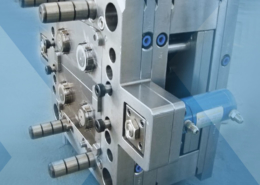
Plastic Injection Molding for Medical Device Industry - injection moulding medic
Author:gly Date: 2024-10-15
As a UK based manufacturer, we can offer help with reshoring to reduce lead-times and production delays of medical devices and components.
Injection molding process description: mold is a tool for producing plastic products. It is composed of several groups of parts, and this combination has a forming die cavity. During injection molding, the mold is clamped on the injection molding machine, the molten plastic is injected into the molding mold cavity, cooled and shaped in the cavity, and then the upper and lower molds are separated. The products are ejected from the mold cavity and left the mold through the ejection system. Finally, the mold is closed for the next injection molding. The whole injection molding process is cyclic.
All kinds of tools and products used in our daily production and life, ranging from the base and body shell of the machine tool to the shell of a embryo head screw, button and various household appliances, are closely related to the mold. The shape of the mold determines the shape of these products, and the processing quality and accuracy of the mold also determine the quality of these products. Because of the different materials, appearance, specifications and uses of various products, molds are divided into casting molds, forging molds, die-casting molds, stamping molds and other non plastic molds, as well as plastic molds.
Our team is committed to delivering the best plastic injection moulding service with dedicated project management from concept to finished product.
We will prepare a bespoke master validation plan and validation protocol for you including a full production part approval process (PPAP).
With ISO 13485 medical standard manufacturing and our new ISO 7 clean room (Class 10,000 clean room) for medical devices, we can help you design and develop high quality injection moulded products as cost effectively as possible. We can also reduce injection mould tool modification or repair times from weeks to just days and shorten the overall product development lead time.
OGM first started supplying medical device companies in the UK over 20 years ago. Our first cleanroom was built in 2000 and today we are one of the leading plastic injection moulders for medical devices and components.
We specialise in high-volume production of plastic parts using precision-controlled robotics. We invest heavily in the latest technology from 3D metal additive manufacturing to high-definition vision systems for inspection and quality control.
General definition of mold: in industrial production, various presses and special tools installed on the press are used to make metal or non-metallic materials into parts or products of the required shape through pressure. Such special tools are collectively referred to as molds.
We can support you through the entire process of bringing your product to market or upgrading and modifying existing products. All manufacturing, assembly, testing and validation is carried out at one of our UK sites in Oxford or South Wales.
To learn more about our plastic injection moulding services please call us on +44 (0)1865 844300 or you can email us at info@ogmmedical.com
OGM Medical is a UK based plastic injection moulding company supplying medical equipment manufacturers globally. We manufacture components and devices for a wide range of customers in the medical, pharmaceutical and life science sectors.
Our experienced team will work closely with the design team to transform your mould tool design into the highest quality injection mould tooling.
In recent years, with the rapid development of plastic mold industry and the continuous improvement of strength and accuracy of general and engineering plastics, the application scope of plastic products is also expanding, such as household appliances, instruments and meters, construction equipment, automobile industry, daily hardware and many other fields. The proportion of plastic products is increasing rapidly. A reasonably designed plastic part can often replace multiple traditional metal parts. The trend of plasticization of industrial products and daily-use products is rising.
Our tool designers can help you with everything you need to produce a successful injection mould design including the best choice of medical grade materials.
We guarantee complete quality control with full product inspection, testing and validation services accredited to medical standard ISO 13485, manufacturing standard ISO 9001 and environmental standard ISO 14001.
GETTING A QUOTE WITH LK-MOULD IS FREE AND SIMPLE.
FIND MORE OF OUR SERVICES:
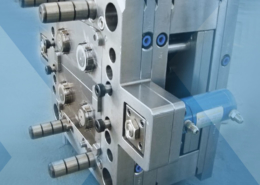
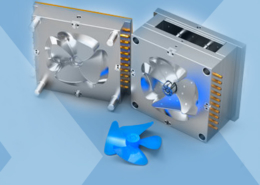
Plastic Molding

Rapid Prototyping
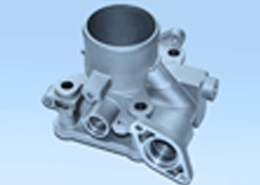
Pressure Die Casting
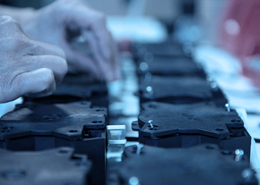
Parts Assembly
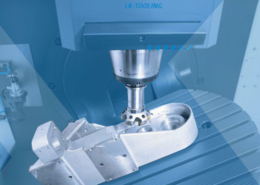