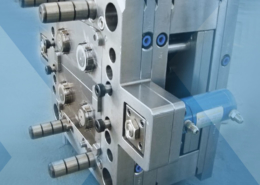
Plastic Injection Molding Company - plastic injection company
Author:gly Date: 2024-10-15
improper processing,such as using the wrong processing parameters or failing to properly dry the plastic material, can result in delamination
By signing up, you agree to our Terms of Use and Privacy Policy. We may use the info you submit to contact you and use data from third parties to personalize your experience.
Next, let’s look at both manufacturing methods in terms of part design and geometry, features and details, and material flexibility.
Using colorants and additives that are compatible with the plastic material to achieve the desired color and appearance.
Improper processing parameters, such as low injection pressure, short injection time, or inadequate cooling time, can also cause short shots by not allowing the plastic material to flow and solidify properly.
Optimize the injection molding process parameters, such as mold temperature, injection speed, and pressure, to ensure even cooling and minimize differential shrinkage.
A well-designed die ensures the even flow of material across the entire profile. Feed rate control can also optimize flow consistency. Importantly, the screw needs to have the correct compression ratio and flight geometry based on the material’s properties. Adjusting the back pressure and the screw speed helps to control the melt pressure and ensures steady material output without degradation.
Excessive injection pressure or speed can also cause flash by forcing the plastic material beyond the intended mold cavity.
Using plastic materials that are more heat-resistant or adding special additives that improve heat resistance and reduce the risk of burn marks.
contamination: such as the presence of foreign particles or moisture, can also cause delamination by preventing the plastic material from adhering properly to the mold surface
Adjusting the injection molding process parameters, such as melt temperature, injection speed, and pressure, to optimize the plastic flow and minimize the occurrence of weld lines.
At Sino-Mold , Our top-notch technical expertise allows us to avoid these defects by all means. Our cost-efficient plastic injection molding services are available for mass production and rapid prototypes. These and many more you will receive when you upload your design files for a quotation.
Flaws in injection molding can significantly impact mold design. Neglecting to maintain the mold appropriately can also act as a trigger for molding defects. As these defects manifest in the final stages, rectifying them can be an arduous and expensive task.
Optimizing the extrusion molding process involves balancing material flow, cooling rates (for hot extrusions), and production speeds. The benefits include higher quality, increased efficiency, and reduced waste. Regardless of the type of machine or process, there are some best practices to follow when extruding plastic or rubber. Innovations are also improving quality.
material incompatibility: such as using different types of plastic materials that are not compatible with each other, can also cause delamination
Blisters refer to raised bumps or defects on the surface of a molded part. This problem can be caused by various factors such as issues with the mold used to create the part, the materials used in the injection process, and the specific injection process itself. Specifically, blisters are caused by trapped gas near the outer layer of the part that cannot be released through normal venting methods. These factors can all contribute to the development of blisters on molded parts.
Improving mold design and optimizing the plastic flow path to reduce the number and size of branching and intersection points.
By signing up, you agree to our Terms of Use and Privacy Policy. We may use the info you submit to contact you and use data from third parties to personalize your experience.
Compare that to extrusions. You might have to wait a lot longer for tooling to arrive – and with far less support for design complexity.Are you ready to get started? Create a free Fictiv account and upload your CAD drawing.
The discoloration is a common defect in injection-molded parts and refers to any variation in color or appearance that deviates from the desired specification. It can occur due to a variety of reasons, including contamination, degradation of the plastic material, overheating, and improper processing.
Accelerate development with instant quotes, expert DFM, and automated production updates.
Performing post-molding operations, such as annealing or stress relief, to reduce the residual stresses that contribute to the formation of weld lines.
Do you have any other good advice for addressing defects in injection-molded products? Share your tips with Louise at https://www.linkedin.com/redir/phishing-page?url=sales02%40sino-mold%2ecom or https://www.linkedin.com/in/louise-injectionmold/. Thank you for your help.
design issues: such as having thin or uneven walls or sharp angles, can cause stress concentrations that lead to delamination.
Optimizing the heating and cooling system of the mold to ensure even temperature distribution on the mold surface, and avoid heat accumulation or insufficient cooling.
By signing up, you agree to our Terms of Use and Privacy Policy. We may use the info you submit to contact you and use data from third parties to personalize your experience.
Use plastic materials with lower levels of filler or reinforcement, or use materials with special additives to improve cooling and minimize sink marks.
Compared to injection molding, extrusion has lower tooling costs. That’s because the dies used are simpler, easier to machine, and therefore less expensive to produce. For the continuous production of simpler parts at high volumes, extrusion provides a faster ROI. For complex parts at high volumes, however, the higher cost of an injection mold can be spread or amortized across many parts.
