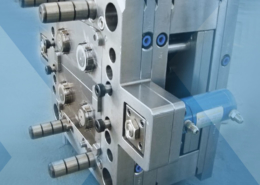
MGS Mfg. Group - mgs injection molding
Author:gly Date: 2024-10-15
What Thermoset Molding Provides – With excellent chemical resistance and stability, thermoset product assemblies and internal components will not corrode, nor be affected physically when exposed to harsh chemicals, fluids, or other challenging environments.
The first substrate is metal, then rigid plastic will be molded around the substrate. This is often used for insert installing,which also called inserts over-molding.
With decades of thermoset molding experience, Woodland Plastics specializes in injection molding of thermoset materials or composites including Phenolic, Bulk Molding Compound (BMC), Epoxy, and DAP with injection press tonnage from 80-500T for both large and small components. Our customers rely on Woodland Plastics as a preferred thermoset molder within a variety of industries and end products. Woodland Plastics molds parts for the Appliance, Automotive, Electrical, Energy, and Industrial markets that require components and assemblies to withstand aggressive and challenging environments. The environments suitable for thermosets include applications experiencing high and intermittent operating temperatures, electrical current, corrosive environments, outdoor and UV exposure, and applications exposed or submerged in chemicals, oils, and/or automotive fluids. Woodland Plastics has offers thermoset molding processes of injection, injection-compression hybrid, and insert molding.
What Thermoset Molding Provides – Consolidation of multiple parts of an assembly. Elimination of costly secondary machining or painting operations.
Injection molding - For low-volume production and mass production projects, it has obvious benefits on time and cost, which can bring the products to the market in a short time.
Why Partner with Woodland Plastics – Woodland Plastics offers integrated manufacturing solutions with support in engineering, tooling, and material selection to efficiently convert customers’ existing metal components or product assemblies to thermoset to drive product performance and lower manufacturing costs.
Ph: 630.543.1144 | Fax: 630.543.1525 info@woodlandplastics.com
Whether a product assembly is completely new to the market, or an existing project exploring a material conversion from a metal or thermoplastic to thermoset; Woodland offers thermoset molding capabilities to alleviate product pain points, reduce manufacturing costs, consolidate the number of parts in an assembly, and improve overall product performance. Implementing molded thermosets into a product assembly protects internal components and product assemblies from degradation or failure, providing an assurance of safe handling and user operability.
●Rubber and plastic overmolding - Different with plastic over plastic, the second mold plastic rubber, not rigid plastic. It is not only can combine different colored parts, also can fixing of rubber grips onto the stiff handle, which can add the flexibility to rigid parts, help to realized the functional of the parts.
Vacuum Casting - When the product is in the premise research and development and testing stage, the number of required is not large, vacuum casting is the most affordable way to do over-molding, which is suitable for prototyping projects under 100 pieces.
Why Partner with Woodland Plastics – Woodland assists with customer light-weighting efforts and leverages approved suppliers for tooling and material selection, keeping overall manufacturing costs competitive against metallic or thermoplastic components.
● Plastic Over Plastic - The substrate is rigid plastic. Then another rigid plastic is molded onto or around the substrate. In this way, it can help to improve the ergonomics of a product, manufacture the product in different colors and resins.
Customer Pain Point – Product application may be exposed to oils, automotive fluids, or even rainwater run-off including salts or other chemicals.
Why Partner with Woodland Plastics – Woodland Plastics has decades of experience molding for a variety of customer and product end-markets including for product applications exposed to oils, fluids, salts, and moisture.
Customer Pain Point – Components or product assemblies may degrade or disfigure while exposed to high heat and high operating temperatures during application use.
What Thermoset Molding Provides – Heat resistance, temperature deflection, & dimensional stability up to 500° Fahrenheit and above.
Compared with insert molding, the second plastic changed from rigid plastic to rubber. The first metal part can be produced by formed, CNC machining, die casting.
The over-molding process produces chemically bonded parts made using various materials. Depending on the materials, we can make the following types of over-molding:
For questions on Woodland Plastics’ thermoset molding capabilities, please contact us via email at sales@woodlandplastics.com or reach us via phone at (630)-543-1144.
Why Partner with Woodland Plastics – With extensive thermoset molding experience, Woodland Plastics manufactures heat-stable components that remain dimensionally stable even within high operating temperatures.
Over-molding is a unique molding process that can combine multiple materials into a single part or product. It is commonly used to produce consumer electronics and industry equipments. SuNPe provides plastic overmold plastic, plastic overmold metal, rubber overmold plastic services for prototyping and production.
What Thermoset Molding Provides – Lowers component or product assembly weight over metallic applications without compromising product performance.
GETTING A QUOTE WITH LK-MOULD IS FREE AND SIMPLE.
FIND MORE OF OUR SERVICES:
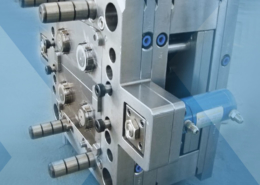
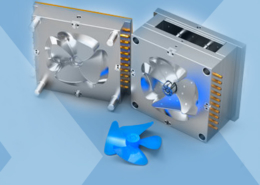
Plastic Molding

Rapid Prototyping
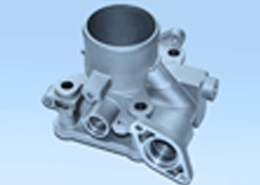
Pressure Die Casting
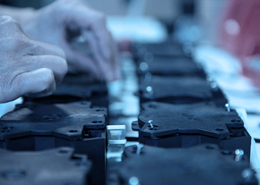
Parts Assembly
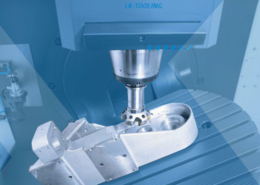