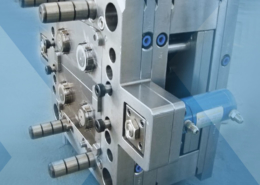
Exploring the Advantages of Low Volume Plastic Injection Molding
Author:gly Date: 2024-06-08
In the realm of manufacturing, efficiency, flexibility, and cost-effectiveness are crucial factors that drive success. Low volume plastic injection molding emerges as a versatile solution, offering tailored manufacturing capabilities for businesses requiring smaller quantities of plastic parts. This article delves into the intricacies of low volume plastic injection molding, examining its significance, applications, technical aspects, and future prospects.
Introduction: Unveiling the Potential of Low Volume Plastic Injection Molding
Low volume plastic injection molding, also referred to as small batch injection molding, caters to the needs of businesses seeking to produce plastic parts in limited quantities. While traditional injection molding techniques are optimized for high-volume production, low volume plastic injection molding fills a crucial niche by providing cost-effective, customizable solutions for small-scale manufacturing needs. This technique offers businesses the flexibility to iterate designs, respond quickly to market demands, and minimize upfront costs associated with tooling and production setup.
Customization Capabilities: Tailoring Solutions to Unique Requirements
One of the primary advantages of low volume plastic injection molding is its ability to provide tailored solutions to meet unique requirements. Whether it's prototyping new designs, producing custom components, or fulfilling niche market demands, low volume plastic injection molding offers the flexibility to manufacture parts with precision and consistency. This customization capability empowers businesses to optimize product designs, enhance functionality, and differentiate themselves in competitive markets, thereby driving customer satisfaction and brand loyalty.
Cost Efficiency: Minimizing Financial Risks
Despite catering to smaller production volumes, low volume plastic injection molding remains highly cost-effective when compared to alternative manufacturing methods. By minimizing tooling costs, reducing material waste, and optimizing production processes, businesses can achieve significant cost savings per unit, even at lower volumes. This cost efficiency is particularly advantageous for startups, small businesses, and niche manufacturers looking to minimize financial risks while maintaining high-quality standards and meeting customer expectations.
Rapid Prototyping: Accelerating Time-to-Market
In today's fast-paced business environment, speed is paramount. Low volume plastic injection molding enables rapid prototyping and iteration, allowing businesses to accelerate time-to-market and gain a competitive edge. By leveraging digital design technologies and agile manufacturing processes, companies can quickly iterate designs, test concepts, and gather feedback from customers, facilitating rapid innovation and adaptation to changing market demands. This agility in product development and production enables businesses to seize opportunities, respond to trends, and stay ahead of the competition.
Material Selection: Balancing Performance and Cost
An essential aspect of low volume plastic injection molding is the careful selection of materials to balance performance requirements with cost considerations. While high-performance engineering resins offer superior mechanical properties and durability, they may come at a higher cost per unit. Conversely, commodity plastics offer affordability but may lack the desired performance characteristics. Finding the right balance between material properties, cost, and production volume is critical to optimizing the manufacturing process and delivering value to customers.
Quality Assurance: Ensuring Consistency and Reliability
Maintaining consistent quality standards is paramount in low volume plastic injection molding to ensure the reliability and performance of the final parts. Robust quality assurance measures, including rigorous testing, inspection protocols, and process monitoring, are essential to identify and mitigate any potential defects or inconsistencies. By prioritizing quality at every stage of the manufacturing process, businesses can instill confidence in their products, build lasting relationships with customers, and enhance brand reputation.
Future Outlook: Embracing Innovation and Collaboration
As we look to the future, the potential of low volume plastic injection molding remains vast and untapped. With ongoing advancements in materials science, automation, and digital manufacturing technologies, the capabilities of low volume plastic injection molding are poised to expand further. Moreover, fostering collaboration between industry stakeholders, academia, and research institutions can drive innovation, accelerate technology adoption, and unlock new possibilities for efficiency, sustainability, and customization in manufacturing.
Conclusion: Embracing the Power of Low Volume Plastic Injection Molding
In conclusion, low volume plastic injection molding represents a pivotal innovation in the realm of manufacturing, offering customized solutions, cost efficiency, and rapid prototyping capabilities for businesses of all sizes. By harnessing the power of low volume plastic injection molding, companies can unlock new opportunities for customization, innovation, and market agility, driving growth and competitiveness in an increasingly dynamic business landscape. As we continue to explore and embrace the potential of this transformative technology, collaboration, innovation, and adaptability will be key to unlocking its full potential and shaping a more efficient, flexible, and sustainable future for manufacturing.
GETTING A QUOTE WITH LK-MOULD IS FREE AND SIMPLE.
FIND MORE OF OUR SERVICES:
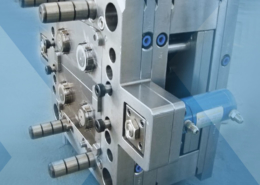
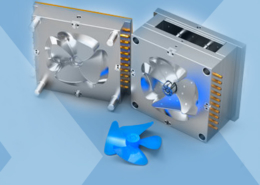
Plastic Molding

Rapid Prototyping
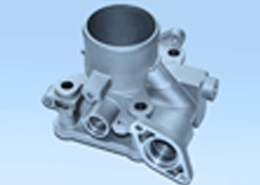
Pressure Die Casting
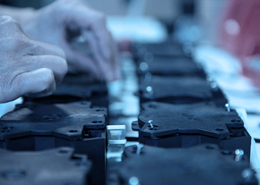
Parts Assembly
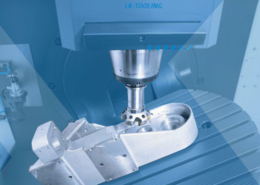