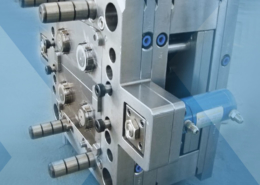
PETG injection molding process and application range - Blog - petg injection mol
Author:gly Date: 2024-10-15
Excellent manufacturability is a must whether you are into the production of medical testing equipment, storage containers, or surgical tools. Otherwise, you may face warranty claims, litigation, and even the worst-case scenarios involving life-threatening concerns due to poorly made parts.
No matter what kind of precision injection molding machine, it must be able to control the repeatability accuracy and quality repeatability of the product in a stable way.
The first is the repetition precision of the product size, and the two is the repeatable precision of the product quality.
The merging of Quickparts and Xcentric helps support customers’ continued growth and proficiency through improved U.S.-based, in-house, and quick-turnaround production. From 3D printing to injection molding, we do it all.
High mechanical strength, good dimensional stability, good vermicular resistance, and wide range of environmental adaptation.
In addition, the barrel temperature should also be accurately controlled, now screw and barrel temperature control by PID (proportional integral differential), the precision can be controlled within l degrees, which can meet the requirements of precision injection molding, if the FUZZY control method is more suitable for precision injection molding.
(3) improve the efficiency of injection rate. In order to achieve the rated injection rate, there are only two ways: one is to improve the maximum injection pressure of the system, and the two is to transform the screw parameters and increase the length to diameter ratio. The injection rate of the precision injection machine is high.
We have worked with the leading manufacturers serving the healthcare industry for 25 years, including diagnostic laboratories and medical device companies. Our know-how in prototyping and medical device molding – coupled with our ever-growing production capacities here in the US – allows us to prototype, injection mold, and 3D-print parts of any complexity.
The phase change contraction is called phase change contraction due to the crystallization of the crystalline resin and the crystallization of the polymer during the orientation process, due to the reduction of the specific volume. The mold temperature is high, the crystallinity is high, the shrinkage rate is large. But on the other hand, the increase of crystallinity will increase the product density, decrease the linear expansion coefficient and reduce the shrinkage rate. Therefore, the actual shrinkage rate is determined by the combination of the two.
In this paper, the precision injection molding is mainly described from the repetition precision of the product size. However, because of the different properties and processing technology of various materials, the precision of the plastic parts can not be equated with the precision of the metal parts. The mold of molded products is an important condition to decide whether the product can meet the design requirements, and the precision injection
From rapid prototyping to product creation at scale, Xcentric, together with Quickparts, brings speed and scale to your prototype, parts, and production projects.
A. POM and carbon fiber reinforced (CF) or glass enhancement (GF). This material is characterized by good creep resistance, fatigue resistance, weatherability, good dielectric properties, difficult to burn, and easy release of lubricants.
Machinability and rigidity, in mold structure design, the number of cavity should not be too much, while the bottom plate, supporting plate and cavity wall should be thicker, so as to avoid the severe elastic deformation of parts under high temperature and high pressure.
B. PA and glass fiber reinforced PA66, its characteristics: strong impact resistance and wear resistance, good flow performance, can form a 0.4mm wall thickness products. Glass fiber reinforced PA66 has heat resistance (melting point 250 C), its disadvantage is that it is hygroscopic, and it should be humidified after general molding.
With Xcentric, you can use plastic, tool steel, and other materials for your molds and start with prototypes to get the approval of the FDA. Then, once you are ready for high-volume production, we can upgrade your molds for continuous performance to create multiple pieces with as little mold degradation as possible.
Compression shrinkage and elastic reduction, the general plastics have compressibility. That is, the specific volume changes significantly at high pressure. Under the general temperature, the specific volume of the molded products will be reduced, the density will increase, the expansion coefficient decreases, and the shrinkage rate will decrease significantly. Corresponding to the compressibility, the molding material has the effect of elastic reduction, which reduces the shrinkage of the products. The factors affecting the molding shrinkage of the products are related to the forming conditions and operating conditions.
Precision injection is a kind of injection molding method which is difficult to meet the requirements of injection molding machine and conventional injection molding process. The concept of precision injection molding is mainly different from “conventional injection molding”. It is based on the rapid development of polymer materials, and uses precise plastic parts to replace high-precision metal parts in the instrument and electronics field.
(3) the temperature control of the working oil must change the high oil temperature, resulting in the fluctuation of injection pressure. We must use the closed loop heating and cooling device to stabilize the oil temperature at 50~55 degrees.
