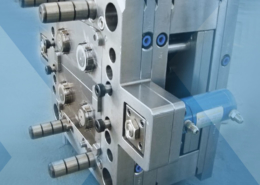
Medical Injection Molding | Thogus | Family-Owned High - medical plastic injecti
Author:gly Date: 2024-10-15
Sustainability is also a key focus, with efforts to develop eco-friendly practices and materials. The use of recycled PET (rPET) in injection molding is gaining traction, reducing the environmental impact of plastic production. Additionally, advancements in biodegradable additives and bio-based PET are being explored to further enhance the sustainability of PET products.
After the molten PET is injected into the mold, it begins to cool and solidify. Controlled cooling is essential to prevent defects such as warping or shrinkage. The cooling process usually involves circulating chilled water or other cooling agents through the mold to maintain a consistent temperature. This step is critical for achieving the desired mechanical properties and dimensional accuracy of the final product.
Before PET resin can be used in injection molding, it must be properly prepared. This involves pre-drying the PET resin to remove any moisture content. Moisture can cause hydrolytic degradation during the molding process, leading to weak and brittle parts. Therefore, it is crucial to dry the PET resin at a temperature of around 160°C to 180°C for several hours.
The solid frame construction with balanced power flows is easily maintained thanks to the small number of moving parts. The use of ecodrive offers the benefits of low heat impact thus keeping heat-related air turbulence to a minimum. This makes the machine perfect for cleanroom applications.
Thanks to all electric drive technology and best of class efficiency. And thanks to a number of further energy saving solutions, such as intelligent energy recuperation. This recuperates energy generated by braking movements and feeds it directly back into the power grid.
The tie-bar-less ENGEL victory covers the clamping force range from 280 to 5000 kN. In fact, the range of applications is considerably broader, as the moulded part to be produced is not limited by the clamping force but by the platen size. Large mould fixing platens and the wide delivery chute of the ENGEL victory guarantee low machine investments, because with the ENGEL victory a machine with a lower clamping force will do the job just as well. Particularly when using large and bulky moulds, substantially lower investments are required for machines.
Injection molding with PET plastic presents several challenges, primarily related to moisture content and melt viscosity. If the PET resin is not adequately dried, the presence of moisture can lead to hydrolysis, resulting in weakened molecular chains and compromised product strength. To address this, maintaining strict control over the drying process and using dehumidifying dryers is essential.
Another challenge is achieving the right melt viscosity. PET has a relatively high melting point, and maintaining a consistent temperature is crucial to ensure a uniform melt flow. Advanced temperature control systems and precision equipment are necessary to maintain the optimal processing conditions.
No matter whether the elastomers are of the thermosetting or thermoplastic type, ENGEL offers just the right machine and processing technology – ENGEL elast and ENGEL LIM, two series of injection moulding machines for flexible materials.
The Machine Concept The ENGEL e-victory range is characterised by a high-precision, servo-electrical injection unit and a tie bar-less, hydraulic clamping unit. All hydraulic movements are powered by the new ecodrive drive unit*. Of course, the e-victory offers all the benefits of the ENGEL victory range. That means: excellent platen parallelism thanks to the patented Flex-Link, CC200 control unit with an intuitively designed touch-screen, and all the benefits of the tie bar-less design. That means: plenty of space for the mould and automation components. (* as of 1,300 kN on request)
Energy saving with tie bar-less benefits Hybrid machine with hydraulic, tie bar-less clamping unit and electrical injection unit.
Once the PET resin is thoroughly dried, it is fed into the injection molding machine. The machine's barrel is heated to a temperature between 250°C and 280°C, melting the PET resin. The molten PET is then injected into the mold cavity under high pressure, typically ranging from 10,000 to 30,000 psi. The high pressure ensures that the molten PET fills all the intricate details of the mold.
The machine‘s impressive energy efficiency translates into cash savings for you. Shot for shot. This helps you keep your ongoing operative costs down to an amazingly low level. This is the intelligent way to save. This is: the ENGEL e-mac.
Polyethylene Terephthalate (PET) plastic is one of the most widely used materials in the manufacturing industry. Its versatility, durability, and recyclability make it an ideal choice for various applications, including packaging, textiles, and more. One of the primary methods of shaping PET plastic into useful products is through injection molding. This blog delves into the process of using PET plastic for injection molding, highlighting each step, the challenges faced, and the future trends in the industry.
Polyethylene Terephthalate (PET) is a type of polyester that is known for its excellent mechanical properties, including strength, toughness, and clarity. It is commonly used in the production of beverage bottles, food containers, and synthetic fibers. PET plastic is favored for its high resistance to impact and its ability to form strong, lightweight products.
