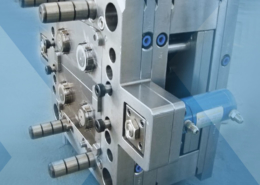
New or Used Injection Molders for sale - Australia - injection mold press
Author:gly Date: 2024-10-15
More than four years on, there are aspects of the COVID-19 pandemic that linger in their impacts to the plastics market and are made visible in our annual survey.
Despite price increase nominations going into second quarter, it appeared there was potential for generally flat pricing with the exception of a major downward correction for PP.
There are a few variations of two-shot molding, including rotary platen, movable core, and overmold. The first two require a second injection unit, two runner systems, and two processes. The latter, in most cases, involves two separate molds—one for each material—but can also be run with one mold, two runner systems, and pick-and-place part transfer, either manually or with a robot.
Thousands of people visit our Supplier Guide every day to source equipment and materials. Get in front of them with a free company profile.
The rotary platen option itself may have two very different meanings to some molders. The simpler one—which I am addressing here—is a vertical platen on one face of the clamp that rotates on a horizontal axis. The other—far more complex—is often referred to as a “cube mold” or “spin stack.” It is a center stack with two or four faces that rotates on a vertical axis. This creates a multi-daylight stack-mold configuration, which is the most complex and costly version of a rotary two-shot mold.
In many cases, decreasing the discharge temperature will improve product quality and perhaps even boost rate. Here are ways to do it.
Second quarter started with price hikes in PE and the four volume engineering resins, but relatively stable pricing was largely expected by the quarter’s end.
The Plastics Industry Association (PLASTICS) has released final figures for NPE2024: The Plastics Show (May 6-10; Orlando) that officially make it the largest ever NPE in several key metrics.
Exhibitors and presenters at the plastics show emphasized 3D printing as a complement and aid to more traditional production processes.
Sustainability continues to dominate new additives technology, but upping performance is also evident. Most of the new additives have been targeted to commodity resins and particularly polyolefins.
Required Documents – There are some necessary documents are needed such as a Drug license and GST number and sometimes even the registration document of your firm or company is also required. DL is issued by your local Food and Drug authorities and GST by the Government.
Finalizing Order Quantity And Composition – The first step is to make a deal with the partner about the quantity and compositions they want. As when they will us a final answer about the quality of injections they want with the formulizations they like to have, we move to another step.
Packing Material – We provide our partners with the customized packaging material option so that they can have their products look the way they like in terms of color, name, and material. Will packaging we provide every detail of the medicine on them so it easy for the doctor and consumer to understand the requirement of the medicines.
Ultradent's entry of its Umbrella cheek retractor took home the awards for Technical Sophistication and Achievement in Economics and Efficiency at PTXPO.
Those not familiar with two-shot injection molding may assume that it’s complex. Yes, it adds another element to part production by involving a second material and process, but it’s not really all that complicated.
With the simpler rotary platen, as defined above, the tooling itself is not that complex; you just have a second runner system and two sets of ejector plates. The movable half is the half that rotates. If you are producing one part per cycle, there will be two ejector cavities (movable half) and two cover cavities (stationary half). The two ejector cavities will be identical, and the cover cavities will have one for the first shot and one for the second shot. So the pattern continues with multiple parts: Two parts in each cycle would have four ejector cavities and four cover cavities. Again, the four ejector cavities would be identical and the cover cavies would have two cavities for the first shot and two cavities for the second shot.
Today, more than ever, granulation is an important step in the total production process. Our expert explains a few of the many common traps to avoid when thinking about granulators
Formnext Chicago is an industrial additive manufacturing expo taking place April 8-10, 2025 at McCormick Place in Chicago, Illinois. Formnext Chicago is the second in a series of Formnext events in the U.S. being produced by Mesago Messe Frankfurt, AMT – The Association For Manufacturing Technology, and Gardner Business Media (our publisher).
Biobrick Pharma has been appreciated and trusted for its quality and packaging of the products. we being one of the key players and top Injection Manufacturer and Suppliers in India understand the importance of life thus we manufacture only quality approved thus range in our certified units.
Raising Quotation – The next step is to state our price which we put after calculation our all requirements such as raw material cost, production chargers, packaging material, etc. when we are ready with the final quotation we put it in front of our partners to discuss it further.
Plastics Technology Top Shops Benchmarking Survey provided both unanimous responses and divided results, but pervasive throughout is the sense of an industry still grappling with the aftermath of 2020’s global pandemic.
