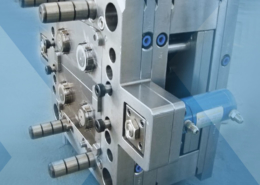
Unraveling the World of Injection Tooling
Author:gly Date: 2024-06-08
Injection tooling stands as a cornerstone of modern manufacturing, facilitating the production of intricate plastic components essential across various industries. In this article, we delve into the realm of injection tooling, exploring its significance, intricacies, advancements, and impact on industrial processes.
Introduction
Injection tooling, also known as injection molds or dies, serves as the backbone of injection molding processes, enabling the mass production of plastic parts with high precision and consistency. From automotive components to medical devices and consumer electronics, injection tooling plays a pivotal role in shaping modern products. Understanding the fundamentals of injection tooling is paramount for manufacturers seeking to optimize production efficiency and product quality.
Evolution and Technological Advancements
The evolution of injection tooling has been marked by continuous innovation and technological advancements. Traditional tooling methods have given way to computer-aided design (CAD) and computer-aided manufacturing (CAM) technologies, revolutionizing the design and production processes. Advanced materials, such as high-strength steels and alloys, have enhanced durability and longevity, enabling injection molds to withstand high pressures and temperatures. Moreover, the integration of automation and robotics has streamlined production workflows, further improving efficiency and repeatability.
Design Principles and Considerations
The design of injection tooling is a complex endeavor that requires meticulous attention to detail and adherence to engineering principles. Factors such as part geometry, material properties, mold flow analysis, and cooling system design profoundly influence the performance and quality of injection molds. Design optimization techniques, including conformal cooling and multi-cavity layouts, are employed to minimize cycle times and maximize productivity. Additionally, considerations for tool maintenance, repairability, and scalability are crucial for ensuring long-term viability and cost-effectiveness.
Material Selection and Surface Treatments
The selection of materials for injection tooling is critical to achieving desired performance and durability. Common materials include tool steels, aluminum alloys, and beryllium copper, each offering unique properties suited to specific applications. Surface treatments, such as nitriding, chrome plating, and diamond-like carbon (DLC) coatings, enhance wear resistance, corrosion resistance, and release properties, prolonging the lifespan of injection molds and improving part quality. Furthermore, advancements in surface texturing technologies enable the replication of intricate surface finishes and textures, enhancing the aesthetic appeal of molded parts.
Precision Manufacturing and Quality Assurance
Precision manufacturing techniques are paramount in ensuring the dimensional accuracy and consistency of injection molded parts. High-precision machining processes, such as CNC milling and electrical discharge machining (EDM), are employed to fabricate intricate mold cavities and features with micron-level precision. In-process monitoring and quality assurance measures, including mold flow analysis, dimensional inspection, and material testing, are implemented to detect defects and deviations early in the production process, minimizing waste and ensuring compliance with stringent quality standards.
Sustainability and Environmental Considerations
In recent years, sustainability has emerged as a key focus area in injection molding, prompting manufacturers to explore environmentally friendly practices and materials. The development of bio-based polymers, recycled plastics, and biodegradable additives offers promising avenues for reducing the environmental footprint of injection tooling. Furthermore, optimization of production processes to minimize energy consumption, waste generation, and emissions contributes to a more sustainable manufacturing ecosystem.
Conclusion
In conclusion, injection tooling plays a central role in modern manufacturing, enabling the production of complex plastic components essential to various industries. Through continuous innovation, technological advancements, and adherence to quality standards, injection tooling manufacturers strive to meet the evolving needs of the market while addressing challenges such as sustainability and cost-effectiveness. As we look to the future, further research and development efforts will be crucial in unlocking new opportunities and pushing the boundaries of injection molding technology.
Through this exploration, we gain a deeper appreciation for the intricacies of injection tooling and its profound impact on industrial processes and product development. By embracing advancements in materials, design, and manufacturing techniques, manufacturers can unlock new possibilities and drive innovation in the dynamic world of injection molding.
GETTING A QUOTE WITH LK-MOULD IS FREE AND SIMPLE.
FIND MORE OF OUR SERVICES:
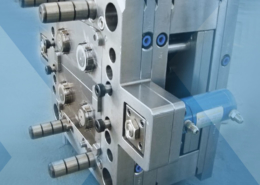
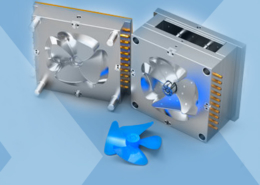
Plastic Molding

Rapid Prototyping
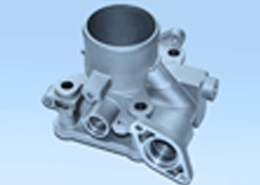
Pressure Die Casting
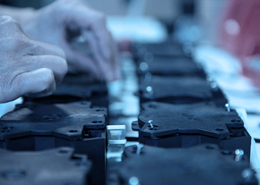
Parts Assembly
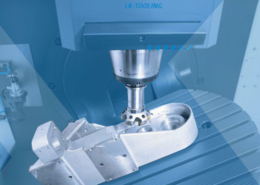