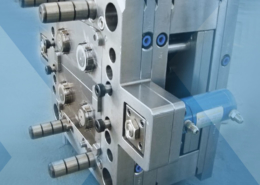
Plastic Injection Molding - Custom Plastic Molding - custom plastic injection mo
Author:gly Date: 2024-10-15
The second type of foam molding uses ordinary injection molding machines but includes a blowing agent in the material mix. These blowing agents are dry chemicals that are added to the plastic granules before they enter the machine. When the plastic is melted by the machine’s heating elements the heat causes the blowing agent to react, turning into a gas and foaming the plastic.
Some common uses of structural foam are in the making of machine housings for businesses, components for point-of-sale displays, container pallets, and machine chassis components.
Insert molding is a subset of injection molding techniques similar to overmolding where metal components are placed into a mold cavity before the actual plastic injection. The insert is precisely positioned inside the mold either manually or by a robotic arm. The mold then closes, and plastic is molded over the insert, creating a single part.
There are two main types of structural foam molding. The first type is known as the low-pressure process. During this process, a gas is added to the melted plastic before it enters the mould. Once the plastic is injected into the mould the gas causes it to foam.
The texture of the plastic these processes produce is often described as a sponge or honeycomb because of the small pockets of air that are created. The honeycomb centre is surrounded by a dense outer layer to ensure stability.
One of the most common applications for insert molding is the creation of metal attachment features for fasteners. Fasteners enable assemblies to be securely assembled and disassembled without product damage. Heat-set threaded inserts are molded into plastic to reduce the risks of thread damage during installation.
There are various sub-processes within injection molding that add further capabilities to this already versatile technology. This article will explore insert molding vs overmolding and the advantages of each.
The texture of the plastic these processes produce is often described as a sponge or honeycomb because of the small pockets of air that are created. The honeycomb centre is surrounded by a dense outer layer to ensure stability.
The content appearing on this webpage is for informational purposes only. Xometry makes no representation or warranty of any kind, be it expressed or implied, as to the accuracy, completeness, or validity of the information. Any performance parameters, geometric tolerances, specific design features, quality and types of materials, or processes should not be inferred to represent what will be delivered by third-party suppliers or manufacturers through Xometryâs network. Buyers seeking quotes for parts are responsible for defining the specific requirements for those parts. Please refer to our terms and conditions for more information.
Structural foam molding is a commonly used process that can create many useful products. The low-pressure version of structural foam molding is a more controlled process than standard injection molding. This allows larger pieces to be produced.
There are two main types of structural foam molding. The first type is known as the low-pressure process. During this process, a gas is added to the melted plastic before it enters the mould. Once the plastic is injected into the mould the gas causes it to foam.
Certified to the highest standards, we typically manufacture parts for the aviation, medical, industrial, and analysis sectors. We pride ourselves on having a highly-skilled and dedicated team of engineers and machine operators who are able to accommodate the needs of all our clients.
Structural foam molding is a commonly used process that can create many useful products. The low-pressure version of structural foam molding is a more controlled process than standard injection molding. This allows larger pieces to be produced.
Many different types of plastic can be used in the structural foam molding process. Each offers its own unique properties and characteristics. Commonly used plastics include the following:
Overmolding is essentially a type of insert molding. However, overmolding vs. insert molding is, as the name suggests, plastic is molded over another molded part. The first component is made inside an injection mold, and it is then placed into a second mold to add the over-molded material. This technique combines multiple plastics for either practical or aesthetic purposes. For example, one might use different durometer plastics to mold a softer plastic over a more rigid one to make a part easier to grip. Using multiple colored plastics in an overmolded part can also distinguish the product from other brands. Overmolding is regularly used on the handles of tools like screwdrivers, power drills, or toothbrushes.
For more information about the types of plastics used in structural foam molding processes and injection molding see here.
Injection molding, which includes the sub-processes insert molding and overmolding, is a versatile and low-cost manufacturing production process that is used in the large majority of consumer products. Injection molding often results in the lowest cost per part when compared to other manufacturing techniques like CNC machining and even 3D printing.Â
Despite the many benefits of insert molding, a few disadvantages need to be considered before choosing to use this sub-process. Â
Some common uses of structural foam are in the making of machine housings for businesses, components for point-of-sale displays, container pallets, and machine chassis components.
Here at Pekago, we offer structural foam molding services to our clients at our state-of-the-art facilities in the Netherlands. With more than three decades of experience in injection molding and structural foam molding, we’re experts are carrying out these precise, high-quality production processes.
