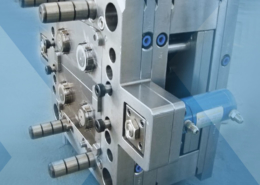
Medical Injection Molding Company - medical device injection molding companies
Author:gly Date: 2024-10-15
Enhanced Product Quality: Two-shot molding can produce more durable, structurally stable products. The integration of two materials can improve overall performance, such as impact resistance and sealing properties.
To produce a single, multi-material component, two different materials are injected into the same mould during the 2k injection molding process. This method is useful for producing intricate, high-quality components that need the blending two or more materials. Separate injections of the two components are made into the mould before they are mixed to form a single component. ACE can efficiently and economically make high-quality, multi-material parts by comprehending and managing these aspects.
Increased Production Hourly Rates: Specialized two-shot molding machines are more expensive than standard injection molding machines. Additionally, operating these machines requires specialized skills, contributing to higher hourly rates.
In summary, two-shot molding is an advanced injection molding technique that efficiently combines two different materials or colors in a single cycle, offering significant advantages in terms of design flexibility, product quality, and production efficiency. Despite its higher initial investment in mold design and machinery, the technology presents a compelling case for applications requiring complex, multi-material components with high precision and strength.
The capability of this injection moulding to shorten production times and boost manufacturing effectiveness is another important advantage. The method eliminates the requirement for separate moulding processes, assembly, or post-molding procedures because it blends two different plastic materials or colours in a single injection moulding cycle. This may lead to shorter cycle times, cheaper labour, and a more effective production process.
DongGuan Company Room 103,#41 Lian Ma Road,Dalingshan Town,Dongguan City,Guangdong Province,China ShenZhen Company Building 5,Juhui Mold Industrial Park,Tianliao Com,Yutang St,Guangming District,ShenZhen City, China
Two-shot molding has the distinct advantage of producing complex, high-quality products with diverse appearances in a single molding cycle. It can reduce post-processing steps, enhance production efficiency, and lower costs. However, this technology demands high requirements for mold design and manufacturing, leading to relatively high initial investments.
Choosing compatible materials is crucial for a successful bond. The substrate and overmolding materials must be compatible in their molten states without adverse chemical reactions. Material suppliers often provide guidance on which material pairings achieve the best adhesion.
Higher Mold Costs: The complex requirements for two-shot molds result in higher costs. Designing and manufacturing these molds demand extensive experience and precision, significantly increasing initial investments compared to traditional molding techniques.
The injection pressure, speed, and melt temperature are important process variables impacting the first shot. These variables affect how the first material flows and is packed, which might impact the consistency and quality of the parts. Higher injection pressure and speed can enhance the first material's packing and raise the possibility of flash or sink markings. To ensure that the first material flows properly and completely fills the mould cavity, the melt temperature must be carefully regulated.
The mold design and review process must be highly meticulous. Given the high cost of two-shot molds, any flaws in the design could lead to modifications in both sets of molds, thereby incurring additional costs. Therefore, the design stage of the molds must carefully consider various elements, including the design of gates and runners, the arrangement of sliders, and the layout of the cooling system. These aspects require thorough verification and validation to ensure no oversight.
In some cases, the substrate’s surface may undergo special treatments such as sandblasting, chemical etching, or surface activation to increase its roughness and chemical reactivity, thereby enhancing the bond strength with the overmolding layer.
Two-shot injection molding, also known as dual-shot or double injection molding, is an efficient injection molding technology that creates composite components made of two different colors or types of plastic materials within a single molding cycle.
The capacity to produce complicated pieces with various material qualities or colours in a single injection moulding cycle is one of the main advantages of this injection moulding. As a result, there is no longer a need for additional assembly or post-molding procedures, improving the parts' consistency and quality. By employing this injection moulding, we may create parts with more exact tolerances, better surface finishes, and greater functionality, which results in a higher-quality product for our clients.
This process must carefully control several factors to attain the necessary part quality and production efficiency, making it difficult to optimize. This study will look into this injection moulding process parameter and how it affects part quality and production effectiveness.
