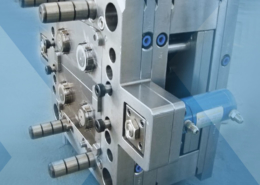
Plastic Injection Molding for Medical Devices - medical plastic injection
Author:gly Date: 2024-10-15
The amount of material injected (shot size) is determined by the size of the injection chamber, regulated by a limit switch controlling how far back the screw travels. High back pressure increases shot size.
Improper injection molding back pressure can have significant consequences. Let’s explore the effects of both excessive and too-low back pressure:
2 shot plastic injection molding enables the use of dissimilar resins to be used in a multi-part assembly. In some instances, a 2 shot mold application may include different colors and also soft and hard materials assembled together in in a single part. Some of the benefits of 2 shot plastic injection molding include elimination of post-molding assembly, fewer injection molding machines to make a single part and reduced part handling by operators by utilizing a single molding operation.
Your Name: Your Email: Resin: Estimated Life of Program: Estimated Annual Volume: Estimated Order Quantities (if Low Volume Molding Project): Target Price (Tooling/Piece Part): Message Attach a File ❌ ❌
The injection mold structure and design directly influence various aspects of the final product, including its dimensional accuracy, surface finish,
Diagram illustrating backpressure. P2 indicates the pressure exerted by the melt on the screw. P1 is the backpressure applied.
Injection pressure is the pressure of the melt acting on the head of the screw during injection molding. This pressure is crucial in ensuring the material fills the mold completely and uniformly. It impacts the flow rate and velocity of the plastic.
In simple terms, adjusting back pressure ensures that the screw moves at the right pace, maintaining the harmony of the injection molding process.
Injection molding back pressure does not raise the melt temperature. However, the melt temperature will increase with the increase of the screw speed. This is because 70%-90% of the energy needed to melt the plastic for the shot comes from the screw rotation.
In the injection molding process, there’s a critical factor known as “injection molding back pressure.” It directly influences the quality of the final product and production efficiency. In this post, we’ll explore what injection molding back pressure is, discover the impact on the molding process, understand injection molding back pressure purpose, discover how to set proper injection molding back pressure, and learn the impact of improper injection molding back pressure on molded parts.
Midwest Mold specializes in the design and build of 2 shot plastic injection molds and has successfully manufactured pre-production and production tooling for structural, water management, crash impact and noise reduction applications.
Injection molding is a cyclic process. In this process, in addition to back pressure, injection pressure, holding pressure, and clam pressure are involved. They are the important parameters for controlling product quality in the injection molding process.
Even with drying, air can be trapped in the melt, leading to imperfections. Back pressure aids in expelling trapped air through pressure gradients, enhancing the effectiveness of venting and preventing defects like air bubbles or voids in the finished product.
Clamp pressure is applied to the mold during the molding process. It is a measure of the force required to keep the mold closed and withstand the pressure exerted by the molten plastic material during injection.
Think of the screw as a revolving component, typically spinning at a rate of 20 to 60 revolutions per minute (rpm). This speed varies depending on the plastic’s characteristics and the specific process. The higher the screw speed, the greater the back pressure.
Back pressure compacts the molten material, bringing its molecules closer together. This enhances density, ensuring a uniform and high-quality product. The image below shows, that as the pressure gets increased the molecules move closer together.
By controlling the movement of the plastic within the mold, back pressure helps manage shrinkage. This ensures that the final part maintains its intended dimensions, free from distortions.
2 shot injection molding reduces the number of machines and molds required to mold two materials together into one part, and it minimizes part handling, all of which can add up to lower costs. In addition to financial benefits, 2 shot molding can provide:
The adjustment of injection molding back pressure should depend on the performance, drying conditions, product structure, and quality of the plastic raw materials. The back pressure is generally adjusted between 3-15kg/cm³. When the surface of the product has a little air, mixed colors, shrinkage, or the size and weight of the product change significantly, the back pressure can be appropriately increased. When the nozzle leaks glue, drools, the melt decomposes due to overheating, the product changes color, or the material returns too slowly, you may consider reducing the back pressure appropriately.
For questions regarding our quote form, data transfers or our FTP site for large files, please contact our data coordinator midwestmold@midwestmold.com.
Slow down the screw retreat speed to fully plasticize the melt in the barrel, increase the mixing uniformity of toner, color masterbatch, and melt, and avoid color mixing in the product.
Have you ever noticed a whitening phenomenon in PVC product whitening? Some of your transparent PVC products, like shower curtains
Injection molding flow marks are a common injection molding defect. While flow marks generally do not influence the structural integrity
In conclusion, achieving precision in the injection molding process is no small feat, and one of the key contributors to this precision is the fine-tuning of back pressure. The proper injection molding back pressure ensures that every product meets the highest standards of quality and consistency. At Zhongde, as a professional on-demand manufacturer, We strive for excellence at every stage of the injection molding process to meet our partners’ product requirements.
Injection molding back pressure, also referred to as plasticizing pressure, is the resistance encountered by the injection screw as it performs its critical role in the plasticization process. It’s defined as “the resistance of the screw to recover as the metering section pumps molten plastic through the non-return valve to the front of the screw.” In simpler terms, it’s the force created as the molten plastic is mixed and pushed forward, pushing back against the injection screw.
Back pressure is the resistance exerted on the back of the screw (screw retraction) during the plasticizing process. It is the core of the injection molding process and has a great relationship with the progress of the injection molding process. Screws play a big role in this process. The screw does most of the work in the process, especially in terms of its movement. Back pressure affects the entire injection process by affecting the screw.
Midwest Mold offers a cost-effective solution to challenges caused by parts that require the use of two different plastics. 2 Shot injection molding is a process that molds one part using two different plastic resins. This enabling technology allows you to use two colors of plastics or to integrate both hard and soft plastics into one part without any post-molding assembly.
Back pressure can increase the temperature of the melt, improve the plasticizing quality of the melt, and improve the fluidity of the melt when filling the mold. There will be no cold glue lines on the surface of the product.
Hold pressure equals 50% of injection pressure. It is the pressure applied to the material after injection to pack it into the mold and compensate for shrinkage. This pressure contributes to the solidification and cooling of the material, playing a key role in preventing defects and warping.
Back pressure is an essential timekeeper. It influences the timing of the injection molding process, ensuring that each step occurs at the right moment, contributing to precision and consistency.
With 2 shot molding, parts can include a clear window, integrated gaskets, movable segments, water shields, or sound or vibration reduction.
GETTING A QUOTE WITH LK-MOULD IS FREE AND SIMPLE.
FIND MORE OF OUR SERVICES:
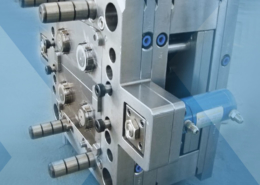
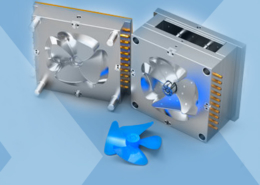
Plastic Molding

Rapid Prototyping
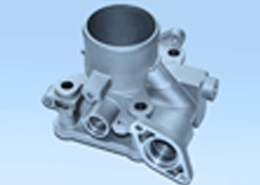
Pressure Die Casting
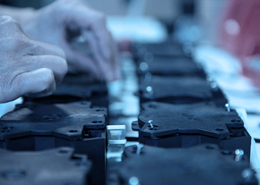
Parts Assembly
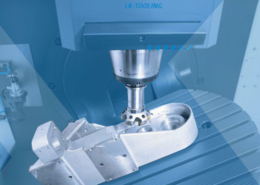