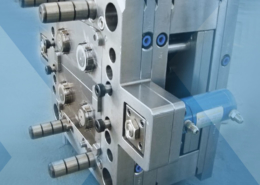
Medical injection molding - medical device plastic molding
Author:gly Date: 2024-10-15
Prototype molds are typically CNC machined in aluminum or brass; the metal is softer and can be machined more quickly and, therefore, less expensive. While aluminum and brass are less robust than stainless steel over hundreds of thousands of molding cycles, molds constructed in these softer metals will typically still produce tens of thousands of parts before the tool wears and, depending on geometry, can produce many more without sacrificing dimensional accuracy over the life of the tool.
Keep in mind that in the first injection parts produced out of the metal injection molding tool the bosses and specified fasteners can be further evaluated and confirmed for performance. There are many screw types available for applications in plastic with varied thread designs.
Injection molding is a process for efficiently creating large volumes of identical plastic parts. The principle of injection molding is very simple. Plastic material is heated until it becomes a viscous melt and is forced into a closed mold that defines the shape of the article to be produced. There, the material is cooled until it reverts to a solid, then the mold is opened, and the finished part is extracted.
Prototype injection molded tooling does not employ automated mechanisms for features in the part that are not in line with the direction of the mold opening. In prototype tooling, these features are created with components (called core pins or pickouts) that are manually loaded into the injection molding cavity and, when the part is molded and ejected from the mold, are ejected with the part. The operator must then manually strip these core pins from the part. The simpler design drastically reduces the cost of the prototype mold as compared to a production mold but increases the cycle time and, thus, the part cost.
When machining injection molds in hardened metals, only small amounts of metal can be removed with each tooling pass, or the cutting tools will break. This is the largest driver for the long lead times to create production tooling, which is typically anywhere from 5 to 16 weeks, depending on part geometry. Larger parts with more complexity take longer to machine. Likewise, parts with intricate geometry that require the use of small cutting tools to create the part geometry in the mold cavity will extend the tooling production timeline.
By reducing the boss’ outside diameter from the overly thick walled recommendation of the screw manufacturer to a reasonably moldable thickness that still provides strength similar to the surrounding plastic walls, using minimal draft on smooth interior boss surfaces, and standing the boss away from outside walls allows for a good combination of strength and low risk of injection molding issues. Outside walls are kept to nearly a constant thickness and joining ribs are kept to 50 to 67 percent of nominal wall thickness. The pilot hole for the screw is sized near but not at the smallest diameter recommended, increased thread engagement depth ensures a strong joint in the plastic injection molded boss, spreading the loads for lower stress.
This can also cause warpage in an injection molded part, and, even worse, the boss features in the part may cause other mold flow problems affecting the injection molded part’s ability to fill out without other flaws.
To dial in the strongest possible boss, yet not have injection molding issues and cosmetic flaws like sink, a good design keeps the intent of the recommendations in mind but cheats a bit on both size and applies a couple of tricks.
With the boss’ bore 30 percent deeper into the nominal base the boss sits on, and an outer surrounding trough at the base of the boss’ wall, the intersecting material sections is minimized which permits thicker boss walls than would be possible without these tricks.
There can be found a lot of injection mold part design suggestions for the creation of bosses, but all too often these guidelines are at odds with themselves. The recommendations can vary depending on whether they are made by a thread forming screw manufacturer, an injection molding contract manufacturer, the final assembly team, or even sometimes an industrial designer. The truth is that all of these inputs need to be considered, and the boss feature needs to perform and not cause cosmetic flaws that are visible on the part. But to achieve that a bit of a compromise needs to be met by the mechanical engineer designing the injection molded part. Of course all team members’ input needs to be considered, and in particular the injection molder needs to be worked with as they will refine the molding process and own the quality of the parts being produced.
Production molds are sophisticated and complicated. In production tooling, features in the plastic part that can’t be formed with the primary core and cavity halves of the mold require side action mechanisms such as slides and lifters. These mechanisms add additional complexity when multiplied across numerous mold cavities.
Injection molded parts are a fantastic solution for medium to high volume products. Depending on the product, the target volume sales per year, cost of goods and the planned repair strategy, molded in plastic bosses offer a low cost way to align parts, and provide options for fasteners for mounting components and securing enclosures. However, proper consideration in the design and placement of the mounting bosses in a plastic part is required to avoid unnecessary cosmetic flaws and proper strength to avoid design failures.
