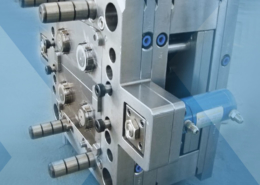
Navigating the Innovations in Medical Molding
Author:gly Date: 2024-06-08
Medical molding stands as a cornerstone of modern healthcare, facilitating the production of intricate components vital for diagnostic, therapeutic, and surgical applications. This article delves into the dynamic realm of medical molding, exploring its significance, evolution, technological advancements, and future prospects.
Introduction: Unveiling the Essence
Introduction to Medical Molding
Medical molding represents a specialized branch of injection molding dedicated to the production of medical devices and components. From syringes to implantable devices, medical molding plays a pivotal role in the healthcare industry, enabling the fabrication of precise, reliable, and biocompatible products essential for patient care. The convergence of materials science, engineering, and regulatory compliance distinguishes medical molding as a critical enabler of healthcare innovation and progress.
Evolution and Growth
The evolution of medical molding parallels the rapid advancements in medical technology and manufacturing processes over the past decades. What began as rudimentary molding techniques has matured into sophisticated operations equipped with state-of-the-art machinery, cleanroom facilities, and stringent quality control measures. The growing demand for personalized healthcare solutions, coupled with regulatory reforms and industry standards, has propelled the expansion of medical molding capabilities, driving innovation and efficiency in healthcare delivery.
The Intersection of Precision and Compliance
At the heart of medical molding lies a delicate balance between precision engineering and regulatory compliance. Ensuring the integrity, safety, and efficacy of medical devices requires meticulous attention to detail at every stage of the manufacturing process. Compliance with standards such as ISO 13485, FDA regulations, and Good Manufacturing Practices (GMP) is non-negotiable, demanding robust quality management systems, comprehensive documentation, and validation protocols. By prioritizing precision and compliance, medical molding companies uphold the highest standards of quality and reliability, instilling confidence in patients, healthcare providers, and regulatory agencies alike.
Exploring the Depths
Material Selection and Biocompatibility
The selection of materials in medical molding is a critical determinant of product performance, safety, and biocompatibility. Biocompatible polymers such as medical-grade thermoplastics and silicone elastomers are preferred for their compatibility with biological tissues and minimal risk of adverse reactions. Furthermore, materials must exhibit properties such as sterilizability, chemical resistance, and dimensional stability to withstand the rigors of medical applications. Collaborations between material suppliers, molders, and medical device manufacturers are essential for optimizing material selection and ensuring compliance with regulatory requirements.
Design for Manufacturability
Design for manufacturability (DFM) principles are pivotal in optimizing the manufacturability, performance, and cost-effectiveness of medical devices. Collaboration between design engineers and molding experts early in the product development process facilitates the identification and resolution of potential manufacturing challenges. Factors such as draft angles, wall thicknesses, undercuts, and material selection are meticulously optimized to enhance moldability, minimize production defects, and streamline post-processing operations. Utilizing advanced simulation tools and prototyping techniques enables iterative refinement of designs, accelerating time-to-market and mitigating development risks.
Technological Advancements and Future Prospects
The future of medical molding is imbued with promise, driven by ongoing technological advancements and shifting healthcare paradigms. Additive manufacturing techniques such as 3D printing are poised to complement traditional molding methods, offering greater design flexibility, customization, and rapid prototyping capabilities. Furthermore, the integration of digital twin technologies, real-time monitoring systems, and artificial intelligence promises to revolutionize process control, predictive maintenance, and quality assurance. Embracing digitalization, automation, and sustainable practices will be instrumental in driving innovation, enhancing patient care, and shaping the future of healthcare delivery.
Conclusions: Paving the Path Forward
In conclusion, medical molding stands as a vital enabler of healthcare innovation and progress, empowering clinicians with the tools and technologies needed to improve patient outcomes and quality of life. By leveraging cutting-edge materials, design methodologies, and manufacturing processes, medical molding companies continue to push the boundaries of what is possible in medical device development. Looking ahead, collaboration, innovation, and a steadfast commitment to patient-centricity will be essential in navigating the complex landscape of healthcare and nurturing a healthier tomorrow for all.
GETTING A QUOTE WITH LK-MOULD IS FREE AND SIMPLE.
FIND MORE OF OUR SERVICES:
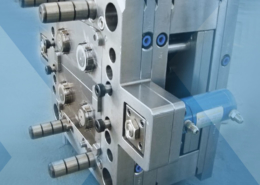
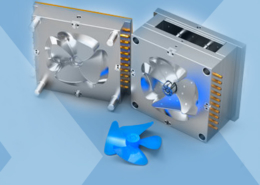
Plastic Molding

Rapid Prototyping
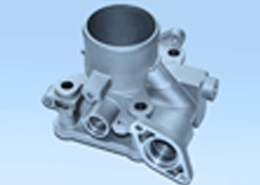
Pressure Die Casting
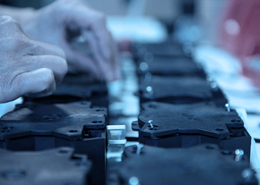
Parts Assembly
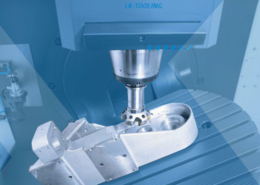