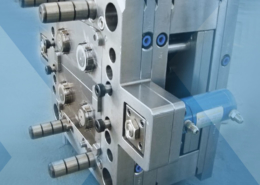
Murray Plastics: Custom Plastic Injection Molding Company - custom plastic moldi
Author:gly Date: 2024-10-15
At Fakuma 2024, ENGEL will present innovative solutions shaping the future of plastics processing. A key highlight is the ...
Speed up tool changes with the set-up assistant in your machine control and reduce your set-up times by up to 80%.Don't miss the live demonstrations of the set-up assistant on the machine exhibit victory 860/160 tech WP (Hall A5 / Booth 5203)!
At Fakuma 2024, ENGEL unveils the latest model of its successful temperature water manifold: the eco-flomo XL. This larger ...
Injection moulding machines from 280 kN to 55,000 kN clamping force for all your requirements. Hydraulic, all-electric, hybrid, horizontal and vertical solutions of the highest quality.
At the “Plasticising” Expert Corner, ENGEL will introduce new technologies aimed at further increasing efficiency, precision, ...
Plastic injection molds can be used for both rapid prototyping and end-use production of plastic parts. Be it for a pilot series of 200 to millions of parts, the injection process will mostly remain the same. Plastic injection molding your prototypes, small or pilot series, will enable you to produce affordable, functional and mechanical parts close to the reality. The difference will lie in the mold itself. We then distinguish between a prototype mold (also called rapid tooling) and mass production mold (also called mass tooling).
The combination of high load capacity, stability, ease of use, flexibility, and efficiency makes ENGEL's viper linear robots ...
You will generally use a prototype mold to produce small series of plastic injected parts from around 200 to a few thousand. The structure of the mold is simplified and optimized so as to accelerate the manufacturing process and lower the overall cost. This kind of mold consists of a standard interchangeable metal mold base and customized aluminium core and cavity inserts. The latter is manufactured your by CNC machining. Machining aluminium is easier and faster, it is also more flexible in case you need to modify or adapt the design. The ejection, guiding, cooling and thermic regulation functions are simplified and using aluminium lowers the injection cycles.
The driving force behind our innovative strength is our employees. We are committed to plastics as the material of the future and work passionately as a large, international team every day to provide our customers with the best solutions for their requirements.
For over 75 years, we have been guaranteeing our customers a head start and constant progress - in line with our motto "be the first". With the development and production of injection moulding machines, technologies and digital solutions, we at ENGEL are shaping the plastics processing of the future.
Frequent mould or material changes without loss of time or performance are just some of the challenges that custom moulders face on a daily basis. Our injection moulding solutions make it possible to remain flexible and efficient in the production of plastic parts.
Competence in injection moulding automation at all levels: From injection moulding machines, robots and conveyor belt systems to peripheral equipment.
We have nine production plants in Europe, North America and Asia as well as subsidiaries and representatives in over 85 countries and over 7,000 employees worldwide.
From June 18 to 20, 2024, ENGEL hosted the Digital Days event in Schwertberg and St. Valentin. Over 400 enthusiastic visitors attended, gaining exciting insights into the current state of advancing digitalisation in injection moulding through practical examples, and offering interesting perspectives on the near future.
Mass production molds are used to produce large scale series of plastic injected parts in their thousands up to several million. The structure of the molds is more complex and is manufactured using robust, high quality steel with components to fit with long-term mass production. This would integrate all the traditional functions such as precise alimentation and guiding, advanced temperature regulation etc. This also means much higher development costs and longer manufacturing process.
From single visual to high end small pilot series of plastic prototype parts, Prototech has always strived to offer you the most flexible and cost-efficient solution to your prototyping needs. Our rapid production delay and affordable aluminum prototyping molds enable to reduce concept risks and lower production costs for your prototypes and small series. For more information or for any project you may have please contact us by filling the form on our contact page.
There are several kinds of plastic injection molds according to the number of parts to be produced and their functions. The molds are the core part of the injection process from the molding to the ejection of the part.
With the CC300 plus, ENGEL introduces an advanced control concept that excels with improved ergonomics and personalisation ...
In times of changing economic conditions, flexibility and responsiveness are trumps. With our stock machines, we provide you with exactly the quick adaptability that market conditions require. Buy an injection moulding machine today and put it into operation soon.
Internet Explorer is no longer supported. Please switch to a current browser to be able to use engelglobal.com to its full extent.
Internet Explorer is no longer supported. Please switch to a current browser to be able to use engelglobal.com to its full extent.
Thinking ahead in plastics processing: Serving the diverse requirements of a modern world with resource-saving processes.
At Fakuma 2024, ENGEL offers a comprehensive overview of the latest innovations in injection moulding and large-scale machinery ...
Our training programme ensures effective knowledge building in injection moulding. Whether digital or on-site, in the training centre or at your machine, with a trainer or as e-learning.
Our digital solutions support you along the entire product life cycle. From component design through sampling and production to maintenance and service.
GETTING A QUOTE WITH LK-MOULD IS FREE AND SIMPLE.
FIND MORE OF OUR SERVICES:
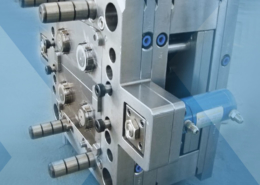
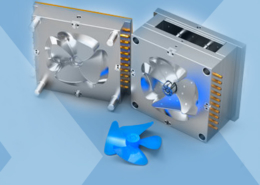
Plastic Molding

Rapid Prototyping
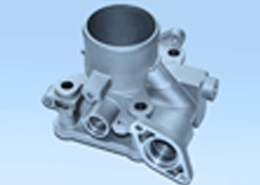
Pressure Die Casting
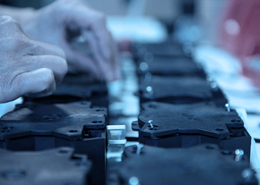
Parts Assembly
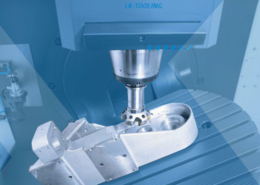