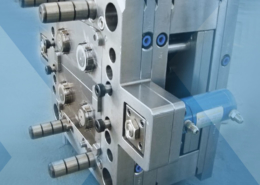
Plastic Injection Molding 101 - Injection Molding Terms - plastic injection part
Author:gly Date: 2024-10-15
Thermolator injection molding is a sophisticated manufacturing technique that involves the precise control of temperature during the injection molding process. By maintaining optimal temperature conditions, thermolators ensure the uniformity and quality of molded products, significantly enhancing efficiency and reducing production costs.
Maintaining consistent quality standards is paramount in thermolator injection molding, given the criticality of temperature control in the molding process. Deviations from optimal temperature ranges can result in defects and imperfections, compromising product quality and reliability. Implementing robust quality assurance protocols is essential to mitigate such risks and ensure compliance with industry standards.
1. Reduced Environmental Footprint: Utilising recycled plastics significantly diminishes the demand for new raw materials, alleviating the strain on our ecosystems.
In the dynamic landscape of manufacturing, the call for environmental sustainability has become increasingly resonant. As a seasoned professional in the field of plastic injection moulding, I am eager to guide environmentally conscious manufacturers, on the transformative journey of incorporating recycled plastics into their injection moulding processes.
As industry leaders, we bear a collective responsibility to shape a sustainable future. Collaboration, knowledge-sharing, and the pursuit of cutting-edge technologies will define the next chapter in injection moulding. By fostering an environment of continuous improvement, we ensure the longevity of our industry and the planet.
Thermolator injection molding stands at the forefront of modern manufacturing, offering innovative solutions to streamline production processes across various industries. This article delves into the intricacies of thermolator injection molding, shedding light on its significance, functionality, and implications for the manufacturing landscape.
Navigating the regulatory landscape is a concern for every conscientious manufacturer. However, the use of recycled plastics aligns seamlessly with existing environmental standards and often exceeds compliance requirements. This alignment not only ensures legal adherence but also positions the company as a responsible industry leader.
As manufacturing technologies continue to evolve, the role of thermolator injection molding is poised to expand further, driving innovation and efficiency across diverse industries. By embracing advancements in materials science, automation, and sustainability, manufacturers can harness the full potential of thermolator injection molding to unlock new opportunities and address emerging challenges.
At its core, thermolator injection molding relies on the principle of heating and cooling materials to facilitate the shaping of molds. Through a series of precise temperature controls and hydraulic mechanisms, molten materials are injected into molds, where they solidify to form finished products. This intricate process demands meticulous attention to detail and advanced technological infrastructure to achieve optimal results.
Allow me to share a notable success story from my own experience. A mid-sized manufacturing firm, initially hesitant to adopt recycled plastics, witnessed a remarkable transformation. After implementing recycled materials, they not only contributed to environmental conservation but also experienced a 15% reduction in production costs.
In conclusion, the journey of recycled plastics in injection moulding is a testament to the industry’s adaptability and resilience. As we stand at the intersection of environmental consciousness and manufacturing innovation, the decision to embrace recycled plastics is not just a choice; it’s a commitment to a future where waste is minimised, and opportunities are maximised.
While the initial investment in transitioning to recycled plastics may raise concerns, conducting a thorough cost analysis reveals the long-term savings potential. Factor in reduced material costs, potential tax incentives for sustainable practices, and the positive impact on brand perception.
Transitioning to recycled plastics requires a strategic approach. Begin by conducting a comprehensive assessment of your current processes and materials. Identify suitable recycled plastics for your specific applications and gradually integrate them into your production line.
During my tenure, I’ve observed that regulatory compliance, when approached as an opportunity rather than a burden, fosters long-term business sustainability. Adhering to eco-friendly practices is not merely a legal requirement; it is an investment in the company’s future resilience.
Compared to traditional molding techniques, thermolator injection molding offers significantly faster cycle times, allowing for higher throughput and increased productivity. The precise control of temperature parameters minimizes downtime associated with cooling and reheating, enabling continuous operation and swift turnaround times.
One of the primary benefits of thermolator injection molding is its ability to produce intricate and precise components with minimal margin for error. By maintaining consistent temperature profiles throughout the molding process, manufacturers can achieve unparalleled levels of accuracy and repeatability, ensuring uniformity across production batches.
Despite its efficiency and precision, thermolator injection molding raises environmental concerns related to energy consumption and material waste. The energy-intensive nature of heating and cooling processes contributes to carbon emissions and resource depletion, highlighting the need for sustainable manufacturing practices and renewable energy sources.
The evolution of thermolator injection molding can be traced back to the mid-20th century, with advancements in materials science and engineering driving its development. Initially utilized in the production of plastic components, thermolator injection molding has since expanded its applications to encompass a diverse range of industries, including automotive, electronics, and medical devices.
