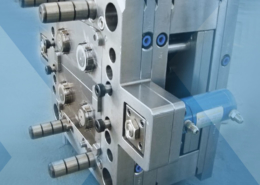
Nissei Injection Molding Machinery - nissei injection
Author:gly Date: 2024-10-15
*(Note flexibility can be achieved through additive techniques but tear strength, chemical resistance and elongation to break will be significantly reduced.)
However neither of these options will truly emulate a production TPE or rubber, especially in areas such as elongation, temperature resistance or stiction. Thus if the goal is to create anything more than a visual prototype there is little option but to manufacture a bridge tool and prototype in the production intent material.
Thermoplastic elastomers (TPE’s) are copolymers that are a blend of rubber and plastic, processed by injection moulding or extrusion. Within TPE’s there are six sub sets, which is where names like TPU and TPV come from.
We are here to help, whether you have 30 years of experience and know exactly what you need or are just starting out on your 3d printing experience and need some advice. Either way we have capability to deliver what you need, when you need it.
Medical and pharmaceutical products play a vital role in the health and safety of patients. As such, ensuring the quality of each product and its individual components throughout the manufacturing process—from design to final inspection—is essential. For this reason, it is vital to partner with an experienced medical/pharmaceutical component manufacturer that emphasizes quality and offers complete part traceability from start to finish.
Thus for a low call off of say 100 parts per year, the lower tool cost and greater cycle time of compression moulding is unlikely to be an issue. As the quantities rise, the number of cavities in a tool can be increased, so a ten, twenty or more cavity tool is possible (geometry permitting).
Materials that can flex are frequently referred to generically as rubbers. However, there are two basic categories simply differentiated by their processing technique, thermoplastic and thermoset.
At The Sterling Healthcare Manufacturing, we understand the importance of quality in component manufacturing. By leveraging our extensive knowledge of the medical and pharmaceutical industries, we provide full-service, turnkey plastic injection molding solutions that fully comply with industry specifications and standards. For additional information about our plastic injection molding capabilities and how we serve the medical and pharmaceutical industries, contact us today.
However, ultimately the additional expense of injection mould tooling and faster cycle time will pay off, and needs to be considered. (material properties being equal)
In contrast TPE’s are processed on conventional injection moulding machines with cycle times similar to moulding conventional thermoplastics.
Prototyping flexible parts can be a challenge. Whilst it is possible to 3D print materials that demonstrate a level of elongation in a variety of harnesses’, their properties fall well short of production intent materials.* Vacuum Casting can offer a better solution, although more costly, again in a range of harnesses’.
Plunkett Associates can support both your prototyping requirements and production requirements, in either class of materials. Drawing on strengths in both tooling and moulding, we will ensure you get to market on time.
We are here to help, whether you have 30 years of experience and know exactly what you need or are just starting out on your 3d printing experience and need some advice. Either way we have capability to deliver what you need, when you need it.
In contrast TPE’s require tooling designed and manufactured to injection moulding standards. Material is processed and injected in the same way as ABS or PC would be for rigid parts. It is more sophisticated than compression mould tooling and as a result more expensive.
As indicated above, injection molding is one of the most efficient and cost-effective ways of manufacturing parts that meet the strict specifications and standards of the medical and pharmaceutical industries. For example, the process is often used to manufacture the small, high-precision components found in diagnostic testing kits, such as the lateral flow in-vitro diagnostic test cartridge produced in large quantities by our team.
At Sterling Healthcare Manufacturing, we specialize in full-service, turnkey plastic component injection molding solutions. Our comprehensive part manufacturing capabilities allow customers to maintain oversight over the production of their parts, resulting in greater transparency and accountability. Additionally, we maintain ISO 9001:2015, our new ISO 13485 cleanroom certification and employ the use of FDA/medical-grade materials to ensure our injection molded components fully meet the strict specifications and standards of the medical and pharmaceutical industries.
