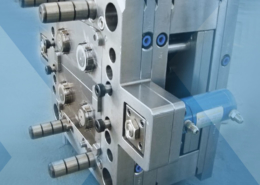
PCS Company - pcs injection molding
Author:gly Date: 2024-10-15
For an injection molder, it’s important to set the injection speed to fill the mold quickly and set the injection pressure so that it’s relatively high. And, because there are important differences between polyethylene types, designers may need help comparing the material properties of LDPE, LLDPE, MDPE, HDPE, and UHMWPE plastics — the following sections explain what designers need to know.
We exist to eliminate bottlenecks in new product development by integrating the people, processes, and platform you need to source custom parts.
By signing up, you agree to our Terms of Use and Privacy Policy. We may use the info you submit to contact you and use data from third parties to personalize your experience.
Overmolding: In overmolding, multi-component pieces are constructed through an “add-on” type of process, where one component is constructed and allowed to fully cool and harden, and then used as a base or core as another portion of the piece is molded around (or “over”) it. Overmolding allows for extensive flexibility with materials and construction, since the core piece does not even necessarily have to be injection molded (or plastic). For instance, a rubber grip can be overmolded around a metal piece.
Polyethylene is generally lightweight, chemically resistant, and electrically insulating. The amount of stiffness and strength varies by PE type, but injection molded PE is often used in parts that need to withstand stress or strain. For designers, selecting the right type of polyethylene may include tradeoffs since higher stiffness is also associated with greater brittleness. Different PE plastics also provide different types of resistance to specific chemicals, or to environmental factors such as sunlight.
Low-density polyethylene (LDPE) remains flexible even at low temperatures, and has good strength relative to its density. It can withstand a significant amount of stretching before it breaks, and is odorless, sterile, and watertight. LDPE also maintains its structural integrity and has low water absorption. Applications for injection molded LDPE include hose fittings for water supplies.
If you’re thinking about selecting polyethylene plastic for your next injection molding project, it’s important to understand the properties, advantages, disadvantages, and applications of each type of PE plastic. This article addresses these subjects, but for a successful project, you’ll also need to follow injection molding best practices — so check out our Injection Molding Design Guide, a free e-book available for download, has the info you need:
Multi-shot molding: In multi-shot molding, a “layering” effect is achieved by injecting partial shots of material in sequence into the mold cavity. The materials neither mix nor harden around one another. Instead, they are “stacked” into the finished piece. Multi-shot molding is also known as sequential molding.
By signing up, you agree to our Terms of Use and Privacy Policy. We may use the info you submit to contact you and use data from third parties to personalize your experience.
Our trained employees ensure your parts will be delivered on time and to spec.
We exist to eliminate bottlenecks in new product development by integrating the people, processes, and platform you need to source custom parts.
Mixed materials: In what might be considered the simplest form of two-component injection molding, two materials can be fed into the injection molding machine simultaneously and mixed as they are heated. This method could be used for aesthetic purposes. Mixing, for example, a dye with the resin to achieve a different color or a more attractive finished appearance. It could also be used to achieve a different physical property than just one resin would offer. For example, mixing a harder resin in to strengthen a piece made primarily from a softer plastic.
Bi-injection molding: In this process, different materials are fed into a mold cavity at different points, through different gates. They begin to harden before their meeting point within the cavity, resulting in a layered effect. In co-injection molding, the materials are not intended to physically mix together. The meeting point of the two materials and, thus, the appearance and function of the finished piece, can be adjusted by fine-tuning the injection speed of each material.
Medium-density polyethylene (MDPE) is durable with high impact resistance and good chemical resistance. It has good shock and drop resistance and can resist many types of chemicals, including diesel fuels, acids, and oils. MDPE resins provide higher stiffness than LDPE and LLDPE, but less than HDPE plastic — so it’s an “in-between” option. Despite its advantages, MDPE has poor resistance to UV light and to solvents.
Polyethylene with a lower density (e.g., LDPE and LLPDPE) has lower crystallinity and greater flexibility. PE with a higher density (e.g., MDPE and HDPE) has higher crystallinity and greater stiffness. Crystallinity is also related to molecular weight, which affects both material properties and processing parameters.
High-density polyethylene (HDPE) is more rigid because of its high crystallinity, but is still a relatively flexible plastic. Compared to other forms of polypropylene, HDPE has a higher tensile strength. This low-cost polymer provides good processability and combines excellent electrical insulating properties with low water absorption. Some HDPE grades are designed to withstand environmental stress-cracking or to provide high stiffness or low shrinkage.
