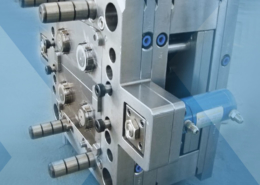
Nissei Injection Molding Machines - Hunter Plastics - nissei injection
Author:gly Date: 2024-10-15
Ultrasonic polishing is a method that uses a tool section for ultrasonic vibration to polish a brittle hard material by using an abrasive suspension. A workpiece is soaked in an abrasive suspension, and then placed in an ultrasonic field together with the suspension that grinds and polishes the surface of the workpiece by the action of ultrasonic waves. Ultrasonic machining has a small macroscopic force, so it does not cause workpiece deformation, but it is difficult to manufacture and install the tooling.
Magnetic grinding & polishing is the use of magnetic abrasives to form an abrasive brush under the action of a magnetic field to grind a workpiece. This method features a high processing efficiency, great quality and easy-to-control processing conditions. With suitable abrasives, the surface roughness able to be obtained through this method reaches up to Ra0.1 μm.
We consistently achieve exceptional customer satisfaction through our seamless service and innovative ways to manage processes, products, and requirements. In addition, our business insight and keen eyes for detail allow us to understand market dynamics and customers’ expectations.
It has been a long year now; we have been helping our clients turn their design ideas into finished products. Hence, you can contact us to discuss.
Mechanical polishing is a method that removes the protruding parts on the surface of a workpiece by cutting or plastically deforming the surface of a material to obtain a smooth surface, during which oilstones, wool wheels and sandpaper, etc. are usually used by performing manual operations, and if the surface quality requirements are high, ultra-precision lapping and polishing will be adopted. Ultra-precision lapping and polishing employs a special-purpose grinding tool, which, soaked in a polishing liquid containing abrasives, is pressed against the machined surface of a workpiece to perform high-speed rotation. With this technology, the surface roughness of Ra0.008 μm is able to be achieved, which represents the best surface roughness among various polishing methods, and is usually applied to the polishing of optical lens molds. Mechanical polishing is the main method of mold polishing.
As a leading plastic injection moulding in Australia, we have expertise in all aspects of the processes involved in plastic product manufacturing. We are known for producing superior quality tooling designs and products. In addition, we adhere to strict process and quality control systems to ensure quality service and products. Therefore, you can rely on us for design consultation, production, and distribution.
Moreover, customised plastic components provide an ideal alternative for industries seeking to mass-produce high-quality, cost-effective parts. It is because they employ the moulds to replicate an item thousands of times.
(7) When the surface of a workpiece is polished with copper- or bamboo-pressed sandpaper, the sandpaper should not be larger than the tool area, otherwise the parts that are not supposed to be ground will be ground.
Sneddon & Kingston are industry professionals when it comes to plastic injection moulding in Melbourne, Sydney and all of Australia. We have the technical proficiency, the industry experience as well as access to modern facilities with automated processes to mass produce quality plastic products for various industrial needs.
The mold polishing differs a lot from the surface polishing required by other industries. Technically, the polishing of a plastic mold should be referred to as mirror finishing. Not only does it impose high requirements for polishing itself, but it also has a high standard for surface flatness, smoothness and geometric precision. The standard for mirror polishing is divided into 4 levels: A0 = Ra0.008 μm, A1 = Ra0.016 μm, A3 = Ra0.032 μm, and A4 = Ra0.063 μm. Since it is difficult to accurately control the geometric precision of a part with electropolishing and fluid polishing, while the surface quality obtained through chemical polishing, ultrasonic polishing, and magnetic grinding & polishing does not meet the requirements, the mirror polishing of precision molds is dominated by mechanical polishing.
Moreover, we rely on various scientific methods, moulding process technologies, and analytical tools to provide custom plastic injection moulding. It allows us to meet the performance and precision needs for complex plastic components and applications. We have experience in specialised, complex design, engineering and support and can perfectly align with your specific project needs.
To improve the polishing speed of a workpiece with a surface roughness of Ra1.6 μm or more, the ultrasonic wave is combined with a dedicated high-frequency, narrow-pulse and high-peak value power source for compound polishing, with ultrasonic vibration and electric pulse corrosion simultaneously acting on the surface of a workpiece to rapidly reduce surface roughness, which is effective for polishing the rough surface of a mold after machining by cutting, milling, EDM and wire cutting.
