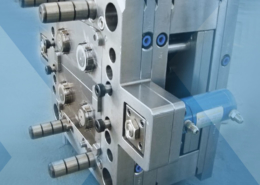
Make Your Own Injection Molding Machine - injection molding at home
Author:gly Date: 2024-10-15
On most machines the mould is held closed by a combination of either a Toggle clamping system that utilises a relatively small hydraulic cylinder or by a Direct Lock system that applies pressure directly using much larger diameter cylinder or combination of cylinders. The force generated is known as the Clamping Force, and is typically measured in either metric tonnes or in kilonewtons (KN), the conversion rate being ten 10,000 KN to one metric tonne.
Sanner takes a scientific approach to designing, developing, and maintaining molds. Sanner’s tooling engineers can design, develop and maintain tooling for even the most complex devices or components. We start with our rigorous tool concepting process followed by mold flow simulation studies to assess material fill data. This data set allows our injection molding designers can better position mold gates, anticipate knit line locations and identify difficult to fill spots within the molds early in the process. All of this is done under the oversight of our metrology group to support component quality all the way through production. Critically, Sanner maintains its molding expertise in-house, with our own tool shop for more control and quicker turnaround in mold development and maintenance. Through scientific injection molding data analysis, Sanner‘s molding processes result in high-quality reproducible parts made by validated processes for CDMO customers.
Sanner’s mold tooling providers include some the world’s most advanced and well-established sources that can support virtually any tooling need. Sanner has been serving drug delivery, diagnostics, and medtech customers for over two decades with production processes and quality systems that are fully adapted to the requirements of the pharmaceutical and medical device industries. This includes our extensive injection molding capabilities from concept, design up to tool maintenance and optimization. We use our ISO Class 7 or 8 cleanrooms as well as unclassified spaces for molding activities, depending on the individual requirements, all operated under an ISO 13485 quality management system (QMS).
HeadquartersSanner GmbH Schillerstr 76 64625 Bensheim GermanyTel.: +49(0)6251 938-0info@sanner-group.com
Still headquartered in Germany, Sanner leverages its development expertise and best-in-class manufacturing capabilities to lead the market in desiccant closures and effervescent tablet packaging, and a sought-after provider of customized solutions for medical devices, diagnostics, pharmaceuticals, and consumer healthcare. To provide customers with a suite of leading, end-to-end services across drug delivery, diagnostics and medtech device sectors, Sanner recently acquired Springboard Pro, a leading device design and development consultancy based in Cambridge, U.K., and the U.S.-based CDMO Gilero, a specialist in medical design, development, manufacturing, assembly and packaging. Since 2021, Sanner Group has been backed by majority shareholder GHO Capital Partners LLP, a leading specialist healthcare investment advisor. Together, GHO and the fourth generation of the Sanner family will continue its successful growth to create intelligent healthcare solutions for a better quality of life.
Our cleanroom molding facilities are capable of manufacturing packaging systems such as complex resealable pipettes, with pre-determined breaking points for dose opening, and thin-wall injection molded parts with exact wall thickness for tight device seals.
Injection Moulding (or Molding to use the US spelling), along with extrusion ranks as one of the prime processes for producing plastics articles. It is a fast process and is used to produce large numbers of identical items from high precision engineering components to disposable consumer goods.
The pressure of injection is high, dependant on the material being processed; it can be up to one thousand atmospheres. Tools tend to be manufactured from steels, (which can be hardened and plated), and Aluminium alloys for increased cutting and hand polishing speeds. The costs associated with tool manufacture means that injection moulding tends to lend itself to high volume manufacture. Details of process costing can be found at:
Our high-precision electric thermoplastic injection molding capabilities are designed to produce molded parts with shot weight accuracy and repeatability at low deviation to mean ratios for high-quality drug delivery, diagnostic, or medtech components.
Injection mouldings count for a significant proportion of all plastics products from micro parts to large components such as bumpers and wheelie bins. Virtually all sectors of manufacturing use injection moulded parts - the flexibility in size and and shape possible through use of this process have consistently extended the boundaries of design in plastics and enabled significant replacement of traditional materials thanks to light weighting and design freedom. The table below shows the type of products that can be injection moulded, but is by no means comprehensive.
CANBIO-ST. Fully digital toggle type machine range by Negri Bossi, up to 500 tonnes clamping force. The Canbio ST machines are also fitted with the energy saving servo pump drive and have an excellent specification as standard.
Sanner offers 2K injection molding capabilities that is ideal for even the most complex molded parts. Sometimes called double injection, multi-material, or two shot molding, it is a specialized molding process that combines different thermoplastics (TP) in a single molding step. 2K molding can produce your complex drug delivery, diagnostic or medtech device parts for better handling characteristics and improved user-convenience.
