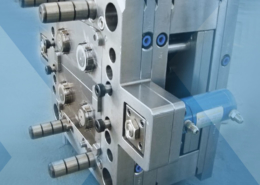
Materials for Home Crafts & Hobbies - thermoplastic molding at home
Author:gly Date: 2024-10-15
(1) Insufficient injection molding capacity – This is caused by an overestimation of the capacity of the injection molding machine, which may also occur due to insufficient plasticizing capacity or insufficient injection volume. Among them, the insufficient plasticizing capability can be increased by extending the heating time, increasing the screw speed and raising the backpressure. If the injection volume is not high enough, the injection machine with a larger injection capacity can be used to solved the problem.
To get the best results from this process, product developers should be aware of the following limitations and potential disadvantages.
Once the base cools and is semi-hardened, the mold is then rotated to a new position and connected to a separate nozzle, gate, and runner system. The remaining void of the mold tool cavity is filled with TPE or TPU elastomer, creating the overmold that bonds to the substrate.
(3) Unstable production cycle – Frequent machine shutdown, and production inconsistent with the normal cycle make some plastics stay in the barrel for too long with reduced density and viscosity, thus resulting in plastic underfill.
Insert molding involves placing a pre-manufactured component, such as a threaded fitting or an electrical contact, onto a mounting pin or other fixture in a plastic injection molding tool. During the molding cycle, thermoforming resin surrounds this insert and solidifies, thereby permanently sealing it into place.
Inserts should be used whenever a plastic case needs to be occasionally opened for service and then locked tight again, such as when performing routine maintenance or changing batteries. They cost a little more but that cost is offset by making a much more durable end product.
Overmolding starts with a base substrate, on top of which a relatively softer TPE or TPU material is bonded. The base can be metal or plastic, although, in this article, we will focus on plastic applications primarily.
Remember that overmolding is rarely used to cover the entire base substrate. Instead, apply overmolding in sections. For each of these, keep in mind these useful design tips:
All in all, the reasons for short shot are multifaceted, which are also mutually restrictive and mutually influential. To reduce and correct such a defect, we need to make adjustments through an overall consideration of the relationship between these aspects, while making constant practice and accumulating experience continuously to quickly identify the causes of underfill, thereby reducing resource waste and improving product yield.
Get 7-day standard lead times on simple parts between 0.5 in. x 0.5 in. and 4 in. x 3 in. Upload your part to see if it’s eligible.
You should consider using insert molding for a few main reasons. The first is that your product application needs strong mechanical fittings to hold two or more parts together, typically for an enclosure or housing. Threaded nutserts are great for this but there are many types of snap connectors as well.
In order to eliminate such defects, the melt / mold temperature, and the injection pressure / speed can be increased to allow the melt to reach the end of the cavity before solidifying. In such a case, a great plastic fluidity is of particular importance, so selecting the plastic with a better fluidity is also a solution. If the flow coverage is too long and the plastic cannot properly fill the injection molded part, it is recommended to change the gate location to reduce the plastic flow length.
This is just a partial overview of insert molding and overmolding. Are they the right solutions for you? Not sure how to apply them to your next project? Just contact our technical experts and we can offer helpful advice about how to get the best results from both processes.
Overmolding uses a special type of plastic injection molding tool, one that has a cavity for the substrate portion and another separate cavity representing the overmolded section.
(2) The flow range of the melt is too long, and the flow resistance is too large – The parts that hinder the flow of the melt include the nozzle, the sprue, the runner, the gate, and the thin walls of a product. The flow resistance of the nozzle can be reduced by increasing the nozzle diameter / temperature, and using a nozzle with a small flow resistance.
While there are many advantages to insert molding, there are some potential drawbacks that designers should be aware of.
(1) Local short shot caused by the flow imbalance in each cavity of a multi-cavity mold – When the injection molding capacity of the injection molding machine is sufficient, this defect is mainly caused by the uneven flow in each gate, i.e., the mold cavities are not distributed in a balanced way.
Get 7-day standard lead times on simple parts between 0.5 in. x 0.5 in. and 4 in. x 3 in. Upload your part to see if it’s eligible.
(2) Try to evenly mix the recycled material and the raw material. Because the recycled pellets, as well as their density are relatively larger than the raw material, if the mixing is not uniform, the amount of the molten material is easily reduced, resulting in reduced injection volume accordingly.
Overmolding also offers more opportunities to be creative by applying colorful designs to improve the appearance of the part as well as its performance.
(1) Poor plastic fluidity – If the plastic material doesn’t feature a great fluidity, it will solidify before reaching the furthest end of the cavity or flowing to the overflow tank, which often results in a short shot.
The first conventional injection cycle forms the substrate, using a standard thermoforming resin. This resin fills the gate, runner, and cavity system of only one part of the mold, while the section representing the overmold is blocked.
Inserts can be either male or female. Female inserts are used to make circular fittings inside the surrounding plastic. When these types of inserts have internal threads, they’re called nutserts. There are many advantages to using both male and female inserts to enhance a product’s appearance and utility.
