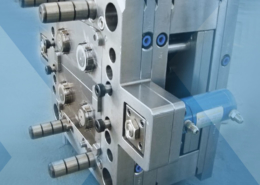
Multi Mold Plastics Inc, 128 Basaltic Rd, Vaughan, ON L4K ... - multi mold plast
Author:gly Date: 2024-10-15
Office:1602, Unit 8, Building 2, Shangxing Commercial Street, Shangde Road, Xinqiao Street, Baoan District, Shenzhen City 518125
CNC machining optionsStainless steels MenuStainless steelsRelated LinksFinishing OptionsCNC Materials MenuFinishing OptionsCNC Materials
What has made the company survive for this long is their use of modern technology and the latest machines for their assembly line. This ensures that the products are of high quality, are reliable, and able to compete with others on the market. Some of the industries that benefit from RYDTOOLING products are spread out in the electronic sector and automotive industries, where the demand for unique and complex parts is ever increasing.
3D Printing options3D printing materials Menu3D printing materials3D Printing LinksThe application of 3D printing in the laryngoscope mold3D printing raise the manufacturing capacityHow much should you pay for your 3D printing components? MenuThe application of 3D printing in the laryngoscope mold3D printing raise the manufacturing capacityHow much should you pay for your 3D printing components?
Die casting optionsAluminium die castingZinc Die castingGravity CastingLow-pressure die casting MenuAluminium die castingZinc Die castingGravity CastingLow-pressure die castingRelated LinksDie casting Tolerance5G productsAutomobile gearboxMaterials for die castings MenuDie casting Tolerance5G productsAutomobile gearboxMaterials for die castings
Some of the top customers that frequent Goodfish Group for their products come from the medical industry, automotive suppliers, OEMs makers, and a host of other commercial enterprises spread out throughout the nation and beyond. The heavy use of technology has been a big factor in ensuring that the company keeps pace with some of its big competitors, and its exponential growth will continue to shoot upwards as its reputation among consumers continues to prosper.
3C consuming electrics keep seeking improments on the product appearance: small, simple, beautiful, dustproof and waterproof. however, the requirement for this kind of mateiral and procesing normally have clashes, which means it is unable to meet more than one requirement with the traditional design or manufacturing.
Factory1:NO. 101,Building 21, Zone B, Yuanshan Industrial Zone, Shangcun Community, Gongming Street, Guangming District, Shenzhen City, Guangdong Province, China
Advantages of multi-shot implant injection molding solutions: it makes one-piece molding and multifunctional integration avaliable, and it supports multi-color modeling without assembly. The key of this technique is the flexible adoptation of bertical injection molding machine. Common machine types include 1 shot x 6stations, 2 shot x 4 stations, 3 shots x 6 stations, among which the multi-station cooling can shorten molding time and increase output. At the same time, it is more convenient to implant injection molding and extract products, and it can achieve automated production.
Strength and Durability: Injection molding reduces the need for making multiple parts and replaces all the unnecessary additions with one complete product. This reduces lines of weaknesses, making the end product strong enough to withstand extreme conditions and pressure. This is the reason why injection molding products are used for some of the most intense industries like the aeronautical space and automotive sectors that can only work with durable and strong products for increased safety.
Finishing Services optionsAnodic OxidationSandblastingPlastic ElectroplatingMetal Electroplating MenuAnodic OxidationSandblastingPlastic ElectroplatingMetal ElectroplatingRelated LinksSecondary processing MenuSecondary processing
The company is operated by a group of highly trained professionals who are invested in research and technology, the two pillars that are responsible for their continued growth over the years. There are a number of industries that rely on their products, and they range from automotive industry, aerospace, the medical industry, food, and beverage, among many others.
With the rapid development of smart phones and mobile Internet, more and more smart wearable products have come into our sight. This type of products require an integrated service achieved within a small space. When producing this type of products, it is hard to fix the impalnts if the mold is opened horizontally with traditional injection molding, and there are risks during mold compression due to the insufficient space in mold. What’s more, it is harder for multi material injection molding. As a new production technology, manufacturers of precision injection molding products with small area functions have unique advantages.
Reduced Waste: As far as recycling is concerned. Injection molding is one of the most effective methods of reducing waste since unused raw materials can always be fed back into the production line without sling any of their good qualities. This is not only good for the environment in general, but it also helps the manufacturer to save a lot of money that would otherwise have gone down the drain.