The injection molding process accommodates a wide range of plastic materials, making it well-suited to produce medical and pharmaceutical parts from whatever medical-grade plastic is required for the project. There are numerous plastics suitable for medical injection molding operations, each of which offers unique properties and performance characteristics. Common plastic material options for medical injection molding include:
Compared to other plastic manufacturing processes, plastic injection molding offers a number of clear advantages, especially when working with a knowledgeable and skilled injection molding partner. These benefits encompass the following:
If you need your component to be recyclable, then thermoplastics are your only option. Rubbers being a thermoset means components are destined for landfill at the end of their life.
Quantity is important as the cycle times of the two processes are wildly different. Rubber (whether synthetic or natural) is a thermoset and as such must cross link during processing – which is referred to as vulcanisation. Depending on a variety of parameters, vulcanisation can take from minutes to hours.
To see an example of our work in the medical industry, check out this case study documenting how we optimized the mold design for a polystyrene diagnostic kit. You’ll also learn about how our custom capabilities — such as machine vision inspection — guarantee quality, cost efficiency, and 100% reliability for every order we complete.
Service environment is also important and both maximum and minimum operating temperatures as well as exposure to solvents need to be taken into consideration. Some rubbers can be better at retaining there elastomeric properties, particularly in high temperature environments and silicones excel in situations where the material must be highly inert.
Plastic injection molding is an efficient and cost-effective method of producing medical and pharmaceutical parts to high levels of precision, accuracy, and quality. It is used to create components from medical devices and equipment to laboratory tools and testing instruments. The following page provides an overview of the plastic injection molding process and its essential role in the medical and pharmaceutical industries.
Given the broad selection of suitable material options available, the first step in choosing a material for a project is narrowing down the list to the material family that fulfills the most part requirements (e.g., tensile strength, temperature load rate, etc.). From there, it is much easier to select the grade that best suits the project. Online databases—such as UL Prospector, MAT Web, and The British Plastics Federation—can provide information about materials that can further facilitate the selection process.
As mentioned above, there are many types of plastics available for medical injection molding operations. Each plastic possesses distinct qualities that influence how it performs in specific applications. Some of the key factors to consider when choosing between the material options include:
Flexible components are present in most assemblies. Whether you want a simple gasket, a seal, a more intricate connector, or a bellows, the common denominator is that the part is required to flex in its operation or assembly.
The decision on whether to injection mould using TPE or to compression mould using rubber is usually a function of quantity and service environment.
Tooling is a requirement to process either option. A large range of rubbers including silicone, nitrile, neoprene, EPDM and Viton can be moulded in compression tooling. This is relatively simple compared to injection mould tooling and multiple cavities can be used to offset longer cycle times.
Advancements in material manufacturing techniques and technologies have led to the widespread use of plastics in modern manufacturing operations. In the medical and pharmaceutical industries, plastics are often used alongside the injection molding process to produce prototypes and full-production units of medical device and equipment components. As newer plastic materials and component designs are developed, injection molded plastics have increasingly contributed to lower infectious disease rates, better pain management, and lower medical costs.
We are product developers. We use our passion and experience to build manufacturing partnerships that our customers can trust. With UK onsite toolmaking and injection moulding we are always here to support your requirements, be they low volume fast turnaround development parts or ‘make to stock’ with a scheduled call off.
GETTING A QUOTE WITH LK-MOULD IS FREE AND SIMPLE.
FIND MORE OF OUR SERVICES:
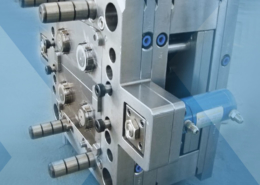
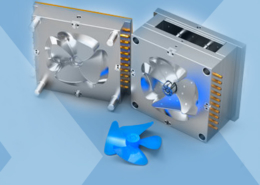
Plastic Molding

Rapid Prototyping
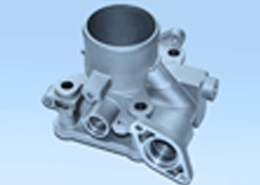
Pressure Die Casting
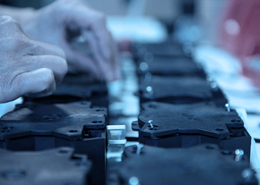
Parts Assembly
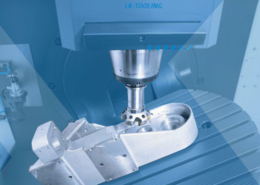