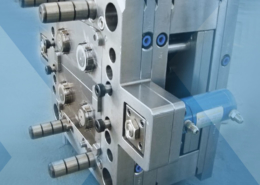
Manufacturing Methods of Plastic Molding - plastic molding and manufacturing
Author:gly Date: 2024-10-15
Each year, the mining industry requires millions of screening panels made from polyurethane plastic. There are hundreds of different panel designs so the injection moulding process requires frequent mould changes. To make the changes as easy as possible only core and cavity of the mould are changed and these parts are made from aluminium so one operator can change to a different panel design in less than 30 minutes without the use of lifting equipment.
The main problem with using aluminium cores and cavities is that they are often damaged during change overs which results in flash on the plastic panels. This flash needs to be removed on every panel produced which is a secondary operation and reduces productivity.
Engaging an experienced injection molding expert in China can help you minimize these challenges. They can offer design improvement suggestions and employ high-quality materials and machinery. A high-quality plastic molding process in China can significantly reduce the occurrence of ejector pin marks.
There are a number of commercially available aluminium alloys made for injection molding. They include Alumec, Bohler 7075, Hokotol, Alumold 500 and QC-10.
There are several benefits to using aluminum molds in injection molding but there are also a number of challenges that need to be taken into consideration before deciding if it is right for you.
The use of aluminium moulds in injection molding is an emerging trend because of its ability to reduce cycle time by as much as 50% when compared to P20 tool steel.
When you choose HLH Prototypes as your plastic molding partner in China, you can rest easy. With our expertise in injection molding, we focus on delivering high-quality, injection-molded parts that meet your specifications every time.
Please place file(s) for transfer in the same folder and ZIP or RAR before attaching. Larger attachments can take a few minutes to transfer depending on your local internet speed :) For attachments over 20MB, click WeTransfer and send to info@HLHPrototypes.com.
Faster cycle times – up to 50% compared with P20 steelIncreased productivity which reduces the number of molds and molding machines requiredLess wear and tear on machines because the moulds are lighter than steelLighter mould means reduced energy consumption by the machine making it cheaper to runCan use glass filled materialsFor injection mold makers:Easier to machine than P20 and H13 tool steel so delivery lead times are shorterLess wear and tear on machineryReduced machine energy consumption making them cheaper to runEasier to handle and transport
Its not as simple as saying you would like to make all of your future moulds from aluminium. R&D must be done and your mould maker must support you.
Aluminium moulds are not for every molder. They will benefit those who have life time production quantities of less than 1 million parts and are committed to solving the challenges they present.
Aluminium can be hard anodized, hard chromium plated or nickel plated for increased hardness, wear resistance and corrosion resistance.
Plastic Today Magazine August 29th 2012 Article “ Aluminum vs. steel tooling: Which material is right, and how to design and maintain?” by Clare Goldsberryhttp://www.plasticstoday.com/articles/aluminum-vs-steel-tooling-which-material-right-how-design-how-maintain-082920122
Plastic molding in China offers a consistent and high-precision method for creating identical plastic parts through custom molds made of aluminum or steel. However, one challenge you may encounter is the appearance of ejector pin marks on your parts. These marks, also known as pin pushes, can not only affect the aesthetic quality but can also undermine the durability and performance of the product.
GETTING A QUOTE WITH LK-MOULD IS FREE AND SIMPLE.
FIND MORE OF OUR SERVICES:
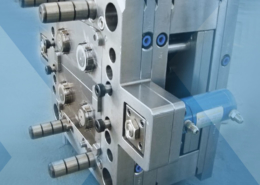
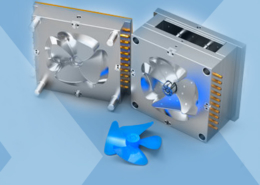
Plastic Molding

Rapid Prototyping
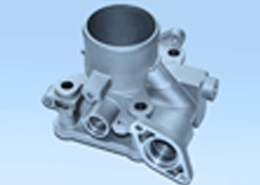
Pressure Die Casting
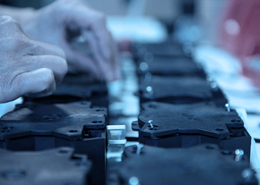
Parts Assembly
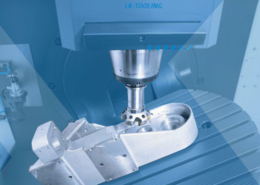