For more information about the types of plastics used in structural foam molding processes and injection molding see here.
Various sub-processes add further capabilities to this already versatile technology. This article will specifically explore insert molding vs. overmolding and the advantages of each.
Structural foam molding is an injection molding derived process that either adds a gas to the polymer to reduce its density or introduces blowing agents to achieve the same result. When the gas or blowing agent is added the plastic foams, hence the name. The end result is a lighter product that requires fewer post-production processes and less assembly.
Insert molding can also eliminate the need for fasteners by including the necessary metal parts in the mold, thus firmly securing the parts into a single bonded component.
Structural foam molding is an injection molding derived process that either adds a gas to the polymer to reduce its density or introduces blowing agents to achieve the same result. When the gas or blowing agent is added the plastic foams, hence the name. The end result is a lighter product that requires fewer post-production processes and less assembly.
Certified to the highest standards, we typically manufacture parts for the aviation, medical, industrial, and analysis sectors. We pride ourselves on having a highly-skilled and dedicated team of engineers and machine operators who are able to accommodate the needs of all our clients.
Injection molding is a broad term used to describe one of the most important processes in the manufacturing industry. Itâs a process that requires a mold, typically made of metal with a cavity in the shape of the desired part. Molten plastic is injected into the mold and ejected. The process repeats to produce thousands of identical parts. Itâs safe to assume that every large-volume plastic part on the market has come from an injection molding machine because the benefits of using injection molding for production are numerous. These benefits include low cost per part, short cycle times, extensive materials, and compatible, in-tolerance parts.
In addition, structural foam products have a high stiffness ratio that can be beneficial in many settings. What’s more, since structural foam products are coated with a strong outer skin, they remain strong, as well as flexible and lightweight.
In addition, structural foam products have a high stiffness ratio that can be beneficial in many settings. What’s more, since structural foam products are coated with a strong outer skin, they remain strong, as well as flexible and lightweight.
Once injection molding is chosen for a specific application, the next step is often whether to use insert molding, overmolding or just stick with plain injection molding. When trying to weigh the advantages of the processes, it is important to accurately define the product application. Each of these processes has specific use cases that are suited to different product types. It can be difficult to gauge which process will best suit your particular product, so itâs good to get expert advice early on. Contact a Xometry representative to leverage decades of vast manufacturing expertise. We will help steer your design decisions in the right direction so that you can choose between insert molding vs. overmolding or just injection molding.Â
In some cases, the finish of a product created using structural foam molding is not acceptable as it creates a streaky surface. This can be remedied with extra filling or painting.
Here at Pekago, we offer structural foam molding services to our clients at our state-of-the-art facilities in the Netherlands. With more than three decades of experience in injection molding and structural foam molding, we’re experts are carrying out these precise, high-quality production processes.
In some cases, the finish of a product created using structural foam molding is not acceptable as it creates a streaky surface. This can be remedied with extra filling or painting.
Despite the many benefits of overmolding, a few disadvantages need to be considered before deciding to use this process. Â
Many different types of plastic can be used in the structural foam molding process. Each offers its own unique properties and characteristics. Commonly used plastics include the following:
The second type of structural foam molding uses ordinary injection molding machines but includes a blowing agent in the material mix. These blowing agents are dry chemicals that are added to the plastic granules before they enter the machine. When the plastic is melted by the machine’s heating elements the heat causes the blowing agent to react, turning into a gas and foaming the plastic.
GETTING A QUOTE WITH LK-MOULD IS FREE AND SIMPLE.
FIND MORE OF OUR SERVICES:
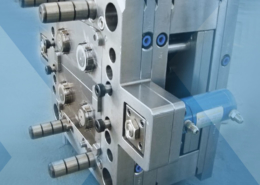
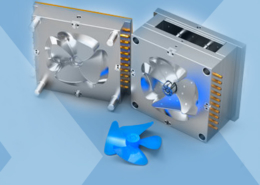
Plastic Molding

Rapid Prototyping
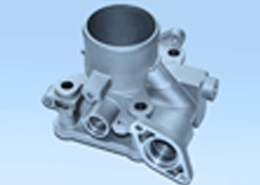
Pressure Die Casting
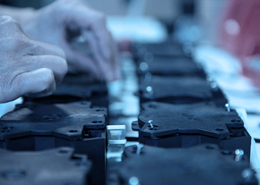
Parts Assembly
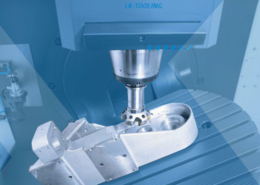