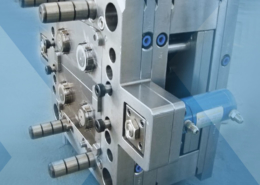
Picking The Right Plastics Manufacturing Process | RIM vs ... - rim plastic mold
Author:gly Date: 2024-10-15
Typically, the cost of the mold, also referred to as the tooling cost, is the major cost driver in injection molding. Let’s take a look at some of the elements that influence the price of an injection mold.
When it comes to injection molding prices, basic plastic injection molds might range from $3,000 to $6,000. A big, more sophisticated high-production, cross-cavity mold can cost between $25,000 and $50,000 or more. Although it may seem obvious, several factors contribute to the cost of injection molding.
We are an ISO-certified, family-owned provider of engineering, custom injection molding, and contract manufacturing. Our clients bring demanding applications requiring Thermoplastic Polyurethane injection molding services and best served by expert engineers.
3D printers can manufacture basic low volume 3D printed molds for as cheap as $100. A metal mold for a mid-volume service life of 1,000-5,000 units costs between $2,000 and $5,000. Mold costs can range from $5,000 to $100,000 for molds with more complicated shapes and prepared for higher production runs of 10,000+ pieces.
To a certain degree, asking for the costs of plastic injection molds cost is similar to questioning how much a car costs. Is your mold going to be a Pinto or a Porsche? Also, keep in mind that the cost of a mold is only the beginning. To calculate complete plastic injection molding costs for any projects, you must also include raw material, operating, and maintenance expenses in the future. These costs are a result of the aforementioned contributing factors.
We have developed hundreds of products, some with thermoplastic polyurethane injection molding, and manufactured millions of parts annually for the medical industry. Medical devices include point of care diagnostics, microfluidics, and pharmaceutical drug delivery applications.
We take pride in the workmanship of our Thermoplastic Polyurethane injection molding services. All Natech tools and production parts are made in the USA. We run three shifts per day, five days per week, and weekends are run on an as-needed basis.
Our precision injection molding options include scientific molding, R&D molding, high-cavitation molding, micro molding, over molding, and insert molding.
Mold manufacturer location: This was also mentioned while researching how mold size may affect your total injection molding expenses. To have your mold wherever it needs to go, an off-site plastic injection mold maker will charge you extra for shipping and handling.
Our mid to high-volume thermoplastic polyurethane injection molding automated and semi-automated manufacturing of plastic injection-molded components and assemblies for single-use, metered-dose, and multi-use disposables for the drug delivery, consumer packaging and diagnostics industries offer high quality at economical value.
Injection molding, the major cost driver is generally mold or tooling expenses. Molds for injection molding are typically created in one of three ways:
Our thermoplastic polyurethane injection molding product finishing capabilities include hot stamping, banding, pad printing, silk screening, flaw coating, conductive painting, cosmetic painting, metalizing, and plating.
For the consumer thermoplastic polyurethane injection molding market we specialize in the automated production of high-volume disposables, unit-dose packaging, caps and closures, and over-the counter diagnostics and drug delivery applications.
Natech’s projects that include Thermoplastic Polyurethane injection molding services are supported by MoldFlow Analysis, a Viscosity Curve, a Cavity Balance Study, a Pressure Window Characterization, a Gate Seal Time Study, and a Cooling Time Study. Natech engineers are masters of insert configuration and design single-cavity R&D molds with steel inserted areas. Interchangeable plates, inserts, and sub-inserts allow for more rapid design iterations at LOWER cost than creating new molds for each feature variation. SPI Class 103 and 104 molds are constructed from P20 steel and aluminum with hot runners and cold runners.
Material cost is determined by the design of a product, the material utilized, and the quantity of material needed to complete the injection molding process.
The production molds for Thermoplastic Polyurethane injection molding projects include high cavitation SPI Class 101 and 102 molds constructed from hardened steel. Cold, runner, hot sprue, and hot runner molds are designed with up to 128 cavities.