This website uses cookies to improve your experience while you navigate through the website. Out of these cookies, the cookies that are categorized as necessary are stored on your browser as they are essential for the working of basic functionalities of the website.
With the increase of complexity of products, three or four color injection molding needs are more popular. Generally speakingk, the three-color machine has two types, one is two station three-color machine, and another one is three station three-color machine. The difference of them is that they adopt differen turntable control mode according to the sturcure design of products (Two sets of moulds or three sets of moulds).
2. Three color injection molding structures are divided into five categories: right angle tricolor – L type, roof tricolor – V type, back tricolor – LW type, back tricolor – VW type, and independent tricolor – LV type.
The company is home to over 250 workers who handle various levels of the injection molding process. They are well trained with the ability to see to each level of injection molding, from coming up with the design, prototyping all the way to the branding part. Their products are in high demand across the country and beyond, with both domestic and commercial industries benefiting from their unique and dependable products. Products made by Sanpac have been certified by the national bureau of standards and are in high demand by consumers both within the East African nation and beyond.
We are going to look at some of these top companies derived from all around the world. We will look at their history, the type of products they make, the number of employees they have, their location, among other important information. If you are looking for an injection molding company to partner with or have business dealings with, then stick to the end, and you may see a couple of them that may fit your needs.
Wide Range of Raw Materials: There’s flexibility when it comes to the range of raw materials that can be used for injection molding, especially plastics. You can go with thermoplastics or thermosets, rubber, and a host of other plastic-based materials. These materials are not only cheaper but are widely available. This makes high-volume production more cost-effective and profitable for those involved.
Having been in the industry for more than 30 years, Britech Industries can be considered to be among the largest injection molding dealers in the great state of Florida. It all began as a small warehouse in Miami that was tasked with the work of supplying manufacturers in the state with extruded rubber parts. As time progressed, the company started evolving, taking on more roles as the demand for injection molds rose as more manufacturers set up shop in the area.
3.When the mold is opened horizontally, the embedded parts need to be specially designed with a fixed structure, or they will be inclined due to gravity.
PMT Inc is another veteran player in the injection molding space, having been active since 1973. Located in El Paso, Texas, PMT Inc deals with the manufacture of precision-engineered and injection molded parts that are used across a wide range of industries that are both found in Texas and beyond. The company offers fully customized services that begin with the initial design, engineering, mold sourcing, and the production process itself, all thanks to a number of highly qualified workers who are able to handle every part of the process with the help of automated systems.
Notable brands and companies that are part of BC Plastics’ clientele include Hutchinsons, Telstra, Ergon, Jetstar, Virgin Air, Landlease, just to mention a notable few. The industries that make use of their products range from the automotive space, medical industry, consumer appliances, and other commercial and domestic purposes. BC Plastics supplies most of Australia with the surplus going overseas as exports to places like China, India, Europe, and North America.
Cost-Effective: A huge chunk of injection molding is automated, and this means that the costs of having to settle salaries or compensate people in case of a workplace injury are all but eliminated. Where robots are involved, the work is not only safer, but the quality is high, the process faster, and this increase in production ensures that more profits come in and losses are minimized.
Montrose Molders is a large part manufacturer that sits on 25,000 square feet of land, which offers more than enough space for heavy machinery and automated systems to be run without any hitch. If you are in New Jersey and you are looking for good injection molding solutions, then Montrose Moldings is where you want to be.
Goodfish Group was established in 2010, starting out as a provider and supplier of injection molding products and services to the neighboring settlements and manufacturers. They gradually expanded with time and are now considered to be among the top injection molding companies in the whole of the UK.
Injection molding process: place pin in station 1. Station 2 combines with the first injection cavity to inject transparent window parts. Station 3 combines with the second injection cavity to inject black shading structure. Station 4 combines with the 3rd injection cavity to inject colored colored shells. Station 5 is are cooled, and the product dislodge is in 6 station. All stations can be operted at the same time.
Sanpac Africa has two branches in Mombasa and Nairobi and has a very interesting history. The company began in 1972 as Santowels Limited, a small factory that manufactured sanitary napkins. This was the main business for a number of years until 1989 when it invested in an injection molding unit, and this opened up more business opportunities for it.