Extrusion can’t produce fine details or intricate surface features. Instead, the level of detail is limited to what can be achieved with a consistent cross-section. To add complexity or additional features, secondary processes such as cutting, drilling, or stamping are used.
Extruding machines can produce solid, semi-hollow, or hollow profiles with a smooth surface finish. First, plastic or rubber is fed into a hopper. Hot extrusion heats the polymer above its recrystallization temperature but cold extrusion is performed at room temperature instead. This material is then conveyed with a screw and forced through a machined metal die under high pressure to achieve the desired shape.
Some injection molding processes may not be effective for the production. The molding process is the leading cause of defects in injection molding parts.
Extrusion and injection molding can both produce plastic and rubber parts. However, extrusion shapes a material into a cross-sectional shape by forcing it through a tool called a die and injection molding introduces material into the tool cavity or “mold.”.
Extrusion is best suited for parts for simple, uniform shapes. Although it can create parts like window frames and trims with complex cross-sections, extrusion requires secondary processes to create fully three-dimensional objects or internal cavities.
This article examines extrusion and injection molding in detail so you can determine whether extrusion or injection molding is the better choice for your project. It also compares these manufacturing processes in terms of cost, scalability, complexity, and efficiency. In addition, you’ll find information about advanced considerations, applications, and trends.
Managing process efficiency and complexity in plastic injection molding is critical for optimizing production, reducing costs, and maintaining quality.
Using plastic materials with appropriate properties, such as low viscosity or high melt flow index, to facilitate material flow into all areas of the mold cavity.
Plastic injection molding is a complex process that requires precision, expertise, and attention to detail. From material selection to tool design, every aspect of the process must be carefully considered and optimized to ensure high-quality, defect-free parts. However, even the most well-designed processes can encounter issues, and how to solve them ? In this article Louise will explore some common process troubleshooting techniques in plastic injection molding, providing insights and practical tips to help you identify and resolve issues in your injection molding processes. #injectionmolding #mold #sino-mold
Our trained employees ensure your parts will be delivered on time and to spec.
Optimizing the injection molding process parameters, such as mold temperature, injection speed, and pressure, to ensure proper processing.
The Injection molding process begins when plastic resin pellets are loaded into a hopper or liquid rubber is mixed. This material is then heated in a barrel until it becomes a thick liquid called melt and injected into a mold cavity under pressure. After the mold is filled, the molten plastic material takes the shape of the tool, which is typically machined from aluminum or steel. The parts cool and are ejected.
Extrusion readily scales from small-to-medium production to higher volumes because of its low tooling costs and simple setups. Injection molding is also scalable but may require a different tool. For example, a soft or semi-hardened steel injection mold isn’t suitable for producing hundreds of thousands of parts, even if commercial rather than fine tolerances are used.
Flow lines are patterns or lines on the surface of a plastic part that are caused by the merging of multiple flow fronts during the injection molding process. They can reduce the aesthetic quality of the part and may also negatively affect its strength and performance. Flow lines usually occur at the intersection or branching points of the plastic flow path, where there may be unevenness or differences in the speed of the plastic flow.
Injection molding and extrusion molding differ significantly when it comes to the complexity and versatility of the parts they can produce. The table below provides an overview.
Plastic extrusion molding supports various polymers, including engineering thermoplastics, thermoplastic elastomers (TPEs), and high-performance materials like PEEK. If you’re used to working with machined metal parts, remember that the part tolerances for extrusions are not as precise because of the tooling that’s used and the material shrinkage that’s expected.
By signing up, you agree to our Terms of Use and Privacy Policy. We may use the info you submit to contact you and use data from third parties to personalize your experience.
Optimizing the injection molding process parameters, such as mold temperature, injection speed, and pressure, to ensure proper processing and prevent overheating.
Injection molding is a common manufacturing process used to produce plastic parts. However, this process can result in various defects, such as blisters, sink marks, weld lines, burn marks, discoloration, delamination, flash, and short shot. These defects can be caused by factors such as material properties, mold design, processing parameters, or maintenance. To minimize or eliminate these defects, solutions such as adjusting processing parameters, optimizing mold design, using appropriate materials, and conducting regular inspections and maintenance can be employed.
Injection molding is ideal for producing parts with intricate shapes and complex geometries. It can also create fully three-dimensional parts with features such as ribs, bosses, snap fits, and complex internal cavities.
For prototyping and low-volume production, and for parts that require commercial tolerances instead of fine ones, molds made of soft or semi-hardened steels can be used instead. Master unit die (MUD) inserts, or MUD molds, can also help to control costs. These universal frames fit into an injection molding machine and hold a removable insert.