In conclusion, while both two-shot molding and overmolding serve to create composite materials through multiple injection processes, they each offer unique benefits suited to different manufacturing needs.
The process of two-shot molding is outlined as follows, highlighting the intricate steps involved in creating a composite component within a single molding cycle:
ACE injection Moulding Company is an ISO 9001: 2015 certified mould manufacturer, providing services to the global plastic injection moulding industry.
Through the methods and mechanisms described above, two-shot molding can achieve a tight bond between the substrate and the overmolding layer, producing composite material products that are both aesthetically pleasing and high-performing. This technology is widely applied in various fields such as electronic devices, automotive parts, and medical instruments, offering more possibilities for product design and functionality.
Reduced Production Steps and Costs: This method consolidates the injection of multiple materials into one cycle, eliminating subsequent processes and lowering both production costs and time.
The parameters during the injection molding process, such as temperature, pressure, and cooling time, need careful adjustment to suit the characteristics of both materials. Proper temperature and pressure can promote good material bonding, while the right cooling time ensures that the materials solidify without internal stress, affecting the bond strength.
In two-shot molding, the bonding between the substrate and the overmolding layer is achieved through chemical and physical processes, involving material selection, mold design, and processing conditions. This bonding process ensures that two different materials tightly integrate in the final product, forming a structurally intact and functionally robust composite. Here are several key factors in this bonding process:
Design Flexibility: It allows designers to combine different colors or types of plastics in one component, offering unique visual and tactile qualities.
At the interface of the two materials in their molten state, molecular diffusion occurs, meaning molecules from one material penetrate into the other. This helps form stronger chemical bonds and physical entanglements, enhancing the adhesion between the two materials
Two-shot molding necessitates the use of a specialized two-shot injection molding machine and precisely designed molds. The design of the mold must take into account the flow, cooling, and solidification characteristics of both materials to ensure they combine correctly within the mold. The steps are as follows:
Cooling and Solidification: Following the injection of the second material, the entire component cools and solidifies within the mold. This stage is critical for the quality of the product, necessitating precise control over cooling speed and time.
DongGuan Company Room 103,#41 Lian Ma Road,Dalingshan Town,Dongguan City,Guangdong Province,China ShenZhen Company Building 5,Juhui Mold Industrial Park,Tianliao Com,Yutang St,Guangming District,ShenZhen City, China
Additionally, this injection moulding provides greater design flexibility, enabling producers to develop parts with more intricate geometries and various material qualities. By combining two different materials or colours, we can produce pieces with distinctive visual or tactile qualities, such as soft-touch grips or translucent elements. We are distinguishing our goods on the market and providing clients with more valuable products.
Last but not least, this injection moulding can assist companies in saving money in several ways. We can reduce labour costs, material prices, and energy costs by shortening the production process, increasing manufacturing efficiency, and minimizing material waste. Businesses can also distinguish themselves in the market and charge more for our goods by making higher-quality parts with more complicated geometries and various material qualities.
Considering the emphasis on production efficiency in two-shot molding, mold designs should aim for automatic degating whenever possible. This means that at the end of the injection molding process, excess material from the injection ports can be automatically removed from the product without manual intervention. This reduces labor costs and enhances production efficiency.
Additionally, this injection moulding can help increase sustainability by lowering material waste. The procedure can lessen the amount of material waste produced during manufacturing since it blends two different materials or colours in a single injection moulding cycle. This can lessen the manufacturing process' negative environmental effects and increase the general sustainability of the company.
Second Injection: After the first part has solidified and been moved to the second position, the second material is injected into the mold through another injection unit, bonding with the first part to form the final product. This step requires precise control to ensure good adhesion between the two materials.
This detailed process showcases the technical complexity and precision required in two-shot molding, allowing for the production of high-quality, multifunctional components used across various industries.
The mould temperature, cooling time, and ejection time are additional process variables that may impact the general quality of these injection moulded parts. The mould temperature needs to be carefully managed to ensure that the materials are filled and packed properly. The cooling period should be carefully calculated to reduce warpage and increase cycle duration. The ejection time needs to be precisely set to prevent causing damage to the pieces when taking them out of the mould. Two types of 2k injection molding process parameters may be made: those that influence the first shot and those that influence the second shot. The first injection of the first substance is referred to as the "first shot," and the subsequent injection of the second material is called the "second shot."