The company has plants in other states that help with bringing their products closer to people from other areas. The new plant has been dealing exclusively with injection molding through the use of thermoplastics and resins. The company has even set aside a separate website for injection molded parts. Britech products are of high quality and are durable, part of the reason why the company continues to expand to new frontiers every year. Some common molds likely to be found in their roster include triangle sections, ribbed stocks, seals, and gaskets, among other plastic products that are used commercially and for domestic purposes.
There are countless other injection molding companies spread out across the globe that are equally as good but couldn’t fit into this review. Injection molding continues to grow with leaps and bounds, and there’s every indication that points to the fact that it will play a vital role in the future of manufacturing. If you have been contemplating getting into the injection molding space but have no clue where to begin, don’t hesitate to visit our website when you get the time. Our qualified team of experts will be there to answer all your questions and concerns.
You have some questions? Upload your drawings or documents, and we have professional technicians to answer them for you.
The demand for Two-Shot molding products in Africa is rapidly increasing, and this has placed companies like Sanpac in a very good position that allows them to take advantage of their resources to further expand their reach locally and beyond.
Speed: Injection molding has one of the shortest cycle times in manufacturing, and this makes it a very fast production process if you have the right tools and people in place. It has a very high output rate, and going with it is the only way manufacturers are able to keep up with the ever-increasing demand for injection molds. Manufacturers are now able to clear their orders ten times faster without compromising the quality of the end products.
It comnines the multi material injection molding and mold, vertical rotary table injection molding machine, automatically extraction and other implantation, as well as other multidisciplinary integrated technologies.
Some of the industries that rely on injection molding products from PMT Inc include the automotive industry, electronics, consumer appliances, medical products and devices, telecom, business devices, boating accessories, and recreational vehicles. Owing to their durability and reliability, almost all the manufacturers in Texas are big clients of PMT inc and if you ever find yourself in need of a good injection molding provider when in Texas, don’t hesitate to give PMT Inc a call.
The company prides itself in its use of the best manufacturing technologies, state-of-the-art machinery, a powerful and talented workforce, and experience. All these factors combine well to produce high-quality and well-balanced products that are in high demand in various industries like automotive, food and beverage, aerospace, medical, among many others. Most of the designs are done in-house by a team of talented designers who then pass on the blueprints to the molding division that ensures the perfect molds are created, just as dictated by client requests.
For original procedure, it needs to design fixed structure between parts or to meet waterproof requirements with auxiliary materials (sealing ring and adhesive). However, due to the aging of sealing ring, strength and stability of dispense glue, the waterproof performance is affected. Now, by multicolor implantation injection molding process, put the key parts in the mold for integrated molding, which largely increase the waterproof performance. While, since this technique require multiple sets of molds, so the cost is indeed higher. Thus, it is often used for large volume and small sized products.
Multi-shot implant injection molding is suitable for producing the bottom cover of this type of band. Combining the six procedures into one procedure not only can significantly simplify the flow, but also saves a large amount of material transfer, personnel input, defective product consumption and other costs. Meanwhile, it also reduces environmental pollution.
1.The overmolding injection molding can be divided into 5 types: 1. Type P (parallel double shot), L (right angle double shot), V (sky side double shot), W (oblique back double shot), H (opposite double shot).
Multi-component injectoin molding is also named as the multi color injection molding process, refering to the mateiral that has two kinds of color or more than two used for injection molding through a mold with one or more runners. At first, it is featured by two-color injection molding. Our daily contact is mostly two-color products. For example, the handle of the toothbrush we use every morning and evening are made with two-color injection molding. The common material of handle used is PP (hard glue)+TPE (soft glue). TPE is the best material to blend with PP adhesive coating, and the coating soft adhesive is to improve the grip.
1. For the traditional horizontal overmolding machine, the position of the shooting table is fixed, and the shooting table other than the second shooting can only be arranged on the top side and the horizontal side (insert the multi shooting table layout mode). The glue feeding channel interferes with each other.
“Two station” refers to teh two positions of the turntable rotation, which equals to the 180 degree turntable control mode of two-color machine, or we can say the two groups are injected into the same mold at the same time in the three groups of injection units of the two station three color machine. So, if the boundary of two components is not adjacent (it can be designed to inject in the same mold at the same time) in products, just producing three component products with two sets of mold, which is suitable for the two station three color machine.
