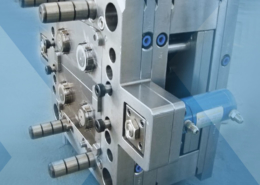
McDonald Plastic Molding's Post - mcdonalds plastic molding
Author:gly Date: 2024-10-15
FDM 3D printing process involves using extrusion for a layer-by-layer deposition of plastic materials until the final product is formed.
Master models can be created using 3D printing or CNC machining. Upon completion of the master model, there is the development of silicone-based casting molds. The raw materials are injected into the mold cavity using a vacuum bell jar. It often takes about 30 to 40 minutes to harden the resulting cast to give a precise duplication of the prototype.
Plastic prototyping is an invaluable tool for entrepreneurs and businesses, especially when aligned with key testing phases: Engineering Validation Test (EVT), Design Validation Test (DVT), and Production Validation Test (PVT). These stages are crucial in assessing and perfecting a physical product before it enters full-scale production.
This section delves into the key considerations that designers and engineers must account for when navigating the complex landscape of plastic prototyping.
When industrial-grade FDM printers are used, fabricators can make a plastic prototype with increased strength and resolution, depending on the materials involved. It is also a flexible procedure, compatible with several materials including PLA, ABS, Nylon, PETG, Polycarbonate, etc.
If your product design requires complicated components and mixed materials, you may be concerned about the multi-step manufacturing and assembly, not only the costs and time involved, but also whether the materials will bond properly and create a long-lasting result. The more steps required, the more time it takes and the more it costs, but with two-shot injection molding, this can streamline manufacturing and improve the results. To help you better understand this method of manufacturing plastics, our injection molding company in North Carolina is taking a closer look at two-shot injection molding.
Vacuum casting is compatible with a wide range of materials, ranging from transparent to opaque. Furthermore, fabricators can reuse the silicone mold to produce up to 25 parts. This process helps you to actualize your design quickly to have product development and mass production in closer proximity.
The final step is the rapid cooling of the plastic into a solid component. The result is a prototype with excellent mechanical properties and a high-quality surface finish. It is compatible with popular plastic material options like ABS, Polyethylene, Polycarbonate, Nylon, HIPS, etc. The plastic injection mold prototype lays down the foundation for subsequent molds you need for complete production runs. Many industries take advantage of this method, including automobile, electronics, medical, and packaging industries.
Looking for plastic prototype manufacturing and fabrication services? Check out RapidDirect and upload your file to get an instant quote.
Digital milling machines significantly enhance the effectiveness of the fabrication process. By employing computers to automate and guide the milling machines with 3D file inputs, fabricators streamline the workflow. CNC prototyping, notably, eliminates the need for molds, making it a more cost-effective solution. The process begins simply with a CAD rendering, setting the stage for efficient project commencement.
With vacuum casting, fabricators can duplicate several plastic parts. It involves the use of a master model to create parts that are suitable for testing. When using vacuum casting for rapid prototyping, the process involves the injection of the raw material into a silicone mold. However, before creating a silicone mold, there needs to be a master model.
A CAD model also shows how the plastic parts fit together and the product’s functioning. Preparing it will help you create a physical prototype model, either visual or functional.
Regardless of the type of plastic prototype you wish to make, there are several methods available. However, four of those methods are more widely used. They include:
There are various techniques available for making plastic prototypes. They include vacuum casting, injection molding, 3D printing, CNC machining, and more. Your choice will depend on your prototype’s application, volume, form, material, and cost.
The essential benefit of a plastic prototype is that it stimulates the actual product features. This way, you can quickly test the design’s correctness and product functionality before going into mass production.
Refer to the accompanying table for a comparison of common plastics and their suitability with different prototyping techniques.
This process empowers designers and prototyping companies to make necessary adjustments, ensuring that both the manufacturer and the end-user receive a well-crafted and market-ready product, facilitating rapid testing and iteration.
Does your design include tight tolerances or complex internal features? The answer to this question will help you choose the correct plastic prototyping technique. Some manufacturing options are limited when it comes to the geometry of designs. Some of them may require high-level design for manufacturing (DFM) optimization before they can be economical or cost-effective. Technologies that can effectively comply with the intended geometry of your plastic part are the best choices.