Tie-bar-less technology means unbeatable mould dimensions. The barrier-free mould area can accommodate large moulds easily, even with bulky core-pulls. Generously dimensioned mould fixing platens can be utilised to their limits (and often beyond) and even tall moulds can be changed quickly. The robust, low friction design also reduces maintenance costs. ENGEL’s patented Flex-Link system and the standard platen parallelism setting ensure maximum platen parallelism whilst minimising mould wear.
Injection Moulding Machinery – from 25 tonne to 5500 tonne clamp force – Hydraulic, Hybrid, Fully Electric, Automation …. all from a single source.
Team work is so often the key to success. This applies not just to co-operation between human beings but also to the interaction of different materials. metal and plastic composites are often of great importance to the optimum performance of technical components and equipment. Their quantity and complexity increase with every new generation of equipment. The same applies to plug/cable combinations. Sensors are increasingly important components in this technology. With its series of insert machines, ENGEL can supply the right combination for all applications.
We had a vision. A machine – compact like no other, equipped with state-of-the-art technology and with every single detail optimised for maximum performance, to guarantee our customers a machine that is as economical as it is precise. This was how the e-max came to be:
Injection molding is a manufacturing process used to produce parts by injecting molten material into a mold. It is highly efficient and capable of producing large volumes of high-quality products with complex shapes. The process involves the following basic principles:
Plastics are made-to-measure materials. Thermoplastics are all-rounders for a wide range of applications, while elastomers are the specialists. Such specific properties as extreme flexibility, a prerequisite for sealing, soundproofing and shockabsorbing functions, open up a whole new world of possibilities for the design and development of innovative products.
Once the PET has cooled and solidified, the mold is opened, and the finished product is ejected. The ejection system, which may include ejector pins or plates, gently pushes the part out of the mold. After ejection, the product may undergo additional post-processing steps such as trimming, polishing, or coating to ensure it meets quality standards. Quality control checks are also performed to detect any defects or inconsistencies.
Injection molding is widely used in the production of various products, including automotive parts, household goods, medical devices, and packaging materials. Its advantages include high precision, repeatability, and the ability to produce complex geometries.
Electric injection moulding machines are the modern alternative to hydraulically driven machines. For 10 years they have been a fixed component of ENGEL’s delivery program. The servo motor drive technology offers an extraordinary precision level with low energy consumption – and thus opens an until now unexplored business potential.
Three different injection unit systems are available, depending on the actual application: the screw unit for wide, universal application, the plunger unit for the processing of highly filled LSR and the double plunger unit for large shot volumes of up to 6,000 cm3.
Mold maintenance and quality are also vital. Any imperfections in the mold can result in defects in the final product. Regular mold inspections, cleaning, and maintenance are crucial to ensure consistent quality and prolong the mold's lifespan.
Innovative like any other ENGEL machine. But with a difference. Fully-electric and compact, extremely economical, but still equipped with the critical options that help customers optimise injection moulding.
The universal machine in the small to mid-sized machine range, between 280 and 2,200 kN with hybrid drive concept as a combination of the tried-and-trusted ENGEL victory clamping unit with the ENGEL e-motion series injection units. The ENGEL e-victory is deployed wherever compatibility with an existing range of moulds, efficient mould changing and easy automation are required. The ENGEL e-victory is the best machine for energy-saving production
The in-mould assembly of plastic parts with components (inserts) manufactured from other materials is an important aspect of industrial production. Injection moulding machines with vertical clamping units not only eases the automation of difficult parts handling operations but also creates the prerequisites for automatic in-mould component assembly.
The ENGEL LIM series of machines for the processing of liquid silicone rubber is based on the ENGEL victory series of small and medium-sized machines equipped with tiebarless clamping units. This modular, service-proven technology platform is combined with special-purpose LIM injection units and LSR feeding and metering systems.
Available in three series – ENGEL victory spex, ENGEL victory tech and ENGEL victory combi – the tie-bar-less ENGEL victory is the ideal modular system for cost-effective injection moulding production. In 2009, tie-bar-less technology marked its 20th anniversary: two decades of the technology has supplied 55,000 machines to 10,000 satisfied customers.
We think about your future! Superior technology – superior value. ENGEL e-max. This means state-of-the-art technology. Fully electric – that means low power consumption, maximum precision, fast, highly dynamic and low noise.
New technologies in injection molding, such as multi-component molding and micro-injection molding, are expanding the possibilities for PET applications. These techniques enable the production of more complex and multifunctional parts, catering to the increasing demands of various industries.
