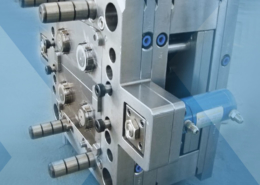
Plastic Crate Mould - LiSong - plastic crate mould
Author:gly Date: 2024-10-15
Our Injection Molding Technology page provides more detail about these services and processes and includes links to YouTube clips that explain them in animations and simple to understand language. Read more here
At Plastikos, our engineering and tooling team has developed our own proprietary mold maintenance program ranging from Level I – Level III. The various preventative maintenance levels are proactively scheduled based on the mold’s production volume, cycle count, and the abrasiveness of the raw material. As a result of our rigorous mold maintenance techniques, we have helped clients extend their mold life beyond 10 million cycles (and counting) in many cases.
LEVEL II PREVENTATIVE MAINTENANCE This is level of PM will build on the first level and we will conduct a deeper dive into the tool. Partial disassembly of the tool will be required as we will lubricate the tool, clean vents, and further inspect for any wear or damage.
We implement Arburg’s proprietary ALS system through our entire precision molding operation. This plant-wide system is used to store and upload a qualified process to any molding machine and virtually eliminate the chance for operator error during process set up. Key process variables can only be accessed (and changed) by a qualified process engineer, further reducing any chance for variation throughout production.
At Plastikos, we are completely standardized on our precision molding equipment along with our auxiliary equipment (dryers, thermolators, hot runner controllers, and so on). All supporting equipment is directly tied into our molding machines, providing real-time data to our engineering and manufacturing team. This real-time data tracking is used detect a variation in any process variables, machine interruptions, and overall product yield for a specific production run.
We have a wealth of experience in traditional molding, over molding, insert molding and 2k molding. These processes are explained in detail here
In both plants, the drying equipment is segregated from the production areas to eliminate fine dusts, and reduce the risk of plastic granules contaminating finished goods, making the workplace dirty or creating slip hazards.
Our team of degreed Plastics Engineers has completed rigorous training in scientific decoupled molding strategies through Penn State’s Plastic Engineering program along with RJG’s Master Molder program. This specialized training is essential for successful process optimization and qualification.
Most of the materials that we process are hygroscopic (they absorb moisture from the air) so they must be dried prior to processing. In Sydney we have Moretto central drying equipment and in Johor we use Motan drying equipment. Both utilize silicon desiccant technology to dry the air to -40°C dew point prior to heating it to the recommended temperature for drying the plastic. With this, we are assured that our materials are properly prepared for processing.
Additionally, we highly recommend implementing each precision mold with cavity pressure sensors as a method to further detect any process variation within the cavity. Once a nominal cavity pressure has been established through the process development phase, a master file can be saved. During start-up production, this master file is uploaded and will provide 100% traceability through the production run. Any product that falls outside of the established process window will be automatically discarded at the press with the use of a 3-axis robot. All molding machines at Plastikos are equipped with this cavity pressure monitoring software and tied directly into our molding machines for real-time process monitoring.
LEVEL I PREVENTATIVE MAINTENANCE This is level of PM is the most common and will be routinely scheduled during a mold’s production run. Minimal disassembly of the tool is required as we will perform a face cleaning of the cavity & core inserts and inspect for any premature wear.
Our team of degreed Plastics Engineers has completed rigorous training in scientific decoupled molding strategies through Penn State’s Plastic Engineering program. This specialized training is essential for successful process optimization and qualification.
Our latest Engel Molding machines in both our Sydney and Johor, Malaysia plants have state-of-the-art technology including:-
Since John Wesley Hyatt and his brother Isaiah patented the first basic plunger plastic injection molding machine in 1872 there have been many changes. They only had celluloid plastic available at the time, now we have hundreds of choices. As to be expected, their machine was crude, they could never have foreseen the capabilities of the modern machines. As engineers and industrial designers increase the complexity of plastic injection molded components, machinery manufacturers and chemical companies rise to meet the new challenges that they create and deliver solutions. W&S is always in touch with the latest developments in industry innovations and are able to deliver the best advice and solutions for your applications.