The precision of the mold mainly depends on the high precision of the mold cavity size, accurate positioning of the cavity or whether the precision of the parting surface meets the requirements. The dimensional tolerances of the general precision injection moulds should be controlled below 1/3 of the dimensional tolerance of the products.
Becoming part of Quickparts expands the capabilities and expertise Xcentric offers, delivering injection molding, CNC machining, and other critical services to customers across the globe.
A. because the injection pressure of the precision injection machine is high, it is necessary to emphasize the stiffness of the clamping system. The parallelism of the moving and fixed templates is controlled within the range of 0.05 to 0.08mm.
The hydraulic system of D. precision injection molding machine should fully reflect the integration of mechanical and electrical apparatus.
The mold is demoulding, and the mold should take less cavity number, less and shorter runner as far as possible, and have higher smoothness than ordinary mold, so it is good for demoulding.
Due to the forced stretching of the molecular chain in the flow direction, the macromolecules in the cooling direction will have the trend of rewinding and recovery, and the contraction will take place in the orientation direction. The degree of molecular orientation is related to injection pressure, injection speed, resin temperature and mold temperature. But the main thing is the injection speed.
When Xcentric does the plastic injection molding of medical parts for you, we always create second-to-none pieces with the needed functionality. In addition, our technical engineering team is here to render assistance during all phases of your project and provide design recommendations if necessary.
(2) the thickness of the precision products can be reduced and the length of the molding can be improved. Taking PC as an example, the injection pressure 177MPa of ordinary machine can form 0.2 to 0.8mm wall thickness products, while the injection pressure of precision machine can form products with thickness between 0.15 and 0.6mm when 392MPa is injected. The ultra high pressure injection machine can obtain more products with a larger flow ratio.
D. PC and GFPC. Features: good wear resistance, enhanced rigidity, good dimensional stability, weatherability, flammability and good molding.
As a combined company, Quickparts and Xcentric offer an in-house, end-to-end solution from first prototype to short-run production, offering more to capabilities and benefits to customers both domestically and worldwide.
C. mold is good and rigid, the dimension precision of the cavity, the degree of finish and the precision of the positioning between the templates are high.
(1) high demand for repeated precision (reproducibility) of injection molding parameters, and multistage injection feedback control should be adopted.
As an innovator of on-demand digital manufacturing, Xcentric offers rapid injection molding, CNC machining, and additive manufacturing services from their Michigan facilities in the USA.
B. requires the protection of the low pressure die and the control of the precision of the clamping force. Because the size of the clamping force will affect the degree of the deformation of the die, it will ultimately affect the dimensional tolerance of the parts.
Medical equipment has a lot to do with the quality of healthcare provided. That is why prototyping is a crucial part of the manufacturing process for validating design decisions and making modifications. If you want your components to perform at their best, look no further than Xcentric, a US-based medical plastic injection molding company.
Abstract: Precision Injection Molding is a kind of plastic injection molding method which requires precision mold and requires precision machines. The content of this blog include concept, characteristic, influential factors, selection of plastic material, precision molds, selection and characteristic of precision plastic injection machines.
(5) if the cooling time is the same for the mold temperature control, the thickness of the product with low mold cavity temperature is larger than that of the product with higher temperature. For example, POM and PA materials, the products with a thickness of 50~100 u m at 50 degrees centigrade temperature decrease to 20~40 m at 80, and only 10 m at 100. Room temperature also affects the dimensional tolerance of precision products.
Engineering plastics are deemed to be the materials of choice for prototypes and full-scale production for medical device components. They require less effort when it comes to the finishing stage and is contamination-resistant to ensure the end product’s safe uses.At Xcentric, we are happy to use engineering plastics and other commercially available materials or those supplied by you for your medical device components. When used as part of additive manufacturing or medical plastic molding, these materials are go-to options for implant positioning systems, drug delivery equipment, and housings for:
The material of precision mould is to choose alloy steel with high mechanical strength. The materials for making cavity and runner must undergo strict heat treatment, and select materials with high hardness (forming parts to reach HRC52), good wear resistance and strong corrosion resistance.
(2) the plasticizing quality requirements, uniform plastic plastic not only affects the quality of injection parts, but also affect the melt through the gate by force, in order to get uniform plasticizing, for design and use of special screw plasticizing technology is essential.