Looking ahead, the future of recycled plastics in injection moulding is teeming with possibilities. Researchers and industry experts are exploring innovative methods to enhance the performance of recycled materials, opening doors to even more sustainable practices.
I recall a project where initial scepticism was replaced by amazement as a state-of-the-art injection moulding machine effortlessly processed recycled plastics, producing components of exceptional quality. Technological progress is propelling the industry towards a future where recycled plastics are not just viable but preferable.
In conclusion, thermolator injection molding represents a paradigm shift in modern manufacturing, offering unparalleled precision, efficiency, and cost-effectiveness. By understanding its principles, advantages, and challenges, manufacturers can leverage this transformative technology to achieve sustainable growth and competitive advantage in an ever-evolving global market.
In these success stories, there is a common thread of adaptability, open-mindedness, and a willingness to experiment. Embracing recycled plastics requires a cultural shift within the organisation, with employees at all levels understanding and championing the cause.
I urge manufacturers, particularly those with a keen eye on sustainability, to consider the transformative power of recycled plastics. In doing so, we not only safeguard the environment but also future-proof our businesses, ensuring they thrive in a world that values ecological responsibility.
Recycled plastics offer a compelling alternative, addressing both environmental concerns and the need for sustainable manufacturing. Contrary to misconceptions, recycled plastics have evolved into high-quality materials suitable for injection moulding, offering a plethora of advantages.
One common hurdle is the perception that recycled plastics compromise product quality. Allow me to dispel this myth. Technological advancements have elevated the quality of recycled plastics, ensuring they meet or exceed the standards set by their virgin counterparts.
To get your components or sub-assemblies manufactured by us, you can call our team on 01543 462 561 or send an email enquiry to [email protected]. Our team of experts will be in contact within hours to help you with your project.
3. Enhanced Corporate Image: Embracing recycled plastics showcases a commitment to environmental responsibility, enhancing brand reputation and resonating with conscientious consumers.
Mould design plays a crucial role in the successful implementation of recycled plastics. Consult with experienced mould designers who understand the unique characteristics of recycled materials. Adjustments may be necessary to optimise the performance of recycled plastics in the moulding process.
Despite the initial investment required for implementing thermolator injection molding systems, the long-term cost savings are substantial. By optimizing material usage, reducing scrap rates, and enhancing production efficiency, manufacturers can achieve significant economies of scale, ultimately driving down per-unit costs and enhancing profitability.
While thermolator injection molding offers numerous benefits, its implementation presents inherent challenges, particularly regarding technological complexity. The integration of temperature control systems, hydraulic actuators, and precision molds necessitates sophisticated engineering expertise and substantial capital investment.
We can advise on the design of your product to suit the manufacturing processes required. We can organise tooling for you and manage the project for you so that you receive conforming parts at a competitive price. And we’ll keep doing that for you for as many years as you need us to.
Let’s delve into real-world examples of manufacturers overcoming challenges. In a recent case study, a forward-thinking company integrated recycled plastics into their injection moulding processes, witnessing a 20% reduction in material costs without compromising product quality. These success stories underscore the tangible benefits awaiting those willing to embrace change.
2. Cost Efficiency: Recycled plastics often come at a lower cost, providing manufacturers with a competitive edge while contributing to overall cost reduction.
Undoubtedly, the environmental impact of traditional plastic manufacturing cannot be ignored. The proliferation of plastic waste has reached alarming levels, prompting global concern and stringent regulations. As manufacturers, we hold a pivotal role in steering the industry towards eco-friendly practices.
Quantifiable benefits extend beyond cost reduction. Improved product quality, a significant decrease in waste generation, and a positive response from consumers all contribute to the success of manufacturers embracing recycled plastics.
GETTING A QUOTE WITH LK-MOULD IS FREE AND SIMPLE.
FIND MORE OF OUR SERVICES:
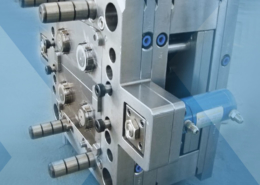
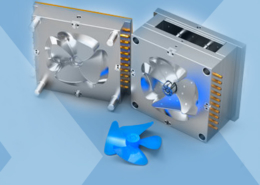
Plastic Molding

Rapid Prototyping
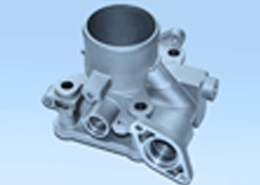
Pressure Die Casting
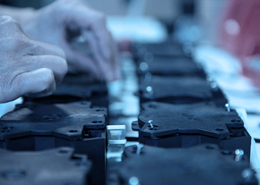
Parts Assembly
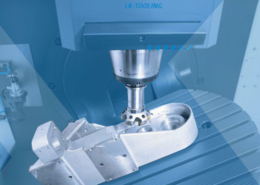