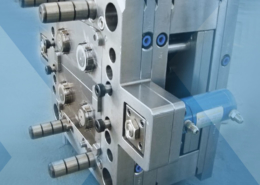
Plastic Injection Molding Company | Twin Cities, Minnesota - local injection mol
Author:gly Date: 2024-10-15
Structural foam’s ability to withstand thermal expansion makes it ideal for products that will be exposed to a wide range of temperatures. Whether it is heat or cold, these products will not warp or lose their properties if exposed to extreme temperatures.
HDPE, or high-density polyethylene, is a flexible and waterproof resin. It has good low-temperature resistance, chemical resistance, and corrosion resistance, and is easily processed at an affordable price.
This manufacturing process can produce identical parts over and over. Additionally, the high-pressure forces used force the plastic against the mold walls, creating highly complex designs with intricate details.
A similar cause is inconsistencies in the material. This means that not all of the resin will fill the mold cavity as intended. For this problem, you should do quality control checks on the storage of the resin or change sources to get a more consistent product.
Port Erie’s large-tonnage injection molding creates large parts with walls thinner than 0.25 inches. Our machines are capable of handling up to 1,650 tons and can create parts up to 20 pounds.
Short-shot issues are often detectable during quality control checks. These can include visible changes in the part’s appearance or dimensions. Other signs are holes or thinner segments on the product’s surface.
This article covers how to diagnose and fix short-shot problems. It will help you get your production line running again. Keep reading to learn more.
Injection molding requires plastic resin pellets to be melted down in the barrel of the injection molded machine. The melted resin is then forced into the mold through a high-pressure nozzle, forcing the material into all parts of the mold cavity. As the plastic cools and hardens, it retains the shape of the mold.
Finally, short-shot issues can be caused by molding machine defects. A machine that produces inadequate pressure is a common culprit.
At Port Erie, we will assess your part and help you determine which process is best for your product’s functionality and your budget. If you need, our engineering team can get involved to help optimize your design, so it is as compatible with its manufacturing process as possible.
Due to the lower pressure used in this molding process, the tooling used does not need to be as durable as high-pressure injection molding tools, saving you money.
Many parts of the injection molding process are being automated, including loading and unloading, inspection and quality control, assembly, and more. Using automation and robotics during the manufacturing process helps to reduce labor costs and production time, increasing your cost savings.
Structural foam molding also allows for the production of very large plastic products with thicker walls. These products are generally heavier than injection molded products, weighing 50 pounds or more. However, structural foam molded products are still more lightweight than solid plastic parts.
Injection molding can be used to produce large plastic products with thinner walls. These products tend to be lighter than those produced by structural foam molding, usually weighing less than 20 pounds.
Our large tonnage structural foam molding produces parts up to 50 pounds with walls thicker than 0.25 inches. These parts are heavy but would weigh significantly more if they were solid plastic.
Another common cause of short-shotting is improper venting. The air inside the mold that the resin displaces needs a space through which to escape.
ABS is a very durable resin with high durability. It also has high tensile strength and is very resistant to physical impacts and chemicals.
Polypropylene is a lightweight, cost-effective, rigid resin. Its chemical and heat resistance along with its high tensile strength and impact tolerance make it a great choice for a wide range of products.
Recalibrating your machine is a good place to start. Also, ensure that the reciprocating screw or the barrel has not been compromised.
Cycle times for injection molding are very short—sometimes only lasting a handful of seconds. It is also possible to use a multi-cavity to produce several different parts in one run, saving even more production time.
Most components are made using plastic injection molding. This is an efficient and reliable method, but there are a few common challenges that technicians can face, including short-shot plastic injection molding issues.
Polyethylene is a durable and lightweight resin that offers excellent load-bearing, shock absorption, vibration-dampening properties, and resistance to chemicals, grease, and moisture. Polypropylene is a rigid and lightweight resin offering excellent compression and impact resistance, as well as chemical, temperature, and moisture resistance.
Working with a manufacturer who has large tonnage capabilities in both low-pressure structural foam molding and high-pressure injection molding grants you a wider range of manufacturing options so you get the best product possible.
At Port Erie Plastics, we are dedicated to providing our clients with the highest quality plastic products possible. From engineering to injection molding or structural foam molding and value-adding secondary operations plus distribution and warehousing, we have you covered.