No matter how impeccable your pieces look on paper, they do not always translate into flawless parts. By leveraging the skills of the Xcentric team, you can achieve manufacturing perfection and streamline production while saving money and time.
The most important technical indicators for evaluating products are the accuracy of the injection products (dimensional tolerances, geometric tolerances and the smoothness of the surface of the products). For injection molding of precision plastic products, we must strictly control 4 factors, including material selection, mold design, injection molding process and operator’s technology level. Precision injection molding machine precision requirements of the products within 0.01 ~ 0.001mm, many also require precision injection molding injection molding machine with high injection pressure, injection speed high requirements; clamping system has enough rigidity and high precision locking, the so-called locking precision refers to the clamping force uniform and adjustable stable and high repeatability, high position precision mold; requirements for pressure, flow, temperature and measurement can accurately control the corresponding precision, using multi-stage or stepless injection molding process to ensure the reproduction conditions and product size precision etc..
D. plasticizing parts: screw, screw head, check ring, material barrel, etc., should be designed into a structural form with strong plasticizing ability, good homogenization degree and high injection efficiency. The screw drive torque is large and can be continuously variable.
There are four factors that affect the shrinkage: heat contraction, phase change contraction, orientation contraction and compression contraction.
(4) effects of pressure, pressure has great influence on the precision of plastic parts, precisely, the pressure can effectively reduce feeding, plastic deformation, control precision plastic parts, pressure stability determines the forming precision of plastic parts, screw the end position unchanged is the determinants of insurance pressure effect.
We offer extensive expertise in serving the medical industry through injection molding parts and prototypes, ensuring we meet your needs for every project.
The accuracy of displacement sensor is up to 0.1mm, so that we can strictly control the metering stroke, injection stroke and the thickness of the rest pad (shooting monitoring point), so as to ensure the accuracy of each injection and improve the molding accuracy of products. The temperature control of the barrel and nozzle is accurate, the overshoot is small and the fluctuation of temperature is small when heating up. PID control should be adopted in precision injection molding, so that the temperature accuracy is between 0.5 and C.
Given that injection molding and additive manufacturing allows for consistent production, you are sure to avoid the risks of ill-fitting or improperly created implants and other parts with our services.
It can take as little as five days to create your prototypes so that you can handle potential compliance issues early on and bring your product to market faster. Both prototyping and medical device injection molding are carried out at our ISO-certified locations in Michigan.
(1) to improve the precision and quality of the precision products, the injection pressure has the most obvious effect on the shrinkage rate of the product. When the injection pressure is up to 392MPa, the molding shrinkage of the product is almost zero. At this time, the precision of the product is only influenced by the control of the mold or the environment. The experiment showed that the mechanical strength increased by 3% ~ 33% after the injection pressure increased from 98MPa to 392MPa.
The proportion system of proportional pressure valve, proportional flow valve or servo variable pump should be adopted in the
Thermal shrinkage is the thermal physical characteristic of the molding material and the mold material. The mold temperature is high, the temperature of the product is high, the actual shrinkage rate will increase, so the precision injection mold temperature should not be too high.
C. because of the high speed of the precision injection molding machine, it is necessary to emphasize the speed of the reaction of the hydraulic system.
Choose from over 40 stock materials for your medical components, or supply materials on your own to ensure the required mechanical properties!
GETTING A QUOTE WITH LK-MOULD IS FREE AND SIMPLE.
FIND MORE OF OUR SERVICES:
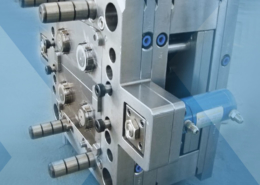
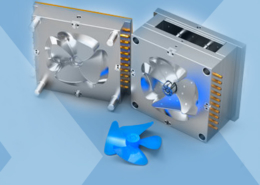
Plastic Molding

Rapid Prototyping
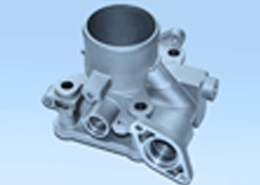
Pressure Die Casting
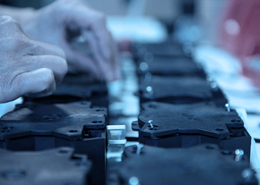
Parts Assembly
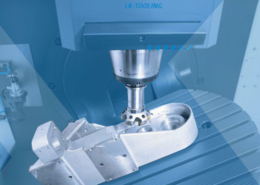