Product developers should consider overmolding in order to improve the grip and texture on parts that need to be held in the hand or to protect the end user against vibration, heat, or electricity. Overmolding is also a great way to permanently bond rubber to metal, as is found on wheels and casters.
Neither overmolding nor insert molding is restricted in their use to any particular industry or product type. Because both methods are so useful and adaptable, new practical applications are being found all the time that take advantage of their benefits. Here are a few examples:
Insert molding is used to put a rubber or plastic handle on a metal part, such as you might find on hand tools or kitchen knives. And insert molding is ideal for sealing wires and electrical connectors into permanent plastic housings that block out dust and moisture.
(2) Oversupply of plastic – If too much plastic enters the barrel, the injection pressure is lost due to the compression of the pellets, thus reducing the pressure required to inject the melt from the nozzle, which is necessary for injection molding, resulting in insufficient injection pressure. The solution is to adjust the amount of feed, i.e., the amount of melt, and make the amount just right for the molding.
And overmolding adds cushioning and shock absorption to many common household items that might protect users from accidental injury.
In this video, Gordon Styles, the founder and President of Star Rapid, goes into greater detail explaining how these processes work, and he gives examples of each. Be sure to check it out for more useful information.
Overmolding is a special form of plastic injection molding. Unlike conventional molding, where a finished product is made in one cycle, overmolding requires at least one additional injection cycle using a dissimilar material. This method is also known as 2K overmolding, two-shot molding, or even multiple material molding.
In this article, we discuss insert molding and overmolding, the advantages of each, and the applications they’re best suited for. We hope these manufacturing insights, along with useful design tips, will help you get great results on your next plastic injection molding project.
During the product design process, the principle of uniform wall thickness must be followed. If it is impossible to maintain a uniform wall thickness, please change the mold design in a timely manner. Increase the number of runners or ribs in the area where the feeding is difficult, so as to avoid the defect of underfill caused by too-thin wall thickness.
If the substrate is a plastic base, then it’s customary to mold it in the same production cycle. This is done because it’s more cost-effective to make the entire finished piece at one time, rather than paying to transport and store semi-finished goods. But the more important reason is that the elastomer will adhere much better to a still-warm, semi-cured, and “sticky” substrate.
Get 7-day standard lead times on simple parts between 0.5 in. x 0.5 in. and 4 in. x 3 in. Upload your part to see if it’s eligible.
Short shot refers to incomplete filling of a mold cavity which results in the production of an incomplete part due to the insufficient plastic fluidity. The main causes are the inappropriate injection pressure and speed (including excessive pressure loss caused by resistance), which are mainly affected by the following aspects:
The process is not limited to just two materials, and can theoretically be expanded to include an indefinite number of additional overmolds. However, in practice, more than two becomes increasingly complex and expensive.
(1) Improper injection molding process – The low barrel temperature, slow injection speed, short injection time, and insufficient backpressure lead to a shortage of plastic.
(3) Poor venting. When filling the cavity, air is trapped to cause counter pressure. When the melt is injected into the cavity, the cavity is often closed by the melt in the very beginning, with air trapped in the unfilled local areas. Also, because the filling speed is too fast, sometimes there is not enough time for the air to be vented through the parting surface but compressed instead, resulting in partial unfilled areas in the cavity, thus short shot in the molded part.
Now, if that design logic is applied to a fleet of aircraft or millions of automobiles on an assembly line, then the reduction in weight and cost becomes substantial.
There are some unique engineering challenges that designers might face when using insert molding. The advantages of added strength and versatility must be weighed against the need for a more careful design for manufacturing review. Here are some useful guidelines to consider:
Which process is right for you depends entirely on your application. Keep in mind that they aren’t mutually exclusive molding methods because they serve different purposes. In fact, it’s not uncommon to find both used on a single product. Think, for example, of a power tool that has overmolded grips on the handle, but that also uses nutserts to bolt the case together.
GETTING A QUOTE WITH LK-MOULD IS FREE AND SIMPLE.
FIND MORE OF OUR SERVICES:
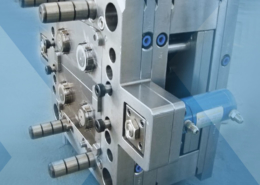
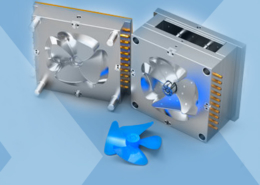
Plastic Molding

Rapid Prototyping
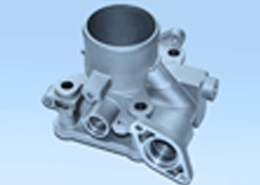
Pressure Die Casting
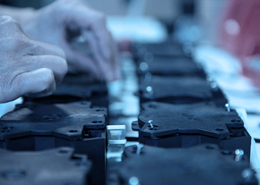
Parts Assembly
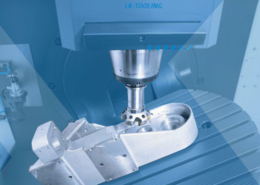