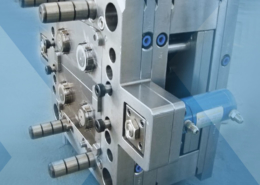
Plastic Businesses | Injection Mouldiing Companies on Sale - injection moulding
Author:gly Date: 2024-10-15
The data shows a slightly different trend for a larger, more complex injection moulded part than the simple/smaller one analysed above. There is a saving of 79% going from 500x to 5000x in nylon and a further 12% going up to 50,000x. This shows that there are still substantial cost savings in manufacturing into the high thousands for larger, more complex parts. The price for 500x is comparable to 3D Printing as the tooling cost is a relatively smaller proportion of the unit cost than the small/simple injection moulded part.
Optimised for mass production of plastic items, our services in Plastic Injection Moulding are backed by deep expertise and industry-leading knowledge.
It is essential that the design of the injection moulded parts are carefully reviewed before production. Removing unnecessary features from the parts will make the tooling easier to machine. Read our Injection Moulding Design Guide to optimise your parts and get a better price for your project.Â
The data again indicates that ABS is the most cost-effective to manufacture in out of the three materials, while polycarbonate is the most expensive. With an increase in quantity from 500x to 50,000x, the lead time only increases by a few days. This is primarily because most of the lead time in an injection moulding project is manufacturing the mould and sampling. Once the mould successfully produces parts to the desired specifications, the parts can be produced rapidly.
In this article Get It Made simulated the production for two different parts, a very simple small part, and a more complex larger part. You can see how prices vary between different common injection moulding materials and part quantities moulded.
Gilero provides a range of manufacturing services, including plastic injection molding and injection mold tool building. We focus solely on the medical device and drug delivery markets. Our medical injection molding facilities follow strict design protocols and process controls to ensure that all products meet the required specifications. Depending on client needs and product requirements, we can offer manual or fully automated production lines for molding and assembly.
Our facility utilizes high-precision plastic injection molding and injection mold tool building equipment. In-house injection molding machines range in tonnage from 30-Ton to 250-Ton. Injection molding capabilities range from single cavity, pre-production injection molds to high cavitation molding using a hot runner system. The injection molding equipment used by Medacys is manufactured by some of the most trusted brands in the industry, including Sumitomo (SHI) Demag, Toyo Machinery, and Haitian International.
In general, injection moulding tooling can cost from £2k to £100k. Costs for moulded parts can range from a few pence to a hundreds of pounds each.
Ready to see how much your part costs to manufacture? Request a free Injection moulding quote today, and one of our engineers will review your project within 24 hours.
Choose our CNC Turning services for circular cross sections. We also offer Turn & Mill capabilities for more complex turned parts.
Request your free injection moulding quote today and one of our engineers will personally review your project within 24 hours. They will then help fine-tune your project to make sure you get the best possible price and lead time for your injection moulding project.
Below is a cost comparison between Nylon, ABS and Polycarbonate (PC) for a simple injection moulded part. The table/graph also compares how the number of parts ordered affects the price and lead time.
Aluminium extrusion is ideal for both single prototypes and large-scale production, offering bespoke, high-standard, consistent cross-sectional profiles.
If you want to know more about materials options for your injection moulding project, read our article about choosing the right Injection Moulding material.
Located in Shenzhen, China, is Medacys – Gilero’s joint venture toolmaking and medical injection molder. This state-of-the-art injection molding facility spans 36,000 square feet and is staffed by manufacturing technicians, tooling designers, quality engineers, and engineering project managers. The expertise of the Medacys team focuses largely on the medtech and biomedical industries. With dedicated tooling, molding, assembly, and lab areas, along with environmentally monitored and controlled cleanrooms, our Shenzhen facility provides plastic injection molding services for companies across the globe.
For Nylon, going from quantity of 500x to 5000x has a 88% total cost per part saving for a simple injection moulded part. For volumes around 500x and below, it can often be cheaper to CNC machine or 3D Print the parts depending on the design. This is because the high tooling costs are spread over a smaller number of parts, making each part more expensive. Going from 5000x to 50,000x sees an additional cost saving of 9%. This demonstrates how increasing the part quantity significantly reduces part cost for smaller volume orders. However, as the order quantity increases, the reduction in unit price becomes less but still significant.
