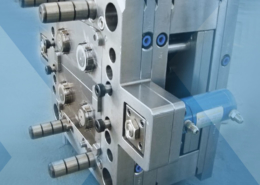
Medical Device Plastic Injection Molding - medical plastic injection molding
Author:gly Date: 2024-10-15
Sterile injectable products are an essential part of the global healthcare system. They are used to treat a wide range of conditions, from life-threatening diseases such as cancer or HIV/AIDS, to chronic conditions such as diabetes and multiple sclerosis, and many other conditions.
The plastic raw material of 5G cap is LLDPE, which has high gloss, high heat resistance and better fluidity than the general materials. In addition, the steel of mold core and cavity is S136, with a hardness of 48-52, which can better for mold life. It could be design with 12 cavities or 16 cavities, each cavity has its own independent cooling system to ensure that the products can be better shaped and cooled.
These dynamics are also driving a growing demand for manufacturing partners who can support the aseptic fill-finish process. These specialized CDMOs (contract development and manufacturing organizations) play a crucial role in maintaining the global supply of sterile injectables.
Today, many authorities are increasing their focus on continuous monitoring of manufacturing processes, data-driven decision making, and risk-based approaches to quality control. To guide a sterile injectable to market in this evolving compliance landscape, drug developers need agile and adaptable manufacturers who can embrace innovation while upholding the highest standards of sterility and patient safety.
The general water bottles are round and sometimes take space in the bags, but these water bottles are square. If they are placed properly, they can save a lot of space inside your bag.
That can include both sterile injectables for clinical and commercial filling services for products that are already on the market. These projects often involve very different processes, production volumes, and timelines that an expert manufacturer can help their customer navigate and plan for.
That is critical because there is no final step to sterilize the drugs in their containers before shipping. Aseptic fill-finish requires advanced equipment and a deep understanding of the complex processes, testing methods, and regulatory standards this method requires.
This highly specialized process is used to produce the many sterile injectable products that cannot tolerate terminal sterilization. This means that full sterility must be maintained across all materials and packaging, process steps, and outputs throughout the entire manufacturing process.
The unscrewing device of this cap mold is hydraulic motor. The ejecting sequence of this cap mold is to let the upper press plate open the mold first, and rely on the I-shaped block to drive the cavity slider to slide away. The mold is opened to a certain stroke, and the caps will be unscrewed by hydraulic unscrewing motor. The left and right thimble plates are performed simultaneously. The spring is pushed out of the barrel by the force of the spring, so that the product is firmly in the core part. After opening the mold, the oil cylinder pushes the rack, drives the central drive shaft, drives 4 product threaded shafts backward to disengage the product, and then relies on the 2 ejector rods on the outside of the machine, and the ejection plate pushes caps off from mold.
Spray cap molds are used in the molds for producing insecticide shells. They are made in accordance with the shape of the insecticide cover required. They are injection molded with plastic and processed into insecticide shell parts through various processes. The principle of the spray tank is that the liquid is pressed out of the valve by using air pressure. The liquid can be sprayed evenly. The direction and dose can be controlled. Any content can be easily put in and easy to use.
Most of the plastic flip top caps mould are designed with two-time ejection structure. The core is pushed out two times. The stripper plate and the ejector sleeve in the middle of the product are pushed out together to 14mm, and then the stripper plate push out continually until the flip top caps drops.
Once again Focare Mould has successfully made another two-color flip top injection mold. It is really difficult to make two-color flip top cap mold especially for 16 cavities. Especially, the diameter of two-color cap is only 20mm and the connection between two materials is so tiny. It is arduous to adjust the connection well completely for 16 cavities. In order to achieve this goal, we must not only have professional mold technology, but also have technical injection molding skill. Focare Mould has its own team in mold design, mold making and injection molding. We have two sets of two-color injection molding machines which permit us to test two-color injection molds and help to train our customers’ engineers when it is necessary.
To protect the medical product and its packaging from contamination, sterile injectables must be manufactured in a highly precise and carefully controlled way. This means using sterile raw materials, maintaining sterile environments, and following strict procedures to prevent contamination at every step of the manufacturing process.