The traditional horizontal injection molding process has encountered more and more bottlenecks in solving such products.
In 1992, the company expanded into the blow molding and extrusion market to further enhance its portfolio and to gain the ability to compete with other major players in the industry. The company continued its upward trajectory, which culminated with another branch being opened in Mombasa and the final rebranding into Sanpac in 2006. To date, the company has been able to evolve into a leading injection molding maker in the region, thanks to the adoption of robotic technology in 2010 to aid with the production process. This boosted productivity to a great extent on top of increasing the range as far as plastic products are concerned.
It didn’t take long for the company to be the supplier of the entire state of Florida, and by 2005, it had started supplying the entire nation and other countries in the region and beyond. 2005 was also the year the company went full-scale with injection molding, adding more clients to their already impressive roster. Some of the industries that are reliant on products from Britech range from food and beverage, automotive, aerospace, drugs, and health industries, among others.
Located in one of the busiest locations in China, RYDTOOLING has been active for over 15 years and continues to expand every year, thanks to the high-quality injection molds the company produces. The main factory is a moderate workshop that sits on 4000 square meters of land and houses about 11 sets of accurate CNC machines and nine sets of EDM machines that are seen to and operated by about 90 employees.
It can reduce the process of assembly, enhance bonding and improve air tightness by completing plastic (soft/hard), silica gel (solid/liquid), hardware (structure/conductor), electronic chips in a machine cycle.
To address the issue of the integrating mateirals with different characteristics and functions thorugh injection moldng and implantation in a small space.
Three station is different. The turntable can be positioned at three different positions (120degrees). In other words, the three groups of injection units of the three station &three color machine are respectively injected into three pairs of molds. Therefore, if the boundaries of the three components in the product are adjacent, the three station & three color machine is applicable.
Transumanoleader officially became a renowned player in the plastic injection circles when it acquired the well known Haitian 200 T automated machines that have been producing all manner of products, including reusable filter masks that have saved many lives in the ongoing COVID-19 pandemic.
On top of all these major branches, the company has a network of smaller locations that handle the distribution of their goods and services on all the continents. Some of the industries that benefit from Husky’s injection molding solutions include the medical and healthcare markets, the food and beverage industries, general packaging, thin-wall packaging, and a number of domestic and commercial uses in varying capacities.
With over 50 years in the game, the company has been able to stay ahead of its competitors by continually evolving with the times. It embraces manufacturing technologies as they come, combining them with state-of-the-art machinery, which ensures that every single product that leaves the assembly line is of the highest quality.
RYDTOOLING products are consumed locally where the demand is ever high due to the high population in the entire country. At the same time, the company has the capacity to produce goods for exports and counts Europe and North America as one of their leading destinations for their injection molds.
The one thing that makes the company stand out so much is the attention to detail that they pour into their work. The products from their assembly line are top of the range and of the highest quality, all thanks to the automated system that they use combined with a highly skilled workforce that is adept at handling the entire production process from inception to design, all the way to packaging and distribution.
Injection molding optionsClear Plastic MoldingInsert MoldingOver MoldingThreaded plastic productsCases for soft rubber mold MenuClear Plastic MoldingInsert MoldingOver MoldingThreaded plastic productsCases for soft rubber moldRelated LinksInjection materialsInjection Molding ToleranceInject Design TipsFinishing OptionsColor card MenuInjection materialsInjection Molding ToleranceInject Design TipsFinishing OptionsColor card
The teams of people behind this success comprise designers, engineers, innovators, software specialists, problem solvers and material handlers who understand their roles and how to properly execute them. The main headquarters of Husky Injection Molding Systems is in Canada, with other major branches in The US, China, Switzerland, Czech Republic, and Luxembourg.
