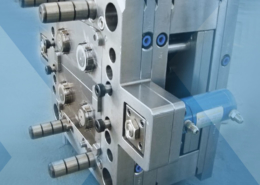
Mini plastic injection molding machine-Moiron - mini injection molding
Author:gly Date: 2024-10-15
If you have a sales inquiry, an RFQ / RFP or if you have any questions, please fill out the form below or email us directly at contactus@sussexim.com
Mold manufacturer location: This was also mentioned while researching how mold size may affect your total injection molding expenses. To have your mold wherever it needs to go, an off-site plastic injection mold maker will charge you extra for shipping and handling.
Material cost is determined by the design of a product, the material utilized, and the quantity of material needed to complete the injection molding process.
3D printers can manufacture basic low volume 3D printed molds for as cheap as $100. A metal mold for a mid-volume service life of 1,000-5,000 units costs between $2,000 and $5,000. Mold costs can range from $5,000 to $100,000 for molds with more complicated shapes and prepared for higher production runs of 10,000+ pieces.
Depending on the needs of the finished products, a broad range of polymers can be utilized for injection molding. The cost involved when you buy plastic injection mold materials varies depending on the material selected. Thermoplastic pellets range in price from $1 to $5 per kilogram.
Sussex IM is a family owned, custom injection molder centrally located in Sussex, Wisconsin. Proud of our Midwestern roots we pride ourselves on providing solutions to meet our customers needs. We look forward to hearing from you.
With the combination of different properties into one part, two-shot injection molding also provides value through improved aesthetics, functionality and quality. While any market will enjoy the benefits of combining materials to improve part integrity and greater visual appeal, as this process improves color and eliminates painting in secondary operations, the medical market has several applications where this manufacturing process is unmatched.
The necessary double injection is carried out on one machine, built and programmed to perform two injections in one cycle. While the process can also occur with two or more molds in multiple injection molding machines, using one mold and one injection molding machine ensures reduced handling and guaranteed cleanliness. The single press method is also the lowest cost.
To a certain degree, asking for the costs of plastic injection molds cost is similar to questioning how much a car costs. Is your mold going to be a Pinto or a Porsche? Also, keep in mind that the cost of a mold is only the beginning. To calculate complete plastic injection molding costs for any projects, you must also include raw material, operating, and maintenance expenses in the future. These costs are a result of the aforementioned contributing factors.
Two-shot, or multi-shot injection molding, is a highly efficient manufacturing process in which molded parts from two or more different materials are combined to build a single product.
At Sussex IM, we strive to solve our customers’ problems in the most efficient way possible. Backed by our proven injection molding expertise, one of the ways that we deliver solutions is through two-shot or multi-shot injection molding. As your injection molding experts, Sussex IM is always looking for new ways to address our customers’ needs. To maintain this responsibility, we have continued to expand our medical injection molding capabilities with the addition of our new Class 8 clean room.
There are numerous benefits of multi-shot injection molding. Providing the simplest and most cost-effective way to produce parts with multiple materials, as the process only requires one machine cycle, multi-shot injection molding delivers reduced costs and needs for labor. The efficient process will also produce higher output levels compared to other manufacturing processes.
If a plastic injection mold factory has the tools and materials, creating molds in-house may be the most cost-effective option if the technical expertise is also accessible. If the tools required for injection molding are not easily accessible, outsourcing lowers the cost of developing a mold.
Material selection is always complicated, and given the recent shortages and price increases, finding your first choice can be nearly impossible, meaning material replacement is a growing need. At Sussex IM, our knowledgeable team is happy to help guide you through the material selection process.
With small desktop injection molding equipment and 3D printed molds, creating modest volumes of components with injection molding is the most cost-effective. Small-scale automated injection molding machines are viable options for medium-series manufacturing of small components.Large industrial injection molding machines can range in price from $50,000 to more than $200,000. These machines also have more strict facility requirements and the need for specialized staff for operations, upkeep, and monitoring. As a result, although injection molding is a core competency, most businesses outsource mass manufacturing to service providers and contract manufacturers, with equipment expenses included in the service prices.
Beyond the ability to seamlessly create multi-color or multi-material parts, two-shot injection molding also is a flexible process that allows for added creativity and complexity in part design, opening up part complexity possibilities. The unique capabilities of two-shot injection molding are especially beneficial for the medical market as medical device designs continue to advance and have become increasingly intricate.
