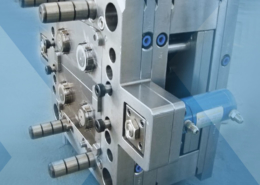
Medical Injection Molding | Thogus | Family-Owned High - medical injection moldi
Author:gly Date: 2024-10-15
The structure of the material is like that of a sandwich, with the low density core completely surrounded by the higher density skin. The texture of the core has been frequently described as resembling a “sponge” or a “honeycomb”. Because of its unique core texture, structural foam is typically anywhere from 20% to 40% lighter than solid polymers, aluminum, steel, sheet molding compound or other commonly used materials.
All-Plastics is on the cutting edge of innovation in plastic injection molding and advanced manufacturing. We utilize scientific injection molding technology and techniques to help you create quality products for applications in pharmaceuticals, the medical, industrial, and packaging industries, and all consumer markets.
However, there is one important difference necessary for the creation of structural foam rather than a solid polymer. In addition to the polyol and isocyanate, an inert gas or chemical blowing agent is added to the mix during the injection process. This changes the nature of the chemical reaction which ultimately occurs.
Due to its not quite solid nature, the base material used in the creation of structural foam is typically a thermoplastic polymer rather than a thermoset. Commonly used thermoplastics include but are not limited to: polyurethane, polycarbonate, polyphenylene oxide (Noryl), polybutylene terephthalate (Valox), and acrylonitrile butadiene styrene.
Injection molding machines are complex machines typically made up of multiple chambers and are powered using electricity or hydraulics. At the very top of most machines is the feeder, a long, cylindrical heated barrel containing a large injection screw.
Although the principle of injection molding is simple, the actual execution of the entire process is actually quite complicated. You have to navigate the complex behaviors of molten plastics and account for the principles of heat transfer and pressure flow. Meanwhile, all the parameters and conditions during production must be maintained precisely to produce a product with the desired characteristics.
Structural foam parts are extremely lightweight – typical weights vary from 55 pounds per cubic foot to a mere 2 pounds per cubic foot. In addition to this decrease in weight, structural foam is strong, durable, and extremely stiff – in fact, up to 8 times stiffer than similar materials such as solid polymers. The modulus of the material increases along with its density, up to a fantastic 250,000 psi. In addition to this, since it is a foam, the material makes for a great thermal and acoustic insulator.
The final product’s material and form are determined before the process begins. You must consider the properties of the desired product and use those considerations to determine the shape of the mold, the thermoplastic material, and how both these components interact during the molding process.
After the cooling period, the material is ejected into a compartment at the bottom of the machine, which signifies that the finished product has been obtained. However, in most cases, the cooled material is dropped onto a conveyor belt for further processing and finishing, which involves such processes as polishing, dying or removing spurs (excess plastic) until finally, the product is packed and distributed to manufacturers.
Structural foam is a manufacturing material which pairs a foamed core with a solid outer “skin,” rather than remaining solid all the way through. It is lightweight and flexible while also maintaining the good strength and stiffness compared with traditional polymers such as polyurethane, polyester or epoxy. The ability of structural foam to produce parts of unprecedented size has led to revolutions in the production of vehicle roofs, interior and exterior body panels, housing for medical equipment, and even skis.
Raw pellets of the chosen material are fed into this chamber and melted beyond their melting point to convert them into a low-viscosity liquid. At the end of the heated barrel is a gate, which in turn connects with the chosen mold tool. As the pellets are melted, the injection screw turns to control the temperature and improve uniformity.
Plastic components produced from injection molding vary and are used in different applications, from medical devices to automotive parts. Its popularity in most manufacturing settings stems from the fact that the process is highly reliable and can produce high-quality plastic products while being relatively inexpensive.
Structural foam is a composite material produced when a polymer, usually thermoset (but can be thermoplastic), is combined with either an inert physical gas, such as nitrogen, or a chemical blowing agent during the molding process. The result is not a solid material but a low-density, microcellular “core” combined with a high density outer “skin”. The core decreases the overall weight of the material while the solid skin allows it to remain strong and impact resistant.
Once equilibrium is reached, the gate opens, and the screw moves forward to inject the molten material into the mold so the molding process can begin.
Structural foam products have a lower than average risk of damage in the mold or during the removal process, making it a highly efficient and easily repeatable method. In addition, structural foam produces no potentially harmful styrene fumes, lowering the health risks for workers involved in the molding process.
The use of structural foam as a manufacturing material comes with a large number of advantages. Of course, structural foam initially became known for its ability to create parts of unparalleled size, such as the roofs or body panels of vehicles. However, it soon became apparent that structural foam promised a number of additional benefits.