The overmolding is normally featured by two sets of compoents. The half is installed on the fixed mold fixed plate of the overmolding injection molding machine, which is also one side of the injectoin molding gate. Another half is installed on the rotating plate of movable mold, which is the side of mold ejection. The rear molds of these two sets of mold are normally same. The cavity is different. When the first kind of material completes the injectino molding, the fixed and movable molds of injection molding machine open. The rotary plate of the moving die rotates 180 ° with the rear die part of the two molds. Now, do not eject the semi-finished products of the first mold back mold, then clamp the mold before carrying out the injection molding of the second kind of mateiral (during this process, the first kind of material will still be made into semi-finished products in the second mold). After thermal insulation and cooling, the fixed and movable molds are opened. The finished product of the first mold is ejected after moving the mold. This is molding cycle process, in which there will be one semi product and one finished product.
Complex Details and Shapes: If complexity is what you are looking for, then injection molding is the best way to get that done. The process accords manufacturers the flexibility to change the mold gates as they dee fit to produce uniquely shaped products that cannot be replicated by any other person unless they get their hands on the same molds. This gives a company a signature look that consumers can identify with.
Montrose Molders has a checkered history that dates all the way back to 1966, meaning they are among the pioneers when it comes to molding, something that is rare since the technology has not been around for very long. The company began as a 22-person tool shop that dealt with the manufacturing of high-tolerance tools that were in demand by plastic-related industries. This continued for a while until they felt the need to expand as the demand grew. In 1972, Montrose Molders finally invested in their first injection molding press and the rest, as they say, is history.
A huge number of the company’s clients are found within Portugal, but it makes more than enough to cater for both domestic and international needs, with exports going as far as the Americas, Asia, and Africa. Transumanoleader has received a number of awards and certifications over the years, a true testament to how good they are at what they do. Despite being around for far less time than most of their competitors, the company has been able to be a trailblazer in the very competitive space that is plastic injection molding.
Sheet metal optionsBending sheet metal processingConsiderations of the sheet metal parts design MenuBending sheet metal processingConsiderations of the sheet metal parts designRelated LinksSheet metal materials MenuSheet metal materials
3. Four color injection molding structure is divided into two types: parallel four-color – LV type and back four-color – LVW type.
Husky Injection Molding Systems Ltd is one of the biggest conglomerates in plastic manufacturing, something that has taken them years to achieve. What started out as a small manufacturer of injection molding products in Canada has now expanded so wide to the point where it has branches in over 149 countries and a workforce of over 4,300 people worldwide.
The company has a team of experts who are adept at handling specific tasks at every stage of the product. The team designs everything from scratch according to the client’s specifications and continues to provide support even when they have delivered the goods. This close relationship with clients is what has made the company continue amassing clients every year. Some of the benefits one can get from working with RYDTOOLING when it comes to injection molding include the following.
Traditionally, it will make the above functions into different plastic parts, and then assemble them together by assembly.
Located in Lisbon, Transumanoleader was created in 2004 as a distributor of goods within the capital. From these humble beginnings, the company has been able to gradually scale its way up finally adopting injection molding into their manufacturing. The company was acquired by a new owner who embarked on transforming the company into the behemoth that it is today.
Lightweight Products: The products made using this method are not only strong and durable but very lightweight, and this makes them very efficient and convenient for a wide range of uses. These products have made a lot of machines safer and cheaper as they are able to reduce the costlier and heavier metal arts that are being phased out slowly.
The company has three production plants located in Cannock, Worcester, and St. Asaph, where the primary production takes place round the clock, operated by over 125 employees. Over the years, the company has been expanding little by little, incorporating other injection molding styles into their assembly lines in a bid to gain more ground in the industry.
Thus, how to present different colors and textures in such small and exquiste space and also taking into account the requirements for dust and water prevention of internal electronic devices has become a major concern for the CMF and structural designer.
They have different characteristics and customers can select according to their needs. Among them, the V and L types are the most commonly used in Europe. P Type is mostly used in Japan or domesitc made machines. With the five forms of two-color machine, it can continue to derive the definition of the injection form of the three color machine and the four color machine:
The automated machines in use are quite big, and for this reason, the company occupies a very expansive space that houses the entire complex. Some of the raw materials that are used commonly by Pradip Plastics range from Nylon, Polycarbonate, Talc, PP, HDPE, TPE, ABS, among many others. Some common products that are manufactured through their injection molding process include windshield containers, ball cages, ducts, brake fluid containers, fuse box covers, and others. The company also produces goods for export which they send to other regions as far as North America, other Asian countries and Europe.