Adjusting the processing parameters, such as increasing injection pressure, prolonging injection time, or increasing cooling time, to provide sufficient material flow and solidification.
Improper mold design, such as inadequate venting or gating, can also cause short shots by restricting the flow of plastic material into the mold cavity.
Delamination is a defect that occurs when the layers of an injection-molded part separate or peel apart from each other, resulting in a weakened or structurally compromised part.
Injection molding supports the use of high-performance polymers like PEEK and other composites, such as glass-filled nylon, that are tailored to impart specific properties. Injection molding is also used with engineering plastics such as polycarbonate (PC) and some elastomers, such as liquid silicone rubber (LSR), for medical devices and aerospace parts.
We exist to eliminate bottlenecks in new product development by integrating the people, processes, and platform you need to source custom parts.
Injection molding also benefits from the use of simulation software, Industry 4.0 and Internet of Things (IoT) integration, and greater integration with enterprise resource planning (ERP) systems.
The plastic material is exposed to excessively high temperatures or prolonged heat exposure, leading to thermal degradation and the release of gases that cause discoloration or burning.
By signing up, you agree to our Terms of Use and Privacy Policy. We may use the info you submit to contact you and use data from third parties to personalize your experience.
Performing regular maintenance and cleaning of the mold and injection molding equipment during production to ensure they are operating properly and maintained in optimal condition.
Material properties, such as high viscosity or low melt flow index, can also contribute to short shots by making it difficult for the plastic material to flow into all areas of the mold cavity.
When you request a quote for injection molded parts, you’ll also receive design for manufacturing (DFM) feedback from our engineering experts. This can help you to accelerate product development, and Fictiv can provide T1 samples in about two weeks.
Injection molding can create parts with fine surface details, including textures, logos, and intricate patterns. It can also mold parts with variable wall thicknesses within the same part. Plus, features like threads, snap-fits, and hinges can be molded directly into the component.
Improper mold design or poor mold maintenance can cause flash by allowing the plastic material to escape from the mold cavity through gaps or spaces in the mold.
Flash is a common defect in injection-molded parts and refers to excess material that extends beyond the intended parting line or mold cavity. It can occur due to several reasons, including improper mold design, poor mold maintenance, excessive injection pressure or speed, and material shrinkage.
A short shot is a defect that occurs when the injection-molded part is incomplete, resulting in missing or underdeveloped sections of the part. It can occur due to several reasons, including insufficient material, improper mold design, processing parameters, or material properties.
Weld lines, also known as knit lines, are areas of an injection-molded part where two or more molten plastic flow fronts converge, resulting in a visible line or seam on the surface of the part. These lines can occur when the molten plastic flow fronts cool and solidify at different rates, creating a visible seam or weakened area. Weld lines can occur in areas of the part where the plastic flow fronts meet, such as in the center of a part or at the intersection of multiple flow paths.
Material shrinkage can also contribute to flash by causing the plastic material to contract and pull away from the mold surface, leaving excess material behind.
Some injection molding defects may be very difficult to address. These defects can arise from various factors, including the molding process, the materials utilized, the maintenance of the equipment, or the storage conditions of the components. Here are several injection molding defects, causes, and solutions.
In general, extrusion has lower production costs than injection molding. Parts that are extruded in long sections require less frequent stops, and there’s no need for ejection since the part is forced through and exits the die. Injection molding processes can achieve faster cycle times with optimized cooling systems, but that adds to a project’s total costs.
Access a wide breadth of capabilities through our highly vetted network.
Create high quality custom mechanicals with precision and accuracy.
With hot extrusion, water baths or air systems provide fast or gradual cooling, respectively. For hollow profiles, internal air or fluid systems can be used to cool both internal and external surfaces at the same rate. Increasingly, infrared thermography or embedded temperature sensors are used to support real-time monitoring and control.
Uneven wall thickness. (plastic material is reinforced with fillers or fibers that interfere with the flow of the molten plastic)
By signing up, you agree to our Terms of Use and Privacy Policy. We may use the info you submit to contact you and use data from third parties to personalize your experience.
Contamination can occur when foreign particles, such as dust, oil, or grease, come into contact with the plastic material during processing. These particles can affect the color and appearance of the final part, resulting in discoloration. Degradation of the plastic material can occur due to exposure to high temperatures, moisture, or ultraviolet light, which can cause the material to break down and change color. Overheating can occur when the mold temperature is too high or the injection speed and pressure are not optimized.