Sneddon & Kingston Plastics is a Melbourne based company specialising in custom injection moulding. For over 60 years we have been a highly regarded and steadfast company supplying to many industries around the world.
Cavity polishing during mold manufacturing is a very important process step that is closely related to the quality and service life of a mold, while also determining the quality of the product. Understanding how polishing works, mastering the technological process and selecting an appropriate polishing method can improve the quality, as well as the service life of a mold, thus improving the quality of the final product.
As specialist plastic injection moulders, we design, optimise, manufacture and supply plastic injection moulded products. We meet the injection moulding requirements of high-quality engineered plastics. Our plastic injected moulded products provide an ideal replacement for heavier metal items.
Our primary services include plastic product design, prototyping for industrial interests, tooling manufacture and plastic injection moulding in Melbourne. If you would like to discuss your next project with our team, give us a call.
When industrial products are developing towards diversification and high quality, it is an important task to improve the quality of the molds that directly affect product quality. During mold manufacturing, smooth mirror finishing after shaping, referred to as surface grinding and polishing of a part, is an important process step to improve the quality of the mold. Understanding a proper polishing method is able to improve mold quality, as well as service life, thereby enhancing product quality.
Fluid polishing relies on a flowing liquid and the abrasive particles it carries to erode the surface of a workpiece for polishing purposes. Hydrodynamic grinding is driven by hydraulics, of which, the medium is mainly made of a special compound (polymeric substance) that flows at a lower pressure and is incorporated into an abrasive that may be made of silicon carbide powder.
With us, you rest assured that we will never pursue your custom injection moulding projects at the cost of material selection, part design, mould design and process control. On the contrary, we take utmost care of these key stages of the product development process to accurately achieve the type of product design you want from us. It also allows us to make you achieve your business goals.
Generally, making an injection mould can cost between $10,000 to $100,000. But the cost varies depending on several factors. As plastic injection moulders, we consider many things before estimating the final price, including your order size, part complexity, labour cost, and specifications.
It appears we’re not the only ones excited about securing our latest contract for Australia Post’s new letter trays, with the Herald Sun publishing the…
Learn more about our plastic injection moulding capabilities in Preston, Melbourne. We continuously invest in the most advanced processing technologies and optimise our techniques in manufacturing to ensure that we remain agile and competitive in the marketplace.
Raw plastic material melting. Injection of the molten material into a mould. Cooling of the molten material into a solid state. Removal of the hardened material from the mould.
(5) To eliminate undercuts caused by mold part grinding, or respond to the situation where some contacting surfaces need to be protected, a saw blade or sandpaper can be attached to the edge to obtain an ideal protective effect.
Chemical polishing refers to the process in which a material is soaked in a chemical medium that allows the micro projections on the material surface to firstly dissolve before the dents, thus obtaining a smooth surface. The method can be applied to polish a workpiece with a complicated shape, and is able to concurrently work on many workpieces to achieve a high efficiency. The surface roughness able to be obtained by chemical polishing is usually Ra10 μm.
Our team specialise in all aspects of product manufacturing. As a family owned business, we are focused on manufacturing and supplying high quality plastic injection moulded products for local Australian markets, and have been doing so for over six decades.
Custom plastic injection moulding is the process that helps create a unique mould. It involves listening to your particular requirements and selecting material based on your specification, and production of plastic parts or products to meet your specific needs.
(4) For workpieces with a large flat surface or a side surface, use oilstone to grind the rough lines and then use straight steel sheets for light transmission inspection, to check whether there are any unevenness or undercuts. If so, it will be difficult to release the part or the part may be damaged.
For more information about our manufacturing capabilities and services, get in touch with our team today. Fulfil your need for specialised moulding and product design with Sneddon & Kingston.
(8) Try not to use a sander to repair the parting surface, because the parting surface polished by the wheel head is rough with uneven waves. When necessary, the wheel head must be fixed with concentric balance.
Today, plastic injection moulding has become one of the most widely used plastic forming processes. It is known for having a wide range of manufacturing applications. In addition, the injection moulding process has many advantages, like customisability, high efficiency, speed, and affordability, which makes it different from other moulding and casting methods.
Injection moulding can be an expensive affair to set up, but it will prove to be a cheaper deal over the long run. In addition, it works best for large production volumes. You can speak to our consultant to discuss your requirements and the cost of injection moulding.
