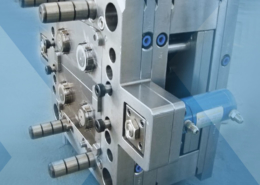
McDonald Plastic Molding History - mcdonalds plastic molding
Author:gly Date: 2024-10-15
Shipping and logistics. Shipping and logistics are required to get finished parts to the customer. These costs will depend on the location of the injection molding supplier and the shipping destination.
CNC machining optionsStainless steels MenuStainless steelsRelated LinksFinishing OptionsCNC Materials MenuFinishing OptionsCNC Materials
Auxiliary equipment. This includes equipment such as temperature controllers, mold heaters, and cooling equipment that are used to control the temperature of molds and injected material.Â
2. The space in the mode locking region is limited, and it needs to repace with the core after finishing the rotation. The space for mold cavity arrangement and slides in mold are smaller.
Multi-component injectoin molding is also named as the multi color injection molding process, refering to the mateiral that has two kinds of color or more than two used for injection molding through a mold with one or more runners. At first, it is featured by two-color injection molding. Our daily contact is mostly two-color products. For example, the handle of the toothbrush we use every morning and evening are made with two-color injection molding. The common material of handle used is PP (hard glue)+TPE (soft glue). TPE is the best material to blend with PP adhesive coating, and the coating soft adhesive is to improve the grip.
Injection molding is commonly used for producing plastic parts such as automotive components, consumer goods, electronics, medical devices, and packaging.
With the increase of complexity of products, three or four color injection molding needs are more popular. Generally speakingk, the three-color machine has two types, one is two station three-color machine, and another one is three station three-color machine. The difference of them is that they adopt differen turntable control mode according to the sturcure design of products (Two sets of moulds or three sets of moulds).
In this article, weâll take a look at common factors that influence the cost of injection molding, including equipment, labor, and materials â as well as tips for reducing manufacturing costs.
1.The overmolding injection molding can be divided into 5 types: 1. Type P (parallel double shot), L (right angle double shot), V (sky side double shot), W (oblique back double shot), H (opposite double shot).
Materials. The most common materials used to make molds are steel and aluminum, with steel being more expensive but longer lasting. Overall, the cost of mold materials can range from a few thousand dollars to tens of thousands of dollars.
Factory1:NO. 101,Building 21, Zone B, Yuanshan Industrial Zone, Shangcun Community, Gongming Street, Guangming District, Shenzhen City, Guangdong Province, China
Injection molding can have high initial costs but is cost-effective for high-volume production. To reduce costs, optimize part design and tooling, select the right materials, and automate your process.
3. Four color injection molding structure is divided into two types: parallel four-color – LV type and back four-color – LVW type.
3C consuming electrics keep seeking improments on the product appearance: small, simple, beautiful, dustproof and waterproof. however, the requirement for this kind of mateiral and procesing normally have clashes, which means it is unable to meet more than one requirement with the traditional design or manufacturing.
How do you optimize part design for injection molding? This complete guide to designing for injection molding provides basic and advanced design tips, including guidelines for creating snap-fits, living hinges and undercuts, and accounting for optimial surface finishes.
Specialty materials. Glass-filled polymers, elastomers, and foamed materials can be used to achieve specific properties in injection-molded parts. The cost of these materials is generally higher than standard thermoplastic materials.
They have different characteristics and customers can select according to their needs. Among them, the V and L types are the most commonly used in Europe. P Type is mostly used in Japan or domesitc made machines. With the five forms of two-color machine, it can continue to derive the definition of the injection form of the three color machine and the four color machine:
When producing parts with injection molding, understanding the range of materials that are available is crucial. Find out more about those materials, their properties, and factors to consider when choosing a material for injection molded parts.
Automation. Automation can help reduce labor costs and increase production efficiency. Consider incorporating automated or semi-automated systems in the production process to reduce labor costs.
Traditionally, it will make the above functions into different plastic parts, and then assemble them together by assembly.
Same for the four-color machine, which can be divided into two station or multi-station & four color machine. Technically, the control precision of multi station rotary table is greatly higher than that of two station. Thus, the manufacting cost of products on this machine is relative high. So, we should select the best option according to the requirements of product structure, like the case of three-color USB flash disk, it is more cost-effective to select multiple stations.
Advantages of multi-shot implant injection molding solutions: it makes one-piece molding and multifunctional integration avaliable, and it supports multi-color modeling without assembly. The key of this technique is the flexible adoptation of bertical injection molding machine. Common machine types include 1 shot x 6stations, 2 shot x 4 stations, 3 shots x 6 stations, among which the multi-station cooling can shorten molding time and increase output. At the same time, it is more convenient to implant injection molding and extract products, and it can achieve automated production.
