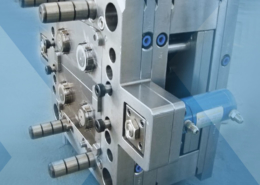
LDPE Injection Molding: Revolutionizing Plastic Manufacturing
Author:gly Date: 2024-06-08
Low-density polyethylene (LDPE) injection molding stands at the forefront of modern plastic manufacturing, offering unparalleled versatility and efficiency. In this comprehensive exploration, we delve into the intricacies of LDPE injection molding, from its fundamental principles to its diverse applications and future prospects.
Introduction: Unveiling LDPE Injection Molding
LDPE injection molding, a cornerstone of contemporary plastic fabrication, marries cutting-edge technology with ingenious design. Its significance reverberates across industries, from packaging to automotive, owing to its remarkable properties and cost-effectiveness.
Material Properties and Composition
LDPE, characterized by its branched molecular structure and high degree of flexibility, exhibits superb moldability and impact resistance. Its composition, predominantly consisting of ethylene monomers, imbues LDPE with unique thermal and chemical stability, rendering it an ideal candidate for injection molding processes.
Process Overview: From Pellet to Product
The LDPE injection molding process commences with the conversion of LDPE pellets into molten form, facilitated by controlled heating within an injection molding machine. Subsequently, the molten LDPE is injected into a mold cavity, where it assumes the desired shape under pressure. The cooling phase solidifies the material, culminating in the extraction of the finished product.
Design Considerations and Mold Optimization
Achieving optimal results in LDPE injection molding hinges upon meticulous design considerations and mold optimization techniques. Factors such as gate design, cooling rate, and part geometry profoundly influence the quality and integrity of the final product. Employing advanced simulation software enables engineers to fine-tune these parameters, thereby enhancing efficiency and reducing production costs.
Applications Across Industries
The versatility of LDPE injection molding finds expression in a myriad of applications spanning diverse industries. In the realm of packaging, LDPE facilitates the production of lightweight, yet durable containers, safeguarding perishable goods during transit. Automotive manufacturers harness the superior impact resistance of LDPE to fabricate intricate components, ensuring passenger safety and vehicle longevity.
Environmental Implications and Sustainable Practices
Amid growing environmental concerns, the quest for sustainable practices in plastic manufacturing assumes paramount importance. LDPE injection molding, with its recyclability and eco-friendly attributes, emerges as a beacon of hope in this regard. Adoption of biodegradable additives and incorporation of recycled LDPE pellets herald a paradigm shift towards a greener, more sustainable future.
Challenges and Future Directions
Despite its myriad benefits, LDPE injection molding confronts certain challenges, including limited dimensional stability and susceptibility to chemical degradation. Addressing these hurdles necessitates concerted research efforts aimed at developing novel additives and refining processing techniques. Furthermore, exploring emerging technologies such as 3D printing holds promise in revolutionizing the landscape of LDPE fabrication.
Conclusion: Pioneering the Future of Plastic Manufacturing
In conclusion, LDPE injection molding epitomizes the pinnacle of innovation in plastic manufacturing, offering a perfect amalgamation of versatility, efficiency, and sustainability. As we navigate the complexities of the 21st century, LDPE stands poised to spearhead a new era of transformative change, transcending boundaries and reshaping industries. Embracing this technology heralds not only economic prosperity but also environmental stewardship, ensuring a brighter, more sustainable tomorrow.
GETTING A QUOTE WITH LK-MOULD IS FREE AND SIMPLE.
FIND MORE OF OUR SERVICES:
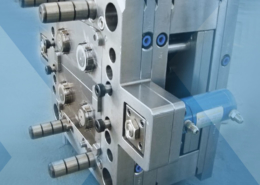
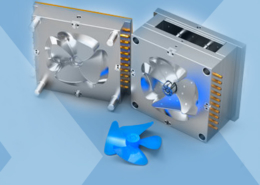
Plastic Molding

Rapid Prototyping
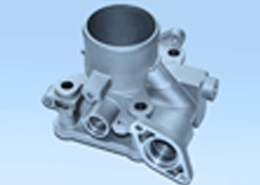
Pressure Die Casting
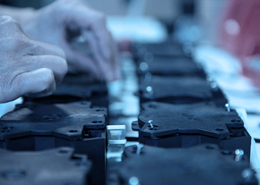
Parts Assembly
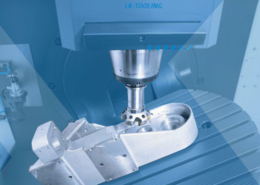