This is simply not the case. Just like 3D printed parts have accelerated the product development process, so too can prototype plastic injection molding drastically improve speed to market, de-risk product failures, and speed up design iterations. Prototype injection molding has progressed. Such plastic parts can be produced quickly at various critical decision points at any point in the design process with lower-cost prototype molds and injection molded parts. When 3D prints have progressed the design as far as it can go, prototype plastic injection molding can produce parts with geometry and material properties identical to production parts, provide the ability to get a head start on design verification and validation testing, and yield cost savings for higher quantities for pilot runs.
Of course each individual design will have its own requirements and priorities. Some parts that are only for function and not seen on the outside of the product can accept molding flaws if they do not impart stresses that compromise overall strength. This is where the design team and the molder need to work together create the best parts possible.
Protoshop Inc. uses steel mold base frames with detail cut into softer metal inserts. This translates to tooling that can produce up to 100K parts, yet is easily modifiable should the part geometry require changes, even non-metal safe changes. Iterations typically occur within a day.
Production molds are designed to reduce the cost of the plastic part as much as possible. While the cost of the plastic is a small part of the overall cost of the molded part, the primary driver of cost is the cycle time of the mold. Cycle time includes the time it takes to close the mold, inject the plastic, cool the part in the mold, and open the mold and eject the part. Production molds can produce a number of parts at the same time with short cycle times; molds are typically built with 2, 4, 8, 16, 32, etc. cavities to reduce part costs, and heating and cooling are added to the mold to speed up the phases of molding. If, for example, the cycle time to create a part is one minute, and the cost to run the mold is $2 per minute, a molded part from a single cavity mold would cost $2, and parts from a 4 cavity mold would cost $0.50.
Changing boss bore size one way or the other may be fairly easy too as this may only require the replacement of a steel pin in the injection molding tool. And this can adjust fastener engagement, assembly torque values, and stresses in the plastic part. This usually is not an issue but is options if needed, say if the plastic alloy is varied during initial part shots.
Prototype parts are created for validation and testing during early design stages. Production parts, on the other hand, are final components produced in bulk following approved designs.
Most prototype molds don’t employ heating and cooling, so the cycle times are longer, and it requires personnel who really know what they’re doing to get the part to fill properly.
A production tool is designed for high-volume manufacturing and is constructed from hardened tool steel. A production tool may have automated slides for side action and multiple cavities. A prototype tool is fabricated in aluminum or brass for short-run manufacturing or concept validation, has hand-loaded core pins, and typically single cavity.
To make the molding challenge even greater for the injection molded part, the boss will need to have draft to allow the part to be ejected from the steel mold tool, at least on its outer diameter walls. This means the cross section of the boss walls will get bigger at the base. It is usually good practice to have a slight fillet at this junction too. However, just like ribs, we talked about earlier, a boss can be thought of as a circular rib, and its wall section should be near 50 to 60 percent of the nominal wall it is bottoming out on, to prevent sink. It becomes difficult to maintain this constraint and have a thick enough wall section at the top of the boss such that the fastener engaging there does not just blow out the side of the boss’ wall, at least for anything other than very short bosses. Keep in mind very short plastic bosses do not allow for as much thread engagement by the fastener. For screws in plastic usually 2 to 2.5 times the nominal screw size is recommended for thread engagement. The number of threads engaged in a plastic bosses helps with strength more than what is conventional for a metal fastener in a steel nut.
Understanding the differences between prototype and production molding can be a game-changer in your product development process. Most think that to have production-equivalent plastic parts, you need to build an expensive, long lead-time, hardened-steel production mold and that this can only happen at the end of the product development process when the design is frozen and production-ready.
If you disable this cookie, we will not be able to save your preferences. This means that every time you visit this website you will need to enable or disable cookies again.
Single-cavity prototype mold fabrication can occur in one week, not several weeks or months. The plastic injection molded parts produced by this tooling can be used for user testing, plastics joining refinement, functional testing, and other part validation activities in advance of investment in production tooling.
Christian is the Executive Director of Operations at StudioRed, a longstanding design studio with over 40 years of experience, known for its dedication to innovation, as evidenced by a diverse portfolio of 4000+ completed projects, 200+ awards, and the successful launch of 450+ products to market. With a background in Economics and Technology Management, Christian helps bring a fresh perspective to the engineering and design team throughout the development process, all while keeping things organized.
A prototype is a preliminary model used for testing, while production refers to the final product made in large quantities after successful prototyping.
