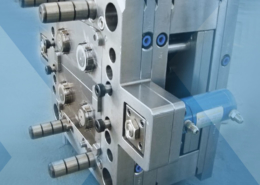
NYLON 66 INJECTION MOULDING - injection molding nylon 66
Author:gly Date: 2024-10-15
Plastic – whether one hates it or likes it; there is no denying that every single day or lives are guided by quite a few things which are made out of plastic. But did you know that most plastic objects are manufactured through a process called injection molding? Do you want a few examples? Well, washers, pulleys, valves, bottle caps, gears, keyboards, computer monitors are all made by this process. So are knobs, power tools, furniture and car panels. While these things are so varied – both in shape and in use, they are all made by the same process. Fascinating, isn’t it? This process of plastic mold fabrication is so popular because it is cost effective, especially when plastic products are being manufactured at a mass scale.
As far as plastic mold fabrication goes, the injection process has almost revolutionized the way in which things are produced in modern times. This process has made fabrication of plastic simpler and a lot faster. It will hardly be an exaggeration to state that the possibility of the use of this process is practically limitless. You might be wondering how this plastic injection molding machine actually works. To start the process, a design of the product is first developed. Then a metal mold is made and that mold is secured to the machine firmly.
Plastic manufacturing and the evolution of thermoplastic injection molding technology has continued to develop with a range of innovative options that add potential savings and performance. Aline Components is a leading plastic injection molding company serving the Tri-State area with the finest plastic parts and employing the most advanced custom plastic injection molding equipment and expertise. Composite molding, also known as core-back molding, is a relatively recent thermoplastic injection molding technique that makes use of innovations in material science to enhance new products and components.
What is even more interesting is that the plastic mold fabrication process was invented more than a century ago. It was invented in the year of 1868 by John Wesley Hyatt. He had injected celluloid into a mold to create billiard balls then. Later on, he created an injecting molding machine by adding a plunger to the design. However, it was in 1946, that James Hendry took the initiative to modify Hyatt’s design of the machine by attaching a screw.
The second part of this process requires that the granules or pallets of plastic material are poured into the heated barrel of the machine and it is forced into the cavity of the mold. In the third and final stage, after the cooling of the mold, the product is popped out. It sounds simple because it really is. This plastic mold fabrication process is efficient and enables the manufacturer to handle mass production of plastic products without spending a fortune on worker handlings. It saves effort, time and money and thus is enjoys uncompromised love from all manufacturers around the globe.
Composite molding uses a two-shot molding technology to add a layer of high performance composite material onto another molded element made from a more rigid plastic. The rigid component acts as a substrate for the composite material. The composite has expansion properties during the curing process, and, after cooling, the final component now has a thick layer of composite firmly affixed to the rigid substrate. Core-back molding has the capability to add more structural strength to components with little added weight, making it an ideal choice for many types of applications where this structural efficiency is desired. New products using core-back molding can also provide this greater strength at a reduced cost to the consumer.
At Aline Components, we work with you to determine if insert molding is right for your plastic part or component, and if so, what material is best suited for the application. We take pride in helping our customers obtain the solutions they need for their product or system to perform to the highest level.
Aline Components serves customers in Pennsylvania, New Jersey, Delaware, New York, and beyond. Conveniently located just outside Philadelphia, its state-of-the-art facility employs the latest injection molding equipment and offers plastic parts with all of the most advanced features, such as insert molding, sandwich molding, stack molding for large production runs, and more. Alineâs services range from CAD/CAM documentation support, rapid prototyping, and short-run processes for rush delivery. If you are looking for experienced plastic injection molding company with a detailed knowledge of the most current plastic manufacturing techniques, including composite/core-back molding, contact Aline Components today.
GETTING A QUOTE WITH LK-MOULD IS FREE AND SIMPLE.
FIND MORE OF OUR SERVICES:
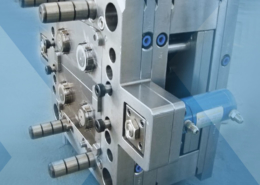
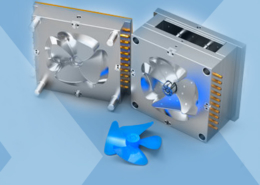
Plastic Molding

Rapid Prototyping
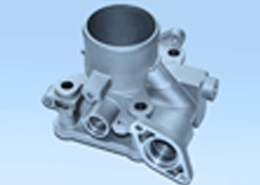
Pressure Die Casting
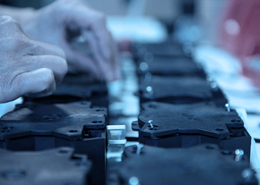
Parts Assembly
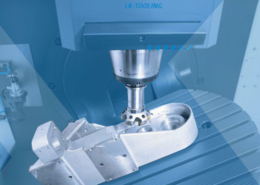