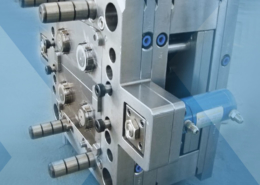
Plastic injection molding cost - EuroPlas - injection mold tooling cost
Author:gly Date: 2024-10-15
Plastic fabrication is essential to most industries. From polystyrene food packaging to industrial components made from engineering-grade PEEK, plastic fabrication contributes hugely to life as we know it. Without the ability to make plastic parts, we would need to develop radically new systems of production.
According to testing, the maximum temperature at which PEEK may be used continuously is 260 degrees Celsius, and its melting point is 341. Because of this, you can use it widely in sectors subject to high temperatures, such as the oil and gas and automotive sectors.
PEEK is impervious to moisture and many different solvents (even when subjected to them in high-temperature and high-pressure steam conditions). Thus PEEK is ideal for use in the oil and gas industry, where chemicals can eat away at subsea pipes, gears, and machinery. It is resistant to jet fuel, hydraulic fluids, and de-icers, all of which are used in the aerospace industry.
Advantages of rotational molding include simpler tooling, consistent wall thickness, and strong external corners. But the process can be slow, since the entire mold needs cooling before part ejection.
Nave ISK-8, Parque Industrial y Logístico Sky Plus, Avenida Mineral de Cinco Señores No.100, del Parque Industrial Santa Fe, Silao de la Victoria, Guanajuato, México
Welding is mostly associated with metals, but plastic welding is a useful plastic fabrication process for joining thermoplastic components not suitable for gluing or other assembly methods.
PEEK injection molding will be at the top of your list if you’re looking for an injection molding material that balances your performance needs, financial constraints, and environmental and sustainability goals.
Not to be confused with extrusion 3D printing, plastic extrusion is the process of forcing plastic through a die to make an elongated plastic part with a consistent profile.
PEEK may react with several acids, including nitric solid, sulphuric, and chromic acid. This eliminates its usefulness in a few situations.
PEEK has several uses in electrical engineering since it is a high-performance material that retains its mechanical properties even when heated. Therefore, we might utilize it in high-temperature electrical tools like soldering irons.
Several plastic resins are suitable for pultrusion, including polyester, polyurethane, and epoxy. Glass fibers are the most common reinforcing material.
But plastic fabrication comprises many different methods. Injection molding, plastic extrusion, and FDM 3D printing are all plastic fabrication methods, and there are many more besides. These different plastic fabrication methods suit different plastic parts, and choosing between them isn’t always straightforward. Budget, part design, and material are just some of the factors that go into choosing a plastic fabrication method.
Selective laser sintering (SLS) is a plastic fabrication process and another form of 3D printing. It is principally used to make nylon parts.
More so than FDM or SLA, SLS is considered an industrial additive manufacturing process and is popular in the automotive industry.
With high-performance features, PEEK is one of the most popular plastic injection molding materials today because of its excellent all-around properties, which may allow it to replace traditional materials like metals and ceramics in many applications. Presently, its most common applications are in the aerospace, automotive, electrical, electronic, and medical device industries.
During this plastic fabrication process, the operator pours urethane casting resin into a silicone mold; a vacuum then removes air pockets and bubbles, resulting in an exceptionally smooth finished part. The urethane parts are then cured in an oven.
Fused deposition modeling (FDM) is the most common 3D printing process for plastic fabrication. It works with common thermoplastics like ABS and PLA, as well as advanced materials like PEEK.
PEEK may be reprocessed several times without changing in any noticeable way because of the extreme stability of its molecules. Companies may reduce their waste management costs while still accomplishing their environmental goals.
Medical analysis instruments, such as endoscope components and dental instrument cleaners, can all be made from autoclave-safe PEEK. With its high strength and low solubility, PEEK has also been used in liquid chromatography columns, tubes, and instrument analytical accessories. Due to its biocompatibility, PEEK has also primarily supplanted titanium as the metal of choice for artificial bone.
Our experts have compiled the following information about PEEK to help you decide whether it is suitable material for your project.
While PEEK naturally has poor resistance to ultraviolet (UV) radiation, this may be remedied by using a carbon addition in the material’s composition.
The plastic fabrication method technique requires an oven and a mold. During the process, the plastic sheet is heated until pliable; it is then stretched over a mold — typically using a vacuum — before being trimmed and cooled.
3ERP is a plastic fabrication expert offering prototyping and low-volume production using a number of plastic fabrication technologies. Get a free quote today.
This article looks at 12 different plastic fabrication methods, explaining their basic processes and why they are useful. For each plastic fabrication method, we will give some examples of how it can be used to make end-use parts.