Located in Maharashtra, Pradip plastics is one of the most renowned injection molding manufacturers in the region and has been actively engaged in the business since 2009. It started as a small company looking to meet the growing demand for high-quality molded parts for the many industries in the area, and over time, it has established itself as a major player, not just in Maharashtra but the entire Indian nation.
The Injection molding process is fully automated, but there are still a number of talented and highly skilled workers who handle the designing part as well as oversee the important bits of the injection process later on. Housed in a huge complex, the company has enough room to set up CNC machines and other components that are used in the prototyping and 3D printing processes, which go hand in hand with injection molding.
BC Plastics is an Australian company that deals with injection molding that has been around for quite a while, providing services and injection molds for the surrounding areas and beyond. The company prides itself on innovation, and this can be seen in the quality of its work. They are also among the few injection molding companies that pay close attention to the environment by using sustainable production methods from how they source their raw materials, how they utilize them, and how they recycle back everything rather than dump them into a landfill.
Injection molding has become a vital manufacturing process around the world, and this has given rise to a number of very exemplary injection molding companies. These companies serve a very wide-ranging sector and more keep popping every day to meet an ever-growing demand for injection mold products.
More and more manufacturers are adopting injection molding for their production, and this is not an accident, and neither are they blindly following a trend. There are good reasons why injection molding has become the go-to option for companies that predominantly deal with plastic products.
With an annual production volume of 150 million injection molded plastics, PMT Inc has received several international awards for its adherence to international standards of quality and safety. Some of the items found in their catalog include lamp sockets, wire harnesses, bobbins, fuse components, computer connectors, and a host of other plastic-based products.
The company has an elite group of workers who have the capacity to design amazing prototypes from scratch, no matter how complicated the request may be. It is this level of reliability that has ensured the company is still standing to this day. Some of the industries that benefit from their products include the automotive, lawn and garden, aerospace, storage, food, and beverage, among many others that serve the daily domestic needs of the population.
The use of technology and the present value-added services are the reason why this company continues to amass a huge number of customers every year. All their products are of high quality, are durable, and are backed by some of the most comprehensive warranty covers. Husky continues to expand its reach to every country on the planet, and all indicators point to a future where the company will be among the biggest conglomerates to ever exist in the injection molding space.
During MSIM, thevertical three-color & six-station rotary table injection molding machine is used. Three cavity and six cores, one out of two with manual placement and pick-up. The whole cycle is 30 sec. The products can be packaged directly after out of mold without assemblying.
Same for the four-color machine, which can be divided into two station or multi-station & four color machine. Technically, the control precision of multi station rotary table is greatly higher than that of two station. Thus, the manufacting cost of products on this machine is relative high. So, we should select the best option according to the requirements of product structure, like the case of three-color USB flash disk, it is more cost-effective to select multiple stations.
Assembly will also brings a series of difficulities, how to add the fastening structure used for fixing, how to combine soft and hard glue, how to hide the assembly line, how to realize the sealing and waterproof of the electronic part, how to make the logo font more permanent, and how to reduce the assembly manpower.
2. The space in the mode locking region is limited, and it needs to repace with the core after finishing the rotation. The space for mold cavity arrangement and slides in mold are smaller.
GETTING A QUOTE WITH LK-MOULD IS FREE AND SIMPLE.
FIND MORE OF OUR SERVICES:
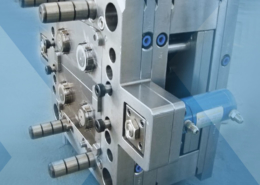
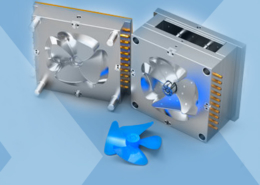
Plastic Molding

Rapid Prototyping
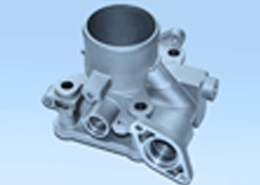
Pressure Die Casting
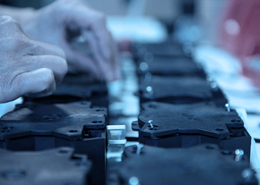
Parts Assembly
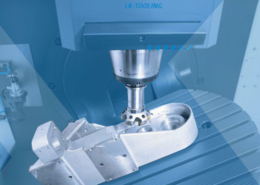