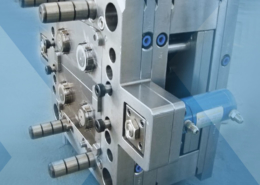
Medical Device Injection Molding - medical device plastic molding
Author:gly Date: 2024-10-15
Injection Process Optimization: Optimize process parameters such as barrel temperature, injection pressure, injection speed, cooling time, and hold pressure to achieve consistent part quality, minimize cycle times, and prevent defects such as warpage, sink marks, or surface blemishes.
Injection molding PEEK requires meticulous attention to material handling, equipment capabilities, mold design, and processing parameters. By adhering to these key elements, manufacturers can produce high-quality, reliable PEEK parts suitable for demanding applications across various industries. For more detailed guidance and best practices, consulting with PEEK material suppliers and injection molding experts is recommended.
Polyetheretherketone (PEEK) is a high-performance engineering thermoplastic known for its excellent mechanical properties, chemical resistance, and thermal stability. When it comes to injection molding PEEK, certain key elements and considerations are essential to ensure successful processing and high-quality parts.
Ming-Li Precision offers advanced capabilities in molding PEEK (Polyether Ether Ketone), a high-performance engineering thermoplastic known for its exceptional mechanical properties, chemical resistance, and thermal stability. With over 100 tons of PEEK material molding production experience, Ming-Li is a valuable partner for industries requiring precision and durability in challenging environments.
A subreddit for anyone in the manufacturing industry. Content is very diverse: you'll find videos, articles and self posts just to name a few.
Material Selection: Choose the appropriate PEEK material grade based on the specific application requirements, considering factors such as mechanical properties, temperature resistance, chemical resistance, wear resistance, and regulatory compliance.
By addressing these key elements and optimizing the PEEK injection molding process, manufacturers can produce high-quality, precision-molded parts with consistent performance and reliability for a wide range of applications.
Tool Fabrication: Fabricate the mold tooling using high-quality materials and precision machining techniques to achieve tight tolerances, smooth surface finishes, and durability. Verify the accuracy of the mold components through thorough inspection and validation.
Venting and Degassing: Ensure proper venting and degassing of the mold cavity to eliminate trapped air and gas bubbles during the injection process, preventing defects such as voids, bubbles, or surface imperfections in the molded parts.
Quality Control and Inspection: Establish comprehensive quality control measures and inspection procedures to monitor part dimensions, surface finish, and physical properties. Conduct regular inspections and testing to verify part quality and consistency.
Mold Design: Design the mold with precision to accommodate the desired part geometry, gating, venting, and cooling requirements for PEEK injection molding. Consider features such as draft angles, parting lines, and vent channels to facilitate mold release and minimize defects.
The design itself is simple, and we're flexible details, but it's basically a two piece shell with 3-4 countersunk recesses for screws on one side and corresponding bosses to thread into. There are standoffs for a PCB, and some other incidental features to position a battery. The walls will be normalized at 1.3-2.2mm, with about 80mm x 40mm overall dimensions.
With over 100 tons of PEEK material molding production experience, Ming-Li Precision's expertise in PEEK material molding positions the company as a leader in producing high-performance components for industries that demand the best in material properties, precision, and durability. With advanced molding techniques, custom tooling, and stringent quality control backed by IATF 16949 certification, Ming-Li delivers PEEK parts that meet the most exacting standards, ensuring reliability and performance in the most challenging applications.
Training and Expertise: Ensure that operators and technicians receive proper training and have expertise in PEEK injection molding techniques, equipment operation, mold maintenance, and troubleshooting to address any challenges that may arise during production.
All that being said, before we pull the trigger on injection molding, I wanted to check if there were any options we may have missed for smaller-run manufacture of these plastic parts, that might have lower cost front-loaded into them. I've looked into things like vacuum molding with silicone molds, and some of the more professional 3D print methods, but had the impression these would be suitable for demonstration purposes (trade shows, promotional materials, etc.) and not to consumer products.
Ming-Li works with a wide variety of materials in our injection molding processes. The high strength-to-weight ratio and heat tolerance of PEEK plastic makes it a popular choice for a wide range of applications including aerospace, biomedical, pharmaceutical, fiber optics, automotive, industrial, and more. In addition to standard injection molding, PEEK resin is also used in overmolding applications to fabricate reinforced components for aerospace and automotive.
Mold Temperature Control: Maintain precise control over mold temperature using water or oil circulation systems to achieve uniform cooling and solidification of the PEEK material, preventing defects such as warpage, shrinkage, or surface irregularities.
Near Net Shapes – What are their benefits? Near net shapes are great for geometries that result in a poor machining yield from a stock shape or those requiring complex tools that are not cost justified by the volume of parts.
We are developing our first product, which is currently at the functional prototype stage. For the next step, we're looking to injection molding, and are working with some vendors to optimize our design for the process and for cost.
This site uses Cookies to improve your browsing experience. we’ll assume you’re OK to continue. If you want to read more about this, please click Use & Disclaimer ,thank you.
PEEK plastic exhibits superb mechanical properties and is highly resistant to chemicals and thermal degradation, making it a highly desirable material for plastic injection molded products. PEEK resin holds up well against high temperatures and long-term liquid submersion and is very durable in harsh environments. PEEK plastic makes an excellent reinforcement material, providing great tensile strength with low weight.
Injection Molding Machine: Utilize a well-maintained injection molding machine with appropriate specifications for processing PEEK material, including barrel temperature control, injection pressure capability, injection speed control, and shot size capacity.
Part Ejection and Handling: Implement reliable part ejection mechanisms (e.g., ejector pins, air ejection) and handling systems to safely remove the molded parts from the mold cavity without damage or deformation.
Our quotes range between $5-12K USD for tooling, and $3-5 USD per part, $17K-20K USD total, giving us an estimated 500 units to sell before breaking even at expected retail of $40 USD, if we ordered 500-1000 parts. The math is loose, and we're not taking into account all costs, marketing, a store's cut, etc.
Injection Unit: Ensure that the injection unit is properly calibrated and equipped with precision metering and mixing systems to accurately dispense the PEEK material into the mold cavity. Pay attention to screw design, back pressure control, and screw/barrel alignment to prevent material degradation and ensure uniform melt quality.
GETTING A QUOTE WITH LK-MOULD IS FREE AND SIMPLE.
FIND MORE OF OUR SERVICES:
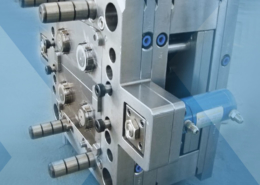
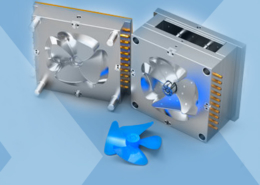
Plastic Molding

Rapid Prototyping
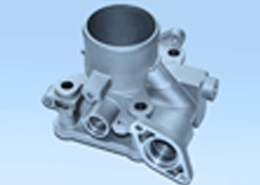
Pressure Die Casting
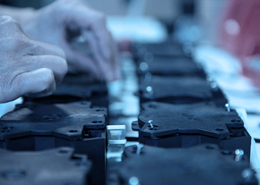
Parts Assembly
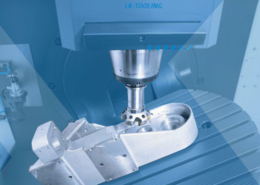