Sanner’s device CDMO teams bring extensive experience in processing a wide range of materials for different applications. Molded materials commonly utilized at Sanner include polypropylene (PP), high-density polyethylene (HDPE), all types of engineering plastics -, and various biobased materials with up to 64 cavities. Don’t hesitate to inquire if your device requires specialized materials.
The Babyplast can also be operated under ISO Class 7 clean room conditions. Furthermore it is also possible to produce LSR parts in the prototype and Scale-up stage.
If you are looking for a product or a moulder, please complete your details below and the BPF will send the detail, on your behalf, to the most relevant companies within the plastics industry who will contact you directly with more details.
VECTOR. Medium to large tonnage by Negri Bossi (650 to 1300 tonnes) toggle machines with ultra-low level design and energy saving electric screw drive as standard. Injection moulding machine manufacturers sometimes quote a figure for the Locking Force of a machine. In the case of a Direct Lock machine, figures are the same as for the Clamping Force. In the case of Toggle type machines, there is a mechanical advantage that means that the Locking Force is around ten percent higher. In a large machine the Locking Force can be up to thousands of tonnes and is spread over the area of the mould. To counteract the injection pressure, a moulding with a large surface area will therefore need a machine with a higher locking force than a moulding with smaller surface area. Other factors such as a thin wall section can also require a higher Locking Force than typical, this being to counter a higher injection pressure being required to fill the mould. There is however a direct correlation between the Clamping / Locking force of a machine and both its physical size and purchase price.
BI-POWER. Large twin platen machine by Negri Bossi (up to 7000 tonnes) with low level design and energy saving electric screw drive as standard.
Machines can be specified with a choice of injection unit size, smaller injection units providing better accuracy if relatively small components are being produced for the size of machine. A good example would be the production of automotive components, where it is often the large and complex mould tools that dictate that a higher tonnage machine is needed for its physical size, rather than its maximum Locking Force. Within each specified size of injection unit, there is also a choice of injection screw diameters. The larger the diameter of screw that is fitted, the larger the maximum ‘shot weight’ of plastic that can be generated will be. There is however a proportional reduction of the maximum injection pressure that can be generated. This is going to be less critical if large components with relatively thick wall sections are being produced using plastic materials that are of lower viscosity.
1. Typical Material Used 2. Typical Products Produced 3. The Process 4. Size of Machine 5. Computer Controlled 6. Contact A Moulder 7. Comparative Production Costs For A Typical Component
The animation linked from this page provides a strong visual description of the injection moulding process. The essential elements are as follows:
Sanner’s CDMO tooling and molding services offer a range of precision molding technologies to develop and produce virtually any device or component for drug delivery, diagnostic, or medtech devices.
Material is introduced into the injection moulding machine via a Hopper. The injection moulding machine consists of a heated barrel equipped with a reciprocating screw (driven by a hydraulic or electric motor), which feeds the molten polymer into a temperature controlled split mould via a channel system of gates and runners.
Our high-precision electric thermoplastic manufacturing capabilities deliver robust production with consistent quality output for virtually any product volume. Additionally, Sanner offers blow molding services at a number of its facilities.
The screw melts (plasticises) the polymer, and also acts as a ram during the injection phase. The screw action also provides additional heating by virtue of the shearing action on the polymer.
Using fully automatic and robot-supported cleanroom production with minimal bioburden, Sanner can produce a range of devices for drug delivery and diagnostic applications. Sanner offers its CDMO customers molding activities in ISO Class 7 or 8 cleanrooms.
Sanner CDMO can utilize its Babyplast micro-injection molding for prototypes, pilot series parts, providing material integrity even with small shot weights (0.1g).
GETTING A QUOTE WITH LK-MOULD IS FREE AND SIMPLE.
FIND MORE OF OUR SERVICES:
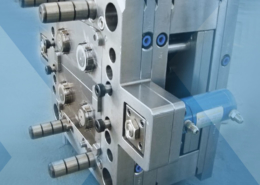
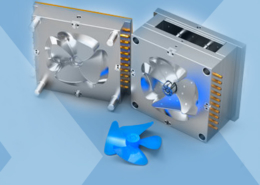
Plastic Molding

Rapid Prototyping
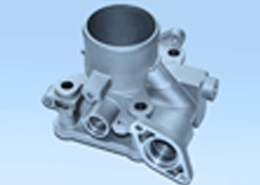
Pressure Die Casting
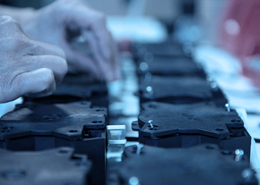
Parts Assembly
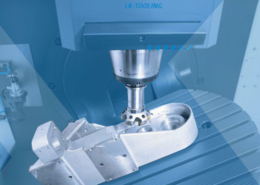