Part size and volume are closely related to the final cost of the prototyping process. Some processes may have higher front costs for setups and tooling while they produce inexpensive parts. In contrast, other processes may have low startup costs but increased part costs due to lesser automation, slower cycle times, and labor costs. Even with increased volumes, the costs of such processes only reduce marginally.
Several factors affect the cost of plastic prototypes. These factors include the materials used, the part’s complexity, and the technique used. However, 3D printing is generally less expensive than CNC machining. Injection molding is somewhat more costly than the initially mentioned processes due to mold milling costs.
Since 1988, Advanced Plastiform, Inc. has been a leading plastics manufacturer in the Southeast and Mid-Atlantic, using thermoforming and injection molding to design and create durable, high-quality products at a low per-unit cost and fast lead time. To learn more about how we can help you reduce your costs and improve your quality, schedule a quote. We work with all types of industries in North Carolina, South Carolina, Pennsylvania, Maryland, Tennessee, Georgia, and Virginia.
FDM issues filaments, but SLA 3D printing employs plastic resin materials for creating prototypes. It involves using a high-powered laser which helps to solidify the model coming using a vat of resin. Manufacturers use this method for several purposes, including dental, medical, and general consumer components.
The extremely high level of precision needed within the aerospace industry makes CNC machining a suitable manufacturing process for the sector.
The process begins similarly to traditional injection molding in which the liquid polymer is injected into a mold and is then cooled, but before it is a solid. Next, the component is robotically or automatically transferred into a new mold where the second material, color, or texture is added, and as it cools, it forms a molecular bond to the first material. The end result is a more completed, highly durable component, part, or product.
How quickly you need the prototype will also affect your choice of technique. Some prototyping methods use sophisticated tooling coupled with automation to create prototypes within 24 hours. However, tooling and setups for some methods could push lead times up to weeks. If you need testing done very quickly, you should choose methods that produce parts rapidly.
You won’t need a more complex mold for the process, and because the parts are manufactured all-in-one, there is no need to weld or join components together. This saves time and minimizes labor, which will save money on overall manufacturing costs.
Since 1988, Advanced Plastiform, Inc., has been providing superior custom plastic molding and fabrication services to companies in North Carolina, South Carolina, Maryland, Georgia and Pennsylvania. Contact us to make an appointment Mon-Fri 8-5.
Injection molding is a highly efficient technique for the mass production of plastic prototypes. This process begins with the creation of a metal die. Following this, plastic resin is transferred into a heated barrel, where it undergoes mixing and is then powerfully injected into the metal die, shaping the final prototype.
The relative pricing of plastic prototype manufacturing will depend on the chosen manufacturing technique and the volume of parts required. Generally, 3D printing presents the most cost-effective option, while CNC machining is also relatively cheap. The injection molding price is a little on the high side because of the mold tooling.
A variety of distinct manufacturing methods are available, each offering unique advantages and different prototyping speeds for creating prototype plastic components.
If you want to produce high-quality machined parts with a sleek appearance, it’s essential to consider some critical factors related to CNC machining.
While the two-shot molding method may seem more complicated and time-consuming than traditional injection molding, the reality is that from start to finish, it offers several advantages when you need something that is more assembled or consists of multiple components or materials. Benefits include:
CNC machining offers another viable and fast-paced method for plastic prototype fabrication. This technology uses a wide range of tools to create 3D models of your design from solid blocks of materials. Creating a plastic CNC prototype involves a subtractive process. That is, materials are being removed from the solid block, unlike 3D printing, which is an additive process. However, this does not mean that fabricators cannot make plastic prototypes with different materials.
The first thing to reason before plastic prototype manufacturing is your CAD (Computer-Aided Design) model. The model is a digital representation of your intended product showing you and the manufacturer how the product should look.
Double shot injection molding is used in a wide variety of applications. In automotive injection molding, one example is molded-in buttons on a steering wheel that are a softer texture than the rest of the wheel. In medical injection molding, you’ll see that dental mouth guards are often made through double molding where the “frame” is a harder plastic while the bite area is softer.
The low fixed costs of 3D printing ensure zero economies of scale. That is, the first copy has the same cost as the last. The fixed costs of CNC machining are also low, with total costs rising at a steady rate. So, you’d expect the cost of each part to be a little higher than similar parts produced with 3D printing.
