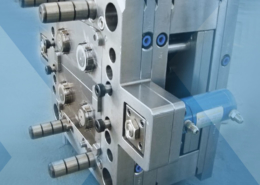
PET Preform Injection Molding : Troubleshooting Guide for ... - preform injectio
Author:gly Date: 2024-10-15
Overmolding is the process through which the injection mold forms multiple layers around a single product. It does this by re-introducing the injection molded parts into the mold.
To understand how it works, you must have basic knowledge of the injection molds tools, what they are, how they work, where to find them, and which injection molding tools are best for specific tasks.
The cavity image is an empty space in the injection mold that transforms the molten plastics to their desired shape and size.
At SMC we understand that precision matters when it comes to micro molded medical parts. We manufacture even the smallest parts while still holding precise tolerances.
The process for injection molding tooling isn’t that complicated. However, the process may vary depending on the products, materials, and specifications you want to meet.
The overmolding process is simple. You start by molding the plastic products with a base-color material, ensuring you leave enough room to fit more plastic products with different colors.
The small opening created when a mold opens is called a gate. Plastic enters the mold cavities through these openings. There are two main gate types found in injection molds. They include:
You can build your molding tools using aluminum or steel. However, aluminum isn’t the best option when producing high-tolerance plastic parts. You should, therefore, use it when making low-tolerant components only.
The first stage in the injection molding process is the design creation and engineering. It involves creating a 3D CAD model of the injection mold and testing its performance, to see if it produces plastic parts with the desired shapes, sizes, and tolerance, using a simulation software.
Copyright ©2023 SMC Ltd. All rights reserved. SMC and the SMC logo are registered trademarks of SMC Ltd. Privacy and Cookie Policy UnitedHealthcare’s Transparency in Coverage
As mentioned, mold plates are one of the molding tools used to produce plastic containers. You can use the number of mold plates to differentiate various plastic injection tools. They include the following:
True micro-molded parts can be smaller than the pellet of resin used, allowing multiple parts to be made from one resin pellet. Our efficient material and tooling techniques deliver exceptional yields of 10,000 parts per pound, including the runner. While miniature parts are the next step larger in physical size, they often have micro features. Knowing how to inspect and package micro and miniature components, assures parts to specification from the molding operation to the end device.
When the molten plastic molds, the clamping unit slides the B plate from the injection mold creating an exit point and pushing the plastic products out of the injection molds using ejector pins.
Generally, this injection molding tool can have single or multiple cavities, depending on your production volume. Single-cavity molds are called single-impression cavity molds, while those with multiple cavities are called multiple-impression cavity molds.
Tools mold design, cavitation, and materials impact the plastic injection tooling tolerance. A simpler process is likely to get and maintain a tighter tolerance than complex parts because they can put tight tolerance at risk as there are other variables, such as the number of cavities, to consider.
The ejector mold or the B plate is the part of the injection molding tool that acts as the exit point through which plastic parts eject from the injection mold.
The next process in the injection molding tooling involves producing several test parts and measuring the properties and dimensions of the molded plastics to see if they meet the required specifications and standards.
SMC's micro molding capabilities yield 10,000 parts per pound of resin. Micro parts are considered less than 0.003 cubic inches and fall between 0.140 x 0.140 x 0.155 inches.
An injection mold or A plate is a machined tool used in the plastic injection molding process. It molds the molten plastics into finished plastic goods.
Tooling material selection is one of the most overlooked yet critical injection molding tooling designs. Your choice of material will significantly influence the lifespan of your injection mold tooling.
There are many types of injection mold you could use for your plastic injection molding process, but two-plate molding is the most used.
Finding the best manufacturing company for your custom injection molding process may be a little challenging. You must know the questions to ask and the response you need.
Plastic injection molding or injection molding is the production of plastic parts in large quantities using injection molding machines.
Generally, you’ll need sophisticated plastic injection molding tools to produce complex parts with added features like threads and undercuts. You may also require additional rotating mechanical gears in case of complex geometries.
Now that you know how plastic injection molding tools work, you can start your project. It’s a pretty straightforward process to create plastic containers in large quantities within a reasonable time frame. It’s also affordable and will help you produce quality pieces within the shortest time possible.
The next step is to create a prototype mold to test the design. This helps you decide whether or not your model will give you the desired outcome. You can also use this stage to improve your mold design before it reaches the final stages.
Another way to differentiate the plastic injection molding tools is through their feeding system, a collection of channels, including the runners, gates, and sprues, which direct the molten plastic into the mold cavity.
It’s the entry point that allows the melted plastic to pass through from the injection unit. The entrance of the injection mold is called the sprue bushing. They connect to runners, tunnels connecting the sprue to the cavity image.
Here’s where you produce the actual mold. You can use various materials, like aluminum and steel, and techniques, such as electrical discharge machining (EDM), CNC machining, or 3D printing to produce the molds.
One of the primary ways to differentiate injection molding is by the number of mold cavities. There are three different types of injection molds under this category. They include the following:
Now that you know your mold qualifies, you can use it for mass production. This involves filling the various mold cavities with the molten plastics and giving it enough time to cool and solidify, taking the mold shape.
The process doesn’t end with a single production. You must maintain the injection molding to ensure it continues producing the high quality products. This means repairing worn parts, making needed adjustments, and cleaning it from time to time.
GETTING A QUOTE WITH LK-MOULD IS FREE AND SIMPLE.
FIND MORE OF OUR SERVICES:
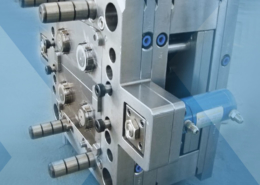
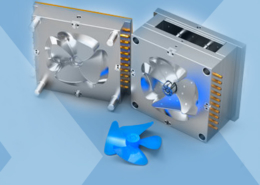
Plastic Molding

Rapid Prototyping
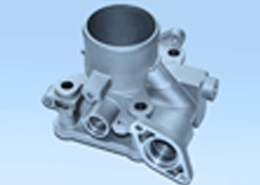
Pressure Die Casting
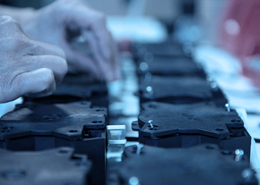
Parts Assembly
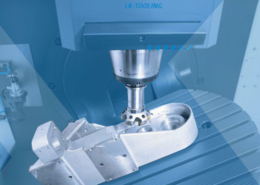