So work toward a balanced design, working with the hole development team to ensure the injection molded boss designs are easy enough to mold and strong enough to hold.
This website uses cookies so that we can provide you with the best user experience possible. Cookie information is stored in your browser and performs functions such as recognising you when you return to our website and helping our team to understand which sections of the website you find most interesting and useful.
Also, if the design of the injection molded part and its bosses have walked the line between the extremes, there is a lot that the molding partner can adjust via process, cycle time and cooling to reduce minor sinks so that cosmetic issues can be eliminated for the “as designed” injection molded part.
Prototype injection molding tools are typically single cavities by design, making it easier to make changes to fine-tune the part geometry. If, after molding parts and testing, a change to the part is needed, only one cavity needs to be modified. Metal-safe and non-metal-safe changes can be accommodated. A metal-safe change means that the part change adds plastic to the part, and the mold is altered by removing metal from the mold. If the change requires adding metal to the mold (removing plastic from the part), prototype tooling is easier to change than production tooling constructed of harder metal with multiple cavities; a pocket is cut into the mold, a plug is pressed into the pocket, and the new geometry is machined. Tools constructed with hardened tool steel must be welded to add material to the mold for non-metal-safe changes.
So where does the problem begin and what are the problems? An oversized boss or improperly placed boss can cause sink marks on opposing walls of the injection molded part which may be key cosmetic surfaces. Sink in injection molded parts is where thick sections of plastic exist due to the intersections of internal features with an outer wall. If the thick section has too much more volume than the adjacent nominal wall thickness of the injection molded part, then the interior most plastic material will cool much more slowly and contract in the already cool and rigid plastic around it, creating dimples in plastic surfaces on the outside and stress in the part.
To get it right it is kind of a balancing act to give the boss enough wall thickness so that as a fastener cuts or forms its way in to the pilot hole of the boss there is enough plastic material to handle those installation forces and enough to ensure that the threads of the fastener can rely on the boss for holding strength. Too little material and the plastic, if it does not break during installation, may cold flow and allow the fastener, and in turn the assembly, to loosen up, as the remaining material is not adequate to spread the stresses of the joint. These loads can vary depending on what is expected of the product, the pressures it sees, and even the range of temperatures it is used at.
On the other hand, an undersized boss may be a breeze to mold but might not retain the installed fastener causing parts and components to become loose and compromise the product, or worse the boss can bust out leading to part rejects in manufacturing and even full out product failure in the field.
When a product design has been proven, and there is high confidence that the design will not change, production tools are machined from ultra-hard tooling steel. The hard metal reduces metal wear as the metal heats and cools, and parts are molded and ejected from the mold over tens or hundreds of thousands of times.
Additionally, a moderately designed screw boss in an injection molded part that has been designed with considerations for the assembly of the product and the part molding requirements will have a little leeway in either direction for further dial in. An approach where a bit more plastic is added to the injection molded part’s design to further thicken a boss will only require removing a bit more tool metal. This is called being metal or steel safe, and it is much easier and inexpensive to modify a metal injection mold tool by removing material than adding it back.
Prototype tooling mitigates scale-up risk and is inexpensive to fabricate; typical costs are $6K to $15K, depending on part complexity and size.
Prototype injection molds use the same injection molding materials that are used in production tooling. The difference between prototype and production injection molded parts lies primarily in the construction of the tooling and the number of cavities in the tool.
GETTING A QUOTE WITH LK-MOULD IS FREE AND SIMPLE.
FIND MORE OF OUR SERVICES:
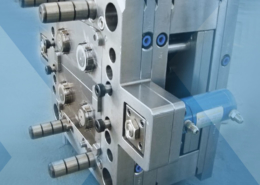
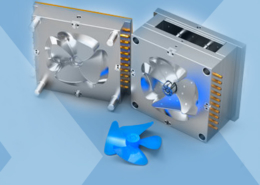
Plastic Molding

Rapid Prototyping
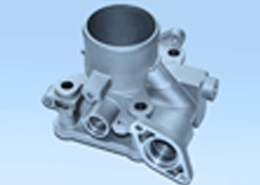
Pressure Die Casting
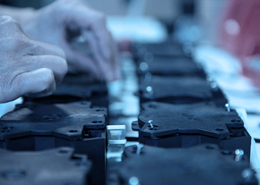
Parts Assembly
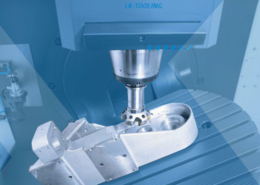