Additionally, prototypes offer the opportunity to present your ideas to potential investors and stakeholders, allowing them to physically interact with and understand your product. They are equally important in market testing. Distributing plastic prototype parts to prospective customers allows you to measure their interest and collect valuable feedback before the product’s official release.
What sets us apart? It’s our commitment to excellence. We offer tailored professional advice and insights to optimize your project, ensuring the highest quality at every stage. Partner with us and benefit from our extensive network across various industries, guaranteeing you the most efficient and innovative prototyping solutions available.
Also called double injection molding, this is a method of manufacture where the goal is to form a part or a product made from two different materials or the same materials with different texture or color in one step, rather than forming them separately and fusing them together.
At RapidDirect, we bring your visions to life with unparalleled expertise in manufacturing services, from initial prototyping to full-scale production. Our team of seasoned engineers and designers boasts a deep understanding of a myriad of techniques, including CNC machining, 3D printing, injection molding, and vacuum casting. We’re not just about building prototypes; we’re about crafting success stories.
Ready to bring your project to life? Contact RapidDirect today! Upload your CAD file and embark on a journey to turn your innovative ideas into tangible, successful products. Let’s build the future together!
Additive manufacturing or 3D printing is one of the innovative techniques following Industry 4.0 that transform the manufacturing world. When it comes to printing prototyping, three methods stand out.
By saving time, minimizing costs, and reducing the steps involved in going from start to finish, you can get your product on the shelves or finish the overall project more quickly. Efficiency in manufacturing leads to overall improvements in operation and reduced costs.
The application of your prototype should be your first consideration. These prototypes find their utility across diverse industries and serve various purposes. For instance, they might be designed for non-functional testing in marketing or sales contexts. Alternatively, it could be aimed at functional testing with target users. Selecting a manufacturing method that accurately replicates the final product’s color, shape, and surface texture is critical to ensure the prototype meets its specific objectives.
For prototype plastic injection molding cost, is relatively high for the first few parts. However, the price steeps lower as the volume increases. It is clear that the plastic prototype cost is relative and depends largely on the method used and the volume required.
SLS technology also utilizes a high-powered laser. However, unlike SLA, it sinters powdered materials together to form a 3D model. This process features print quality that is superior to FDM’s. Plastic prototyping created via this method is more functional and has higher resolutions. They are generally more durable and flexible than FDM prints.
When two materials are joined, there’s often trimming and scrap, but when they are molded together, we can minimize the waste and reduce the materials used. Again, this lowers costs, but it also improves the sustainability of the product.
Consider whether your prototype will be subjected to particular stresses or strains. It’s crucial to find a balance between cost, aesthetics, and functionality when choosing the right material for your prototype. Before making a decision, compare the desired characteristics of your application with the capabilities of various manufacturing methods.
Plastic parts do not often get the credit they deserve for the role played in our world. There’s hardly a place you’ll enter without finding them, ranging from your computer keyboard to the lid of your coffee cup. However, every plastic product began as a prototype. This is why we are here to look at the methods available for making plastic prototypes. Let’s get right to it!
GETTING A QUOTE WITH LK-MOULD IS FREE AND SIMPLE.
FIND MORE OF OUR SERVICES:
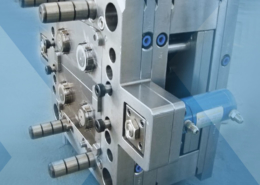
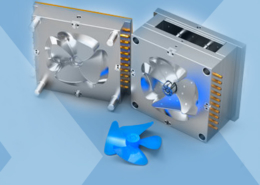
Plastic Molding

Rapid Prototyping
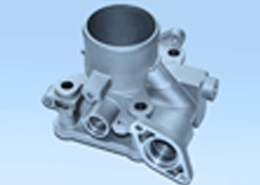
Pressure Die Casting
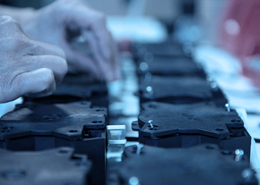
Parts Assembly
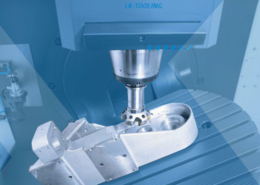