Creating more sophisticated molds necessitates technical knowledge. As a result, companies typically outsource specific aspects of injection molding, for instance, mold design and production.
If a plastic injection mold factory has the tools and materials, creating molds in-house may be the most cost-effective option if the technical expertise is also accessible. If the tools required for injection molding are not easily accessible, outsourcing lowers the cost of developing a mold.
We provide Thermoplastic Polyurethane injection molding services in New York, New Jersey, Connecticut, Pennsylvania, Florida, California, Illinois, Oregon, Maryland, Massachusetts, Colorado, and Michigan and other regions.
With small desktop injection molding equipment and 3D printed molds, creating modest volumes of components with injection molding is the most cost-effective. Small-scale automated injection molding machines are viable options for medium-series manufacturing of small components.Large industrial injection molding machines can range in price from $50,000 to more than $200,000. These machines also have more strict facility requirements and the need for specialized staff for operations, upkeep, and monitoring. As a result, although injection molding is a core competency, most businesses outsource mass manufacturing to service providers and contract manufacturers, with equipment expenses included in the service prices.
For injection molding, special-purpose equipment ranging from tiny personal molding machines that enterprises may use in-house to big industrial injection molding equipment primarily handled by providers, contractors, and major manufacturers is utilized.
In the electronics market, including thermoplastic polyurethane injection molding, we draw upon deep experience in comprehensive analysis and testing for evaluation and verification to design and build lighter, more durable electronics components.
Our mold maintenance plans for projects that include Thermoplastic Polyurethane injection molding services ensure each mold undergoes regular cleaning and review at predefined intervals based upon the number of setups and cycles. Mold inspections, general mold maintenance, major mold maintenance and preventative maintenance are standard operating procedures.
Our thermoplastic polyurethane injection molding assembly and joining capabilities include product filling, foil/heat sealing, ultrasonic welding, heat staking, mechanical assembly, pinning & UV/hot melt gluing, custom packaging/kitting, and pouching.
Depending on the needs of the finished products, a broad range of polymers can be utilized for injection molding. The cost involved when you buy plastic injection mold materials varies depending on the material selected. Thermoplastic pellets range in price from $1 to $5 per kilogram.
Clients trust Natech to be the Thermoplastic Polyurethane injection molding experts in engineering and manufacturing. Our engineers’ experience includes mold qualifications in medical IQ/OQ/PQ, high volume automation in consumer packaging, and engineering-grade resins and ultra-polymers in electronics.
The simple answer is that plastic injection molds range in price from $100 for a 3D printed injection mold to $100,000 plus for a sophisticated multi-cavity steel mold for greater manufacturing loads, which is typically the most important fixed start-up cost in injection molding. However, because these expenses are spread across hundreds or thousands of components, injection molding is a suitable method for mass-producing plastic parts at a low cost.
Each development project requiring Thermoplastic Polyurethane injection molding services is managed by a Project Engineer who monitors and controls deliverables and provides regular status updates.
GETTING A QUOTE WITH LK-MOULD IS FREE AND SIMPLE.
FIND MORE OF OUR SERVICES:
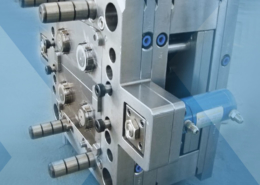
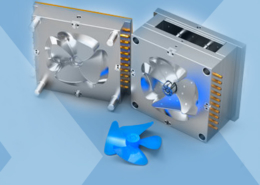
Plastic Molding

Rapid Prototyping
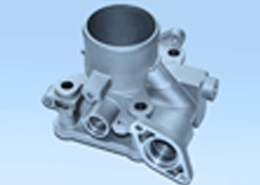
Pressure Die Casting
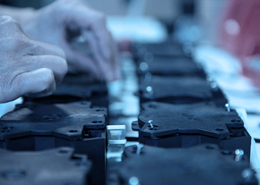
Parts Assembly
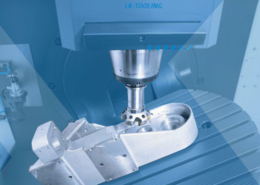