Rooted in advanced moldmaking and driven by unparalleled precision molding expertise, nothing defines Micro Mold and Plastikos more than our people. With more RJG Master Molders and degreed Plastic Engineers than any other manufacturer our size–and a vast majority of larger resources as well–you’ll find a tight-knit, technologically advanced workplace that’s brimming with talented, motivated individuals. Committed to innovation, we bring together experts from various disciplines to deliver exceptional products, service and value on every project. It’s a mindset that extends throughout our entire organization and influences our approach as we cultivate future strategic partnerships.
Scientific molding consists of sequential steps that are followed to establish nominal fill time, injection pressure, gate freeze time, pack pressure, cycle time, and clamp tonnage among other process variables. From there, key process parameters are often tested through the means of a Design of Experiment (DOE) to reach the process window that will be duplicated each production run.
The chart below provides a comprehensive list of the precision injection molding equipment that we utilize at Plastikos. All departments are supported by our highly-trained team of processing, tooling, and quality control experts.
Industry 4.0 strategies have been implemented plant-wide to provide enhanced data sharing and traceability among molding machinery. This proprietary system ensures only our process engineers can adjust process parameters, which minimizes manual error during production startup.
We also utilize IQMS throughout our facility to optimize scheduling, production monitoring, and preventative mold maintenance. These combined industry 4.0 efforts have led to a remarkable 99% year-over-year on-time delivery.
LEVEL III PREVENTATIVE MAINTENANCE This is level of PM requires full disassembly of the tool and is scheduled off the mold’s cycle count and production volume. Wear items will be replaced, as needed. Water lines are fully cleaned to prevent scaling and manifolds will be serviced, where applicable.
Plastikos & Plastikos medical operate around the clock to further minimize downtime / risk to our customer’s supply chain. Due to the extensive engineering & automation techniques, many of our high-volume molding machines can run completely light’s-out at night & weekends. All departments (QC, tool maintenance, material handling, etc.) are staffed to support this 24/7 schedule.
Injection molding can be described in simple terms as the high pressure injection of liquid plastic raw material into a mold which shapes, cools and solidifies the polymer into the desired shape.
Our Arburg and Kraus Maffi injection molding machines provide the latest technologies with extraordinary accuracy and repeatability.
Our In-house Mold Maintenance Department is staffed with experienced toolmakers—ensuring the longevity of our customers’ injection molds and minimizing downtime due to repair and maintenance issues. All spare steel is assigned a custom detail number and cataloged in our ERP system which will notify us when we need to reorder certain spare cavity & core inserts.
Our Sydney Australia plant has injection molding machines that range from 20 tonne clamping capacity to 700 tonne and our Johor, Malaysia has machines from 80 tonne to 350 tonne.
Two white room molding centers with all-electric high-speed machines ranging from 66T – 220T. All molding machines are equipped with cavity-pressure monitoring software (eDART) and many outfitted with 3-axis robotics for part handling.
Process validation is a critical step in the development cycle before the mold & product can be deemed fit for production. During this process, scientific molding principles should be applied to establish the nominal running conditions for that given mold, material, etc.
Digitalizing a manufacturing operation remains at the forefront of Industry 4.0. The ability to gather real-time data has become essential when optimizing key elements such as product yields, machine efficiency, product quality, and overall profitability.
GETTING A QUOTE WITH LK-MOULD IS FREE AND SIMPLE.
FIND MORE OF OUR SERVICES:
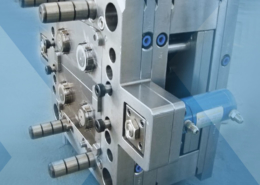
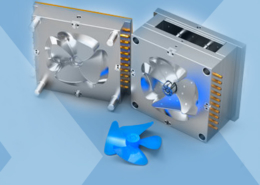
Plastic Molding

Rapid Prototyping
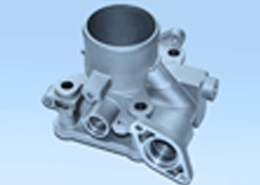
Pressure Die Casting
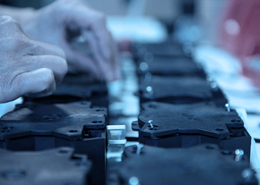
Parts Assembly
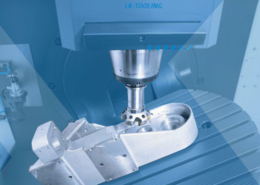