Because the aseptic fill-finish process is so technically complex, companies that develop sterile injectable therapies often turn to specialized manufacturing partners like Vetter for support. Aseptic fill-finish companies typically have dedicated facilities and a specialized workforce like ours.
The process is relatively faster than other options and more cost-efficient, as it requires less specialized knowledge, equipment and processes – but it can only be used with products and materials that can withstand temperatures up to 121 degrees Celsius or radiation exposure.
At every stage in the development of a sterile injectable, both drug owners and their partners must also navigate the complex, ever-evolving world of regulatory oversight and compliance standards. As both science and technology advance, regulators around the world are continually adapting and updating their standards in response – with many of those standards becoming more and more stringent every year.
Here’s a closer look at sterile injectables, including how they’re made, their many applications, and why they require highly specialized manufacturing methods.
Plastic liquor caps are different from the ones we usually use. They are not sealed by threads or barbs like plastic caps of mineral water bottles, but by oak plugs. However, the oak plugs may cause decay or cracking after long-term and long-distance transportation or weather, plastic caps are needed to keep them sealed and protect oak plugs.
Today, sterile injectables are playing a larger and larger role in the global healthcare system every year. A number of factors are driving this trend, and have a deep impact on the global market for sterile injectables. Some of the most important dynamics include:
Sterile injectables are medications and other therapeutic products that are administered directly into the bloodstream or tissues of the body.
Each cavity of this cap mold is designed with separate inserts, so that each cavity product in the process of injection molding maintain the same injection molding pressure, clamping force and other molding conditions, so that the product quality is more stable and reliable. Moreover, the independent insert design can make the life of the mold longer. If there is any problem with the parts, the parts can be directly replaced without affecting the production schedule.
Unlike non-sterile drugs – like pills, gels, or aerosols – sterile injectables are bypassing the body's natural defenses. Delivering a product this way can be highly effective, but also increases the risk that any product contamination may pose to the patient.
CDMOs like Vetter support many essential steps in the process of developing and manufacturing sterile injectables. Vetter has more than 40 years experience specializing in complex drug substances and delivery formats, including both sterile injectables for clinical trials and commercial filling for sterile injectable products. We also have a proven track record of success in helping our customers bring high-quality products and therapies to market worldwide.
Sterile injectables must therefore be free of microorganisms, particulates, or other contaminants that could harm a patient. Protecting that sterility requires a specialized manufacturing process that’s far more technically complex than many other medical products.
Manufacturers that handle sterile injectables may also offer specialized support for specific phases in a product’s development as well.
This approach relies on carefully controlled environments and procedures to reduce the risk of contamination during the manufacturing process, but actual sterilization occurs as a final step before the product is released. Typically, the product and container are sterilized by steam and/or gamma radiation.
GETTING A QUOTE WITH LK-MOULD IS FREE AND SIMPLE.
FIND MORE OF OUR SERVICES:
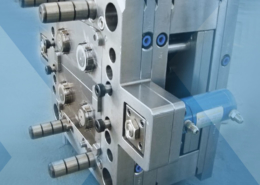
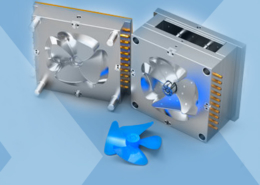
Plastic Molding

Rapid Prototyping
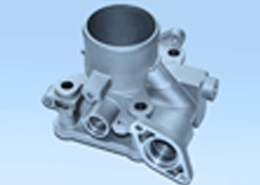
Pressure Die Casting
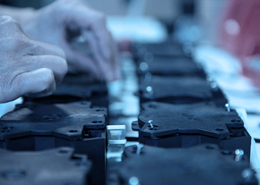
Parts Assembly
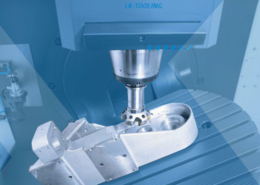