Several types of high-performance polymers may only fulfill a single need, such as resistance to chemicals or extreme temperatures. On the other hand, most of them fall short of meeting different standards, such as resistance to wear or mechanical strength.
Tensile strengths of 29000 psi at 299°C are possible for PEEK-based composites reinforced with carbon fibre. In this way, it outperforms nylons, acetal (PolyOxyMethylene or POM), polyesters, and polycarbonates in terms of strength and stiffness.
Additionally, PEEK does not require metal machining or thermoset curing to be mass-produced via injection molding, which reduces the number of processing steps required. In the end, you’ll save money and time thanks to this. In harsh environments, PEEK injection molding typically performs better than metal. Because of this, it is used frequently in the manufacture of the airplane and car parts, as well as medical and industrial components, semiconductors, and electrical and electronic gadgets.
Blow molding is a plastic molding process that is less widely used than injection molding. It has three distinct variants: extrusion blow molding, injection blow molding, and injection stretch blow molding.
En PAEK (PolyArylEtherKetone) category is the most prominent of the few high-performance polymers, with PEEK (PolyEtherEtherKetone) being the most prevalent.
PEEK may serve dependably within the human body for long periods since it is non-toxic and does not harm living tissue. The quality makes it so useful for usage in medical implant components. However, due to its chemically inert and physiologically unresponsive nature, PEEK has a limited ability to attach to bone tissue after implantation in vivo.
The plastic welding process has a huge number of variants, including hot gas welding, speed tip welding, and contact welding. The majority of variants involve preparing the surface of the plastic, applying heat and pressure, then cooling.
SLA produces brittle but exceptionally smooth parts, which can also be transparent. It is often used for prototyping but also has applications in dentistry in jewelry.
This high-volume plastic fabrication process works by heating plastic in a barrel, then forcing it — using a reciprocating screw — into a die, giving it its final shape with a continuous profile. The resulting plastic extrusion hardens as it cools down.
In place of metal, PEEK resin may make lighter, fatigue-resistant, and oil-free components. This includes the separating claws of copiers, special heat-resistant bearings, chains, gears, and so on.
Specialize in CNC machining, 3D printing, urethane casting, rapid tooling, injection molding, metal casting, sheet metal and extrusion
Stereolithography (SLA) is a different form of plastic 3D printing that works with photopolymeric resins instead of thermoplastic polymers.
Plastic CNC machining is a very popular plastic fabrication process. It encompasses CNC milling, CNC turning, and other related processes.
Studies have demonstrated that PEEK is more durable than other polymers and certain metals. PEEK is resistant to creep deformation under extreme loads and temperatures. Its low friction coefficient resists wear and tear and generates less commotion. Because of these advantages, it is an excellent option for use in piezas para automóviles. PEEK also performs very well when tested for fatigue from repeated pressure and stress, another wear indicator. Because of its lower weight compared to comparable metals, it finds use in the transportation industry and beyond, particularly in cars and planes, where it helps save fuel. PEEK’s exceptional durability makes it an excellent choice for creating artificial organs and other medical devices.
Injection molding is suitable for a huge variety of materials and parts. Parts must have thin and consistent walls but can otherwise assume various shapes and sizes.
Common plastic extrusion materials include polyethylene, polypropylene, acetal, and nylon. The process also has variants like blown film extrusion and tubing extrusion.
This plastic fabrication processes works using a mold and a molten thermoplastic tube called a parison (instead of fully melted pellets). Pressurized air enters the parison, causing the plastic to expand and touch the internal walls of the mold, eventually assuming the shape of the mold cavity.
Rotational molding is another plastic molding process — one that uses high temperatures and low pressure to form plastic parts. It works by rotating a mold to move the plastic material around inside.
The plastic fabrication technique of pultrusion is suited to fiber-reinforced plastics. During the process, a roll of reinforced fibers is pulled through a tank of plastic resin, which impregnates the fibers, and then through a heated die, giving the fiber-reinforced resin its custom profile.
SLS is a powder bed fusion process. It works by using a laser to selectively sinter 2D shapes in plastic powder, layer by layer, building a complete plastic part. It is broadly similar to the metal additive manufacturing process of selective laser melting (SLM). An advantage over other plastic 3D printing methods is that it does not require support structures.
Thermoforming is a type of plastic fabrication that resembles molding but which uses gently heated plastic sheet instead of fully molten plastic.
Although different machines work in different ways, plastic machining generally entails cutting away sections from a plastic workpiece using either manual or computer-controlled cutting tools. Machining is highly accurate, works with a range of plastics, and is better than molding for making thick-walled parts.
PEEK may still be utilized in certain airplanes despite aluminum being the material of choice in the aerospace industry due to its reduced weight. PEEK has better recyclability than aluminum, but it is more expensive to make, which is the material’s only real drawback.
