two qualities are essential to make electronic products safer to use.
Large-part injection molding is specifically developed to produce massive-sized components. It involves injecting molten plastic into a mold reflecting your ideal design. Robust machinery is required for this technique. Pieces of equipment must withstand the great tonnage or weight of the material. Using and handling these resources makes it a specialized service in manufacturing.
Large-part injection molding in China also uses hot-runner and cold-runner systems. These two methods are basic techniques in plastic manufacturing, in which both use molten material. The difference is the temperature needed to transfer the viscous polymer. The former method requires intense heated runners. The latter, however, does not need high temperatures to move the molten material.
By understanding when and how to implement rapid injection molding, businesses can stay competitive and meet the ever-evolving demands of their industries.
One of the standout reasons to choose rapid injection molding is its flexibility. This process enables companies to experiment with different materials, design iterations, and product variations quickly, allowing for faster adjustments and improvements without the lengthy setup times of traditional methods.
When working with this specialized method, it is only right to partner with the best team. Our experts at Richfields Corporation are highly knowledgeable about large-part injection molding in China. Whether you are looking to satisfy automotive or consumer goods specifications, you are thoroughly guided by our professionals. Equipped with advanced technologies and powerful machinery, your product can easily take shape with us.
Insert molding requires the addition of inserts in the molding process. These inserts are metal material and are placed into position in the cavity before injecting the molten plastic. When the general process is done, the metal insert is not removed. Rather, it becomes a part of the plastic component. It is the ideal process in creating strong, durable, and lightweight plastic components.
Innovative solutions are not unfamiliar to large-part injection molding in China. Being the hub of world-class plastic manufacturers, your plastic products have access to many resources. From the best machinery and a diverse range of materials to signature techniques and unprecedented expertise, you are extensively guided throughout the production.
Rapid injection molding offers a variety of benefits, making it an appealing choice for manufacturers. The core advantages revolve around speed, precision, and the ability to produce high-quality parts in shorter lead times compared to traditional injection molding.
Its ability to quickly produce high-quality parts, especially for prototypes and small production runs, makes it an invaluable tool for industries like automotive, healthcare, and consumer goods.
Large-part injection molding in China is designed to satisfy unique applications. Whether they are plastic decking or electronic casings, large-format items can be carefully made to accentuate every feature. Every intricate design can be emphasized in its production, ensuring your specifications are met. This technique makes certain of the quality and performance of every product.
By integrating rapid injection molding, companies can achieve enhanced precision and scalability, ensuring high-quality outputs with shorter lead times.
Large part injection molds are significantly focused areas in plastic manufacturing. Due to the high volume of materials needed and the use of robust equipment, there are many at stake in its production.
As industries push for faster turnarounds without compromising on quality, rapid injection molding becomes a go-to solution. Its relevance spans across multiple sectors, helping businesses meet tight deadlines while maintaining the high standards required for complex products.
You can choose structural foam molding for your large-part injection molding in China. It involves the combination of a polymer and inert physical gas or a chemical agent, which are thermoset polymers and nitrogen gas. This technique produces a sponge or honeycomb-like core with high-density outer skin. With this texture incorporated into the product, they are lighter than any solid components.
Many industries have adopted rapid injection molding due to its speed, precision, and flexibility. These sectors require quick turnarounds and high-quality products to remain competitive in the market.
GETTING A QUOTE WITH LK-MOULD IS FREE AND SIMPLE.
FIND MORE OF OUR SERVICES:
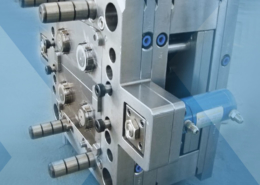
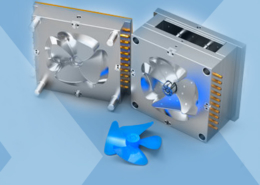
Plastic Molding

Rapid Prototyping
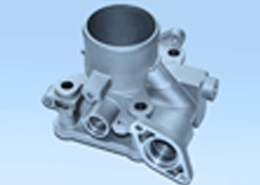
Pressure Die Casting
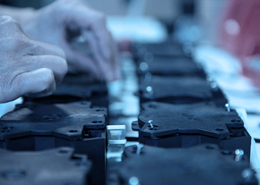
Parts Assembly
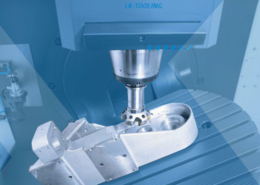