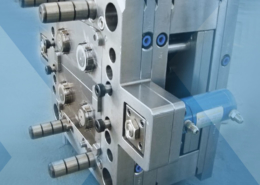
Moldable Plastic Sheets - 3 Sheets - heat plastic to mold
Author:gly Date: 2024-10-15
We are here to help, whether you have 30 years of experience and know exactly what you need or are just starting out on your 3d printing experience and need some advice. Either way we have capability to deliver what you need, when you need it.
What if I don't want so many parts though? Then tooling must be considered. Tooling is traditionally expensive, and takes a long time to produce. That said it is the ‘enabler’ that permits the benefits identified earlier and the good news is, these days there are numerous alternative tooling options that can be considered to make the costs less inhibitive.
We are product developers. We use our passion and experience to build manufacturing partnerships that our customers can trust. With UK onsite toolmaking and injection moulding we are always here to support your requirements, be they low volume fast turnaround development parts or ‘make to stock’ with a scheduled call off.
This typically includes installing the tool into the moulding press, drying and loading the specified material/colour, setting up the moulding conditions and running initial QA samples for approval. Then at the end of the moulding run purging out any residual material, applying any protection to the tooling before stripping it out of the press and returning it to stores.
1. A pallet injection mold comprises a moving part and a fixing part. The moving part is provided with a ejection plate, and the ejection plate has ejection rods through the moving part. The moving part and the fixing part are respectively provided with a conflicting first switching module and the second switching module, the cross section of the first switching module and the second switching module are square. The first switching module and the second switching module four same sides are respectively provided with a forming block, The moving part and the fixing part have a first fixing groove and a second fixing groove for all the first switching module and the second switching module.
2. The side of the first fixing groove is sliding connected with a first sliding rod, and the center of the all changing module is rotating connected with the first sliding rod, and the first sliding rod is connected with the ejection plate
A wide variety of tools could be produced for £5,000 – £7,000, although large complex items can see this exceed £30,000. The only way to accurately quantify this is to obtain a quotation against the specific data involved.
The pallet is a kind of plastic product that people use to carry goods in daily life and the factory to carry products. The pallet is mainly made by injection molding of the pallet injection mold, and the pallet needs to adapt to different handling conditions, and the structure will usually change slightly. In particular, there are many changes in the reinforcement ribs of the pallet. At present, people will re-make a mold according to each change, resulting in a greatly increased processing cost, and the pallet injection mold is relatively big size, leading to replacement the mold is very difficult.
All will give different results. However, whichever option is employed it can be seen that there is a dramatic difference between:
Costs are driven by part complexity, size and time. It is unusual to see any mould tool offered for less than £2,000 and in this case the parts may well carry a substantial premium.
We are specialists in low volumes, so if you are considering injection moulding for your project but are unsure of the potential price point for your quantities, please contact us. We will be happy to advise.
Colours can require masterbatch or compounding and add further to the costs especially if universal grades cannot be used.
We are here to help, whether you have 30 years of experience and know exactly what you need or are just starting out on your 3d printing experience and need some advice. Either way we have capability to deliver what you need, when you need it.
Press size is a function of tonnage (force required to hold the mould tool closed during the injection cycle) and shot weight (amount of plastic delivered to the mould per cycle). The larger the press the more expensive it is both in terms of depreciation and power to operate.
Most definitely, yes! The ability to have prototypes in the production intent material is a huge driver. Nowadays we get involved in moulding as few as 2 parts, we have multiple tooling options at our disposal both to advance prototyping and also tackle low volume production.
Quoted times will only apply to T1 (first trial), so any tweaks will increase the lead-time. More typical timescales would be around 2 – 4 weeks.
5. An auxiliary ejector pin is arranged on the ejection plate, and the auxiliary ejector pin runs through the conflict plate and the first sliding rod in turn.
Whether a press is run manned or unmanned is more often dictated by the tooling rather than the press. With small batches, lose inserts may be used requiring an operator to load and unload the inserts every cycle. Alternatively there may be a post moulding operation that is completed by the operator (or robotic alternative) whilst running the mould – this could be printing or packing.
Tooling costs will vary dramatically depending on the specification. It is not just the tool cost that is important, but matching it to the quantities required and deciding how to account for the cost. Getting this right and aligned to the production quantities is vital.
This process is obviously independent of how many parts are produced and often quoted as a ‘setup’ charge, especially if dealing with low volumes. It can take anything from an hour to half a day depending on a number of factors like the size of the tool, configuration, what material/colour options are being changed and inspection/dimensional requirements.
Moulding is ideal for these requirements; with cycle times measured in seconds and part costs measured in pence allowing for the product pricing that we all take for granted. Add to this flexibility, potential materials stretching from soft elastomerics to metal replacement polymers and the scope begins to become apparent.
Development Tooling and moulding parts can be produced in a few days, but this will be subject to a string of conditions relating to the geometry, material, finishes etc.
We are surrounded by injection moulded parts in every facet of our lives, from light switches to the electric kettles we use to the keys on our keyboards. The one thing all these items have in common is that they are produced in high numbers, frequently hundreds of thousands upwards.
Material costs vary substantially from one material to another, and also depend heavily on the quantity being procured. For example it is quite possible to see a 10:1 difference in price between buying a single 25kg sack and 3 tonnes of material.
Additional information on the different types of tooling and options to reduce both the cost and associated lead-time for low quantities can be found here.
4. A conflict plate is arranged on one side of the ejection plate near the moving mold. The first sliding rod is fixably connected to the side of the conflict plate, and the conflict plate and the thimble cladding plate are connected by an elastic part.
If you have any new mould projects, welcome to contact by whatsapp or mob: 8613867644770. We make not only pallet mould, but also more other injection moulds with a series a advanced processing, numerical control equipment, a set of advanced CAD/CAE/CAM technology, and in the field of daily necessities mold has a set of unique experience.
3. The side of the second fixed groove is sliding connected with a second sliding rod, and the center of the second switching module is rotating connected with the second sliding rod, and the second sliding rod is provided with a locking piece.
GETTING A QUOTE WITH LK-MOULD IS FREE AND SIMPLE.
FIND MORE OF OUR SERVICES:
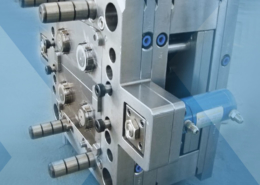
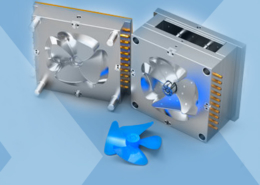
Plastic Molding

Rapid Prototyping
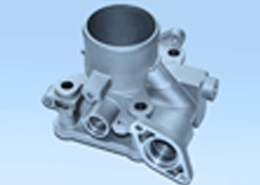
Pressure Die Casting
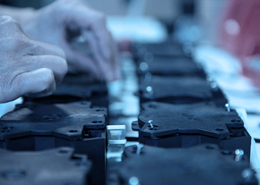
Parts Assembly
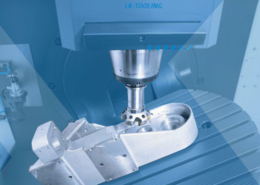