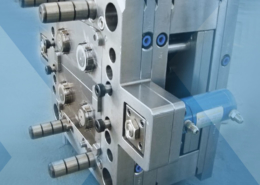
Plastic - plastic molding 1 2
Author:gly Date: 2024-10-15
Scientific molding involves using data to develop a process that produces repeatable results with little to no variation. Through resin expertise and testing, dimensional or mechanical characteristics of a molded part can be optimized. Often achieved through the use of SOLIDWORKS® Plastics Premium software (mold flow simulation) and RJG eDart® process control systems, predictive insight, process validation and complete process documentation are vital to producing demanding parts.
When our customers need a high-quality and reliable injection molding company, we listen to their needs and go to work. Steady demand for our services has continued and we were proud to grow into our brand new facility in 2022. Come visit us and you will walk away confident to make us your injection molding supplier.
As it continues to evolve, scientific molding has helped optimize injection molding production processes in a way that now allows manufacturers to lean on technology that creates an even greater global competitive advantage.
Equipment and software that help monitor real-time production processes guide the scientific molding stages and provide a critical advantage. In addition, quality control issues can be avoided by having automated containment control and traceability for specific applications. From collecting data to machine maintenance, process development to resin characteristics, and much more – scientific molding helps identify efficiencies which result in greater value and better parts for customers.
This guide will help you understand the metal to plastic conversion process, its benefits, and how to partner with your injection molder to collaborate on all design for manufacturability elements.
A full service plastic injection molding company dedicated to USA manufacturing excellence. Our complete in-house control over the mold build and injection molding process cuts costs and gives you single source responsibility for quality.
A full service CNC machining company supplying custom parts with USA manufacturing reliability. Our in-house control over the complex machining process and quality assurance cuts costs and offers you 100% compliance to your needs.
How does scientific molding benefit product manufacturers and OEMs? When implemented methodically by an injection molder, scientific molding results in better parts and fewer rejects.
We give our customers exceptional customer service and a hassle-free sourcing experience. We guarantee consistent high quality injection molded parts, Precision CNC machining, no hidden nickel and dime charges, and fast delivery of your production. Your satisfaction is our main focus.
Rosti works with some of the world’s leading producers to face up to the manufacturing challenges in e-mobility. This is a sector with rapid growth – driven by environmental pressures…
Are you interested in learning more about scientific molding and how it can benefit your custom part? Learn how Plastic Components, Inc. will strive to be your best supplier and a team you can count on.
Injection molders should understand how to avoid designing a part, building the tooling, and beginning the molding process only to find out that the design does not work in production. Scientific molding can help manufacturers steer clear of this situation.
This guide will walk you through a comprehensive overview of the plastic injection molding process from design through production – including essential elements of molding.
MSI Mold has been helping customers with their plastic injection molding needs since 2005. We have built more than 2,500 molds for plastic injection and have shipped over 25,000,000 parts and assemblies to a long list of industries. Customers choose MSI Mold to be their injection molding supplier for our outstanding customer service, consistent high quality injection mold parts, and reliable on-time deliveries.
Get high-quality, affordable custom plastic parts and molds made in the USA by our experienced injection molding company. Your injection molds and production parts are manufactured completely in-house. Now offering custom machined parts - ITAR : ISO 9001 Compliant
This guide will help you understand the importance of DFM, and how to partner with your injection molder during the design validation process prior to tooling kick-off.
Recorded data can be used to assess quality control and make any necessary tweaks to tooling – improving overall part quality. Once all quality parameters have been met, the implementation of scientific injection molding practices help to greatly streamline the production process. These actions can be so effective that less involvement is needed by both machines and operators. In fact, cutting-edge injection molders have begun instituting revolutionary lights-out manufacturing practices. This is where factories and production facilities are equipped with innovative and automated machinery to conduct tasks that would normally need the presence of a human.
Design engineers should lean on past learnings and expertise in optimizing part design for unique applications. Scientific molding elements associated with part design may incorporate using the latest software and technology including computer aided engineering, mold flow, and prototype development that will validate the part’s end use.
Plastic variables require understanding the nature of the material to be molded and its preferred molding conditions. When a material’s key characteristics, behavior, and response to processing is understood, scientific molders can optimize the molding process to produce the most consistent part possible.
According to Kip Doyle, author of an article on the Top 10 Reasons Why Molders Fail at Scientific Molding, many molders can’t get past a “machine-focused” approach and mold from the plastic’s “point of view.” He cites that many articles have been written on the four primary plastic variables (plastic temperature, plastic flow, plastic pressure, and plastic cooling rate and time), and a scientific molder must understand this approach and the process optimized from the perspective of the plastic.
Testing can then be applied to check for any imbalances among cavities. When this analyzation is complete, a gate seal study can be performed to gather data on where the gates seal fully, and at what points in the mold cavities. Recording findings and making recommendations for adjustments in the process or tooling, is essential to correcting potential defects.
It’s not hard to understand how computing and innovation have positively impacted industries of all types over the past 35 plus years. The injection molding industry is no exception. Plastic…
Scientific molding practices can also be used to optimize tool design or to optimize poorly designed tools. It is essential for injection molds to be evaluated for their performance in the production of consistent, defect-free parts. Engineers should examine every aspect of a mold’s mechanical functionality, using the appropriate material settings.
- Previous:Plastic - plastic molding 1 2
- Next:Plastic - plastic molding 1 2
GETTING A QUOTE WITH LK-MOULD IS FREE AND SIMPLE.
FIND MORE OF OUR SERVICES:
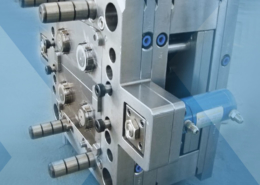
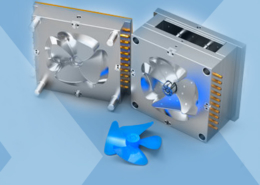
Plastic Molding

Rapid Prototyping
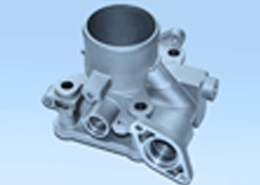
Pressure Die Casting
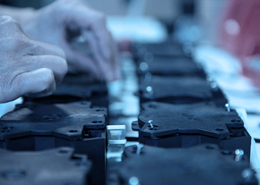
Parts Assembly
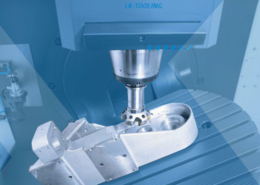