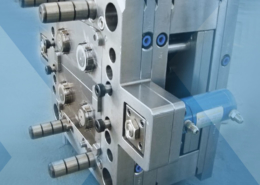
OGM Medical: Injection Moulding - medical injection moulding
Author:gly Date: 2024-10-15
POM injection molding produces parts made of polyoxymethylene (POM), an engineering thermoplastic that includes both homopolymer and copolymer versions of acetal. Homopolymer acetal has a highly ordered crystalline structure for increased strength, but can be difficult to process because of its precise melt temperature. Copolymer acetal has a wider range of processing temperatures, but is mechanically weaker because it only has regions of crystallinity.
Ready to get started? Create your free Fictiv account and request an injection molding quote today — we make complex parts at ridiculous speeds!
By signing up, you agree to our Terms of Use and Privacy Policy. We may use the info you submit to contact you and use data from third parties to personalize your experience.
By signing up, you agree to our Terms of Use and Privacy Policy. We may use the info you submit to contact you and use data from third parties to personalize your experience.
Proper modeling is important because POM is prone to shrinkage rates of 2 to 3.5%. Most shrinkage occurs while the part is still within the mold during the cooling stage, but a small amount of shrinkage still occurs after ejection, especially for Delrin®. This homopolymer POM variant has higher shrinkage rates than copolymer acetals.
Injection molded POM products can be made of grades that are rated as food safe in accordance with FDA, USDA, NSF, Canada AG, or 3-A Dairy material standards. Applications include injection molded plastic parts for food processing equipment.
Our trained employees ensure your parts will be delivered on time and to spec.
We exist to eliminate bottlenecks in new product development by integrating the people, processes, and platform you need to source custom parts.
Accelerate development with instant quotes, expert DFM, and automated production updates.
POM has excellent fatigue resistance and can be used in applications that have multiple load/unload cycles, such as gears. Homopolymer POM (e.g., injection molded Delrin®) has greater fatigue strength than copolymer POM.
Injection molded POM has good resistance to creep, the tendency of a solid material to undergo slow deformation when subjected to persistent mechanical stresses. POM can also be subjected to long-term loading with minimal permanent deformation.
Below you’ll find the physical, mechanical, and molding properties of some POM trade names. The only homopolymer listed is Delrin 100, and the other POM plastics are acetal copolymers.
By signing up, you agree to our Terms of Use and Privacy Policy. We may use the info you submit to contact you and use data from third parties to personalize your experience.
Low-Density Polyethylene (LDPE) was discovered by accident in 1933 by chemists Reginald Gibson and Eric Fawcett at Imperial Chemical Industries (ICI) in the United Kingdom. During an experiment involving the high-pressure polymerization of ethylene, they inadvertently produced a white, waxy substance, which turned out to be LDPE.
As the data above shows, POM has excellent tensile and flexural strength but a high shrink rate. The homopolymer Delrin® has the greatest tensile strength because of its highly ordered crystalline structure. Note that some POM grades can be modified with fillers to increase mechanical strength, corrosion resistance, or UV (ultraviolet light) resistance.
Many suppliers offer copolymer acetals but only DuPont makes the resin that is used in Delrin®, a homopolymer with exceptional properties. Delrin® plastics are graded based on strength, stiffness, viscosity, and resistance, with applications that support both plastic injection molding and CNC machining. Applications for injected molded POM parts include components that are used in automotive, fluid handling, medical, and healthcare applications.
If you have an injection moulding project and are considering using LDPE, please get in touch with our technical team on 01280 706335 for a free consultation!
Welcome to BPY Plastics Ltd, your one-stop shop for all your injection moulding needs! As a leading supplier in the industry, we offer a wide range of products and services to meet our customers' needs. Our commitment to quality and innovation has earned us a reputation for excellence.
Create high quality custom mechanicals with precision and accuracy.
POM can be challenging to process because of its high-temperature sensitivity. For injection molders, there are four key considerations.
Injection molded POM can withstand continuous service temperatures up to 105°C. Homopolymer POM has higher instantaneous heat resistance and copolymer POM has a better long-term thermal resistance. POM plastic is flammable, however, and it won’t self-extinguish once it’s ignited.
POM plastics have excellent mechanical properties for rigidity, tensile strength, and flexural strength — but homopolymer acetals have better mechanical properties. Applications for high-strength POM include conveyor belts and safety restraints.
Although POM has a relatively high shrinkage rate during injection molding, this plastic provides excellent dimensional stability once parts have cooled. This enables injection molded POM to retain its form and maintain its tolerances in demanding applications.