Rotary two-shot molding, from my perspective, is the simplest version of the options, But there are still critical things to consider, such as tooling, crush, support and the processes for both shots. In this article, I will focus on the version of the process that uses a rotary platen. The tool itself can have a rotary plate built in, actuated by hydraulics or a rack system. This makes the tooling a little more complex and typically is used when the molder does not do a lot of two-shot molding.
When, how, what and why to automate — leading robotics suppliers and forward-thinking moldmakers will share their insights on automating manufacturing at collocated event.
Learn about sustainable scrap reprocessing—this resource offers a deep dive into everything from granulator types and options, to service tips, videos and technical articles.
Now the pharmaceutical industry is expanding very rapidly because of the increasing demands of pharma products and injection, as per the report the market of injectable products has reached the worth of USD 483.45 billion in the year 2019, and it is rising at a Compound Annual Growth Rate (CAGR) of 12.9%, and many experts are expecting it to reach USD 1,251.28 billion by the end of 2027. Looking at these facts it becomes obvious that the demand for injectable products is going to be at a peak in the coming time as well, which is the reason that many injection manufacturing companies are investing more in injectables.
Today we have more than 250 products in Biobrick Pharma with DCGI Approval.We have always focused on improving the health of community by offering safe efficacious and quality Products to cure Peoples on india.
While the major correction in PP prices was finally underway, generally stable pricing was anticipated for the other four commodity resins.
August 29-30 in Minneapolis all things injection molding and moldmaking will be happening at the Hyatt Regency — check out who’s speaking on what topics today.
Product Delivery – The final step of our procedure includes packing our whole product by using quality-approved material which is done in a temperature-controlled and germ-free warehouse. After the whole order is packaged it is delivered to our partner’s sites.
With a rotary-platen mold, it is critical to have locators on the mold and the machine platens to ensure that it is exactly on center of the rotary platen. If the mold is not exactly on center, you will have alignment issues; when the mold rotates 180° it can damage the leader pins, bushings, and shutoffs. It is also important to consider tonnage with part surface area. In most cases your cavities will be off-center—first shot on one half and second shot on the other half—so you will not have full advantage of the machine tonnage to compensate for the cavity plastic pressure.
In a time where sustainability is no longer just a buzzword, the food and beverage packaging industry is required to be at the forefront of this innovation. By adopting circular packaging processes and solutions, producers can meet regulatory requirements while also satisfying consumer demand and enhancing brand reputation. Join Husky to learn more about the broader implications of the circular economy — as well as how leading brands are leveraging this opportunity to reduce costs, increase design flexibility and boost product differentiation. Agenda: The cost and operational benefits of embracing circularity Key materials in circular packaging — including rPET and emerging bioplastics How to design a circular food and beverage package Strategies for selecting sustainable closures to future-proof packaging solutions Optimization and streamlining of production processes for enhanced efficiency How Husky Technologies can enable your sustainable success
Take a deep dive into all of the various aspects of part quoting to ensure you’ve got all the bases—as in costs—covered before preparing your customer’s quote for services.
This 1-day technical conference and exhibition showcases innovative developments in materials, processing and equipment for the additive manufacturing industry. This conference is specifically designed to inform, update and educate plastic processors about implementing new additive manufacturing technologies. Hear technical presentations on the newest advances in additive manufacturing related to: design, materials development, processing equipment and enabling technologies, new applications and more. See exhibits from engineering plastic suppliers, compounders, molders, design and engineering firms and machinery suppliers. Experts will show you how to apply the latest technologies to your next project or program. The conference includes a full day of technical presentations, plenary and keynote presentations on business trends; breakfast, lunch and breaks; exhibits of advanced technologies and an evening networking reception. Note: Additive Manufacturing Media executive editor Stephanie Hendrixson will moderate the Supporting AM Adoption in Northeast Ohio panel at 11:20 a.m.
Across all process types, sustainability was a big theme at NPE2024. But there was plenty to see in automation and artificial intelligence as well.
This CW Tech Days virtual event will explore the technologies, materials and strategies used by composites manufacturers working in the evolving space market. Presentations from industry experts will emphasize the use of composite materials in applications requiring the weight savings, structural benefits and ability to withstand extreme temperatures that only composites can provide.
Mold maintenance is critical, and with this collection of content we’ve bundled some of the very best advice we’ve published on repairing, maintaining, evaluating and even hanging molds on injection molding machines.
In this collection of articles, two of the industry’s foremost authorities on screw design — Jim Frankand and Mark Spalding — offer their sage advice on screw design...what works, what doesn’t, and what to look for when things start going wrong.
It’s important to understand what materials are being used and their ability to bond to each other. A mechanical bond is necessary—with details and holes in the part design—but some materials do not like to adhere to each other. Most of my experience is with using TPE or TPU as the second shot and PP, PC/ABS, or ABS as the first shot (substrate). There are also cases were the same material with different colors or additives is used for two-shot molding.