Two-shot molding, a sophisticated injection molding technique that simultaneously uses two different materials or colors in the same molding process, demands highly precise molds. Ensuring the success of this process involves strict control over several aspects.
Mold design is also critical in ensuring a good combination of the two materials. The mold must precisely control the flow path of each material, ensuring that the second material forms a stable and uniform coverage over the first material’s surface.
The second shot's process variables include the second material's melt temperature, injection pressure, and speed. These factors may affect the part's overall quality and the adherence of the two materials. Increased injection speed and pressure can strengthen the bond between the two materials but also raise the possibility of cavities or delamination. To achieve adequate flow and adhesion to the first material, the melt temperature of the second material needs to be carefully managed.
This process requires a specialized two-shot injection molding machine equipped with two separate sets of screws and barrels. This technology is capable of producing components with both aesthetic appeal and functional strength, finding widespread applications in the automotive, consumer electronics, and medical equipment industries.
Environmental Concerns: Utilizing two distinct materials complicates recycling efforts, as effectively separating these materials can be challenging. The complexity of recycling and the inability to reuse production rejects pose significant challenges for two-shot molding.
The precision of mold alignment is crucial. Two-shot molding employs molds that include two sets of lower molds (moveable) and two sets of upper molds (stationary), which need to rotate or shift during the molding process to align interchangeably. It is essential to ensure that both sets of molds are completely consistent in terms of outer dimensions, internal cavities, and height.
When discussing two-shot molding technology, it’s common to compare it with overmolding. Though these two techniques seem similar in many aspects, involving multiple (two or more) injection molding processes, there are key differences between them.
First Injection: The process begins with the injection of the first material into one of the injection units of the molding machine, forming part of the product. Once this step is completed, the partially formed component remains fixed within the mold or is moved to another position through rotation or shifting of the mold.
Typically, a CMM (Coordinate Measuring Machine, a three-dimensional measuring equipment) is used in production to check the precision of the molds, preventing injection molding defects such as flash due to misalignment.
For companies wishing to make complex parts with varying material qualities or colours, two-shot injection moulding, commonly known as injection moulding, has much to offer. We'll go over some of the main advantages of this injection moulding in this post, along with how it can enhance your company's operations.
Mold Rotation or Shifting: For some two-shot molding processes, the semi-finished product from the first injection needs to be transferred within the mold to a second injection position. This can be achieved by rotating or shifting the mold, depending on the design of the two-shot molding machine used.
Mold Opening and Ejection: After cooling and solidification, the mold is opened, and the finished two-color product is ejected.
This video shows the trial process of 2-shot molding. Because the product is small and has an undercut feature, it can’t be automatically removed from the mold. It might get stuck on the mold’s lifter, so it needs to be taken out manually.
GETTING A QUOTE WITH LK-MOULD IS FREE AND SIMPLE.
FIND MORE OF OUR SERVICES:
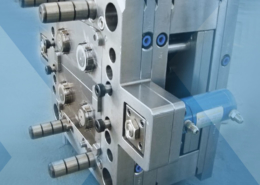
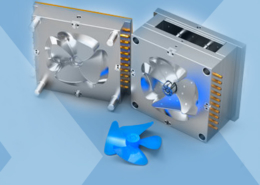
Plastic Molding

Rapid Prototyping
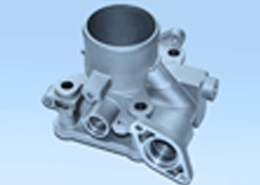
Pressure Die Casting
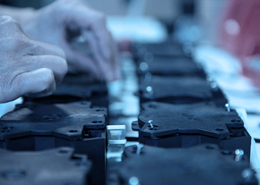
Parts Assembly
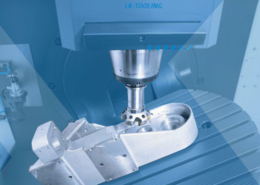