As one of the leading plastic injection moulding manufacturers, we can help you with a quality injection moulding process.
Moreover, as one of the leading plastic injection moulding manufacturers, we can develop game-changing prepositions for your business to support you throughout your journey. So, whether you want plastic product design, prototyping samples, injection moulding, mould design, mould manufacture, or plastic optimisation, we are your one-stop destination.
Choosing an appropriate manufacturing process – There are three main ways to manufacture a plastic part: injection moulding, CNC machining and additive processing. You will have to choose the most appropriate process depending on your requirement and budget.
(9) The shape of the grinding tool should be close to the surface shape of the mold, so as to guarantee that the workpiece is not deformed by grinding.
(3) Some workpieces may have multiple components assembled together for grinding. It is necessary to separately grind the rough texture or EDM pattern of a single workpiece before grinding and smoothening the assembled workpiece.
Prototype Building – Building a prototype is the final step before the production procedure. It reveals possible problems in real-world applications. Thus, it allows you to hone your designs and determine the functionality and efficiency of the plastic part.
The team at Sneddon & Kingston provide plastic injection moulding in Melbourne for various industrial sectors throughout Australia. We provide manufacturing solutions for; water filtration, food packaging, industrial packaging, automotive, construction, medical and pharmaceutical niches and so much more.
The basic principle of electropolishing is the same as chemical polishing, which is to selectively dissolve the surface of a material to create a smooth surface. Compared with chemical polishing, it can eliminate the influence of the cathode reaction, thus producing a great effect.
Coming up with a design idea – A design idea doesn’t involve sketching up your vision but also other factors like your material preference, the environment in which you will use the product and the factors that can affect its performance, tolerance requirements etc. You can get a consultation regarding all these factors.
(6) Pull back and forth to grind the flat surface of a mold, and try to keep the handle of the oilstone as horizontal as possible. Do not exceed 25°, because when the slope is too large, the force is pressed top-down, which may lead to the creation of many rough lines on the workpiece.
(1) Before you begin to machine a new cavity, first inspect the surface of the workpiece and then clean it with kerosene, so that the cutting feature of the oilstone does not malfunction due to attraction of dirt.
It offers more advantages than metallic products because of its lighter, stronger, superior, and long-lasting characteristics.
Therefore, you can rely on us for mass-producing plastic components. We use a reliable and economical process to produce high-quality components with great dimensional consistency.
The plastic injection moulding technique necessitates incredible accuracy with maximum flexibility. This method has benefited many industries as the technology is used to produce products of different types and sizes for various purposes. Its application can be found in multiple industries like automotive, infrastructure, medical, food packaging, aerospace, household appliances, building and construction, etc.
Injection Moulding Breathes Life into Australia’s Specialist Food Market! Since the turn of the century, food packaging has undergone a quiet transformation. Partly driven by…
(2) When grinding a rough surface, the job should be carried out from the difficult part to the easy part. Especially for some dead corners that are difficult to grind, the deep bottom must be ground first, and finally the sides and the large flat surface.
The injection moulding process involves using an injection moulding machine, raw plastic material, and a mould. First, the raw plastic material is melted in the injection moulding machine. It is then injected into the mould. Here it is allowed to cool down and get solidified into the final part.
GETTING A QUOTE WITH LK-MOULD IS FREE AND SIMPLE.
FIND MORE OF OUR SERVICES:
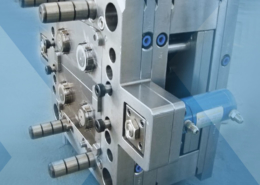
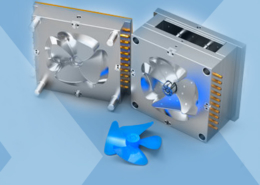
Plastic Molding

Rapid Prototyping
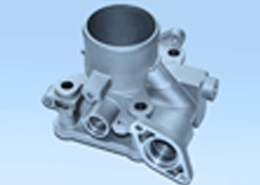
Pressure Die Casting
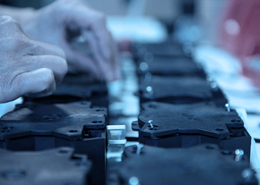
Parts Assembly
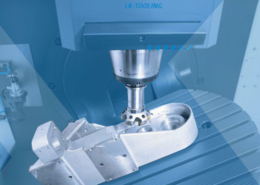