In this collection of content, we provide expert advice on welding from some of the leading authorities in the field, with tips on such matters as controls, as well as insights on how to solve common problems in welding.
technotrans says climate protection, energy efficiency and customization will be key discussion topics at PTXPO as it displays its protemp flow 6 ultrasonic eco and the teco cs 90t 9.1 TCUs.
Your problem may be related to tooling, material, processing, or combinations thereof. Here’s how to find the root cause.
In this collection, which is part one of a series representing some of John’s finest work, we present you with five articles that we think you will refer to time and again as you look to solve problems, cut cycle times and improve the quality of the parts you mold.
Resin drying is a crucial, but often-misunderstood area. This collection includes details on why and what you need to dry, how to specify a dryer, and best practices.
This Knowledge Center provides an overview of the considerations needed to understand the purchase, operation, and maintenance of a process cooling system.
For the last 5 years, we have been offering reliable injection manufacturing services in India and bring new and innovative injection formulations to bring in the market for curing many other health diseases. Some experts of the industry are working with us who dedicate their best efforts to formulating and manufacturing the best quality products for our partners to distribute all over the nation at affordable prices. We have a wide product portfolio of 400+ products that we manufacture with many different and well-known brands. We have established ourselves in the field of Injection Manufacturer and Suppliers in India and with the help of our franchise partners, we became about to cure many diseases and make living healthy.
The other version of two-shot molding is the movable core, which does not require a rotary platen. The cavitation will be like a normal mold: one part, one cavity. The movable cores move internally to adjust for the second shot. The mold closes and injects the first shot; then the first-shot core/slide is pulled, the second-shot core/slide is set, and then the second shot is injected. There are cases where there is just one core/slide, which pulls back after the first shot and creates the cavity for the second shot. In either case, the setup and process are the same.
There are five specific areas that designers and manufacturers need to consider to realize the potential of these unique materials.
Biobrick pharma delivers the best pharmaceutical products range in the market with the most eye-catching prices. We are trying to deliver very easy and flexible business opportunities to our partners in the form of PCD Pharma Franchise and by offering our best third party injection manufacturing services in India. With the help of our skilled and experienced staff, we are capable to manufacture and delivering bulk orders in the shortest time frame.
Reduce cost – The company has also taken some efficient steps to reduce the cost of mold manufacturing by making the use of rational material, prolong the service of the injection molding tool life, and shortening the manufacturing process of injection molding.
Join KraussMaffei for an insightful webinar designed for industry professionals, engineers and anyone interested in the manufacturing processes of PVC pipes. This session will provide a comprehensive understanding of the technology behind the production of high-quality PVC pipes: from raw material preparation to final product testing. Agenda: Introduction to PVC extrusion: overview of the basic principles of PVC pipe extrusion — including the process of melting and shaping PVC resin into pipe forms Equipment and machinery: detailed explanation of the key equipment involved — such as extruders, dies and cooling systems — and their roles in the extrusion process Process parameters: insight into the critical process parameters like temperature, pressure and cooling rates that influence the quality and consistency of the final PVC pipes Energy efficiency: examination of ways to save material and energy use when extruding PVC pipe products
In this three-part collection, veteran molder and moldmaker Jim Fattori brings to bear his 40+ years of on-the-job experience and provides molders his “from the trenches” perspective on on the why, where and how of venting injection molds. Take the trial-and-error out of the molding venting process.
Moretto offers plastics processors and micromolders for a broad suite of auxiliary solutions targeted specifically for precision processing.
Mike Sepe has authored more than 25 ANTEC papers and more than 250 articles illustrating the importance of this interdisciplanary approach. In this collection, we present some of his best work during the years he has been contributing for Plastics Technology Magazine.
Currier Plastics had a major stake in small hotel amenity bottles until state legislators banned them. Here’s how Currier adapted to that challenge.
Discover how artifical intelligence is revolutionizing plastics processing. Hear from industry experts on the future impact of AI on your operations and envision a fully interconnected plant.
Concerning tool design, you need to make sure the first-shot cavity has support against the second-shot cavity pressure. At times, ribs or undercuts are needed to hold the first shot in place to prevent flash and deformation. Make sure your hydraulic cylinders actuating the cores are robust enough to resist the cavity plastic pressure or you will be struggling with flash and narrow process windows.