It works by selectively curing photopolymeric resins using a light source such as a laser. (Digital light processing, a related technology, used a projector instead.) Parts are printed layer by layer as the print bed moves through the resin vat.
This fast plastic fabrication method works by heating plastic pellets until they melt, then forcing the molten plastic into a metal mold using a reciprocating screw. The molten material cools down, solidifies, and assumes the shape of the mold cavity. The solid part is then ejected from the mold.
You should calculate how much of a return on investment PEEK injection molding will deliver in light of its more excellent price, even though it will enable you to make lighter, stronger, and more chemically resistant components that will last longer. Prototool‘s material selection experts are here to provide a hand. With our help, even the most complex products may be designed and manufactured in weeks and brought to market.
PEEK, or polyetheretherketone is a semi-crystalline polymer and a high-performance engineering plastic. This material is biocompatible, has a high melting point (343°C), and has excellent mechanical properties. It is presently a popular research injection molding material. The advantages, features, and potential uses of PEEK injection molding are briefly discussed in this post.
Among these qualities, PEEK excels in mechanical, wear, heat, and chemical strength. It can be recycled and repurposed without much hassle. High purity, corrosion resistance, and electrical insulation are additional features.
FDM works by heating up extruded thermoplastic filament, then depositing it in precise shapes from a moving nozzle (attached to a printhead) according to computer instructions. 2D slices of the part are printed layer by layer until the complete 3D object is built.
The automotive components industry in Europe is seeing the most significant growth in using PEEK resin. Components around the engine, variable speed transmission parts, steering elements, and so on were all manufactured using a PEEK plastic injection mould instead of some customary expensive metals. As the automobile industry adapts to the needs of miniaturization, low weight, and cost reduction, the demand for injection moulded PEEK resin will grow.
PEEK injection molding, compared with other plastic injection moldings, needs to provide higher injection pressure, injection speed, and stable heating. In addition, you must pay attention to the diseño de moldes, so it’s best to find a professional special plastic injection factory to produce what you want. It would be better if all of these were effectively controlled from the beginning of the diseño de moldes, which can avoid unnecessary risks in production. This article is a thorough introduction to PEEK injection molding, including its types, applications, considerations, and other aspects.
During the rotational molding process, powdered plastic is placed in a mold, which is heated and rotated about two (or more) axes. This rotation ensures that molten plastic covers the entirety of the inside of the mold and assumes the shape of the cavity.
PEEK is a semi-crystalline, opaque substance that belongs to the family of polímeros known as PAEK, which comprises aryl, ether, and ketone chemical groups. PAEK is a subset of the PolyKetone family of polymers. PEEK’s high melting point and excellent mechanical properties come from the aryl and ketone components in its composition. PEEK’s ether group allows it to be both malleable, which contributes to its toughness, and chemically inert, providing resistance to chemical exposure.
Because of its large volume and surface resistivity, PEEK can maintain its excellent insulating performance even when subjected to wide swings in temperature and other environmental factors.
With a flammability grade of UL 94 V-0, PEEK is safe to use in environments where temperatures reach over 600 °C during combustion. When burnt at high temperatures, it also creates less smoke. This is why it is so famous for making components for passenger planes.
In small quantities, FDM is very fast and cost-effective and can produce a wide range of shapes, including those with complex internal geometries. However, it does not produce especially strong parts.
Vacuum casting is a plastic fabrication process usually employed for small batches of colorful prototypes. It uses silicone molds to make urethane plastic parts.
GETTING A QUOTE WITH LK-MOULD IS FREE AND SIMPLE.
FIND MORE OF OUR SERVICES:
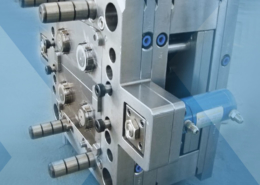
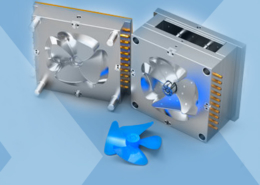
Plastic Molding

Rapid Prototyping
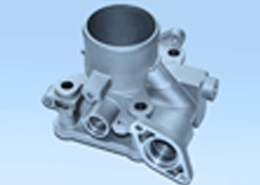
Pressure Die Casting
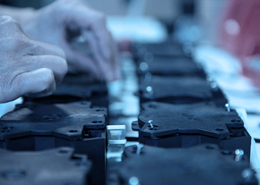
Parts Assembly
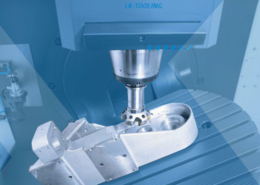