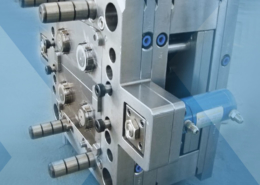
Medium to Large Plastic Injection Molds - large plastic molds
Author:gly Date: 2024-10-15
Time to market – Sometimes it pays to get your product out as quickly as possible. A short run can help to ensure you reach your customers before a competitor.
If you’re new to two-shot plastic injection molding, you might think it is more complex, more expensive, or more time consuming than other plastic molding processes. Taken alone, those may be true, but two-shot also creates considerable functionality and cost savings.
The first is similar to traditional injection molding: A shot of resin is injected into a mold and cooled to form a solid part. In the second phase, the just-molded part is transferred to a second mold via a rotating platen or a robotic arm, and receives the second shot of resin – in, through or around certain parts of the first molded part, depending on the design. The two plastic resins then form a molecular bond and the multi-resin molded part is cooled and ejected.
Injection molding is a manufacturing technique that has been around for decades and it still remains the most popular method of producing plastic products today. In terms of accuracy, efficiency, or cost – no other process is as versatile or cost-effective. Even as you’re reading this, you’re likely surrounded by-products created via plastic injection molding.
Do you need design-for-manufacturing (DFM) assistance? Or, are you ready for production? We have a full suite of services to offer and a lifetime mold guarantee.
Two-shot injection molding allows for the creation of complex mold designs that incorporate multiple materials for functionality that cannot be achieved through other molding processes.
Two-shot injection molding is the ideal plastic molding process for complex, multi-color, and multi-material plastic products, especially in high-volume production scenarios.
If you’ve got manufacturing needs but aren’t sure how to proceed, Rex Plastics can help. Whether it’s a short run or full scale, we make sure you get the right process for your product. With decades of experience and cutting-edge technical design, Rex Plastics is a trusted leader in plastic injection molding. If injection molding sounds right for you, drop us a line; we can answer all your questions and help set you up on the path to success.
From consumer goods to construction, two-shot molded components are used in nearly every industry, but are most commonly found in applications requiring high functionality.
While 10,000 may seem like a lot, in the world of injection molding it’s actually fairly limited. If your project requires fewer than 10,000 parts, short-run injection molding could be a perfect solution.
You can rest assured you’re getting the quality you need at a competitive market price when you choose us for your two-shot molding solutions.
Plastics are among the most inexpensive materials out there. They’re also durable, pliable, and versatile enough that you can produce millions of parts with just one injection mold! And because plastic has such high yield rates for producing consistent products – usually under 1% rejection rate- this process is ideal if consistency matters to your brand or project.
Two-shot molding allows multiple components to be molded with a single tool, reducing the amount of labor needed to run your parts and eliminating the need to weld or join components after the molding process.
Accessibility – The production capabilities of injection molding offer huge advantages to companies that can afford it. Short runs make these benefits accessible to small and medium-sized businesses.
It requires high levels of technical expertise and attention to detail, and even the smallest mistakes can cost big money, especially in high-volume production scenarios. That’s why it’s critical to find a highly capable supplier. Look for excellent supplier quality scorecards, defined processes to mitigate against flash, flow lines, and short-shots, and contingency plans to expand capacity as your business and your two-shot molding needs grow. Once you find a supplier, involve them early on in the design phase of your part. They can identify potential problem areas and engineer value into your product.
When tolerances and on-time-delivery are important, OEMs choose us for two-shot injection molded parts. We’re more than a manufacturer. We’re problem-solvers, working both with customers and vendors to build functionality, safety, and efficiency into everything we produce.
Two-shot injection molding reduces the number of components in a finished assembly, eliminating an average of $40K in development, engineering, and validation costs associated with each additional part number.
When a major automotive OEM failed a side impact crash test, they relied on their Tier 1 supplier and us to develop a two-shot injection molding solution to reinforce the vehicle’s frame.
What’s the best way to make sure that your injection molding is cost-effective, efficient, and consistent? Short-run molding! This specialized process involves using molds made from less expensive aluminum or steel. You can expect many of the same benefits of injection molding when producing small runs without sacrificing quality or performance; it’s an easy choice if you’re looking for value on a budget and need fewer than 10,000 units.
Maybe you’ve been turned off by a manufacturer’s quality or delivery issues? We’re here to tell you that you deserve better!
Iteration – A short run can be an invaluable step between prototype and mass production. Used as a sort of test run, short runs can help a product develop as it begins to turn a profit, and give you the opportunity to make changes to your product while it is still relatively easy.
Compared to other methods of plastic molding, two-shot is ultimately a more cost-efficient way of producing an assembly with multiple components. Here’s why:
With today’s technology, it’s never been easier to create quality, durable products in such a short amount of time. To learn more about injection molding, check out our introductory blog here.
The customer is a Tier 1 international automotive supplier with an emphasis on innovation and technology. The company’s products include automotive exteriors, closures, roof systems, and seating – to name a few.
Two-shot is carried out within a single tool, allowing for lower tolerances than other molding processes, a high level of accuracy and repeat-ability, and reduced scrap rates.
The injection molding process is complex, and each product requires a different type of mold. Generally, molds used for high volume production are made from hardened steel, a tough and durable material perfectly suited for the pressure and temperature extremes involved in injection molding. Just one of these molds can be used to create hundreds of millions of parts over its lifetime. Because of this, the mold is usually the most expensive part of your production run. But what if you don’t need millions or even hundreds of thousands of parts? What if you need 10,000 or fewer?
GETTING A QUOTE WITH LK-MOULD IS FREE AND SIMPLE.
FIND MORE OF OUR SERVICES:
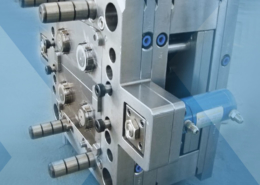
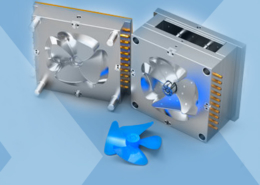
Plastic Molding

Rapid Prototyping
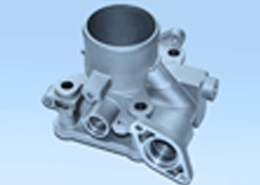
Pressure Die Casting
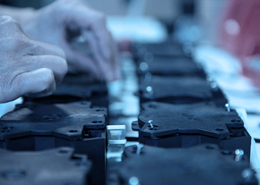
Parts Assembly
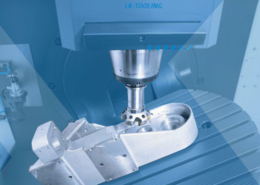