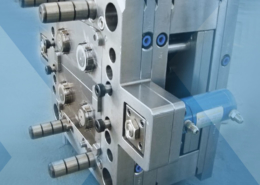
PCS Company Suppliers Showroom - pcs injection molding
Author:gly Date: 2024-10-15
Medical injection molding is a core technology of Aberdeen Technologies and represents a cutting edge solution to the manufacturing needs of healthcare companies who produce medical molded devices. As an insert molding manufacturer, we provide assistance to device manufacturers who approach us with new product concepts and ask us to mold parts for clinical trials and marketing evaluations.
Aberdeen’s primary goal is total customer satisfaction for even your most challenging projects. Our company culture is one of honor, respect and service with the highest degree of competence and professionalism that you will find anywhere.
In the medical field, we often see metal combined with the plastic part. This is called insert molding and is a very common practice for injection molders to do. You see this all over the medical arena from needles to EKG hook up leads and more.
The most common types of materials used in medical insert molding are thermoplastics. These are materials that can be heated up into a molten state and pushed through a barrel into a mold. These molds can simply be open and shut type designs, which are what you would expect for, say a simple product such as a cake mold. Or they can be very complex with moving side parts called slides. Of course, the simpler the mold the better for maintenance and longevity. However, complex parts will need these complex designs in order to produce the desired part.
We use cookies on this website to ensure your user experience. Please click the button if you agree to the use of cookies. When you keep browsing this website, this will also mean that you are giving consent to the use of cookies.
From the standpoint of temperature variance of molten resins, theoretically it is desirable that screw rotational speed be lower and the back pressure be higher, but the following parameters are practical from the productivity point of view:
The process is capable of making FDA approved medical devices that are both durable and reliable. This type of molding can also be used to make prototypes to send and get the much-needed FDA approval. Medical injection molding can be performed in a clean room and the components can be sterilized without harm as well. Let's take a look at injection molding.
The discoloration of a molding is related to the material temperature and retention time in the cylinder of the molding machine. Although the discoloration slightly varies with grades, the general discoloration limit for DURACON M90-44 is shown in Fig. 4-4 The permissible retention time is determined by discoloration rather than deterioration of properties.
Sometimes the components need to be manufactured separately and then assembled. This is very common in many cases and this can be done by hand or robot.
Although the normal injection speed is 5-50mm/s (0.3-3m/min), the actual speed is determined in consideration of molding shape, wall thickness, required properties of moldings, runner thickness, gate size, etc.:
Injection molding is a very common way to form plastic parts and components. Depending on the material, the parts can be very strict with their tolerances as well as easy to process. Injection molding is one of the most common types of forming plastics. It is used in a variety of industries and not just for medical injection molding. In fact, you probably have a wide variety of injection molded parts all around you and simply don't know it. Your basic pens, your keyboard, and even your phone have injection molded components in them.
It should be taken into consideration that excessively low back pressure causes unstable metering due to the trapping of air and excessively high back pressure causes drooling from the nozzle and prolongs the plasticization time.
Prime examples were molding non-communicating passageways through a plastic manifold, molding critical tolerance pacemaker components, and even molding around glass formations without breaking or cracking. Our advanced injection molding equipment makes even the most difficult projects possible.
Although the injection pressures of DURACON are as follows, the actual pressure is determined in consideration of appearance and dimension of moldings, flowability, mold shrinkage and the required properties of the moldings.
The melting point of DURACON® POM is approximately 165°C, but from the practical point of view a material temperature of 190-210°C (if possible 200-210°C) is appropriate. The material temperature is generally set 10-15°C higher than the cylinder temperature (front section). An example temperature distribution of the cylinder is shown below, and it is recommended that the temperature be directly measured by a thermometer inserted into the block of molten material as it exits the nozzle.
We provide assistance throughout each stage of your program, from design recommendation through mold tooling fabrication, prototyping, first article approval, process validation, full scale production medical molding, and transfer of turnkey system to customer facilities if requested.
However, there are other types of plastics called thermosets that also can be used for injection molding, but the process is far different. These materials are most likely not going to be used for medical molding as they cannot be recycled as easily as the thermoplastic materials. Because of this, you don't see thermosets used as often as you do thermoplastics. A good example of a thermoset is your car tires. This is where they cannot be melted down and reshaped into something.
Although the normal mold temperature of DURACON is 60-80°C, the actual mold temperature should be determined in consideration of properties of moldings, surface appearance, dimensional change in use, molding cycle time and other factors. For example, in case of moldings used in elevated temperature, mold temperature must be higher than the application temperature, or molded products must be annealed in order to prevent dimensional change during use. Moldings which require mirror surfaces are often molded at a mold temperature as high as 120°C. When the mold temperature is set at temperatures as low as 30-40°C in order to shorten the molding cycle, the following points should be taken into account:
Medical injection molding is a manufacturing process that produces plastic medical devices and components. It involves melting plastic resin pellets and injecting the molten material into a mold to create a specific shape. This process allows for precise control over the product's size and shape and is subject to strict quality and regulatory standards.
Once these new devices are produced, we assist our customers in transitioning the project into the production phase. Quality and customer satisfaction are our primary goals, and Aberdeen can work with both high and low quantity requirements with over 700 square feet of cleanroom injection molding space.
GETTING A QUOTE WITH LK-MOULD IS FREE AND SIMPLE.
FIND MORE OF OUR SERVICES:
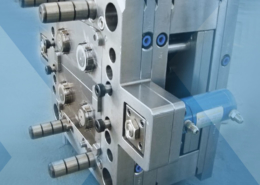
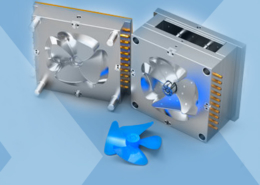
Plastic Molding

Rapid Prototyping
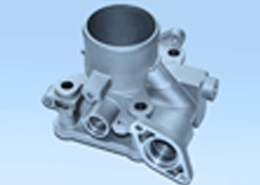
Pressure Die Casting
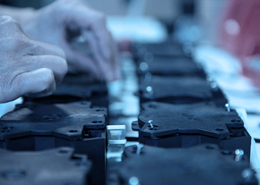
Parts Assembly
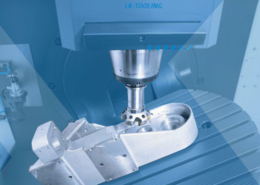