In plastic injection molding, molecular weight is significant not only because of its relationship to crystallinity, but also to a thermoplastic’s melt rheology. Specifically, higher molecular weight resins like UHMWPE have higher viscosity and a higher pressure drop in the injection mold cavity during filling. Consequently, higher packing pressure must be used to compensate for the cavity pressure drop. Otherwise, the lower pressure melt will result in shrinkage in the final part.
Access a wide breadth of capabilities through our highly vetted network.
Accelerate development with instant quotes, expert DFM, and automated production updates.
HDPE’s high mold shrinkage is a disadvantage, however. Most of this shrinkage occurs during cooling and can affect dimensional stability and part tolerances. Although it’s possible for an injection molder to accurately predict the amount of shrinkage, molded HDPE parts that shrink unequally can warp, a common molded part defect. HDPE is also susceptible to stress cracking and has poor UV resistance and low heat resistance. Some grades offer improved performance properties, such as resistance to sunlight.
By signing up, you agree to our Terms of Use and Privacy Policy. We may use the info you submit to contact you and use data from third parties to personalize your experience.
As a designer, it’s not your job to control these processing parameters; however, a skilled injection molder will make getting them right a priority.
By signing up, you agree to our Terms of Use and Privacy Policy. We may use the info you submit to contact you and use data from third parties to personalize your experience.
Polyethylene injection molding produces parts from polyethylene (PE), the world’s most commonly used plastic material. This thermoplastic polymer has a variable crystalline structure that, in part, determines its material properties. With plastics, the degree of crystallinity has a significant effect on hardness and density. In turn, this affects attributes such as stiffness and flexibility. Applications for polyethylene range from packaging and pipes to electrical, medical, and industrial products.
By signing up, you agree to our Terms of Use and Privacy Policy. We may use the info you submit to contact you and use data from third parties to personalize your experience.
In semi-crystalline materials like PE plastic, the mold temperature affects the degree of crystallinity in the polymer. That’s because crystals only form at temperatures below a polymer’s melting point, but above its glass transition (Tg) temperature. With polyethylene, the mold temperature can also vary significantly, depending on the type of PE plastic that’s processed.
LDPE is susceptible to stress cracking, however, and has lower strength and stiffness than other types of polyethylene. Although LDPE has good resistance to alcohols, dilute alkalis, and acids, it has limited resistance to mineral oils, oxidizing agents, and some types of hydrocarbons. This low-cost polymer is also highly flammable and offers poor resistance to ultraviolet (UV) light, which makes it unsuitable for outdoor applications.
Melt temperature is the temperature of a polymer as it exits the nozzle and enters the mold. This processing parameter affects viscosity, a measure of resistance to flow. It also affects molecular weight, which determines how far a plastic can stretch before rupturing. Depending on the type of polyethylene, melt temperature can vary significantly.
Injection molding offers an extremely versatile range of manufacturing options, as the nature of the process means that it’s suitable for a host of part and product designs and types. Beyond the standard injection molding process, even more versatility and efficiency can be achieved via two-component injection molding. As the name suggests, two-component injection molding involves using more than one material in the molding of one part. This differs from the more typical single-component injection molding process, where only one base resin is injected into a mold.
Because UHMWPE is almost totally inert, this type of polyethylene can be used in corrosive or aggressive environments at moderate temperatures. It remains resistant to many solvents at higher temperatures, but with notable exceptions such as aromatic and halogenated hydrocarbons. The specific UHMWPE grade determines the amount of resistance wear, chemicals, and the impact that the material provides.
In addition to material properties and injection molding guidelines, it helps to understand four key processing parameters that injection molders need to control.
With specific types of additives, however, LDPE can have UV resistance and even serve as an anti-static barrier for sensitive electronic components. Importantly, LDPE is relatively easy to process during plastic injection molding. LDPE has a melt temperature between 160°C to 260°C and post-mold shrinkage is between 1.5% and 3.5%.
As with most any manufacturing process, two-component injection molding isn’t the right answer for every application. In scenarios where certain material properties are required — for example, medical or food applications — two-component molding may compromise the critical safety qualities of the core material. Two-component molding also shouldn’t be used when only one component will suffice. For example, with purely functional products such as mechanical components and other commodities. In other words, two-component molding shouldn’t be sought just because it’s a possibility. Unnecessary addition of components and thus, resource expenditure, results in wasted production efficiency.
By signing up, you agree to our Terms of Use and Privacy Policy. We may use the info you submit to contact you and use data from third parties to personalize your experience.
