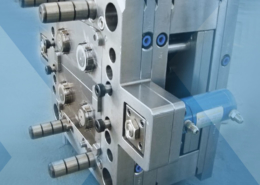
NyproMold: From Art To Part and Everywhere in Between - nypro injection molding
Author:gly Date: 2024-10-15
After the second opening of the mould, the moving mould, which has already been injected twice, will ejected the plastic 2k part.
(1) Insert/over moulding is done using a common injection moulding machine, where the product is taken out from one mould and then put into another mould for a second injection moulding.
2)Application to hand-held products such as walkie-talkie housings, toothbrush handles, power tool handles, spanners and thermoses to improve feel.
The different TPE models from RTP, as pictured, differ considerably in their compatibility with plastics, even though they all belong to the TPE range (X indicates good compatibility).
Now that you know a few of the areas where material selection makes a difference, the following checklist can be a good reference point of factors you should consider:
The simple answer to the question of “why is material selection important for plastic injection molding?” is what we just mentioned — it factors into just about every aspect of the product development process. For instance:
After the 1st injection, if the surface of the part fits directly into another fixed mould, it should be ensured that the plane has a sufficiently large release slope to avoid scratching when the mould is closed.
In the plastics family, only ABS and polysulfone (PSU) surfaces can be plated. If a partial area or a single side of the product requires plating, the plated area should be injected with ABS and the area that does not require plating should be injected with other materials such as PC.
The Draft Angle is important for two-colour injection moulding because it determines which mould the part is attached to during the rotation process.
The material you use plays a role in the end function and performance of your product itself: choose the wrong material, and your product may not work properly. A more flexible resin isn’t suited to a function where rigidity and strength are required. More importantly, non-food grade or medical grade materials can present real health hazards and risks if used in food or medical functions.
Now, let’s take a look at some of the most common resins used in plastic injection molding, as well as some of their qualities and optimal uses.
Acrylic: Frequently used to mimic the appearance of glass, acrylic is used in applications like sunglasses and display cases. Acrylic has a high hardness rating, making it exceptionally scratch resistant, and it is also highly resistant to breakage.
Different resins have different qualities that play a role in the manufacturing process, like melting point, cooling point and viscosity. More complex molds may require a material that’s better able to reach all areas for full coverage, and different melting points and cooling points can help avert problems like sink and cavities in your product.
Polycarbonate (PC): Polycarbonate is a transparent thermoplastic that offers some of the strongest, most shatter-resistant construction available for plastic injection molded products. Polycarbonate is typically transparent in its raw form, and it is highly receptive to sterilization, making it well-suited for medical applications (although it may not be used for medical components intended for placement in the human body). While its strength and break resistance make polycarbonate a common choice in eyeglass lenses and some types of shatterproof or bulletproof glass, it is not very scratch resistant, and so will typically need to be treated or coated with a harder material after the injection molding process. Polycarbonate is also not especially resistant to repeated vibration or stress, as automotive or aerospace components would encounter, and should not be used for these applications.
The chart above can be used as a general selection guide only. It is always best to contact your plastics supplier for a more professional opinion when selecting a specific material type. You can contact us too! info@ptsindu.com
Epoxy: Epoxy is a thermoset resin that as such, offers extremely high strength, as well as resistance to heat and many chemicals after curing. It is important to note that the qualities of epoxy differ based on the curing (or hardening) agent used, so be sure to have a thorough understanding of your product’s end requirements before choosing epoxy as a plastic injection molding resin. Due to its high electrical insulation abilities, epoxy is frequently used in circuits and transistors. Epoxy can also be found in motor and transformer components, as well as in marine applications, such as plugs.
The design of the Cosmetic mating surface at the first and second injection is very challenging and must provide sufficient bonding strength, otherwise flying edges, burrs, rolled edges and flaking can easily occur, especially in 2k injection moulding of hard and soft plastics. Common Cosmetic mating surface designs include stepped and fluted.
Plastics are different, their chemical properties are different, and their compatibility will directly affect the bonding strength and bonding effect of2 K injection moulding/double injection molding.
The two plastics are injected on the same injection moulding machine and moulded twice, but the product only comes out once. Therefore, two-colour injection moulding is usually done by one set of moulds and requires a special two-colour injection moulding machine.
ABS: ABS is a very common thermoplastic that can be used for a wide variety of end products. It is relatively inexpensive and provides strong rigidity and resistance to breaking or shattering, even upon impact. It is also resistant to a number of acids and other corrosives, but not all of them. ABS is not suitable for food use, and it is flammable and shows poor resistance to sunlight. Aesthetically, ABS in its raw form appears white or translucent, although it can be colored using additives. ABS is found in applications like electronic casings, automotive components where shock resistance is important, and toys like Lego.
Polyethylene (PE or PET): Polyethylene is a very strong thermoplastic with an extremely high melting point and a high viscosity. Thin-walled, high-strength applications are the ideal application for polyethylene, and it is also frequently found in disposable plastic water bottles. Polyethylene boasts a high viscosity that makes it well-suited for more complex molds; however, mold setup and cooling times can be longer. For applications where recycling is a concern, polyethylene is one of the best choices you can make.
On the first injection, the part should be attached to the moving mould; on the second injection, the part should be attached to the ejector side of the mould.
Because of the different chemical properties of different plastics, their compatibility will directly affect the bonding strength and bonding effect of the bonding surface, not all plastics have good compatibility with each other.
3)Products that require a multicoloured appearance, such as keyboards, the use of two-colour injection moulding makes them beautiful without the risk of rubbing off during use.