Plastics Technology covers technical and business Information for Plastics Processors in Injection Molding, Extrusion, Blow Molding, Plastic Additives, Compounding, Plastic Materials, and Resin Pricing. About Us
Crush would be defined as the shutoff to prevent the second-shot material from flashing or bleeding out onto the first-shot plastic where it doesn’t belong. Crush is a raised area of cavity steel that presses into the first shot to prevent flash, typically 0.003-0.005 in. Also, in areas with thicker wall stock on the first shot, you may have to add extra crush to compensate for the extra shrinkage. You can crush by adding steel to the second-shot shutoff or adding first-shot material by removing steel.
Here we have got a procedure of our manufacturing process which will help you to understand our company working method in a better way. We have a huge team of workers who are the main heroes of our company as they put their all dedication and hard work into our production process.
Gifted with extraordinary technical know how and an authoritative yet plain English writing style, in this collection of articles Fattori offers his insights on a variety of molding-related topics that are bound to make your days on the production floor go a little bit better.
Plastics Technology’s Tech Days is back! Every Tuesday in October, a series of five online presentations will be given by industry supplier around the following topics: Injection Molding — New Technologies, Efficiencies Film Extrusion — New Technologies, Efficiencies Upstream/Downstream Operations Injection Molding — Sustainability Extrusion — Compounding Coming out of NPE2024, PT identified a variety of topics, technologies and trends that are driving and shaping the evolution of plastic products manufacturing — from recycling/recyclability and energy optimization to AI-based process control and automation implementation. PT Tech Days is designed to provide a robust, curated, accessible platform through which plastics professionals can explore these trends, have direct access to subject-matter experts and develop strategies for applying solutions in their operations.
Join Wittmann for an engaging webinar on the transformative impact of manufacturing execution systems (MES) in the plastic injection molding industry. Discover how MES enhances production efficiency, quality control and real-time monitoring while also reducing downtime. It will explore the integration of MES with existing systems, emphasizing compliance and traceability for automotive and medical sectors. Learn about the latest advancements in IoT and AI technologies and how they drive innovation and continuous improvement in MES. Agenda: Overview of MES benefits What is MES? Definition, role and brief history Historical perspective and evolution Longevity and analytics Connectivity: importance, standards and integration Advantages of MES: efficiency, real-time data, traceability and cost savings Emerging technologies: IoT and AI in MES
AIM Processing has parlayed small part molding expertise and aggressive automation, even for short run production, into a highly successful custom molding business.
This month’s resin pricing report includes PT’s quarterly check-in on select engineering resins, including nylon 6 and 66.
Join this webinar to explore the transformative benefits of retrofitting your existing injection molding machines (IMMs). Engel will guide you through upgrading your equipment to enhance monitoring, control and adaptability — all while integrating digital technologies. You'll learn about the latest trends in IMM retrofitting (including Euromap interfaces and plasticizing retrofits) and discover how to future-proof your machines for a competitive edge. With insights from industry experts, it'll walk you through the decision-making process, ensuring you make informed choices that drive your business forward. Agenda: Maximize the value of your current IMMs through strategic retrofitting Learn how to integrate digital technologies to enhance monitoring and control Explore the benefits of Euromap interfaces and plasticizing retrofits Understand how retrofitting can help meet new product demands and improve adaptability Discover how Engel can support your retrofitting needs, from free consultations to execution
After successfully introducing a combined conference for moldmakers and injection molders in 2022, Plastics Technology and MoldMaking Technology are once again joining forces for a tooling/molding two-for-one.
Join Engel in exploring the future of battery molding technology. Discover advancements in thermoplastic composites for battery housings, innovative automation solutions and the latest in large-tonnage equipment designed for e-mobility — all with a focus on cost-efficient solutions. Agenda: Learn about cutting-edge thermoplastic composites for durable, sustainable and cost-efficient battery housings Explore advanced automation concepts for efficient and scalable production See the latest large-tonnage equipment and technology innovations for e-mobility solutions
We are known as the best Injection Manufacturer and Supplier in India as the company works most effectively and efficiently. There are many strict steps taken by us which help us to work in better ways. We understand the importance of the money thus we go through several parameters that help us to reduce our production chargers which also reduces the prices of our medicines.
You also need to make sure the first-shot part is supported in the second-shot cavities to prevent the second-Shot cavity pressure from deforming or compressing the first-shot material. I have seen many times where the first-shot part was not supported properly, which contributed to flash and deformed parts. Remember that the second shot is applying thousands of pounds of plastic pressure against the first-shot plastic, not just the steel.
Mixed in among thought leaders from leading suppliers to injection molders and mold makers at the 2023 Molding and MoldMaking conferences will be molders and toolmakers themselves.