Linear-low-density polyethylene (LLDPE) is not only flexible and stretchable, but also puncture and impact resistant. Compared to LDPE, injection-molded LLDPE has greater chemical resistance, better mechanical characteristics at high and low temperatures, high surface gloss, and good resistance to cracking. This type of PE plastic also has good stress cracking and impact resistance while providing a barrier to water.
Co-injection molding: In co-injection molding, two full material shots are injected into the cavity, one right after the other, resulting in the materials hardening around each other while becoming fully bonded. This process is useful for creating, say, a soft rubber exterior around a hard plastic core.
Ultra-high molecular weight polyethylene (UHMWPE) has excellent mechanical properties, such as high abrasion resistance and impact strength. With its low coefficient of friction, it also provides good abrasion and wear resistance. Medical applications for UHMWPE include the articulating surfaces of joint replacements used in hip, knee, ankle, and shoulder surgery.
At RevPart, we specialize in helping our customers find the best solution for their product, with innovation, quality and efficiency as our core goals for you. Our extensive prototyping capabilities and services — including injection molded prototypes — mean that we can work with you in a cost-efficient manner to fine-tune the best design for your product, including two-component molding methods. The advantages of injection molding prototypes allow us to work together to zero in on how the full production process eventually can and should work — a benefit that isn’t available through other methods of prototyping.
By signing up, you agree to our Terms of Use and Privacy Policy. We may use the info you submit to contact you and use data from third parties to personalize your experience.
With plastic injection molding, HDPE has a melt temperature between 200°C and 300°C and a mold temperature between 10°C and 80°C. A higher mold temperature can improve the appearance of a molded HDPE part and provide a shinier and glossier surface. Mold shrinkage ranges between 1.5% and 4%, depending on processing conditions and the thickness of the final component.
Create high quality custom mechanicals with precision and accuracy.
Polyethylene injection molding offers many advantages, but it can also pose challenges during material selection, part design, and processing. With Fictiv, your operating system for custom mechanical parts, you get expert design for manufacturing (DFM) feedback along with your quote and manufacturing guidance every step of the way. Our injection molding expertss understand the properties of each PE plastic and our global network of manufacturing partners have experience injection molding LDPE, LLDPE, MDPE, HDPE, and UHMWPE.
By signing up, you agree to our Terms of Use and Privacy Policy. We may use the info you submit to contact you and use data from third parties to personalize your experience.
Two-component injection molding can be achieved in several ways, with each method yielding different results and effects. Below, we’ll take a look at each:
By signing up, you agree to our Terms of Use and Privacy Policy. We may use the info you submit to contact you and use data from third parties to personalize your experience.
Ready to get started? Create a free Fictiv account and upload your design to get a quote today — we produce complex injection molded parts at ridiculous speeds!
LLDPE is similar in structure to HDPE but has a higher softening point and a higher strength and relative breaking extension. LLDPE is also more difficult to process than LDPE and has a narrower temperature range for heat sealing, which is used in packaging applications and industrial laboratories. Applications for injection molded LDPE include enclosures, caps, snap fits, and lids.
With extensive knowledge and experience with materials and various methods of injection molding and other manufacturing, we offer our expertise in the service of creating the best possible product for you.
Two-component injection molding can be the right choice in a number of scenarios, depending on the requirements and design of the piece or product.
GETTING A QUOTE WITH LK-MOULD IS FREE AND SIMPLE.
FIND MORE OF OUR SERVICES:
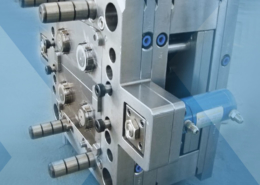
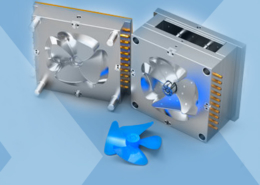
Plastic Molding

Rapid Prototyping
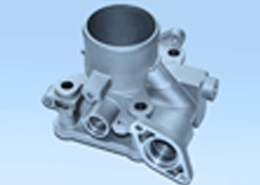
Pressure Die Casting
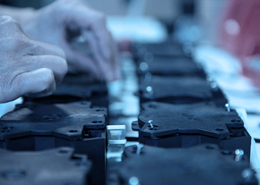
Parts Assembly
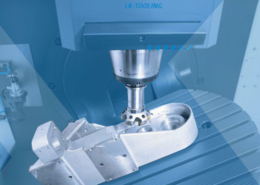