By signing up, you agree to our Terms of Use and Privacy Policy. We may use the info you submit to contact you and use data from third parties to personalize your experience.
These properties make LDPE suitable for a wide range of injection molding applications, including packaging (bottles, caps, and containers), consumer goods (toys and household items), electrical components, and medical products. Its versatility, cost-effectiveness, and ease of processing make it a popular choice in many industries.
POM can be challenging to process, but injection molded POM parts have excellent properties such as high lubricity, mechanical strength, and fatigue resistance. When you partner with Ficiv, we provide design for manufacturing (DFM) feedback along with your injection molding quote and manufacturing guidance every step of the way. And you can rest assured that our carefully vetted network of manufacturing partners have POM injection molding experience and the skill to produce the quality parts you need, no matter how complex your design is.
By signing up, you agree to our Terms of Use and Privacy Policy. We may use the info you submit to contact you and use data from third parties to personalize your experience.
To successfully injection mold POM parts, molders need to maintain a medium to high injection speed and an injection pressure between 70 and 120 MPa.
By signing up, you agree to our Terms of Use and Privacy Policy. We may use the info you submit to contact you and use data from third parties to personalize your experience.
Gibson and Fawcett’s discovery marked the first successful synthesis of polyethylene and led to the commercial production of LDPE by ICI starting in 1939. LDPE’s properties, including its flexibility, toughness, and resistance to moisture, have made it a widely used material in packaging, containers, and various consumer goods.
This article examines the material properties of POM plastics, the advantages of POM injection molding, and some design guidelines and processing parameters. And if you’re working on injection-molded POM parts, you’ll find tips, tricks, and best practices in our Injection Molding Design Guide.
If POM is heated past its decomposition temperature, this engineering thermoplastic can break down into corrosive by-products that damage the injection mold. Therefore, it’s important to keep the temperature of molten POM below 210°C. In addition to the proper temperature, molders need to use a short heating cycle. As the temperature increases, the recommended residence time decreases. For best results, maintain mold temperatures between 60 to 100 °C.
POM has excellent lubricity because of its low coefficient of friction, so this engineering thermoplastic is ideal for applications where there’s exposure to sliding friction. Injection molded POM also has good resistance to wear, aka the ability of a material to resist the progressive loss of surface volume due to mechanical actions (such as repeated rubbing).
By signing up, you agree to our Terms of Use and Privacy Policy. We may use the info you submit to contact you and use data from third parties to personalize your experience.
By signing up, you agree to our Terms of Use and Privacy Policy. We may use the info you submit to contact you and use data from third parties to personalize your experience.
Access a wide breadth of capabilities through our highly vetted network.
By signing up, you agree to our Terms of Use and Privacy Policy. We may use the info you submit to contact you and use data from third parties to personalize your experience.
Because POM plastic resists most fuels and solvents, it’s often used to mold fuel tanks and chemical storage tanks. POM can be damaged by phenols, however, and it doesn’t resist strong acids and bases.
POM does not readily absorb moisture and has an absorption rate of only 0.2 to 0.5%. However, it’s often recommended to dry POM resin prior to processing, typically for 3 to 4 hours. The exact drying temperature depends on the POM grade.
We exist to eliminate bottlenecks in new product development by integrating the people, processes, and platform you need to source custom parts.
GETTING A QUOTE WITH LK-MOULD IS FREE AND SIMPLE.
FIND MORE OF OUR SERVICES:
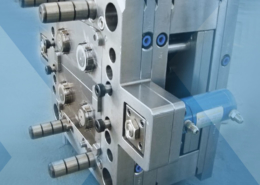
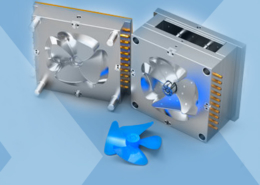
Plastic Molding

Rapid Prototyping
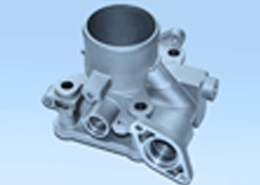
Pressure Die Casting
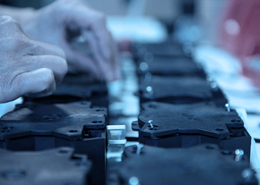
Parts Assembly
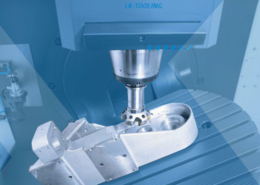