Among its advantages, injection molding supports design complexity and has well-defined rules as described in Fictiv’s Injection Molding Design Guide, a free resource that’s available for download. The hardened steel molds that support tight tolerances are more expensive, but they can provide a cost-efficient return on investment (ROI) across a high volume of parts.
Injection molding produces solid parts but cannot create hollow ones. This manufacturing process supports considerable design complexity, however. Depending on the quality of the tooling, injection molded parts can have tight tolerances. It’s also possible to injection-mold parts with a textured surface finish or features such as logos.
We exist to eliminate bottlenecks in new product development by integrating the people, processes, and platform you need to source custom parts.
In addition to issues that may arise during the molding process, defects in injection-molded parts can also be attributed to factors related to the plastic resin used, or the way in which it was handled prior to production. These types of defects can range from relatively minor cosmetic imperfections to more serious issues that compromise the structural integrity of the part and potentially pose safety risks in certain applications.
Adjusting injection molding process parameters, such as melt temperature, injection speed, and pressure, to optimize plastic flow uniformity and speed.
Fictiv provides injection molding services and delivers complex parts at ridiculous speeds. The tooling that’s used in injection molding is more expensive than the dies for extrusions, but injection molds made of soft or semi-hardened steels cost less than hardened steel molds.
Using plastic materials with lower viscosity or using materials with special additives that improve plastic flow and minimize the occurrence of weld lines.
By signing up, you agree to our Terms of Use and Privacy Policy. We may use the info you submit to contact you and use data from third parties to personalize your experience.
By signing up, you agree to our Terms of Use and Privacy Policy. We may use the info you submit to contact you and use data from third parties to personalize your experience.
By signing up, you agree to our Terms of Use and Privacy Policy. We may use the info you submit to contact you and use data from third parties to personalize your experience.
Perform post-molding operations, such as annealing or stress relief, to reduce the residual stresses that contribute to sink marks.
Improving the mold ventilation system to ensure proper airflow and reduce the risk of trapped air pockets that can cause burn marks.
Extrusion is a proven process that molds continuous lengths of plastic and rubber so they have uniform cross-sectional shapes. These profiles can be as simple as a tube or cord but are sometimes more complex. For example, door and window seals can be extruded into shapes that resemble the letters D, E, J, P, or U. Typically, the extruded profile or extrudate is cut into lengths or individual parts.
Insufficient material can cause short shots by not providing enough plastic material to fill the mold cavity completely.
Burn marks are discolorations or black or brown spots on the surface of an injection-molded part caused by excessive heat during the molding process. These marks can negatively affect the aesthetic quality of the part and may also weaken the material, reducing its strength and performance.
Higher screw speeds can increase extrudate output, but they can also result in inconsistent material flow. That’s why many extruders now use feedback systems that automatically adjust screw speeds based on processing parameters like melt pressure. If high-volume production is critical, hot extrusion equipment with fast-melting polymers may be required.
Sink marks are depressions or indentations on the surface of an injection-molded part that is caused by variations in the cooling rate of the plastic material. These variations can result in uneven shrinkage and warpage of the part, leading to localized areas of surface depression. Sink marks can occur in thick sections of the part where the cooling rate is slower, and are more likely to occur when using materials with high levels of filler or reinforcement.
Injection molding’s ability to maintain precise dimensions and tight tolerances across high volumes makes it an asset for demanding applications. Injection-molded parts are also suitable for industrial assemblies. Because each injection molded part has its own tolerances, designers need to account for tolerance stack-ups so that all of the assembled parts fit together.
GETTING A QUOTE WITH LK-MOULD IS FREE AND SIMPLE.
FIND MORE OF OUR SERVICES:
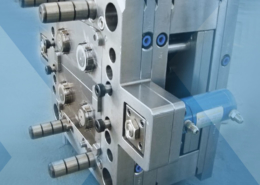
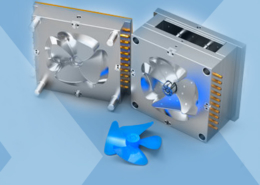
Plastic Molding

Rapid Prototyping
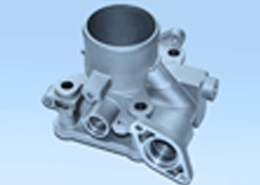
Pressure Die Casting
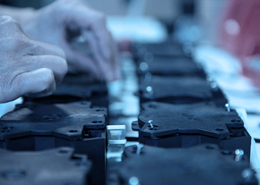
Parts Assembly
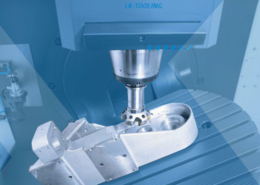