When it comes to injection molding prices, basic plastic injection molds might range from $3,000 to $6,000. A big, more sophisticated high-production, cross-cavity mold can cost between $25,000 and $50,000 or more. Although it may seem obvious, several factors contribute to the cost of injection molding.
For example, a medical device housing would require a material that is both durable and aesthetically pleasing. Two-shot injection molding can also offer an end-product that features a rigid plastic housing with a soft-touch grip.
This versatile manufacturing process produces complicated molded parts that may have different colors, components or materials. Usually, those factors are limited to two different types, but with customization of the molding machine and mold construction, a part could utilize up to three materials. Additionally, the use of multiple injection molding machines can create an even larger combination of materials.
If you have a sales inquiry, an RFQ / RFP or if you have any questions, please fill out the form below or email us directly at contactus@sussexim.com
Creating more sophisticated molds necessitates technical knowledge. As a result, companies typically outsource specific aspects of injection molding, for instance, mold design and production.
When examining the end-use, it is vital to understand if the device will require higher durability, protecting against being exposed to fluctuating temperatures and the resilience required. For medical applications, considerations of FDA regulations the product will need to meet, especially if the device will be inserted into the human body or in contact with bodily fluids, will be critical.
Typically, the cost of the mold, also referred to as the tooling cost, is the major cost driver in injection molding. Let’s take a look at some of the elements that influence the price of an injection mold.
As the case with any manufacturing process, material selection is a critical part. In multi-shot injection molding, the selection process becomes even more vital as the resin not only has to be a fit for the end-use application, but the materials have to be a fit, chemically, with each other. Otherwise, bonding will not occur. Another way to overcome this challenge is through part design, mechanically bonding the two materials via internal channels and interlocking features. Typically, to aid in this decision-making process, a material compatibility chart is available to determine which resins may work together for this particular kind of injection molding.
Injection molding, the major cost driver is generally mold or tooling expenses. Molds for injection molding are typically created in one of three ways:
The simple answer is that plastic injection molds range in price from $100 for a 3D printed injection mold to $100,000 plus for a sophisticated multi-cavity steel mold for greater manufacturing loads, which is typically the most important fixed start-up cost in injection molding. However, because these expenses are spread across hundreds or thousands of components, injection molding is a suitable method for mass-producing plastic parts at a low cost.
To enhance all of our injection molding expertise, Sussex IM has complete service offerings including, design for manufacture, dedicated 3PL capabilities and inventory management to round out our full-solutions service. From start to finish, we are the comprehensive partner to ensure success – that’s the Sussex Solution.
For injection molding, special-purpose equipment ranging from tiny personal molding machines that enterprises may use in-house to big industrial injection molding equipment primarily handled by providers, contractors, and major manufacturers is utilized.
With the recent increased demand for medical products, multi-shot injection molding is as popular as ever. The multi-shot injection molding manufacturing technique offers several favorable qualities that appeal to the medical market including, the opportunity for increased sterilization, molding precision and cycle time.
If you have a medical device application, multi-shot injection molding can benefit your needs and the advantages this manufacturing capability provides.
At Sussex IM, we recognize the nuances necessary for medical injection molding. To continuously serve the increased demand for medical manufacturing and new product development, we have strengthened our capabilities to support medical injection molding with our ISO Class 8 clean room.
GETTING A QUOTE WITH LK-MOULD IS FREE AND SIMPLE.
FIND MORE OF OUR SERVICES:
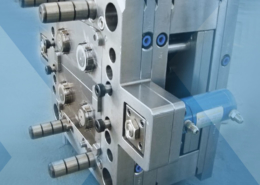
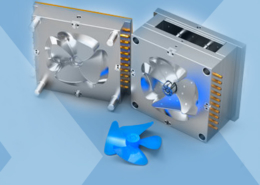
Plastic Molding

Rapid Prototyping
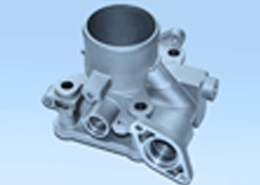
Pressure Die Casting
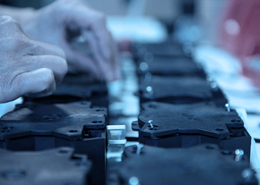
Parts Assembly
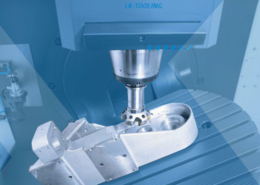