Finally, the right thermoplastic polymer must also be used, depending on the desired properties of the final product. Each type of polymer possesses different properties, such as densities, moisture resistance, thermal and pressure resistance, tensile strengths, and rigidities, among others, and must be considered beforehand. The most common thermoplastics used include:
The mold is subjected to intense heat and pressure to shape the material being injected during the molding process. As such, the mold material must be able to withstand these harsh conditions while shaping the material without reacting with the material itself. In this regard, steel and aluminum are the two most common materials used in mold construction. Meanwhile, the shape of the mold is created using computer-aided design (CAD) and 3D modeling software due to their complex shapes.
Lastly, structural foam also features highly paintable, aesthetically pleasing surfaces. In-mold painting (IMP) is possible for all structural foam products, further saving time and money. Multiple colors can also be applied to a single part in-mold. The surface is easy to clean and can be sawn, screwed, nailed or stapled without experiencing any problems.
Sometimes, you are required to manufacture parts of a size larger than can be produced using traditional materials. How can these parts be created without sacrificing strength, stiffness and overall quality? Luckily, there is a simple, affordable solution: structural foam.
In addition, structural foam retains the impact, element and temperature resistance common to thermoplastic and thermoset polymers. It experiences minimal to no thermal expansion, making it perfect for products which will be utilized in a wide variety of climates or temperatures. The acoustic and sound dampening properties of structural foam are also superior to those of standard solid polymers.
The plastic injection molding process is one of the most widely used methods of producing plastic products due to its flexibility, efficiency, consistency, and cost-effectiveness while maintaining product quality.
It involves converting thermoplastic polymers into low-viscosity molten fluids to be mechanically injected into a mold holding the shape of the desired product. The mold, which also contains a cooling mechanism, brings down the temperature of the injected polymer to solidify the plastic product, which is then ejected from the mold. After this, the mold is recovered to repeat the process.
Less polyol and isocyanate are used than in standard solid polyurethane reaction injection molding, so that the resin does not completely fill the mold. Instead, the gas or blowing agent is activated by the reaction between the two components. It expands, filling the empty space of the mold with foam. This creates the “honeycomb” texture for which the interior core of structural foam is known. Surface cells collapse when they come in contact with the walls of the mold, resulting in the creation of the solid skin which surrounds the outside of the material.
The process of molding parts from structural foam is very similar to the traditional method of reaction injection molding. Two components, for example polyol and isocyanate (which are combined in order to create polyurethane) are stored in liquid form in separate containers. They are mixed together to form a resin which is injected into a pre-prepared mold and cures via the means of a chemical reaction.
The injection molding process is a complex yet essential method of production that is also one of the most popular methods of mass-producing plastic products today.
As the molten plastic reaches the end of the barrel, the gate closes, and the screw moves back, causing the molten material and the pressure inside the barrel to build up.
At the same time, the two sections of the mold tool close and are held together under high pressure. Balancing the two pressures is critical to ensure no plastic material escapes during injection.
Structural foam is also highly moldable; it is able to produce variant wall thicknesses across a single part. In some cases, structural foam has even been able to generate wall thicknesses greater than the previous maximum of ½ inch (13mm). It also allows for thick ribs and bosses and reduces the risk of “sinks” over ribs or heavy cross-sections due to the lower viscosity of the mixture. Structural foam products experience less stresses overall during the molding process, and are highly resistant to warpage or deformation.
Structural foam molding is also a highly cost-efficient process. Lower pressures and clamping forces are required during the injection and curing periods, allowing the tooling and molds to be made from lower cost materials such as aluminum. Cycle times are competitive with those of injection and reaction injection molding, making this a time-saving process as well as a money-saving one.
GETTING A QUOTE WITH LK-MOULD IS FREE AND SIMPLE.
FIND MORE OF OUR SERVICES:
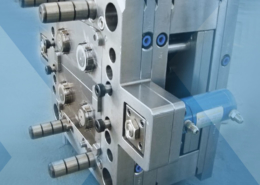
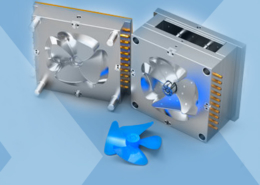
Plastic Molding

Rapid Prototyping
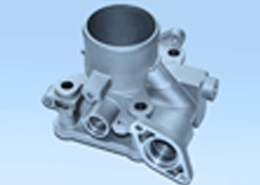
Pressure Die Casting
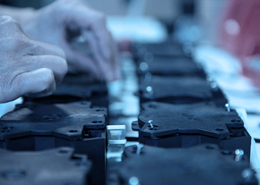
Parts Assembly
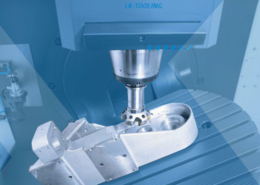