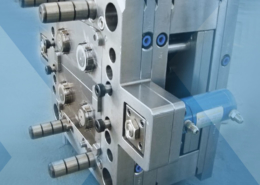
Unraveling the Economics of Injection Moulding Mould Cost
Author:gly Date: 2024-06-08
Introduction:
Injection moulding is a ubiquitous manufacturing process utilized across various industries for the mass production of plastic components. At the heart of this process lies the injection moulding mould, a crucial tool that shapes the final product. Understanding the intricacies of injection moulding mould cost is essential for businesses aiming to optimize their manufacturing processes while managing expenses effectively. This article delves into the factors that influence injection moulding mould cost, providing insights into the economics of mould fabrication and its implications for businesses.
Material Selection and Cost Implications
The choice of materials for injection moulding mould fabrication significantly impacts cost considerations. Different mould materials, such as steel, aluminum, and alloys, come with varying price points, each offering distinct advantages in terms of durability, heat resistance, and machinability. While steel moulds are durable and well-suited for high-volume production, they entail higher upfront costs due to material expenses and longer machining times. Conversely, aluminum moulds offer cost-effective options for prototyping or low-volume production but may require more frequent replacement or refurbishment, leading to higher lifecycle costs. Balancing material selection with cost considerations is crucial for achieving cost-effective mould fabrication without compromising on quality or performance.
Complexity of Mould Design
The complexity of mould design is another key factor influencing injection moulding mould cost. Intricate part geometries, undercuts, and complex features necessitate specialized mould designs and machining techniques, driving up fabrication expenses. Advanced mould designs incorporating features such as multi-cavity layouts, interchangeable inserts, and conformal cooling channels offer benefits in terms of production efficiency and part quality but may incur higher upfront costs. Moreover, factors such as tolerances, surface finishes, and finishing requirements further contribute to mould complexity and cost implications. By optimizing mould design for manufacturability and cost efficiency, businesses can mitigate expenses while achieving desired part specifications.
Production Volume and Economies of Scale
Production volume plays a significant role in determining injection moulding mould cost. Economies of scale dictate that larger production runs typically result in lower per-unit mould costs due to spreading fixed expenses across a greater number of parts. However, smaller production runs may incur higher setup costs, tooling expenses, and overhead, leading to comparatively higher unit mould prices. Manufacturers must carefully evaluate production volume requirements and optimize batch sizes to maximize cost efficiency while minimizing inventory holding costs. Additionally, strategic planning and forecasting can help businesses align production volumes with market demand to optimize resource utilization and minimize wastage.
Technological Advancements and Cost Optimization
Technological advancements in mould fabrication processes and equipment present opportunities for cost optimization in injection moulding. Innovations such as computer-aided design (CAD), simulation software, and additive manufacturing technologies streamline mould design, optimize tool paths, and reduce lead times, ultimately driving down fabrication costs. Additionally, advancements in materials science, such as the development of high-performance tool steels and coatings, enhance mould durability and longevity, reducing maintenance costs and downtime. By embracing technological advancements and adopting best practices in mould fabrication, businesses can achieve cost-effective production while maintaining competitiveness in the market.
Conclusion:
In conclusion, injection moulding mould cost is influenced by various factors, including material selection, mould design complexity, production volume, and technological advancements. By understanding these factors and implementing strategic measures for cost optimization, businesses can effectively manage mould fabrication expenses while maintaining quality standards and meeting customer expectations. Continuous innovation in materials, processes, and technologies presents opportunities for further cost reduction and efficiency improvement in injection moulding, ensuring competitiveness and sustainability in a rapidly evolving manufacturing landscape.
Word Count: 582
GETTING A QUOTE WITH LK-MOULD IS FREE AND SIMPLE.
FIND MORE OF OUR SERVICES:
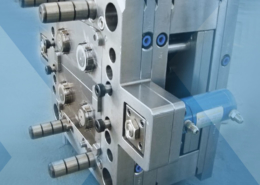
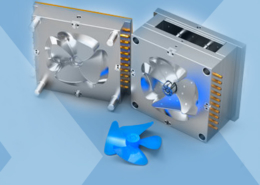
Plastic Molding

Rapid Prototyping
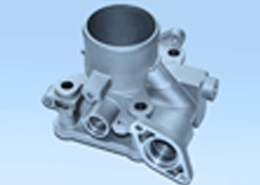
Pressure Die Casting
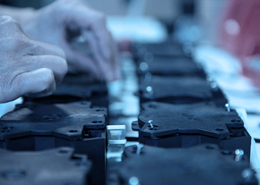
Parts Assembly
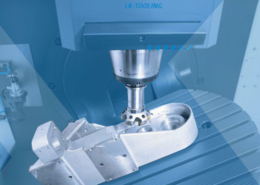