As I mentioned, the movable/rotating half contains the first-shot cavities and the stationary half contains cavities for the first shot and the second shot. After injection, the mold rotates to align the first shot with the second-shot cavity. So in one cycle you are molding the first shot with the base material and molding the second-shot material over the first-shot parts from the previous cycle. There are two sets of ejector plates because you are only ejecting the parts with both materials molded, leaving the others to have the second shot molded. There are two important things to consider in the tool design for the first shot when it is in the second-shot position: crush and support.
Top Injection Manufacturing Company in India – Biobrick Pharma, established in the year 2015 is a reputed company engaged in the manufacturing and trading of a wide range of injections, tablets, capsules, syrups, soft gel, and hard gelatin capsules, etc. We are an ISO accredited company with WHO & GMP certified units that manufactures all the products under the norms of the healthcare organization to maintain the national as well as international quality standards.
With advocacy, communication and sustainability as three main pillars, Seaholm leads a trade association to NPE that ‘is more active today than we have ever been.’
Over the years, I have preached about robust process windows. In two-shot molding, this becomes a greater focus with another variable involved. People often will process the first shot to address issues with the second-shot process, or the opposite. Crush, support, deflection, and inadequately sized cylinders can all contribute to issues that many molders will process around, putting them at risk for quality issues and scrap.
While prices moved up for three of the five commodity resins, there was potential for a flat trajectory for the rest of the third quarter.
Product Manufacturing – The main task that takes place is well-maintained and prepared manufacturing units that are national and international certified and ensures the quality of the injections to be 100%. All the production takes place under the supervision of the experts and goes through several tests before getting shift to the final step.
Improvements in nozzle design in recent years overcome some of the limitations of previous filter, mixing, and shut-off nozzles.
ABOUT THE AUTHOR: Randy Kerkstra has been in the plastics industry for more than 26 years, occupied frequently with troubleshooting injection molding. He is currently a tooling manager for a large, multi-plant molding and manufacturing company. Contact: kbmoldingsolutions@gmail.com.
Multiple speakers at Molding 2023 will address the ways simulation can impact material substitution decisions, process profitability and simplification of mold design.
What are the basic building blocks of plastics and how do they affect the processing of that material and its potential applications in the real world? Meet the repeat unit.
Use of Better technological level – We have opted for new techniques and latest machinery in our production sites, with the new materials to improve the manufacturing efficiency for better results.
Shorten the manufacturing cycle – We make effort to shorten the process of the forming technique of injection by drawing up a reasonable systematic manner, making use of scientific and economic equipment, and using the latest techniques to manufacture single-piece production into multi-piece production.
Introduced by Zeiger and Spark Industries at the PTXPO, the nozzle is designed for maximum heat transfer and uniformity with a continuous taper for self cleaning.
The increasing chronic health issues like Arthritis, Asthma, Cancer, Chronic Obstructive Pulmonary Disease, Diabetes, and Wilson’s disease like autoimmune diseases, cystic fibrosis, hepatitis C, hemophilia, etc. are also the reasons for increasing demand for injectables, as these issues can be cured effectively with injections. We BioBrick Pharma, being the top Injection Manufacturer and Supplier in India, think it’s our responsibility to contribute as much as we can in the world for mankind.
An overview on the use of chemical foaming agents (CFAs) to successfully foam single and multilayered rotational molding parts, this webinar will illustrate the multiple benefits rotational molders can achieve, including reducing resin consumption, decreasing part weight, enhancing wall thickness and improving structural rigidity. Agenda: Charging the mold Dosing ratios Venting Optimal decomposition temperatures, cycle times and drop times for drop box applications Cooling considerations
GETTING A QUOTE WITH LK-MOULD IS FREE AND SIMPLE.
FIND MORE OF OUR SERVICES:
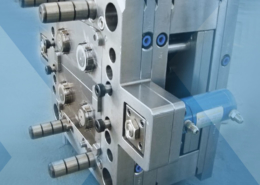
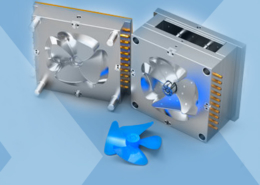
Plastic Molding

Rapid Prototyping
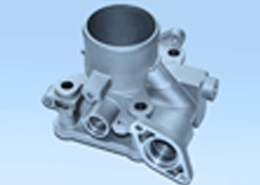
Pressure Die Casting
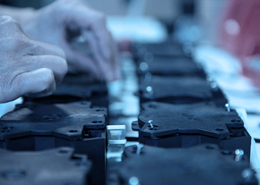
Parts Assembly
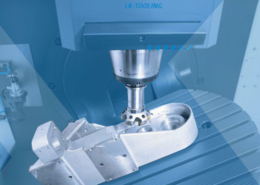