When comparing the three materials, the data shows that ABS is the cheapest material to manufacture with, and polycarbonate is the most expensive. The lead time only increases by a few days going from 500x to 50,000x. This is because the bulk of the lead time for an injection moulding project is manufacturing the mould and sampling. Once the mould produces parts to specification, part production is very fast.
With many years of experience, sheet metal parts can be a great low-cost option for certain high and low-volume applications.
In comparison to other manufacturing practices, plastic injection molding for medical devices is very flexible and allows for full customization of components. It is used in high volume situations to fulfill injection molded medical device and drug delivery devices with high accuracy and precision. From an operational perspective, plastic injection molded medical devices are produced with low labor costs, are positioned to be scalable as the client grows in sales, and are more environmentally friendly due to the extended life of the product and reduction of waste.
Below is a cost comparison between Nylon, ABS and Polycarbonate (PC) for a complex injection moulded part. There is also a comparison of how the price and lead time change according to the number of parts ordered.
Our 3D printing solutions cater to personalised needs with a diverse range of materials and colour options, perfect for intricate plastic components and small batches.
Injection moulding is a manufacturing process often used to produce high volumes of plastic parts. This manufacturing process starts by creating and machining a mould with precision to form the partâs features. Then molten plastic resin is injected into the metal mould cavity. The plastic moulded parts subsequently cool and are ejected from the mould cavity. If you want to know more about the injection moulding process, read our Injection Moulding Guide.
The choice of material will depend on the specific requirements of the part being produced, such as its mechanical properties, chemical resistance, and environmental factors like temperature and humidity.
Get It Made was founded in 2011 with a mission to make manufacturing simple. Based in London, UK, Get It Made provides outstanding manufacturing services to companies across the globe.
Gilero stands out as an excellent choice for medical device injection molding manufacturing. Medacys, our joint-venture facility in Shenzhen, China, spans 36,000 square feet and is equipped with cutting-edge technology. The skilled team, comprising manufacturing technicians, tooling designers, quality engineers, and engineering project managers, specializes in the medtech and biomedical sectors. This specialization ensures a deep understanding of the unique requirements and regulatory standards in these fields. Gilero offers dedicated areas for various manufacturing processes, including tooling, molding, assembly, and laboratories. We maintain environmentally controlled cleanrooms for precision. Our in-house injection molding machines range from 30-Ton to 250-Ton, and they use equipment from trusted brands like Sumitomo (SHI) Demag, Toyo Machinery, and Haitian International.
Tooling is often a key part of the economics in plastic injection moulding, this is because it is a large up-front investment. And this cost needs to be amortised into expected part volume, over a number of years. If injection moulding isn't suitable, it is very possible 3DÂ Printing or CNCÂ Machining could be a better option. Depending on the parts' features, the machining of a complex mould will require more time and expense, increasing the upfront costs of the project. This is the main reason why injection moulding is mainly used for high volumes.
However, once you have the moulding tool, the plastic moulded parts will have a very low unit cost. And the tooling is usually CNC machined from a high quality steel, allowing more than one production run using the same tool, so it will last many years.
GETTING A QUOTE WITH LK-MOULD IS FREE AND SIMPLE.
FIND MORE OF OUR SERVICES:
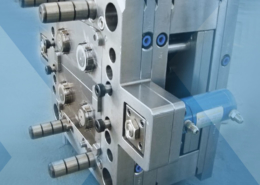
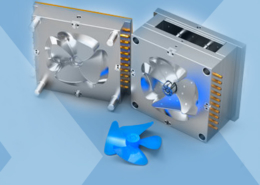
Plastic Molding

Rapid Prototyping
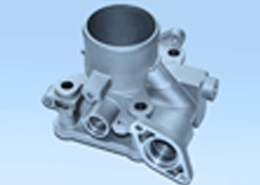
Pressure Die Casting
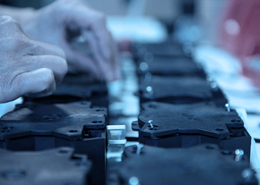
Parts Assembly
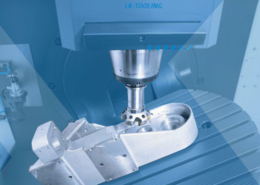