PTS Industrial Ltd is Specializing in precision manufacturing and injection molding parts since 2002. We supply CNC machining (milling&turning) parts and injection molding parts for various industries to customers worldwide.
Knowing the requirements of your particular injection molding process (like mold design and complexity), as well as those of your end product, can help you choose a material with the qualities you need, at the lowest cost possible. Don’t end up paying a premium for material aspects and features that you don’t need.
2k injection molding(2shot injection molding or double shot injection molding)is a manufacturing process used when referring to molding two materials/colors into one plastic part. This plastic molding technology blends two materials or two different colours materials into one ending plastic part by using 2k injection molding machine.
2k injection moulding is a type of injection moulding, so DFM design guidelines for injection moulding, such as uniform wall thickness, avoidance of sharp corners and even transitions, must also be observed for 2k injection moulding.
The strength of the bond between the base material and the cover material depends on the compatibility between the materials, the process temperature, the bonding surface, the moulding sequence and the design of the internal bonding surface mechanical interlocking structure.
Today I’m going to show you an article to let you understand 2k injection molding in 2022!(2k Injection Molding Factory/Expert/Supplier based on China.)
The first injection of the base material and the second injection of the cover material are injected out simultaneously, requiring two injection nozzles on the injection machine, each injecting a different colour or a different base material and cover material.
Polypropylene (PP): Polypropylene is commonly used in consumer-packaged goods like water bottles, as well as household items like garbage cans, pails and flatware. It is also frequently used in living hinges and scientific lab supplies due to its shatter-resistant properties. With its low cost, high strength and flexibility, polypropylene is ideally suited to high-volume production runs, and works well even in complex molds due to its very high viscosity. Polypropylene is readily available in a clear raw form, although it is naturally opaque.
Material selection plays an important part in just about every facet of the plastic injection molding process, so it’s critical not to overlook this step. Here, we’ll take a look at the “why” of material selection — how it affects your product and the manufacturing process — as well as the “what” — meaning, you’ll learn a bit about some of the most commonly used plastic injection molding materials, what their qualities are, and their functions.
3) Compared to insert/overmold injection moulding, 2k injection moulding does not require the insertion of inserts, resulting in shorter and more efficient moulding cycles, as well as higher quality.
1) Used in power switches, mobile phone keys, car switches, etc. to meet the requirements of partial light guidance or light transmission.
Therefore, when designing products for two-colour injection moulding,The first and most important thing is to choose the most suitable substrate material and covering material。
2k injection moulding is the simultaneous injection of two plastics at once in a dedicated two-colour injection moulding machine.
2)The difference between the melting temperature of the base material and the covering material does not exceed 30-60°. The melting temperatures of common plastics are shown in the following chart.
After the first injection of the base material, the mould is opened and then rotated by 180° using the rotatable structure of the injection machine, then closed the mold and start second shot inejction by using a different colour of material or a different material (covering material) than the first injection.
When the internal bonding surface is too small, the roughness can be increased by nibbling on the bonding surface on the one hand, and mechanical interlocking structures can be designed on the other.
2 shot injection moulding can integrate multiple functions into one plastic part, such as soft-sensitive surfaces, ergonomic design, two-colour appearance, brand identity, feature improvement, noise reduction, shock absorption, water resistance and impact protection, saving design space and reducing the number of components, etc.
The weight difference between the base material and the cover material should not be too big different, otherwise it will affect the moulding cycle and injection pressure etc.
In this article, the first injected material is referred to as the base material and the second injected material is referred to as the overlay material.
A toothbrush is a product that combines hard and soft plastics. A hard plastic is used for the main part of the toothbrush to provide sufficient strength; a soft plastic is used for the part that comes into contact with the hand to ensure a tactile feel; at the same time two-colour injection moulding provides the toothbrush with a colourful appearance.
2) The plastic is in a molten state throughout the entire process of two-colour injection moulding, with no cooling shrinkage, which means that there is the opportunity to form a strong chemical link between the base material and the overlay material, with high strength and reduced risk of burrs occurring.
Polystyrene (PS): Polystyrene is best for plastic injection molding where budget is a concern; however, there are tradeoffs in strength and other qualities. If a break-resistant product is required, it’s best to look elsewhere. Polystyrene is ideal, however, for disposable products, and is frequently used in food packaging as well as single-use lab applications like petri dishes. Note that polystyrene does not offer high resistance to heat (only up to about 212 degrees Fahrenheit/100 degrees Celsius).
GETTING A QUOTE WITH LK-MOULD IS FREE AND SIMPLE.
FIND MORE OF OUR SERVICES:
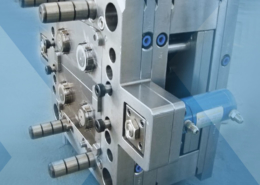
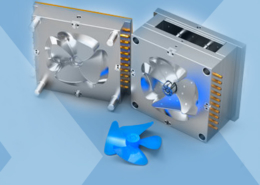
Plastic Molding

Rapid Prototyping
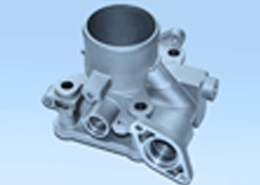
Pressure Die Casting
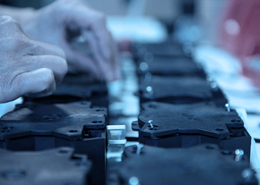
Parts Assembly
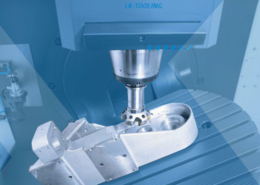