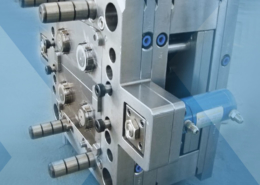
Unveiling the World of Molded Parts
Author:gly Date: 2024-06-08
Introduction:
Molded parts are ubiquitous in our daily lives, serving as integral components in a myriad of products across various industries. From automotive and aerospace to electronics and consumer goods, molded parts play a crucial role in shaping modern manufacturing. Understanding the intricacies of molded parts offers insights into the processes, materials, and applications that drive innovation and efficiency in product development. This article delves into the world of molded parts, exploring their significance, manufacturing techniques, and diverse applications.
Manufacturing Processes
Molded parts are produced using a range of manufacturing processes, each offering unique advantages in terms of efficiency, precision, and cost-effectiveness. Injection molding, the most common method, involves injecting molten material into a mold cavity under high pressure to form complex shapes with tight tolerances. Other processes such as blow molding, compression molding, and rotational molding offer specialized solutions for producing hollow, large-scale, or intricate parts. By leveraging the appropriate manufacturing process, manufacturers can tailor their approach to meet specific design requirements and production goals, ensuring optimal part quality and performance.
Materials and Properties
The choice of materials for molded parts is vast, ranging from thermoplastics and thermosets to elastomers and composites. Each material offers distinct properties such as strength, flexibility, durability, and chemical resistance, making it suitable for specific applications. Engineering polymers like ABS, polycarbonate, and nylon are favored for their mechanical properties and versatility, while elastomers like silicone and polyurethane offer flexibility and resilience. Additionally, advancements in material science have led to the development of bio-based and recycled materials, addressing sustainability concerns and reducing environmental impact. By selecting the appropriate material for molded parts, manufacturers can optimize performance, longevity, and cost-effectiveness while aligning with environmental goals.
Design Considerations and Optimization
Design considerations play a pivotal role in the success of molded parts, influencing factors such as manufacturability, functionality, and cost efficiency. Design for manufacturability (DFM) principles aim to optimize part geometry, draft angles, wall thicknesses, and surface finishes to facilitate smooth production processes and minimize defects. Additionally, features such as ribs, bosses, and fillets are incorporated to enhance structural integrity, reduce material usage, and improve part performance. Advanced design tools such as computer-aided design (CAD) software and finite element analysis (FEA) simulations enable designers to iterate and refine part designs iteratively, ensuring optimal outcomes in terms of functionality, aesthetics, and cost.
Applications and Industries
Molded parts find applications across a diverse range of industries, contributing to the functionality, aesthetics, and performance of countless products. In the automotive sector, molded parts are used in interior components, exterior body panels, and under-the-hood applications to enhance safety, comfort, and fuel efficiency. In the medical field, molded parts play a critical role in devices and equipment such as syringes, catheters, and diagnostic instruments, ensuring precision, reliability, and patient safety. Moreover, in consumer electronics, molded parts are integral to the design and functionality of smartphones, laptops, and home appliances, enabling sleek aesthetics and seamless user experiences. By catering to the specific needs and requirements of different industries, molded parts continue to drive innovation and progress in product development and manufacturing.
Conclusion:
In conclusion, molded parts are indispensable components in modern manufacturing, offering versatility, efficiency, and performance across various industries. By understanding the manufacturing processes, materials, design considerations, and applications associated with molded parts, businesses can unlock opportunities for innovation, cost optimization, and market competitiveness. Moreover, as technology advances and market demands evolve, the landscape of molded parts will continue to evolve, presenting new challenges and opportunities for manufacturers and designers alike.
Word Count: 598
GETTING A QUOTE WITH LK-MOULD IS FREE AND SIMPLE.
FIND MORE OF OUR SERVICES:
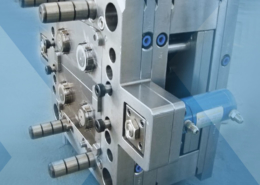
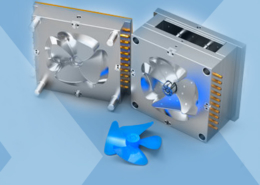
Plastic Molding

Rapid Prototyping
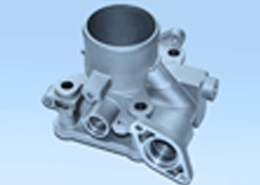
Pressure Die Casting
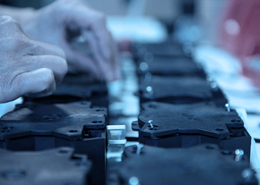
Parts Assembly
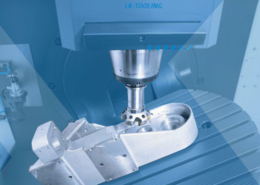