Find out about the manufacturing technique used to injection mold a second material over or around a part to create a new one.
Injection molding machine. This is the primary piece of equipment used for injection molding. The cost of an injection machine will vary depending on its size, complexity, and features, with prices ranging from a few thousand dollars to several hundred thousand dollars.
Operator labor. Injection molding requires skilled machine operators to operate and maintain injection molding machines. As with any skilled position, exact costs depend on the location and the operatorâs experience.Â
Injection molding is ideal for producing high-volume, high-precision parts with consistent quality. It is commonly used to create automotive parts, electronic components, medical devices, and consumer goods.
To address the issue of the integrating mateirals with different characteristics and functions thorugh injection moldng and implantation in a small space.
Online manufacturing platforms. The right platform can cut costs of injection molding by offering instant quotes, fast turnaround, and help in selecting the right materials for the job, as well as connections to a large network of trusted manufacturers around the world.Â
It can reduce the process of assembly, enhance bonding and improve air tightness by completing plastic (soft/hard), silica gel (solid/liquid), hardware (structure/conductor), electronic chips in a machine cycle.
Injection molding often comes with high initial tooling costs, limited flexibility for small production runs, and material and part design limitations.
1. For the traditional horizontal overmolding machine, the position of the shooting table is fixed, and the shooting table other than the second shooting can only be arranged on the top side and the horizontal side (insert the multi shooting table layout mode). The glue feeding channel interferes with each other.
The costs of injection molding arenât solely centered on equipment and materials. Like any business or service, there are many moving parts that require oversight and management. Here are a few of them.
Three station is different. The turntable can be positioned at three different positions (120degrees). In other words, the three groups of injection units of the three station &three color machine are respectively injected into three pairs of molds. Therefore, if the boundaries of the three components in the product are adjacent, the three station & three color machine is applicable.
The overmolding is normally featured by two sets of compoents. The half is installed on the fixed mold fixed plate of the overmolding injection molding machine, which is also one side of the injectoin molding gate. Another half is installed on the rotating plate of movable mold, which is the side of mold ejection. The rear molds of these two sets of mold are normally same. The cavity is different. When the first kind of material completes the injectino molding, the fixed and movable molds of injection molding machine open. The rotary plate of the moving die rotates 180 ° with the rear die part of the two molds. Now, do not eject the semi-finished products of the first mold back mold, then clamp the mold before carrying out the injection molding of the second kind of mateiral (during this process, the first kind of material will still be made into semi-finished products in the second mold). After thermal insulation and cooling, the fixed and movable molds are opened. The finished product of the first mold is ejected after moving the mold. This is molding cycle process, in which there will be one semi product and one finished product.
Assembly will also brings a series of difficulities, how to add the fastening structure used for fixing, how to combine soft and hard glue, how to hide the assembly line, how to realize the sealing and waterproof of the electronic part, how to make the logo font more permanent, and how to reduce the assembly manpower.
Tooling refers to the design and manufacturing of the mold or tool used to create injection-molded parts. Here are a few cost-related factors for injection molding tooling.
Mold design. The cost of mold design depends on the complexity of the part being produced, the number of cavities in the mold, and the level of precision required. This can range from a few thousand dollars to tens of thousands of dollars.
The cost of injection molding depends on factors such as part size and complexity, the type of material used, and the quantity of parts being produced. Typically, the larger and more simple the part, and the higher the quantity, the lower the cost per part.
Injection molding optionsClear Plastic MoldingInsert MoldingOver MoldingThreaded plastic productsCases for soft rubber mold MenuClear Plastic MoldingInsert MoldingOver MoldingThreaded plastic productsCases for soft rubber moldRelated LinksInjection materialsInjection Molding ToleranceInject Design TipsFinishing OptionsColor card MenuInjection materialsInjection Molding ToleranceInject Design TipsFinishing OptionsColor card
Machining. When machining is needed to create a mold, this can range from a few thousand dollars to tens of thousands of dollars.
This website uses cookies to improve your experience while you navigate through the website. Out of these cookies, the cookies that are categorized as necessary are stored on your browser as they are essential for the working of basic functionalities of the website.
Sheet metal optionsBending sheet metal processingConsiderations of the sheet metal parts design MenuBending sheet metal processingConsiderations of the sheet metal parts designRelated LinksSheet metal materials MenuSheet metal materials
What is Delrin and why is it unique among the many manufacturing materials available? Delrin, or POM-H (homopolymer acetal), is used in CNC machining, 3D printing and injection molding to create durable, precise components. This article explores Delrinâs properties and how to get the most out of the material.
What are the common applications of injection molding? What sets it apart as a manufacturing process? This article covers the key benefits of injection molding and provides insight into whether injection molding is right for your industryâs applications.
