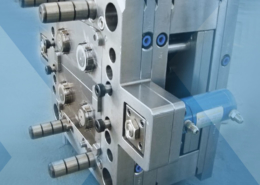
Mould - NSW Health - molding medical
Author:gly Date: 2024-10-15
PVC is a common plastic that has several uses, including piping, flooring, medical equipment, insulation, and more. PVC’s widespread industrial application necessitates not only that it be exceptionally tough, but that its melting point is similarly high. Therefore, the melting point of PVC is close to 210 degrees Celsius.
While everyone desires low-cost injection molding, it’s equally vital to avoid the pitfalls of subpar quality and compromised mold making that often accompany “cheap” options. Sungplastic, drawing from extensive experience and global manufacturing advantages, offers low-cost injection molding without compromising on quality.
There are different types of plastic material available in the market, however, it is important to have a clear understanding of distinct materials for a better injection molding material selection
Injection molding is a complex manufacturing process that requires multiple steps and expertise to ensure each step is performed accurately. In a fiercely competitive market, low-cost injection molding manufacturing has also become a factor that manufacturers need to consider. Low-cost injection molding is the key to maintaining competitiveness and is crucial to the long-term development of enterprises. However, cutting corners anywhere can have costly consequences. Therefore, when looking for an affordable injection molding solution, it is crucial to choose an experienced and skilled company. Sungplastic is an injection molding manufacturer with extensive experience, and we are able to provide low-cost injection molding services without sacrificing quality. Welcome to contact our professional team to discuss your next project and learn more about our affordable injection molding solutions.
Temperature is a naturally very important factor in the process of plastic injection molding, and two specific temperature types hold an especially vital role. These temperature types are the melt temperature and the mold temperature. These are two distinct metrics that are connected in some way, and both of them speak volumes about how the finished injection-molded products will look, feel, and hold up over time. When it comes to the manufacturing of plastic parts using plastic molding, medical plastics manufacturer ensures that there is a correct melt temperature and mold temperature in order to guarantee that the final properties of the part will satisfy its performance requirements. Contact Seasky Medical for more information on the subject.
The price of plastic raw materials directly affects the cost of injection molding, because plastics are usually the main raw materials for low-cost injection molding manufacturing. The following are some common plastic raw materials and their relative prices:
Melt temperature is not the same as the barrel setpoints, which display the methods employed to achieve it. The actual melting temp of plastic also depends on the mechanical work applied to the material, the residence period, and the condition of the screw and barrel. When discussing mold temperature, most people incorrectly assume that this has no bearing on the quality of the finished product. Although subtle, its impact on the finished product’s qualities is significant.
The quality of the molded plastic and the efficiency of the production process depending on the injection molding temperature is just right. One can melt plastic if one heats it up high enough. When plastic is heated, it loses its rigidity and softens. Nonetheless, this is dependent upon the plastic variety employed and the plastic melting temperature. When heated, some plastics become pliable, while others melt completely. The melting point is the temperature at which a polymer begins to show evidence of a phase transition from ordered to disordered as a result of heating.
The well-known polystyrene foam is made from polystyrene (PS), a strong polymer. Since a high melting point is not necessary, this plastic melts at temperatures of about 90 degrees Celsius.
The answer is very simple. It starts with finding a company that can provide high quality parts while enabling low-cost injection molding manufacturing. Sungplastic achieves cost efficiency by selecting appropriate plastic raw materials, mold steel, and introducing injection molding automation. These methods provide us with complete control over a low-cost injection molding process, ensuring that every part manufactured is of exceptional quality.
Instead, they should combine a lower melt temperature with a higher mold temperature. This will likely result in the creation of a component that has superior final qualities and a shorter cycle time, which will ultimately enhance part quality and decrease costs.
The injection molding process, though sophisticated and extensively used for manufacturing parts with complex geometries, can …
An individual can get flexible polymer polyethylene (PE) in two major forms, low-density polyethylene (LDPE) and high-density polyethylene (HDPE). This plastic softens and melts at higher temperatures. The melting point of LDPE is 105 degrees Celsius, while that of HDPE is 125 degrees Celsius. Packaging films, bags, and sheets are just some of the many products that benefit from polyethylene’s versatility.
Related Articles:How Much does Injection Molding Cost?Reduce Injection Molding Cost – Adjust Machine Settings to Maximize EfficiencyUnderstanding Plastic Injection Mold Cost
Higher model temperatures result in lower levels of molded in-stress and higher impact strength, fatigue performance, and stress-crack resistance in amorphous materials like polycarbonate and ABS.
Nylon is a common name for polyamide (PA), which is another name for the material. The melting point of polyamides is around 200 degrees Celsius, which is quite high. The only real drawback of polyamide is that it degrades in the presence of water. The fabric-like qualities of polyamide make it a popular choice for usage in the textile industry, where it is widely employed in the production of apparel.
It is crucial to have a solid understanding of how the temperature of the mold and the temperature of the melting work together to produce the final part qualities. In the majority of situations, the most optimal performance can be achieved by combining a lower melt temperature with a higher mold temperature.