The most common resins used in structural foam molding are polyethylene and polypropylene. Both resins possess advantageous properties that make them ideal for this process.
Structural foam molding and these two resins are great for creating large industrial totes and grilles for lawn and garden tractors due to their durability and resistance to heat, chemicals, and moisture.
Another mold-design problem that can cause a short shot is an imbalance in the mold or inadequate dimensions of runners and gates. Inconsistent mold thickness can lead to temperature control issues as well.
You can easily fix this by either increasing the melt temperature or choosing a different resin with a lower viscosity. Also, better control over mold and melt temperatures throughout the process can help ensure the right viscosity.
Short-shot plastic injection molding refers to a common issue in the molding process. This occurs when the melted plastic resin fails to fill every space within the mold cavity. This results in a malformed component that must be remade.
There are three common resins used in high-pressure injection molding: HDPE, ABS, and polypropylene. Again, each has its own advantages and is chosen based on the application of the product being produced.
High-pressure injection molding is used to create many outdoor products, including DuraTrac outdoor floors and lawn or garden carts.
Nova is a world-class producer of plastic molded components for clients in both the automotive and non-automotive industries.
Misplaced nozzles, sprues, runners, and gates also can cause uneven polymer flow. Making minor adjustments to the placement of these–or mold design in general–can produce a more natural melt flow.
If not, it will become trapped in the mold, causing inadequacies. Checking your vents or adding more vents during the design phase may help alleviate this problem.
Now that you understand how to diagnose and fix a short-shot plastic injection molding issue, you can take steps to minimize downtime and optimize output. Catching these problems early can help you avoid major losses down the road.
There are several main causes of short-shot issues. A common one is a high plastic viscosity. This restricts flow, so smaller crevices in the mold do not get filled.
Low-pressure structural foam molding can create parts with variable wall thicknesses. However, cycle time will be determined by the thickest part. Uniform wall thickness is always best. Also, due to the low pressure used in the process, there is a reduced risk of warping and deformation during the manufacturing process.
Plastic is used in almost every industry. These include consumer goods, construction, aerospace, computer, and automotive technologies, to name a few.
Plastic plays an integral part in almost every person’s life. It helps make products and components that are durable, corrosion-resistant, strong, and light.
Luckily, while the injection molding process doesn’t produce much waste, any unused or waste plastic produced can be recycled for future products.
Large plastic products can be produced in two ways, large-tonnage injection molding and large-tonnage structural foam molding. Both can produce products that can replace metal, wood, concrete, or fiberglass. Each process, however, has its benefits and specific applications, so it is important to understand the processes and their benefits.
Nova Stevensville is an original equipment manufacturer (OEM) that serves automotive and other industries. We pride ourselves on meeting the unique needs of each client by supplying the precise parts they need to be successful. Contact us today for pricing or to learn more about our products and services.
Low-pressure structural foam molding requires nitrogen gas and/or a chemical blowing agent to be mixed with the melted resin. This mixture is then injected into a mold under significantly lower pressure than traditional injection molding techniques. Structural foam molding produces very large parts with thicker walls, making them very durable.
GETTING A QUOTE WITH LK-MOULD IS FREE AND SIMPLE.
FIND MORE OF OUR SERVICES:
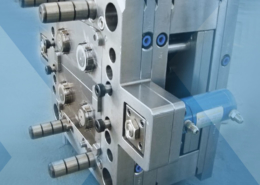
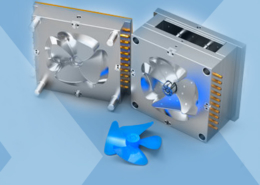
Plastic Molding

Rapid Prototyping
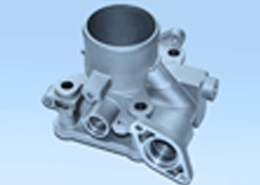
Pressure Die Casting
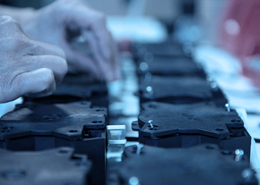
Parts Assembly
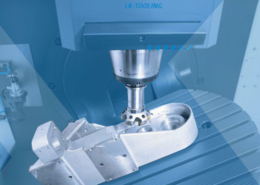