Quality control. Quality control is critical to ensure that injection-molded parts meet their required specifications. This may include the cost of manual part inspection, equipment to measure parts, as well as the cost of corrective actions or iterations.
Injection molding process: place pin in station 1. Station 2 combines with the first injection cavity to inject transparent window parts. Station 3 combines with the second injection cavity to inject black shading structure. Station 4 combines with the 3rd injection cavity to inject colored colored shells. Station 5 is are cooled, and the product dislodge is in 6 station. All stations can be operted at the same time.
“Two station” refers to teh two positions of the turntable rotation, which equals to the 180 degree turntable control mode of two-color machine, or we can say the two groups are injected into the same mold at the same time in the three groups of injection units of the two station three color machine. So, if the boundary of two components is not adjacent (it can be designed to inject in the same mold at the same time) in products, just producing three component products with two sets of mold, which is suitable for the two station three color machine.
Colorants and additives. Colorants and additives such as UV stabilizers, flame retardants, and impact modifiers can be added to base materials to achieve specific properties or aesthetics. The cost of these additives depends on type and quality.Â
Want to learn more about die casting? In this article, weâll take a look at the process, its history and current uses, advantages, design guidelines, and more.
Thus, how to present different colors and textures in such small and exquiste space and also taking into account the requirements for dust and water prevention of internal electronic devices has become a major concern for the CMF and structural designer.
Project management. As Protolabs Network manages your injection molding project from beginning to end, this cost includes things like labor, software tools, and associated overhead costs.Â
Injection molding is a manufacturing process used to produce parts by injecting molten material â often plastic â into a mold. The material is then cooled and solidified, and the finished part is ejected from the mold.
Molds. The cost of molds depends on the size, complexity, and material of the part being produced. A simple mold can cost a few thousand dollars, while a more complex mold can cost tens of thousands of dollars or more.
Want to learn how to design undercuts that donât cause damage to your parts? Check out our article, which offers tips and tricks for DFM with undercuts, examples of when you might need them, and more. Undercuts in injection-molded parts present a host of challenges to designers and manufacturers. In this article, weâll take a look at the definition of undercuts, their purpose, applications, and tips for designing parts with them.
It comnines the multi material injection molding and mold, vertical rotary table injection molding machine, automatically extraction and other implantation, as well as other multidisciplinary integrated technologies.
You can learn more about the injection molding process including important design considerations, and contact networksales@protolabs.com for personalized advice about your project.
With the rapid development of smart phones and mobile Internet, more and more smart wearable products have come into our sight. This type of products require an integrated service achieved within a small space. When producing this type of products, it is hard to fix the impalnts if the mold is opened horizontally with traditional injection molding, and there are risks during mold compression due to the insufficient space in mold. What’s more, it is harder for multi material injection molding. As a new production technology, manufacturers of precision injection molding products with small area functions have unique advantages.
Tooling optimization. Optimizing the mold design and manufacturing process can help reduce the tooling cost. Using aluminum rather than steel tooling, for example, can be a cost-effective option for low-volume production runs.
You can reduce the costs of injection molding by optimizing design and tooling, selecting the right materials, considering production volume, and considering automation for your injection molding process.
Learn what to consider when making a choice between 3D printing and injection molding, the benefits of each manufacturing method, and more.
Injection molding offers high production speed, design flexibility, and repeatability with precise tolerances. It is suitable for producing complex parts with consistent quality, and is the most cost-effective option for high-volume production.
Why is it important to design draft angles for injection molding custom parts? This article covers why draft angles are essential and how to design them better to get the most out of your injection molding designs.
Office:1602, Unit 8, Building 2, Shangxing Commercial Street, Shangde Road, Xinqiao Street, Baoan District, Shenzhen City 518125
Want to learn more about exactly how an injection molding machine functions, as well as its individual parts? This article puts injection molding machines under the microscope, with detailed descriptions of their components and an in-depth guide to the injection molding process.
In this article, weâll take a look at common factors that influence the cost of injection molding, including equipment, labor, and materials â as well as tips for reducing manufacturing costs.
2. Three color injection molding structures are divided into five categories: right angle tricolor – L type, roof tricolor – V type, back tricolor – LW type, back tricolor – VW type, and independent tricolor – LV type.