Cost estimation and control in low-cost injection molding involve a thorough analysis of various factors throughout the production process. By estimating and controlling costs at each stage of the injection molding process, we can optimize production efficiency, reduce waste, and offer low-cost injection molding solutions without compromising on quality. Continuous monitoring and improvement are essential to achieving and maintaining cost-effectiveness in the long run. Here’s a breakdown of how costs are estimated and controlled for low-cost injection molding:
The melting temperature of polypropylene (PP) is 165 degrees Celsius higher than that of high-density polyethylene (HDPE) plastic (which is 130 degrees Celsius). When exposed to colder temperatures, polypropylene plastic begins to degrade more quickly. Therefore, it is used for things like coffee mugs, plastic tableware, and sturdy home furnishings.
Mold steel is a critical component of injection molds and has a direct impact on cost and production quality. Here are some common mold steel materials and their relative prices:
Plastic Mold Manufacturing Plastic Injection MoldingRapid PrototypingCNC MachiningSheet Metal StampingPressure Die CastingSilicone & Rubber PartsSurface Finishing
Seasky Medical serves you with medical injection molding solutions from design to tooling to material selection and manufacturing. Contact our specialized team and solve your problem now.
Now, these plastic molders are compelled to lower the temperature of the mold in order to recoup the productivity that was lost as a result of lengthier cooling cycles necessary by higher melt temperatures. This is done in order to regain the productivity that was lost. Due to the high melt temperature compared to the low mold temperature, the characteristics of the component are frequently impaired, leading to an unstable part.
The mentioned plastic melting point and plastic melting temperature chart are correct but should be used as a reference. Talking to the raw materials provider or the concerned medical molding company is the best bet for maximizing production output.
Seasky Medical serves you with medical injection molding solutions from design to tooling to material selection and manufacturing. Contact our specialized team and solve your problem now.
The choice of mold steel depends on the characteristics of the desired product, the life of the mold and production requirements. High-quality tool steel is more expensive, but it can provide longer service life and better forming quality, which can reduce production costs in the long run and meet the needs of low-cost injection molding. During the mold design phase, manufacturers need to carefully weigh material selection to balance cost and performance.
Sungplastic is a plastic product manufacturer with rich experience in injection molding. According to the different product development requirements, we flexibly adjust the manufacturing process to achieve high quality, high efficiency and more economical.
People tend to dismiss information about the boiling point of plastic and mold temperatures as meaningless digits on a screen, yet knowing the proper temperatures is crucial. Injection molding isn’t as simple as it seems because the molding circumstances have a huge impact on the end product’s strength, durability, and visual appeal. Differentiating between process conditions and the setpoints used to exert control over them is essential. The material’s true temperature as it leaves the nozzle and enters the mold is known as its melt temperature.
Mold temperature becomes critical in determining the degree of crystallinity in a polymer when working with semi-crystalline materials. As a result, this has implications for a wide range of performance characteristics, including fatigue resistance, wear resistance, creep resistance, and dimensional stability at elevated temperatures.
We offer a variety of manufacturing services: Rapid Prototyping, Tool Making, Injection Molding, Product Design and Development, CNC Machining and Metal Stamping. You can choose from a variety of plastics, silicone rubber, or metal for your product. Regardless of mass production or small batch customization, Sungplastic has always been committed to providing assured, efficient and more economical one-stop processing services for your projects.
However, the majority of plastic injection molders are just people who push buttons, and they lack the technical skills necessary to execute and manage these two essential components of plastic molding. They believe that increasing the temperature of the melt is the only way to successfully lower the resin’s viscosity.
Injection molding is a widely used manufacturing process in which molten plastic material is injected under high pressure into a mold cavity. Once the plastic has cooled and solidified, the mold is opened to reveal the final product. This versatile technology can be used to produce a wide variety of plastic parts and products, from small complex components to large complex items. Injection molding is favored for its efficiency, precision and ability to create complex geometries. Due to its ability to mass-produce high-quality, cost-effective, and consistent plastic parts, it is used in a variety of industries, including automotive, electronics, medical devices, and consumer goods.
However, initial investment costs for setting up automated systems and training personnel can be significant. Therefore, a careful analysis of the production volume, part complexity, and expected long-term benefits should be conducted to determine the feasibility of automation in reducing overall costs in injection molding operations and meeting the needs of low-cost injection molding.
Plastic injection molding is a complex manufacturing process that demands expertise at every stage to ensure top-notch results. Cutting corners at any point in the process can result in costly repercussions. Therefore, when seeking affordable injection molding solutions, it’s crucial to partner with a company that possesses the necessary experience and knowledge.
GETTING A QUOTE WITH LK-MOULD IS FREE AND SIMPLE.
FIND MORE OF OUR SERVICES:
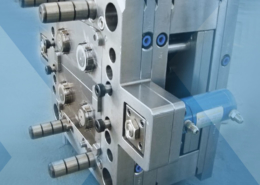
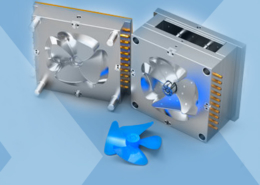
Plastic Molding

Rapid Prototyping
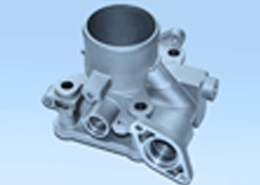
Pressure Die Casting
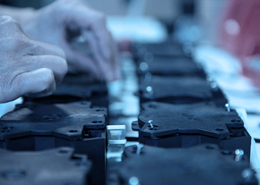
Parts Assembly
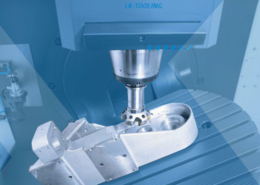