Thanks to the advantages of tie-bar-less technology, the ENGEL victory is the ideal machine for technical and thick-section parts.
The field of PET injection molding is continuously evolving, with innovations aimed at improving efficiency, quality, and sustainability. Advances in PET resin formulations have led to materials with enhanced properties, such as improved barrier performance and greater clarity. These innovations allow manufacturers to produce better-performing products while reducing material usage.
Understanding the process of using PET plastic for injection molding is essential for producing high-quality, durable products. From material preparation to post-processing, each step requires careful attention to detail and adherence to best practices. Despite the challenges, ongoing innovations and future trends promise to make PET injection molding more efficient, sustainable, and versatile. As the industry continues to evolve, manufacturers will be better equipped to meet the growing demands for PET products while minimizing their environmental footprint.
Lighter, more precise, faster, more constant and also smaller. The requirements of modern products and their individual parts will always be selective. These requirements demand new technical possibilities. In plastic injection moulding this means: Highest consistency and precision or the best energy efficiency with low emissions. The full electric drive technology in the ENGEL e-motion range offers exactly these advantages.
One of the key advantages of PET is its recyclability. PET can be melted down and reformed multiple times without significant degradation in quality, making it a sustainable choice for many applications. Additionally, PET's resistance to moisture and chemicals makes it suitable for packaging foods and beverages, ensuring that products remain safe and fresh.
Large-capacity injection moulding machines with clamping forces of over 3500 kN have been an important part of the ENGEL range of machines for over 40 years. No matter whether their clamping units operate with toggle clamps or hydraulic pressure pads, ENGEL machines have always been of optimum service to manufacturers of large injection moulded parts. The current duo series, featuring a two-platen design, continues in this tradition and sets new standards in flexibility and performance.
With its the speed series, ENGEL continues its tradition of toggle clamp technology in line with state-of-the-art developments. Systematic re-engineering in conjunction with an efficient hydraulic drive system are the essential basis of this series of high-performance injection moulding machines.
In line with the advancements and future trends in PET injection molding, Wankai is at the forefront of innovation with its High-Brightness PET Resin. This specialized resin is designed to offer superior clarity and brightness, making it ideal for high-quality, aesthetically pleasing products. Wankai's High-Brightness PET Resin not only meets the stringent requirements of modern injection molding but also enhances the overall appearance and performance of the final products. By using advanced formulations and maintaining rigorous quality control, Wankai ensures that their PET resin provides consistent, reliable results, enabling manufacturers to produce top-tier products with enhanced visual appeal and structural integrity.
A machine that combines great performance with amazing precision. All electric. A machine that offers you a huge amount of freedom. Freedom enough to design your individual injection moulding applications with the required degree of flexibility.
For over 40 years, ENGEL has been offering a comprehensive range of machines specially designed for the processing of thermosetting elastomers (rubber compounds)
There are also benefits in terms of automation. Robots and automation equipment have free access to the mould area, which means parts can be removed faster. Between them, the machine and the robots only have small footprints; they are even able to operate efficiently in low-ceilinged halls.
Thanks to the large selection of serial options, the ENGEL e-victory represents a combination of maximum precision and efficiency in plasticising and injection and the most economical, tie bar-less clamping system.
The innovative ENGEL e-mac does not use up too much of your floor space despite offering excellent performance. It is a machine that is extremely frugal. In ongoing operations, because it uses very little energy. But above all in terms of capital outlay: keyword: unbeatably inexpensive purchasing price.
GETTING A QUOTE WITH LK-MOULD IS FREE AND SIMPLE.
FIND MORE OF OUR SERVICES:
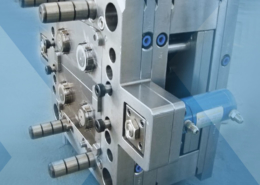
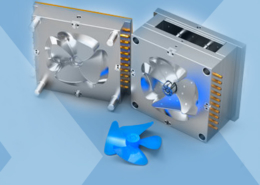
Plastic Molding

Rapid Prototyping
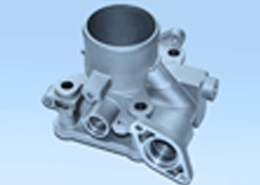
Pressure Die Casting
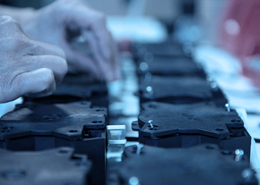
Parts Assembly
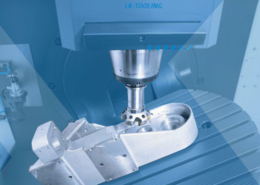