There are different types of costs in injection molding, including equipment costs, mold and tooling costs, material costs, and labor or service costs. As stated above, these costs will vary, depending on complexity, size, quality, materials, and other factors.Â
Design optimization. Optimizing a partâs design can help reduce material costs and minimize mold complexity. Simple designs with fewer features can result in lower tooling costs, which can reduce a projectâs overall cost. Our automatic DFM analysis identifies potential issues with your design, helping to reduce your costs.Â
Material selection. Less expensive materials can reduce material costs, but it's important to balance cost with part performance â meaning choosing the right material for the job is critical. Protolabs Network is always available to advise on this.Â
3D Printing options3D printing materials Menu3D printing materials3D Printing LinksThe application of 3D printing in the laryngoscope mold3D printing raise the manufacturing capacityHow much should you pay for your 3D printing components? MenuThe application of 3D printing in the laryngoscope mold3D printing raise the manufacturing capacityHow much should you pay for your 3D printing components?
What are the most common defects in the injection molding process and how do you avoid them? This article provides six essential design tips for avoid production defects while reducing the cost and lead time of your molded parts.
Tooling maintenance costs. Molds require regular maintenance to ensure they are able to produce high-quality parts. The cost of mold maintenance will depend on the frequency of maintenance and the level of necessary repairs.Â
Material handling equipment. This includes equipment such as dryers, hoppers, and conveyors that are used to handle and transport the raw materials used in injection molding.Â
3.When the mold is opened horizontally, the embedded parts need to be specially designed with a fixed structure, or they will be inclined due to gravity.
Multi-shot implant injection molding is suitable for producing the bottom cover of this type of band. Combining the six procedures into one procedure not only can significantly simplify the flow, but also saves a large amount of material transfer, personnel input, defective product consumption and other costs. Meanwhile, it also reduces environmental pollution.
Thermoplastic materials. Thermoplastic materials are the most commonly used materials in injection molding. They include polypropylene, polyethylene, and polystyrene, and typically range from less than a dollar to around $10 per pound.Â
Finishing Services optionsAnodic OxidationSandblastingPlastic ElectroplatingMetal Electroplating MenuAnodic OxidationSandblastingPlastic ElectroplatingMetal ElectroplatingRelated LinksSecondary processing MenuSecondary processing
During MSIM, thevertical three-color & six-station rotary table injection molding machine is used. Three cavity and six cores, one out of two with manual placement and pick-up. The whole cycle is 30 sec. The products can be packaged directly after out of mold without assemblying.
You have some questions? Upload your drawings or documents, and we have professional technicians to answer them for you.
For original procedure, it needs to design fixed structure between parts or to meet waterproof requirements with auxiliary materials (sealing ring and adhesive). However, due to the aging of sealing ring, strength and stability of dispense glue, the waterproof performance is affected. Now, by multicolor implantation injection molding process, put the key parts in the mold for integrated molding, which largely increase the waterproof performance. While, since this technique require multiple sets of molds, so the cost is indeed higher. Thus, it is often used for large volume and small sized products.
Injection molding is widely used in the automotive, consumer goods, medical, and construction sectors due to its ability to produce complex and high-quality parts.
Tooling and maintenance equipment. This includes equipment such as mold cleaning and maintenance equipment, and tooling and machining equipment used to make and modify molds.
Die casting optionsAluminium die castingZinc Die castingGravity CastingLow-pressure die casting MenuAluminium die castingZinc Die castingGravity CastingLow-pressure die castingRelated LinksDie casting Tolerance5G productsAutomobile gearboxMaterials for die castings MenuDie casting Tolerance5G productsAutomobile gearboxMaterials for die castings
The traditional horizontal injection molding process has encountered more and more bottlenecks in solving such products.
Thermoset materials. Thermoset materials â such as epoxy and phenolic resins â are often used for applications that require parts with temperature or chemical resistance. Because they exhibit specialized properties, the cost of these materials is usually higher than thermoplastic materials.
GETTING A QUOTE WITH LK-MOULD IS FREE AND SIMPLE.
FIND MORE OF OUR SERVICES:
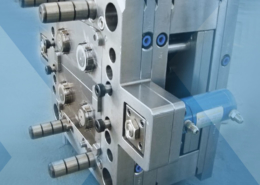
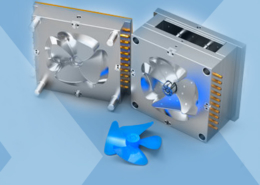
Plastic Molding

Rapid Prototyping
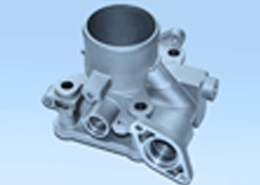
Pressure Die Casting
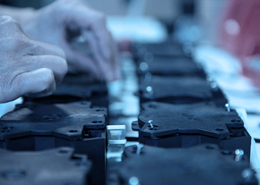
Parts Assembly
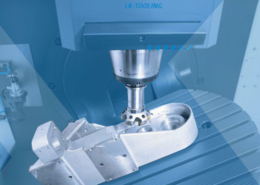